Introduction
Printed circuit boards (PCBs) form the backbone of all modern electronics. They provide the mechanical support to mount electronic components and the electrical connections between components through copper traces etched on the board. For high frequency and high speed signals, copper is the material of choice for PCB fabrication. Copper clad laminate sheets, comprised of a dielectric substrate like FR-4 with thin copper foil laminated on one or both sides, are used as the starting raw material for making PCBs. The properties and quality of the copper foil directly impact the performance of the finished PCB. This article provides a detailed overview of copper coated sheets used for PCB fabrication.
Copper Foil Properties
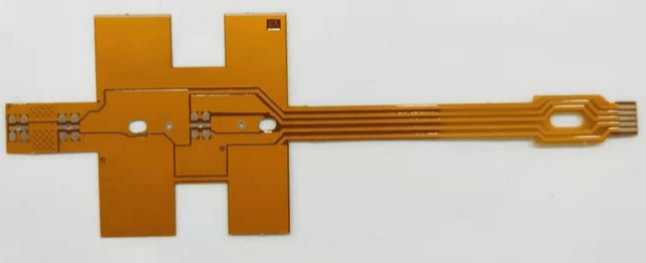
The key properties of electrodeposited copper foils used in PCBs are:
Thickness
- Available from 5 μm to 105 μm
- Thinner foils used for finer lines and spaces
- Thicker foils provide better current carrying capacity
Surface Roughness
- Matte or low profile (LP) 1-4 μm roughness
- Very low profile (VLP) 0.4-1.2 μm roughness
- Smooth or reverse treated foil (RTF) 0.05-0.2 μm roughness
- Determines fine line etching and lamination bonding
Grain Structure
- Rolled foils have elongated grain structure
- Electrodeposited foils have equiaxed grains
Ductility
- Important for lamination bonding
- IPC minimum elongation of 20% for electrodeposited foil
Yield Strength
- Annealed foils around 50-90 MPa
- Rolled foils up to 350 MPa
PCB Copper Foil Types
There are two main types of copper foils used in PCB fabrication:
Rolled Copper Foil
- Produced by mechanically rolling and annealing electrolytic tough pitch (ETP) copper
- Grain structure and strength depends on rolling and annealing process
- Used for thicker foils above 35 μm
Electrodeposited Copper Foil
- Produced by electrolytic plating of copper on a drum surface
- Drum surface ground and polished to control roughness
- Used for foils below 35 μm thickness
- More consistent properties than rolled foil
Some other foil types:
- Electrodeposited copper on carrier foil like stainless steel allows even thinner foils
- Wrought copper foils produced by repeated cold rolling and annealing
Copper Foil Manufacturing Process
Copper foils are manufactured using both rolling and electrolytic deposition processes:
Rolled Copper Foil Manufacturing
- Start with electrolytic tough pitch (ETP) copper cathode
- Roll through a series of rollers at controlled pressure to reduce thickness
- Anneal at high temperature to recrystallize grain structure
- Repeat cold rolling and annealing to achieve final thickness and temper
- Apply surface treatment if needed
Electrodeposited Copper Foil Manufacturing
- Start with stainless steel drum with ground and polished surface
- Rotate drum slowly through an electrolytic bath with copper sulfate solution
- Apply voltage to deposit copper uniformly over drum surface
- Control deposition rates and drum rotation to achieve desired thickness
- Remove foil from drum surface
- Rinse and treat foil surface as needed
Copper Foil Surface Treatments

Copper foil receives various surface treatments to promote adhesion and bonding to the dielectric substrate:
- Nodules – Small copper nodules deposited electrolytically on the surface that grip into the substrate resin
- Silane coating – Thin silane layer enhances resin bonding during lamination
- Reverse treat – Electrolytic deposition of ultra-smooth layer improves laminate bonding
PCB Copper Clad Laminates
Copper clad laminates (CCL) used for PCB fabrication consist of copper foil bonded to a dielectric substrate like FR-4. Some key properties:
- Dielectric materials – FR-4 glass fabric, polyimide, PTFE, ceramic filled laminates
- Dielectric thickness – Typically 0.2 mm to 6.0 mm
- Copper thickness – From 5 μm to 105 μm on one or both sides
- Bond strength – Withstand PCB fabrication processing > 2.8 N/mm peel strength
- High frequency dielectric – Controlled dielectric constant and loss tangent
Key PCB Copper Foil Specifications
Important parameters and tests specified for copper foil include:
IPC-4562 Copper Foil Specification
- Thickness
- Elongation
- Tensile strength
- Peel strength
- Surface roughness
- Visual imperfections
IPC-TM-650 Testing Methods
- Microsection tests
- Elongation and tensile strength
- Peel strength
- Surface roughness
- Visual and dimensional tests
- Purity analysis
Benefits of Copper Foil for PCBs
Some key benefits of using copper foils for PCB fabrication:
- Excellent electrical conductivity suited for high speed signals
- Allows etching fine lines and spaces down to 5 μm
- Good thermal conductivity helps transfer heat from components
- Solderability allows mounting components and connectors
- Available in a wide range of thicknesses and surface finishes
- Mature industry with high reliability and quality standards
PCB Copper Foil Trends
Emerging trends in PCB copper foil technology include:
- Ultra-thin foils below 3 μm thickness enable finer lines and spaces
- Very low profile foils promote lamination bonding for high density PCBs
- Carrier copper foils with stainless steel allow 1 μm thickness
- Surface finishing enhances high frequency performance
- Direct plating processes skip copper foil for ultra-thin copper PCBs
Applications of Copper Foil for PCBs
Major applications utilizing PCB copper clad laminates include:
- Consumer electronics – Cell phones, tablets, computers, appliances
- Automotive electronics – Engine control units, infotainment, sensors
- Industrial – Programmable logic controllers, test equipment
- Medical – Imaging, patient monitoring equipment
- Aerospace and defense – Avionics, guidance systems, communications
High performance applications require advanced PCB materials fabricated from copper foils.
Frequently Asked Questions
What are the different types of copper foils used in PCBs?
The main types are rolled copper foil and electrodeposited copper foil. Rolled foil is produced by mechanically rolling and annealing electrolytic copper to achieve the desired thickness and properties. Electrodeposited foil is produced by electroplating copper onto a polished drum surface to achieve a consistent thickness and roughness.
Why is the surface roughness of copper foil important?
The surface roughness of the foil impacts bonding strength during lamination and allows finer line width etching. Typical foils come in low profile (1-4 μm), very low profile (0.4-1.2 μm) and ultra-smooth reverse treat (0.05-0.2 μm).
What is the role of copper in the PCB fabrication process?
Copper forms the conductive traces that connect the components mounted on the PCB. The traces are formed by lithographic printing and etching of the copper foil laminated onto the PCB dielectric substrate. The copper thickness ranges from 5 μm to 105 μm.
What are some key tests conducted on copper foil?
Important tests are thickness, surface roughness, peel strength, tensile strength and elongation. Visual inspection and microsection are also conducted. IPC-4562 and IPC-TM-650 have detailed test methods for foil qualification.
How thin can PCB copper foils be? What are the challenges with thinner foils?
Standard foils range from 5 μm to 35 μm thickness. Ultra-thin foils down to 1 μm are now being developed. Challenges include handling delicate thin foils and ensuring adequate adhesion and bond strength.
Leave a Reply