Introduction to Clearance and Creepage Distances
In the world of electrical engineering and electronics design, ensuring the safety and reliability of equipment is of utmost importance. Two critical factors that contribute to this goal are clearance and creepage distances. These distances play a vital role in preventing electrical breakdowns, short circuits, and other hazardous situations.
What is Clearance Distance?
Clearance distance refers to the shortest distance through air between two conductive parts or between a conductive part and the grounded surface of the equipment. It is a measure of the insulation’s ability to withstand electrical stress without breaking down.
What is Creepage Distance?
Creepage distance, on the other hand, is the shortest path along the surface of an insulating material between two conductive parts or between a conductive part and the grounded surface of the equipment. This distance is crucial in preventing surface leakage currents, which can occur due to contamination, moisture, or other environmental factors.
Importance of Clearance and Creepage Distances
Maintaining proper clearance and creepage distances is essential for several reasons:
-
Safety: Adequate distances prevent electrical shocks, fires, and other hazards that could harm users or damage equipment.
-
Reliability: By ensuring proper insulation and preventing surface leakage currents, these distances contribute to the long-term reliability and performance of electrical devices.
-
Standards Compliance: Adhering to the recommended clearance and creepage distances is necessary to meet various safety standards and regulations, such as IEC, UL, and EN standards.
Factors Affecting Clearance and Creepage Distances
Several factors influence the required clearance and creepage distances in an electrical design:
1. Voltage
The voltage between conductive parts is a primary factor in determining the necessary clearance and creepage distances. Higher voltages require greater distances to prevent electrical breakdown and surface leakage currents.
2. Pollution Degree
The pollution degree of the environment in which the equipment will be used also affects the required distances. There are four pollution degrees defined in the IEC 60664-1 standard:
- Pollution Degree 1: No pollution or only dry, non-conductive pollution occurs.
- Pollution Degree 2: Only non-conductive pollution occurs, except for occasional temporary conductivity caused by condensation.
- Pollution Degree 3: Conductive pollution or dry, non-conductive pollution that becomes conductive due to condensation is present.
- Pollution Degree 4: Persistent conductivity occurs due to conductive dust, rain, or other wet conditions.
Higher pollution degrees require greater creepage distances to prevent surface leakage currents.
3. Material Group
The insulating material’s properties also influence the required creepage distances. The IEC 60664-1 standard defines four material groups based on their comparative tracking index (CTI):
- Material Group I: CTI ≥ 600
- Material Group II: 400 ≤ CTI < 600
- Material Group IIIa: 175 ≤ CTI < 400
- Material Group IIIb: 100 ≤ CTI < 175
Materials with higher CTI values require smaller creepage distances.
4. Altitude
For equipment operating at altitudes above 2,000 meters, the clearance distances must be increased to compensate for the reduced air density and dielectric strength.
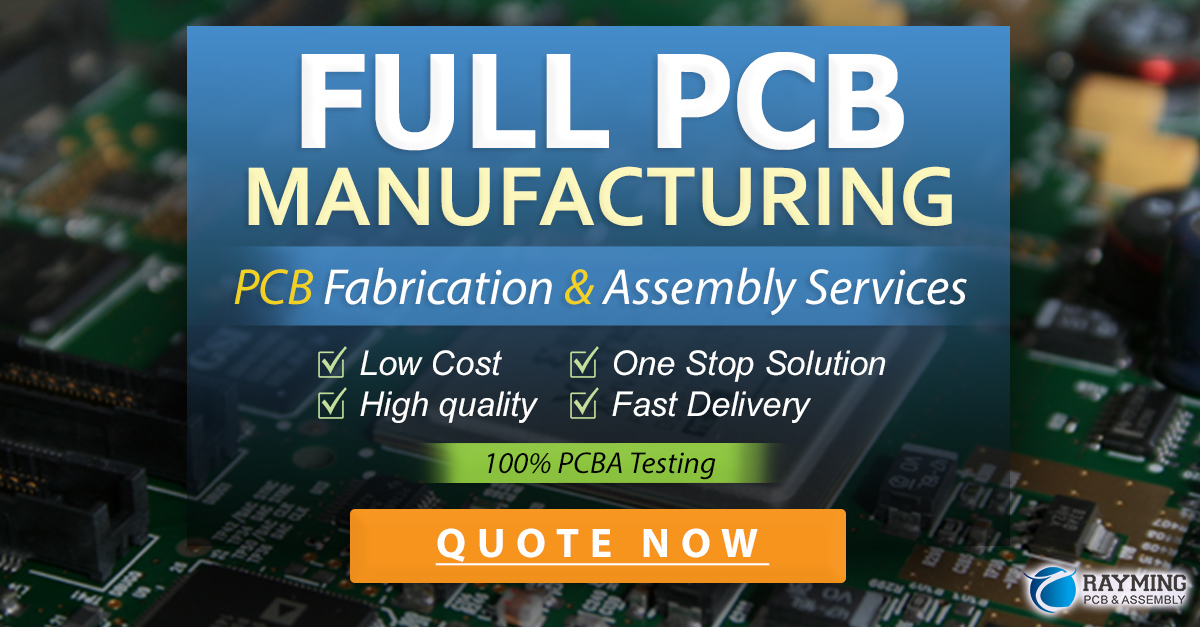
Calculating Clearance and Creepage Distances
To determine the required clearance and creepage distances for a given design, engineers can refer to tables provided in various safety standards. These tables offer minimum distances based on factors such as voltage, pollution degree, and material group.
Example: Clearance Distance Calculation
Consider an electrical device with a working voltage of 250 V AC and a pollution degree of 2. To determine the minimum clearance distance, we can refer to Table 1 below, which is adapted from the IEC 60664-1 standard:
Voltage (V AC) | Pollution Degree 2 Minimum Clearance (mm) |
---|---|
≤ 50 | 0.2 |
≤ 100 | 0.2 |
≤ 150 | 0.5 |
≤ 300 | 1.5 |
≤ 600 | 3.0 |
Based on the table, the minimum required clearance distance for our example is 1.5 mm.
Example: Creepage Distance Calculation
Now, let’s consider the same device with a working voltage of 250 V AC, a pollution degree of 2, and an insulating material from Material Group IIIa. To find the minimum creepage distance, we can use Table 2 below, which is also adapted from the IEC 60664-1 standard:
| Voltage (V AC) | Pollution Degree 2 Minimum Creepage (mm) |
| | Material Group IIIa |
|—————-|——————————————-|
| ≤ 50 | 1.6 |
| ≤ 100 | 2.0 |
| ≤ 150 | 2.5 |
| ≤ 300 | 4.0 |
| ≤ 600 | 8.0 |
For our example, the minimum required creepage distance is 4.0 mm.
Practical Considerations
When designing electrical equipment, engineers should keep the following points in mind:
-
Always choose the larger of the required clearance and creepage distances to ensure safety and reliability.
-
Consider the manufacturing tolerances and potential variations in the insulating material’s properties when determining the actual distances to be used in the design.
-
Regularly inspect and maintain equipment to ensure that the clearance and creepage distances remain adequate throughout the device’s lifetime.
-
Stay updated with the latest safety standards and regulations, as they may change over time.
Frequently Asked Questions (FAQ)
-
What is the difference between clearance and creepage distances?
Clearance distance is the shortest distance through air between two conductive parts, while creepage distance is the shortest path along the surface of an insulating material between two conductive parts. -
Why are clearance and creepage distances important?
Clearance and creepage distances are essential for ensuring the safety and reliability of electrical equipment by preventing electrical breakdowns, short circuits, and surface leakage currents. -
What factors affect the required clearance and creepage distances?
The main factors that influence the required distances are voltage, pollution degree, insulating material group, and altitude. -
How can I determine the required clearance and creepage distances for my design?
Engineers can refer to tables provided in safety standards such as IEC 60664-1, which offer minimum distances based on factors like voltage, pollution degree, and material group. -
What should I do if I’m unsure about the required clearance and creepage distances for my project?
If you are unsure about the required distances, consult with experienced electrical engineers, refer to the relevant safety standards, and consider seeking advice from the equipment manufacturer or a third-party testing and certification agency.
Conclusion
Clearance and creepage distances are vital considerations in the design of safe and reliable electrical equipment. By understanding the factors that affect these distances and adhering to the recommended minimum values, engineers can create designs that prevent electrical breakdowns, short circuits, and surface leakage currents.
Regularly reviewing and updating designs to comply with the latest safety standards and best practices is essential to ensure the ongoing safety and performance of electrical devices. By prioritizing clearance and creepage distances, engineers can contribute to a safer and more reliable world of electronics.
Leave a Reply