What is a Breakaway Tabs PCB?
A Breakaway Tabs PCB, also known as a snap-off PCB or break-off PCB, is a type of printed circuit board that features tabs or sections that can be easily separated from the main board. These tabs are designed to be broken off cleanly, allowing for easy customization and configuration of the PCB to suit specific needs.
Breakaway Tabs PCBs are commonly used in prototyping, testing, and small-scale production, where flexibility and adaptability are essential. They offer several advantages over traditional PCBs, including:
- Cost-effectiveness: By allowing multiple designs on a single board, Breakaway Tabs PCBs reduce production costs and minimize waste.
- Customization: Users can easily break off the desired sections to create a custom PCB that meets their specific requirements.
- Convenience: Breakaway Tabs PCBs eliminate the need for cutting or drilling, making the customization process quick and easy.
Types of Breakaway Tabs PCBs
There are two main types of Breakaway Tabs PCBs:
-
Perforated Breakaway Tabs PCBs: These boards feature perforated lines between the tabs and the main board, allowing for easy separation by hand.
-
V-Groove Breakaway Tabs PCBs: These boards have v-shaped grooves cut into the board between the tabs and the main section. The v-grooves allow for clean, precise breaks when the tabs are snapped off.
Designing a Breakaway Tabs PCB
When designing a Breakaway Tabs PCB, several factors must be considered to ensure proper functionality and ease of use.
PCB Layout Considerations
-
Tab size: Determine the appropriate size for the breakaway tabs based on the components and circuitry they will contain. Ensure that the tabs are large enough to accommodate the necessary components and traces but small enough to be easily snapped off.
-
Spacing: Provide adequate spacing between the tabs and the main board to allow for clean, easy separation. The spacing should be wide enough to prevent accidental breaks but narrow enough to maintain structural integrity.
-
Component placement: Arrange components on the tabs and main board in a logical manner, taking into account the intended use of each section. Ensure that components on the tabs do not interfere with the breaking process.
-
Trace routing: Route traces carefully to avoid crossing the breakaway lines. If traces must cross the breakaway lines, use techniques such as v-grooves or perforations to ensure clean breaks without damaging the traces.
Breakaway Mechanism Selection
When choosing between perforated and v-groove breakaway mechanisms, consider the following factors:
-
Ease of separation: Perforated tabs are generally easier to separate by hand, while v-groove tabs may require the use of pliers or other tools for a clean break.
-
Precision: V-groove tabs offer more precise and clean breaks compared to perforated tabs, which may result in rough edges or debris.
-
Structural integrity: Perforated tabs may be more susceptible to accidental breakage during handling and assembly, while v-groove tabs provide better structural integrity.
Design Tools and Software
Several PCB design software packages support the creation of Breakaway Tabs PCBs. Some popular options include:
- Altium Designer
- KiCad
- Eagle CAD
- OrCAD
- Cadence Allegro
These tools offer features such as automatic tab generation, v-groove and perforation placement, and design rule checking to ensure proper layout and manufacturability.
Manufacturing Breakaway Tabs PCBs
Once the design is complete, the next step is to manufacture the Breakaway Tabs PCB. The manufacturing process is similar to that of traditional PCBs, with a few additional considerations.
PCB Fabrication Process
-
Gerber file generation: Export the PCB design as a set of Gerber files, which contain the necessary information for each layer of the board, including the breakaway tabs and v-grooves or perforations.
-
Board fabrication: The PCB manufacturer uses the Gerber files to create the physical board, typically using a combination of etching, drilling, and plating processes.
-
V-groove or perforation creation: If v-grooves are used, they are typically cut into the board using a specialized milling machine. Perforations are created using a drilling or punching process.
-
Solder mask and silkscreen application: A solder mask is applied to the board to protect against short circuits and improve solderability. Silkscreen labels are added to identify components, connectors, and other features.
-
Quality control: The manufacturer inspects the finished boards to ensure they meet the specified requirements and are free of defects.
Choosing a PCB Manufacturer
When selecting a PCB manufacturer for your Breakaway Tabs PCB project, consider the following factors:
-
Experience: Choose a manufacturer with experience in producing Breakaway Tabs PCBs to ensure they have the necessary expertise and equipment.
-
Capabilities: Verify that the manufacturer can accommodate your specific design requirements, such as board thickness, material selection, and surface finishes.
-
Quality control: Ensure that the manufacturer has a robust quality control process in place to identify and correct any issues during production.
-
Lead time and pricing: Compare lead times and pricing from multiple manufacturers to find the best balance between cost and delivery speed for your project.
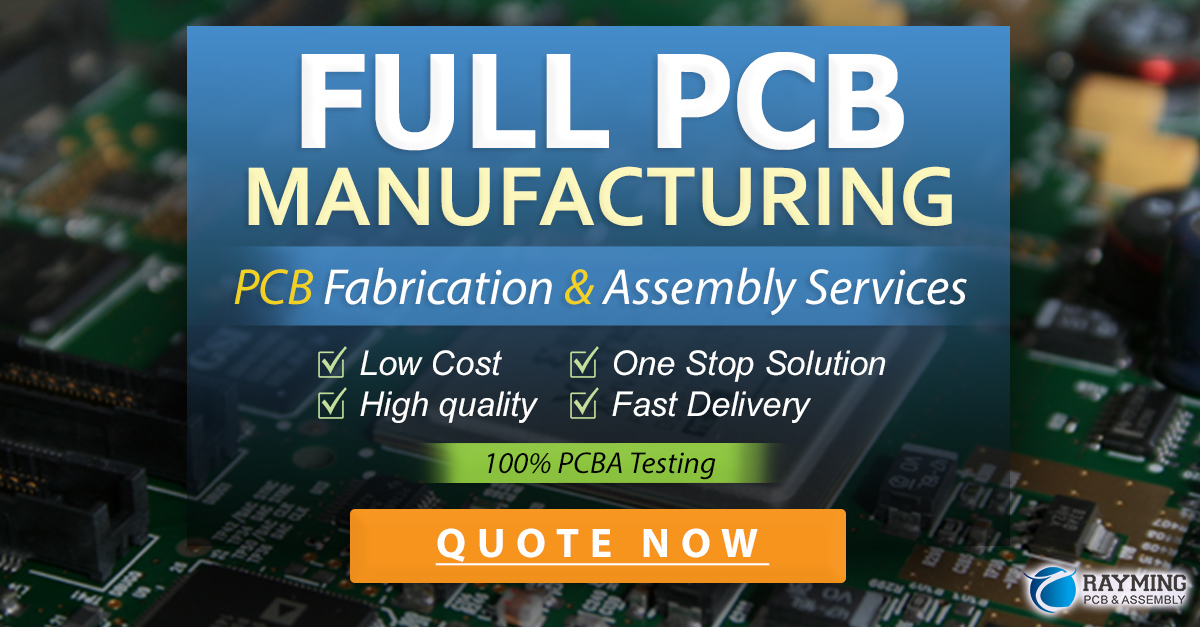
Assembling and Using Breakaway Tabs PCBs
Once the Breakaway Tabs PCB has been manufactured, it’s time to assemble the components and put the board to use.
Component Assembly
-
Soldering: Use standard soldering techniques to attach components to the board, taking care not to apply excessive heat or pressure near the breakaway tabs.
-
Inspection: Visually inspect the assembled board to ensure all components are properly seated and soldered.
-
Testing: Perform any necessary functional tests to verify that the assembled board operates as intended.
Breaking Off Tabs
To break off the tabs from the main board, follow these steps:
-
Identify the break line: Locate the v-groove or perforation line between the tab and the main board.
-
Support the board: Hold the main board securely, ensuring that it is supported on both sides of the break line.
-
Apply pressure: For perforated tabs, grasp the tab firmly and apply steady pressure to snap it off. For v-groove tabs, use pliers or a similar tool to apply pressure evenly along the break line until the tab separates.
-
Clean up: If necessary, use a file or sandpaper to smooth any rough edges on the main board or the separated tab.
Customization and Configuration
One of the key benefits of Breakaway Tabs PCBs is the ability to easily customize and configure the board for specific applications. Some common customization options include:
-
Jumper settings: Use jumpers or solder bridges to configure the board’s functionality, such as selecting between different voltage levels or communication protocols.
-
Connector options: Break off tabs with different connector types or pin counts to match the requirements of the target system.
-
Feature selection: Remove tabs containing unnecessary features or components to minimize board size and cost.
Breakaway Tabs PCB Applications
Breakaway Tabs PCBs are used in a wide range of applications, from prototyping and testing to small-scale production runs. Some common applications include:
Prototyping and Testing
Breakaway Tabs PCBs are ideal for prototyping and testing new designs, as they allow for quick and easy customization without the need for multiple board revisions. Designers can create a single board with various configurations and break off the desired sections for testing and evaluation.
Education and Training
In educational settings, Breakaway Tabs PCBs can be used to teach students about PCB design, assembly, and customization. The modular nature of these boards allows for hands-on learning experiences and encourages experimentation.
Small-Scale Production
For small-scale production runs, Breakaway Tabs PCBs offer a cost-effective solution by allowing multiple product variations to be manufactured on a single board. This approach reduces setup costs and minimizes waste compared to producing separate boards for each variation.
Customized Devices
Breakaway Tabs PCBs are well-suited for creating customized devices or modules for specific applications. By designing a board with various breakaway sections, users can create tailored solutions that meet their unique requirements without the need for custom PCB fabrication.
FAQ
-
What is the minimum tab size for a Breakaway Tabs PCB?
The minimum tab size depends on several factors, including the components and traces on the tab, the breakaway mechanism (perforations or v-grooves), and the manufacturing capabilities of the PCB fabricator. As a general guideline, tabs should be at least 5mm wide and 10mm long to ensure structural integrity and ease of separation. -
Can I use both perforations and v-grooves on the same Breakaway Tabs PCB?
Yes, it is possible to use both perforations and v-grooves on the same board. This approach can be useful when different sections of the board require different levels of precision or ease of separation. However, keep in mind that using both methods may increase the complexity and cost of the manufacturing process. -
How do I ensure traces do not break when separating tabs?
To prevent traces from breaking during tab separation, follow these guidelines: - Route traces perpendicular to the break line whenever possible
- Avoid placing traces too close to the break line
- Use teardrops or anchor points to reinforce traces at the break line
-
Consider using v-grooves instead of perforations for more precise breaks
-
Can I use any PCB material for Breakaway Tabs PCBs?
Most standard PCB materials, such as FR-4, can be used for Breakaway Tabs PCBs. However, some materials may be more brittle or prone to cracking during the breaking process. Consult with your PCB manufacturer to select the best material for your specific application and breakaway requirements. -
How do I panelize Breakaway Tabs PCBs for manufacturing?
When panelizing Breakaway Tabs PCBs, consider the following: - Use a panelization tool or software to automatically generate the panel layout
- Ensure adequate spacing between individual boards to allow for clean separation
- Add fiducial marks and tooling holes to aid in assembly and manufacturing
- Verify that the panel design meets the manufacturer’s requirements and design rules
Breakaway Mechanism | Ease of Separation | Precision | Structural Integrity |
---|---|---|---|
Perforations | High | Low | Low |
V-Grooves | Medium | High | High |
Table 1: Comparison of perforations and v-grooves for Breakaway Tabs PCBs
Application | Benefits of Breakaway Tabs PCBs |
---|---|
Prototyping | Quick customization, reduced costs, faster iterations |
Education | Hands-on learning, encourages experimentation |
Small-scale Production | Cost-effective, minimizes waste, allows for product variations |
Customized Devices | Tailored solutions, eliminates need for custom PCB fabrication |
Table 2: Benefits of Breakaway Tabs PCBs for various applications
In conclusion, Breakaway Tabs PCBs offer a versatile and cost-effective solution for a wide range of applications, from prototyping and testing to small-scale production and customized devices. By understanding the design considerations, manufacturing processes, and assembly techniques involved in creating Breakaway Tabs PCBs, designers and engineers can leverage their benefits to create flexible, adaptable, and efficient electronic systems.
Leave a Reply