What is Automated Optical Inspection?
Automated Optical Inspection is a non-contact, non-destructive testing method that uses digital cameras and image processing software to automatically detect and classify defects on the surface of manufactured products. AOI systems capture high-resolution images of the product, analyze the images using pre-defined criteria, and identify any defects or anomalies that fall outside of acceptable tolerances.
AOI is commonly used in the electronics industry for inspecting printed circuit boards (PCBs), but it is also used in a wide range of other industries, including:
- Automotive
- Aerospace
- Medical devices
- Consumer products
- Packaging
Benefits of Automated Optical Inspection
There are numerous benefits to using AOI in manufacturing, including:
-
Improved quality: AOI systems can detect defects that are difficult or impossible for human inspectors to see, ensuring that only high-quality products are shipped to customers.
-
Increased efficiency: AOI can inspect products much faster than manual inspection, allowing manufacturers to increase throughput and reduce production costs.
-
Reduced labor costs: By automating the inspection process, manufacturers can reduce the need for manual labor, freeing up workers to focus on higher-value tasks.
-
Consistent results: AOI systems use objective criteria to evaluate products, ensuring that inspection results are consistent and repeatable.
-
Early defect detection: By inspecting products early in the manufacturing process, AOI can identify defects before they become more costly to fix or result in scrap.
How Automated Optical Inspection Works
AOI systems typically consist of the following components:
- Lighting system: Provides consistent and uniform illumination of the product being inspected.
- Digital cameras: Capture high-resolution images of the product from multiple angles.
- Image processing software: Analyzes the captured images and compares them to pre-defined criteria to identify defects.
- Conveyor system: Moves the product through the inspection station.
- Reject mechanism: Automatically removes defective products from the production line.
The AOI process can be broken down into the following steps:
-
Product setup: The product is placed on the conveyor system and aligned for inspection.
-
Image acquisition: The digital cameras capture images of the product from multiple angles.
-
Image processing: The image processing software analyzes the captured images and compares them to pre-defined criteria.
-
Defect detection: Any defects or anomalies that fall outside of acceptable tolerances are identified and classified.
-
Defect classification: The identified defects are classified according to their type and severity.
-
Reporting: The AOI system generates a report detailing the inspection results, including the number and type of defects found.
-
Reject mechanism: If a product is found to be defective, it is automatically removed from the production line by the reject mechanism.
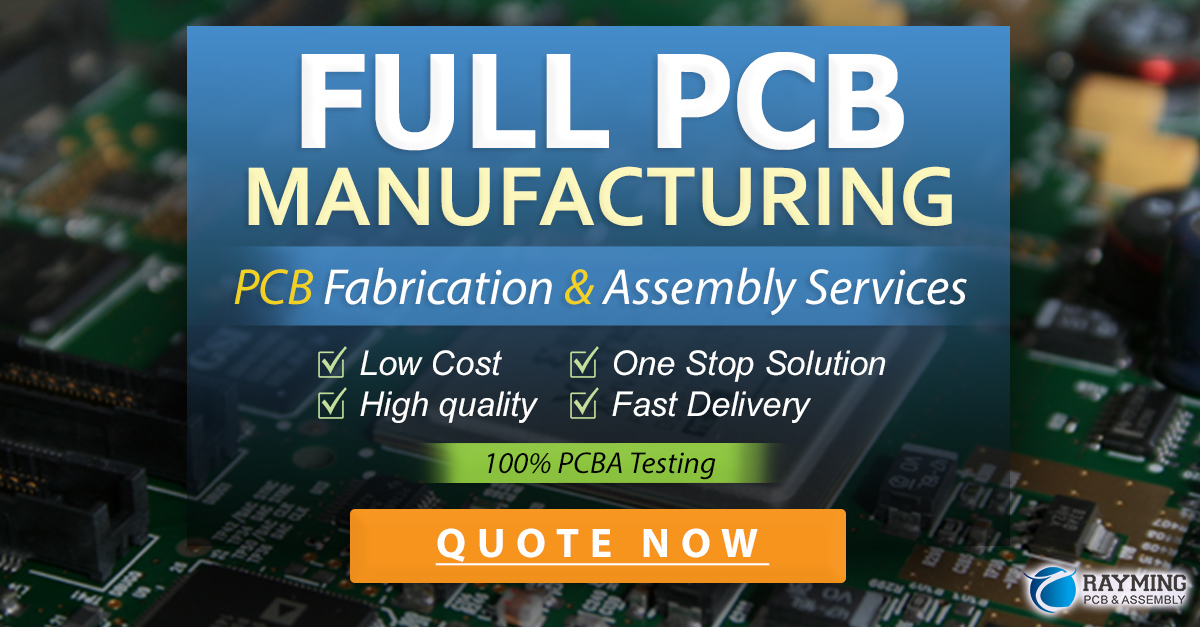
Types of Defects Detected by AOI
AOI systems can detect a wide range of defects, including:
- Missing components
- Incorrect component placement
- Solder defects (bridges, balls, insufficient solder)
- Component polarity
- Trace defects (opens, shorts)
- Contamination (flux residue, dirt)
- Cosmetic defects (scratches, dents)
The specific types of defects that can be detected by AOI depend on the industry and product being inspected. For example, in the electronics industry, AOI is commonly used to detect defects on PCBs, such as:
Defect Type | Description |
---|---|
Solder bridges | Unintended connections between two or more solder joints |
Solder balls | Small spheres of solder that can cause short circuits |
Insufficient solder | Solder joints that do not have enough solder to form a reliable connection |
Component shift | Components that are not centered on their pads |
Component skew | Components that are rotated or tilted relative to their pads |
Tombstoning | Components that stand up on one end due to uneven heating during soldering |
Advantages of AOI over Manual Inspection
While manual inspection still plays an important role in many manufacturing processes, AOI offers several key advantages over manual inspection:
-
Speed: AOI systems can inspect products much faster than human inspectors, often at rates of thousands of products per hour.
-
Consistency: AOI systems use objective criteria to evaluate products, ensuring that inspection results are consistent and repeatable.
-
Accuracy: AOI systems can detect defects that are difficult or impossible for human inspectors to see, such as hairline cracks or subtle color variations.
-
Scalability: AOI systems can be easily scaled up to handle larger production volumes without requiring additional labor.
-
Traceability: AOI systems generate detailed reports that provide a record of every product inspected, making it easy to trace defects back to their source.
Limitations of AOI
While AOI is a powerful tool for detecting defects in manufactured products, it does have some limitations:
-
Initial setup: AOI systems require significant upfront investment in equipment and programming to set up and configure for a specific product.
-
Limited defect types: AOI systems are best suited for detecting surface defects and may not be able to detect internal or functional defects.
-
False positives/negatives: AOI systems can sometimes generate false positive or false negative results, requiring additional manual inspection to verify the results.
-
Product variability: AOI systems may have difficulty inspecting products with high variability or complex geometries.
Despite these limitations, AOI remains a valuable tool for ensuring product quality and reducing the risk of defects reaching customers.
Implementing AOI in Manufacturing
Implementing AOI in a manufacturing process requires careful planning and execution. The following steps can help ensure a successful AOI implementation:
-
Define inspection requirements: Clearly define the types of defects that need to be detected and the acceptable tolerances for each defect type.
-
Select appropriate equipment: Choose an AOI system that is capable of detecting the required defect types and can handle the production volume and product variability.
-
Develop inspection criteria: Work with the AOI vendor to develop inspection criteria that accurately detect the required defect types without generating excessive false positives or false negatives.
-
Integrate with production line: Integrate the AOI system into the production line, ensuring that it does not create bottlenecks or disrupt the flow of products.
-
Train operators: Train production staff on how to operate and maintain the AOI system, including how to set up products for inspection and interpret inspection results.
-
Monitor and optimize: Continuously monitor the performance of the AOI system and make adjustments as needed to optimize its effectiveness and efficiency.
The Future of AOI
As manufacturing processes continue to evolve and become more complex, the demand for advanced inspection technologies like AOI will only continue to grow. Some of the key trends and developments shaping the future of AOI include:
-
3D AOI: 3D AOI systems use multiple cameras and advanced algorithms to create a three-dimensional model of the product being inspected, allowing for more accurate defect detection and measurement.
-
AI and machine learning: The integration of artificial intelligence and machine learning into AOI systems will enable them to learn and adapt to new products and defect types over time, improving their accuracy and efficiency.
-
Inline vs. offline inspection: While most AOI systems today are used for offline inspection after the product has been manufactured, there is growing interest in inline AOI systems that can inspect products in real-time as they are being produced.
-
Integration with other inspection methods: AOI is often used in conjunction with other inspection methods, such as X-ray inspection or functional testing, to provide a more comprehensive quality control solution. In the future, we can expect to see even greater integration between these different inspection technologies.
FAQ
What types of products can be inspected using AOI?
AOI can be used to inspect a wide range of products, including printed circuit boards, automotive parts, medical devices, consumer products, and packaging. Essentially, any product with a surface that can be imaged can potentially be inspected using AOI.
How much does an AOI system cost?
The cost of an AOI system can vary widely depending on the specific requirements of the application, such as the size and complexity of the products being inspected, the required defect detection capabilities, and the production volume. Entry-level AOI systems can start at around $50,000, while high-end systems can cost $500,000 or more.
How fast can AOI systems inspect products?
The inspection speed of an AOI system depends on several factors, including the size and complexity of the product, the number of cameras and viewing angles, and the image processing capabilities of the system. In general, AOI systems can inspect products at rates ranging from a few hundred to several thousand products per hour.
Can AOI systems inspect 100% of products?
Yes, AOI systems can be used to inspect 100% of products on a production line. However, the feasibility of 100% inspection depends on factors such as the production volume, the speed of the AOI system, and the level of defect detection required. In some cases, manufacturers may choose to use AOI for sample inspection rather than 100% inspection.
How do AOI systems handle product variability?
AOI systems can handle some degree of product variability by using adaptive algorithms and machine learning to adjust the inspection criteria based on the specific characteristics of each product. However, excessive product variability or complex geometries can still pose challenges for AOI systems and may require additional programming or specialized equipment to inspect effectively.
Conclusion
Automated Optical Inspection is a powerful technology that is transforming the way manufacturers ensure product quality and consistency. By leveraging advanced imaging systems and sophisticated algorithms, AOI enables manufacturers to inspect products quickly, accurately, and reliably, reducing the need for manual inspection and minimizing the risk of defects reaching customers.
As manufacturing processes continue to evolve and become more complex, the demand for advanced inspection technologies like AOI will only continue to grow. With ongoing developments in areas like 3D AOI, AI and machine learning, and inline inspection, we can expect to see even greater adoption of AOI across a wide range of industries in the years to come.
Leave a Reply