Introduction to AOI in PCB and SMT Manufacturing
Automated Optical Inspection (AOI) plays a critical role in ensuring quality and reliability in Printed Circuit Board (PCB) and Surface Mount Technology (SMT) production lines. AOI systems use advanced imaging and computer vision algorithms to quickly and accurately detect defects, such as missing components, improper soldering, and incorrect component placement, that may occur during the manufacturing process.
In the fast-paced world of Electronics Manufacturing, where product lifecycles are short and time-to-market is crucial, AOI has become an indispensable tool for maintaining high quality standards while keeping up with production demands. By catching defects early in the manufacturing process, AOI helps reduce rework costs, minimize scrap, and improve overall production efficiency.
This article will delve into the importance of AOI in PCB and SMT production lines, its working principles, the types of defects it can detect, and the benefits it offers to manufacturers. We will also discuss the latest advancements in AOI technology and explore how it integrates with other quality control measures in the manufacturing process.
The PCB and SMT Manufacturing Process
To understand the role of AOI in PCB and SMT manufacturing, it is essential to have a basic understanding of the manufacturing process itself. PCBs are the backbone of modern electronics, providing the necessary electrical connections and mechanical support for components. SMT is a method of mounting components directly onto the surface of a PCB, as opposed to through-hole technology, which involves inserting component leads through holes in the board.
The typical PCB and SMT manufacturing process involves several steps:
- PCB Design and Fabrication
- Circuit design and schematic creation
- PCB Layout and routing
-
PCB Fabrication (etching, drilling, plating, etc.)
-
Solder Paste Printing
-
Application of solder paste onto PCB pads using a stencil
-
Component Placement
-
Automated pick-and-place machines place components onto the PCB
-
Reflow Soldering
-
The PCB passes through a reflow oven, melting the solder paste and forming electrical connections
-
Inspection and Testing
-
Visual inspection and functional testing to ensure proper assembly and functionality
-
Conformal Coating and Final Assembly
- Application of protective coatings and final assembly into the end product
AOI is typically employed after the solder paste printing, component placement, and reflow soldering stages to detect and prevent defects from propagating further down the production line.
Types of Defects Detected by AOI
AOI systems are designed to detect a wide range of defects that can occur during the PCB and SMT manufacturing process. Some of the most common types of defects include:
- Component Placement Defects
- Missing components
- Misaligned or rotated components
- Incorrect component polarity
-
Wrong component type or value
-
Solder Joint Defects
- Insufficient or excessive solder
- Solder bridges or shorts
- Cold Solder Joints
-
Lifted leads or tombstoning
-
Solder Paste Defects
- Insufficient or excessive solder paste
- Solder paste smearing or slumping
-
Solder paste registration errors
-
PCB Defects
- Broken or damaged traces
- Etching or plating defects
- Contamination or foreign objects
- Incorrect hole sizes or locations
By detecting these defects early in the manufacturing process, AOI helps prevent faulty boards from progressing to later stages, reducing rework costs and improving overall product quality.
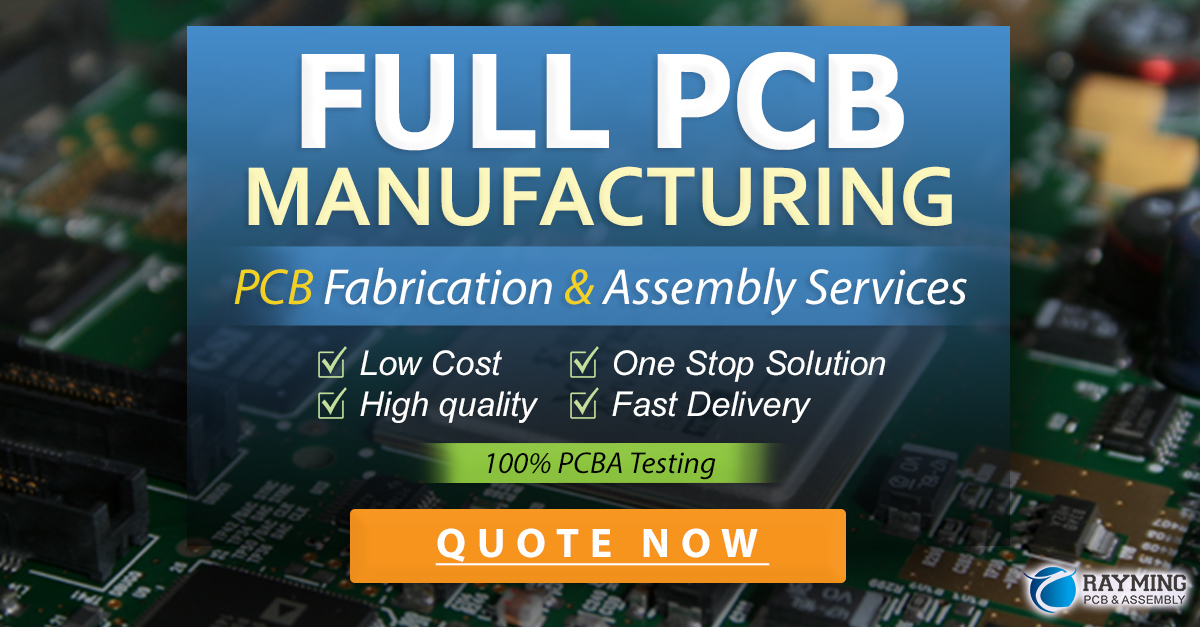
How AOI Works
AOI systems use a combination of high-resolution cameras, lighting systems, and advanced image processing algorithms to inspect PCBs and identify defects. The basic working principle of an AOI system can be broken down into three main steps:
- Image Acquisition
- The PCB is illuminated using a controlled lighting system, which may include various lighting angles and colors to enhance defect visibility
-
High-resolution cameras capture images of the PCB from multiple angles
-
Image Analysis
- The captured images are processed using computer vision algorithms and compared to a reference image or CAD data
-
The system looks for deviations from the expected patterns, such as missing components, improper alignment, or solder defects
-
Defect Classification and Reporting
- Detected defects are classified according to predefined categories and severity levels
- The system generates a report detailing the location, type, and severity of each defect
- The report is used to guide rework efforts and track process improvements
Modern AOI systems use advanced technologies such as machine learning and artificial intelligence to continuously improve their defect detection capabilities and adapt to new product designs and manufacturing processes.
Benefits of AOI in PCB and SMT Manufacturing
Implementing AOI in PCB and SMT production lines offers numerous benefits to manufacturers, including:
- Improved Product Quality
- Early detection and prevention of defects
- Reduced risk of faulty products reaching customers
-
Increased customer satisfaction and brand reputation
-
Increased Production Efficiency
- Reduced rework and scrap costs
- Faster identification and correction of process issues
-
Improved first-pass yield and overall equipment effectiveness (OEE)
-
Cost Savings
- Reduced labor costs associated with manual inspection
- Minimized material waste and rework expenses
-
Increased production throughput and capacity utilization
-
Traceability and Process Improvement
- Detailed defect data for root cause analysis and process optimization
- Ability to track and trend defect rates over time
-
Facilitates continuous improvement initiatives and operator training
-
Compliance with Quality Standards
- Helps manufacturers meet stringent quality requirements in industries such as automotive, aerospace, and medical devices
- Provides objective, consistent, and documented inspection results
- Supports ISO, IATF, and other quality management system certifications
By leveraging the benefits of AOI, manufacturers can improve their overall competitiveness, reduce costs, and deliver higher-quality products to their customers.
Integration of AOI with Other Quality Control Measures
While AOI is a powerful tool for detecting defects in PCB and SMT manufacturing, it is most effective when used in combination with other quality control measures. Some common techniques that complement AOI include:
- In-Circuit Testing (ICT)
- Electrical testing of individual components and circuits on the PCB
-
Detects defects such as open or short circuits, incorrect component values, and poor solder joints
-
Functional Testing
- Testing the PCB or final product under actual operating conditions
-
Verifies proper functionality and performance of the assembled system
-
X-Ray Inspection
- Non-destructive inspection of solder joints and internal structures
-
Detects defects such as voids, cracks, and bridging that may not be visible to AOI
-
Statistical Process Control (SPC)
- Monitoring and controlling process parameters to prevent defects from occurring
- Uses statistical methods to identify trends and variations in the manufacturing process
By integrating AOI with these other quality control measures, manufacturers can create a comprehensive and robust quality assurance system that catches defects at multiple stages of the manufacturing process and drives continuous improvement efforts.
Advancements in AOI Technology
As the demands for higher quality, faster production, and more complex PCB designs continue to grow, AOI technology is evolving to meet these challenges. Some of the latest advancements in AOI include:
- 3D AOI
- Uses multiple cameras or structured light systems to create a three-dimensional representation of the PCB
-
Enables detection of defects such as warpage, coplanarity issues, and lifted components
-
Machine Learning and AI
- Utilizes deep learning algorithms to improve defect detection accuracy and reduce false positives
-
Enables the system to adapt to new product designs and manufacturing processes without extensive programming
-
High-Resolution Imaging
- Employs advanced camera systems with higher resolutions and faster frame rates
-
Allows for the detection of smaller defects and faster inspection speeds
-
Inline and 3D Solder Paste Inspection (SPI)
- Integrates SPI with AOI to provide a more comprehensive inspection solution
-
Enables early detection of solder paste defects before component placement
-
Big Data Analytics
- Utilizes data from multiple AOI systems and other quality control measures to identify trends and patterns
- Enables predictive maintenance, process optimization, and continuous improvement initiatives
As AOI technology continues to advance, manufacturers can expect to see even greater improvements in defect detection accuracy, inspection speed, and overall production efficiency.
Frequently Asked Questions (FAQ)
- What is the difference between 2D and 3D AOI?
-
2D AOI uses a single camera or multiple cameras to capture two-dimensional images of the PCB, while 3D AOI uses multiple cameras or structured light systems to create a three-dimensional representation of the PCB. 3D AOI can detect defects that may not be visible in 2D images, such as warpage, coplanarity issues, and lifted components.
-
Can AOI replace manual inspection entirely?
-
While AOI can significantly reduce the need for manual inspection, it is not a complete replacement. Some defects, such as those related to component functionality or visual aesthetics, may still require manual inspection. Additionally, AOI systems may generate false positives or false negatives, requiring human intervention to verify and correct.
-
How does AOI handle different component types and sizes?
-
AOI systems can be programmed to recognize and inspect a wide range of component types and sizes. This is typically done by creating a library of component models and teaching the system to identify them based on their visual characteristics. Modern AOI systems can also adapt to new components using machine learning and AI algorithms.
-
What is the typical defect detection rate of AOI systems?
-
The defect detection rate of AOI systems can vary depending on factors such as the complexity of the PCB, the types of components, and the specific AOI system being used. However, modern AOI systems can typically achieve defect detection rates of 95% or higher, with some systems claiming rates as high as 99.9%.
-
How does AOI fit into the overall quality control strategy?
- AOI is an essential component of a comprehensive quality control strategy in PCB and SMT manufacturing. It works in conjunction with other techniques, such as in-circuit testing, functional testing, X-ray inspection, and statistical process control, to provide a multi-layered approach to defect detection and prevention. By integrating AOI with these other measures, manufacturers can create a robust quality assurance system that drives continuous improvement and ensures the delivery of high-quality products to customers.
Conclusion
AOI has become an indispensable tool in PCB and SMT manufacturing, enabling manufacturers to detect and prevent defects early in the production process, improve product quality, increase efficiency, and reduce costs. As PCB designs become more complex and time-to-market pressures continue to rise, the importance of AOI will only continue to grow.
By understanding the working principles of AOI, the types of defects it can detect, and the benefits it offers, manufacturers can make informed decisions about implementing and optimizing AOI in their production lines. Moreover, by staying up-to-date with the latest advancements in AOI technology, such as 3D AOI, machine learning, and big data analytics, manufacturers can ensure they are well-positioned to meet the quality and productivity challenges of the future.
Ultimately, the successful integration of AOI into a comprehensive quality control strategy, alongside other measures such as in-circuit testing, functional testing, and statistical process control, will be key to driving continuous improvement and maintaining a competitive edge in the fast-paced world of electronics manufacturing.
Leave a Reply