Flexible circuits, also known as flex circuits, are a type of printed circuit board that can bend and flex. As technology has advanced, flexible circuits have become increasingly popular due to their many advantages over traditional rigid circuit boards. One of the leading manufacturers of flexible circuits is Allflex, which offers a variety of flexible circuit solutions for a wide range of applications.
An Introduction to Flex Circuits
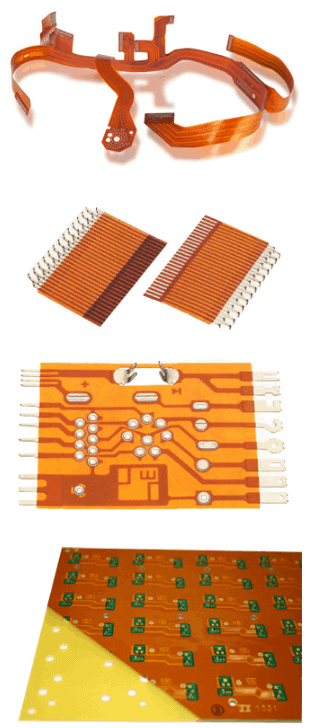
A flexible circuit consists of conductive pathways and traces etched from copper sheets laminated onto a flexible dielectric film substrate such as polyimide or polyester. The traces interconnect various components mounted on the flex circuit and provide electrical connections.
Flexible circuits provide many benefits compared to traditional PCBs:
- Flexible – Can bend and flex repeatedly to fit and move within confined spaces
- Lightweight – Weigh less than rigid boards
- Thin – Extremely thin profile, as little as 1 mil thickness
- Durable – Withstand vibration, shock, and extreme temperatures
- Reliable – Proven high reliability and excellent electrical performance
- Customizable – Can be manufactured in many shapes and configurations
Some key applications of flex circuits include:
- Portable electronics
- Medical devices
- Automotive electronics
- Industrial equipment
- Aerospace and military products
Allflex Flex Circuits Overview
Allflex has over 50 years of experience manufacturing custom flex circuits of all types. With advanced solutions and capabilities, Allflex has become a trusted flex circuit provider for many major companies.
Some key benefits and offerings of Allflex’s flexible circuits include:
- Capability to manufacture simple to complex flex designs
- Flex-rigid boards with integrated rigid and flex sections
- Single, double, and multilayer flex constructions
- Blind and buried vias for multilayer boards
- Fine line/space traces down to 1 mil
- Integrated soldermask and coverlayers
- Parts-on-flex integration and assembly
- Extensive design support and prototyping services
Allflex utilizes the latest materials and manufacturing processes to produce the most reliable flex circuits on the market. A wide range of substrate materials are available, including polyimide, polyester, PEN, and more.
Types of Flex Circuits from Allflex
Allflex has the expertise to design and manufacture just about any type of flex circuit configuration and application. Here are some of the most common types of flex circuits produced:
Single Layer Flex Circuits
Single layer flex circuits have a single conductive layer of traces and components on one side of the flexible substrate. They represent the simplest and most cost-effective flex circuit design. Single layer circuits work well for low complexity connections.
Double Layer Flex Circuits
Double layer flex circuits contain conductive traces on both sides of the flexible substrate. This allows for increased circuit complexity and trace density, as traces can crossover between layers. Vias interconnect the two sides. Double layer flex circuits are suitable for more complex designs.
Multilayer Flex Circuits
Multilayer flex circuits have three or more conductive trace layers separated by flexible dielectric films. Multilayer construction allows for still greater circuit complexity and interconnectivity using buried and blind vias to route between layers. Shielding layers can also be incorporated.
Rigid-Flex Circuits
Rigid-flex circuits combine rigid board sections integrated with flexible circuits. This allows high component density on rigid sections while still maintaining flexing ability of the flex circuit areas. Rigid-flex is ideal for applications that require both rigidity and flexibility.
Flex Assemblies
Flex assemblies or “flex assemblies” have electronic components mounted and soldered directly onto the flexible circuit. This provides a lightweight, space-saving interconnect solution. Allflex has capabilities for through-hole and surface mount assembly.
Allflex Flex Circuit Applications
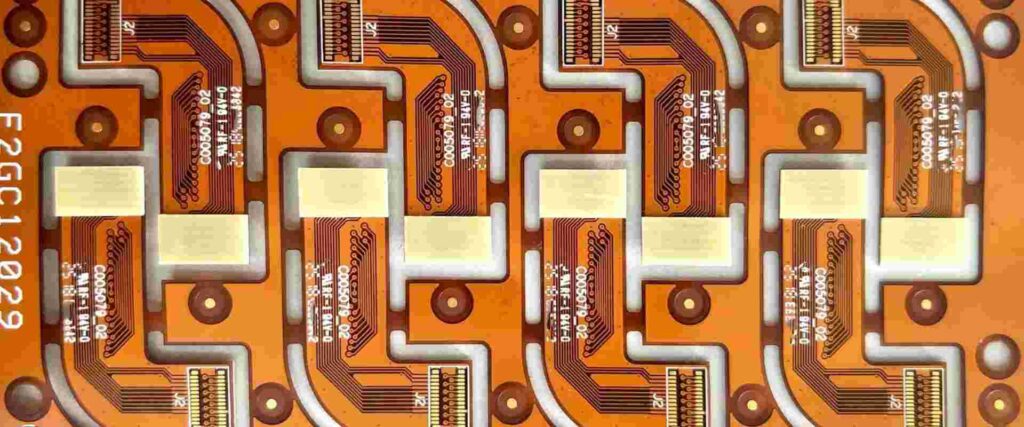
With their thin, lightweight, and bendable properties, Allflex’s flex circuits are ideal for many modern electronic product applications:
Aerospace and Defense
Allflex flex circuits withstand shock, vibration, temperature extremes, and other harsh conditions found in aircraft, satellites, missiles, and other military systems. Flex circuits are much lighter than traditional wiring harnesses.
Automotive Electronics
Flex circuits are increasingly used in cars, trucks, and other vehicles. Auto applications include circuitry for engine systems, instrument panels, safety systems, navigation displays, and control panels.
Medical Electronics
In medical devices such as patient monitors, MRI machines, and surgical equipment, flex circuits can withstand repeated bending and twisting. Excellent reliability is also critical.
Consumer Electronics
Wearable devices, mobile phones, tablets, cameras, and portable gadgets benefit from thin, lightweight flex circuits to interconnect smaller components.
Internet of Things (IoT) Devices
Interconnectivity of smart home, office, and industrial devices requires robust, flexible circuitry. Flex circuits suit many compact IoT product designs.
Robotics
Robotics and automated systems involve motion and articulation where rigid boards would fail. Allflex’s flex circuits accommodate moving joints and mechanisms.
The Benefits of Using Allflex Flex Circuits
With modern electronic products becoming smaller, lighter, and more portable, the inherent properties of flex circuits make them an ideal interconnect solution. There are many advantages of specifying Allflex as a flex circuit supplier:
- Proven Reliability – Allflex’s flex circuits meet stringent quality standards and reliability testing.
- Design Support – Allflex’s engineering team provides extensive design review and recommendations to optimize flex circuits.
- Assembly Services – Allflex offers parts-on-flex assembly for complete flex circuit solutions.
- Quick Prototypes – Allflex can produce prototypes in as little as 24 hours to verify designs upfront.
- Advanced Materials – A broad selection of flexible substrate and cover layer materials are available.
- Supply Chain Expertise – As a major flex provider, Allflex has preferred access to key substrate materials.
- Flexible Manufacturing – Allflex can accommodate high mix/low volume to low mix/high volume demands.
- Miniaturization Capabilities – Allflex specializes in micro-flex circuits with ultra-fine features.
- Robust Designs – Allflex experts design flex circuits for reliability, not just basic function.
By partnering with Allflex for your next flex circuit needs, you gain the backup of a proven industry leader focused on flexible circuit solutions.
Questions and Answers About Allflex Flex Circuits
Here are answers to some common questions about Allflex’s capabilities for developing and manufacturing flexible circuits:
Q: What types of substrate materials can be used for Allflex’s flex circuits?
A: Allflex offers several common flex circuit substrate materials, including polyimide, polyester, PEN, PET, and others. Our engineers will recommend the best material choice for your mechanical, electrical, and application requirements.
Q: What are the minimum trace/space widths achievable on Allflex flex circuits?
A: Utilizing advanced photolithographic processes, Allflex can manufacture flex circuits with minimum trace/space of 1 mil for reliable, high density designs. Even finer geometries are possible for some applications.
Q: Can rigid sections (like PCBs) be integrated with Allflex’s flex circuits?
A: Yes, Allflex produces rigid-flex circuits combining rigid board areas interconnected by flexible circuits. This provides design flexibility to mount components, ICs, connectors, etc. in either rigid or flex zones.
Q: Does Allflex provide engineering support and prototyping services?
A: Absolutely. Allflex’s engineering team reviews customer designs to optimize flex circuit performance, reliability, and manufacturability. We produce rapid prototypes for design verification and proof-of-concept.
Q: What are some common applications suitable for Allflex’s flex circuits?
A: Flex circuits from Allflex thrive in aerospace, defense, telecommunications, medical, robotics, automotive, and consumer electronics applications where flexibility, miniaturization, and ruggedness are required.
Q: What types of quality certifications does Allflex have for flex circuit production?
A: Allflex maintains the highest quality standards with ISO 9001 and AS9100 certification. We follow rigorous quality inspection, testing, and control methods throughout the flex circuit fabrication process.
Q: Can Allflex provide turnkey flex assembly services?
A: Yes. In addition to flex fabrication, Allflex provides parts-on-flex assembly. We have capabilities for through-hole and surface mount soldering, automated placement, full test/inspection, and complete box build assembly.
Q: How can I get a quotation for my custom flex circuit project?
A: You can easily request a free quotation by uploading your flex circuit specifications on our website or by contacting our engineering sales team. We will respond promptly with a detailed quote.
Leave a Reply