Understanding Small Batch assembly
Small batch assembly refers to the process of producing a limited number of products, typically ranging from a few units to a few thousand. This approach is particularly useful for businesses that require flexibility, customization, and quick turnaround times. Some common applications of small batch assembly include:
- Prototyping and product development
- Limited edition or specialty products
- Niche market offerings
- Testing market demand before mass production
Advantages of Small Batch Assembly
- Lower initial investment
- Faster time-to-market
- Greater flexibility and customization
- Reduced inventory risk
- Opportunities for product refinement and iteration
In-House Small Batch Assembly
One of the most cost-effective approaches to small batch assembly is to handle the process in-house. This option allows you to maintain complete control over the production process and eliminates the need for outsourcing fees. However, it’s essential to consider the following factors before deciding to assemble your products in-house:
Equipment and Tools
Investing in the right equipment and tools is crucial for efficient and accurate assembly. Consider the following:
- Workbenches and ergonomic furniture
- Hand tools (e.g., screwdrivers, pliers, wire cutters)
- Power tools (e.g., soldering irons, heat guns, electric screwdrivers)
- Specialized equipment (e.g., 3D printers, CNC machines, Laser Cutters)
Equipment/Tool | Purpose | Estimated Cost |
---|---|---|
Workbench | Provides a sturdy and organized workspace | $200 – $1,000 |
Hand Tools | Essential for basic assembly tasks | $100 – $500 |
Power Tools | Speeds up assembly processes | $200 – $1,500 |
Specialized Equipment | Enables advanced manufacturing capabilities | $1,000 – $10,000+ |
Staffing and Training
Having a skilled and well-trained assembly team is essential for maintaining product quality and efficiency. Consider the following:
- Hiring experienced assemblers or technicians
- Providing comprehensive training for new hires
- Developing standard operating procedures (SOPs) for consistent results
- Implementing quality control measures to ensure product consistency
Inventory Management
Effective inventory management is crucial for minimizing costs and ensuring a smooth assembly process. Consider the following:
- Implementing a just-in-time (JIT) inventory system to reduce storage costs
- Establishing relationships with reliable suppliers for timely component delivery
- Utilizing inventory management software to track stock levels and reorder points
Outsourcing Small Batch Assembly
If in-house assembly is not feasible or cost-effective for your business, outsourcing to a third-party provider can be an excellent alternative. Outsourcing allows you to leverage the expertise, equipment, and resources of specialized assembly services without the need for significant capital investments.
Finding the Right Assembly Partner
When searching for a small batch assembly partner, consider the following factors:
- Experience and expertise in your industry or product type
- Quality control processes and certifications (e.g., ISO 9001)
- Flexibility and adaptability to your specific requirements
- Pricing structure and minimum order quantities (MOQs)
- Lead times and delivery options
- Communication and customer support
Domestic vs. Overseas Outsourcing
When outsourcing small batch assembly, you’ll need to decide between domestic and overseas providers. Each option has its own advantages and disadvantages:
Factor | Domestic Outsourcing | Overseas Outsourcing |
---|---|---|
Cost | Higher labor costs | Lower labor costs |
Lead Time | Shorter shipping times | Longer shipping times |
Communication | Easier communication (same time zone, language) | Potential communication barriers |
Quality Control | Easier to visit and monitor production | More difficult to oversee production |
Intellectual Property | Generally better IP protection | Potential IP risks |
Effective Communication and Collaboration
To ensure a successful outsourcing partnership, it’s essential to establish clear communication channels and collaborate closely with your assembly provider. Consider the following:
- Providing detailed product specifications, drawings, and assembly instructions
- Conducting regular progress updates and quality checks
- Establishing a point of contact for seamless communication
- Visiting the assembly facility in person, if possible, to build a stronger relationship
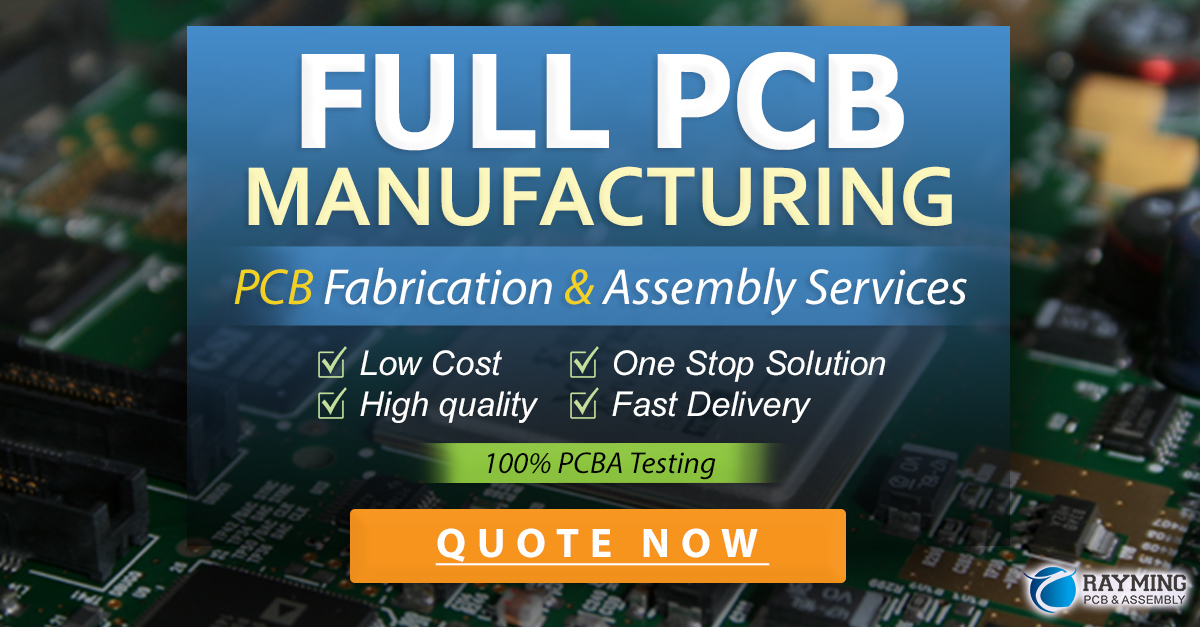
Alternative Small Batch Assembly Options
In addition to traditional in-house and outsourced assembly, there are several alternative options that can be particularly suitable for small batch production:
3D Printing and Additive Manufacturing
3D printing and additive manufacturing technologies have revolutionized small batch production by enabling rapid prototyping and customization. These methods allow you to create complex geometries and intricate designs without the need for expensive tooling or molds. Some popular 3D printing technologies include:
- Fused Deposition Modeling (FDM)
- Stereolithography (SLA)
- Selective Laser Sintering (SLS)
- Multi Jet Fusion (MJF)
CNC Machining
Computer Numerical Control (CNC) machining is a subtractive manufacturing process that uses computer-controlled machines to remove material from a solid block or blank to create a desired shape. CNC machining is ideal for creating high-precision components and can be used with a wide range of materials, including metals, plastics, and composites.
Laser Cutting and Engraving
Laser cutting and engraving technologies use high-powered lasers to cut, etch, or mark materials with precision. These methods are particularly useful for creating intricate designs, custom labels, and branding elements on various materials, such as wood, acrylic, leather, and metal.
Cost-Saving Strategies for Small Batch Assembly
To further reduce the costs associated with small batch assembly, consider the following strategies:
-
Design for Assembly (DFA): Optimize your product design to minimize the number of components and simplify the assembly process, reducing labor costs and assembly time.
-
Standardization: Use standardized components and materials whenever possible to benefit from economies of scale and lower procurement costs.
-
Bulk purchasing: Negotiate better prices with suppliers by purchasing components and materials in larger quantities, even if you only assemble in small batches.
-
Continuous improvement: Regularly review and optimize your assembly processes to identify inefficiencies and implement cost-saving measures.
-
Automation: Invest in automated equipment or collaborate with partners who offer automation services to reduce labor costs and increase productivity.
Frequently Asked Questions (FAQ)
- What is the minimum order quantity (MOQ) for small batch assembly?
-
MOQs vary depending on the assembly provider and the complexity of the product. Some providers may offer assembly services for as few as 10-50 units, while others may require a minimum of a few hundred units.
-
How long does small batch assembly typically take?
-
Lead times for small batch assembly depend on factors such as the complexity of the product, the size of the order, and the chosen assembly method. In general, small batch assembly can take anywhere from a few days to several weeks.
-
What materials can be used in small batch assembly?
-
Small batch assembly can accommodate a wide range of materials, including plastics, metals, wood, composites, and electronics components. The specific materials used will depend on the product requirements and the chosen assembly method.
-
How can I ensure the quality of my small batch assembled products?
-
To ensure product quality, establish clear quality control procedures, conduct regular inspections, and work closely with your assembly partner to address any issues promptly. Consider implementing quality management systems such as ISO 9001 to maintain consistent quality standards.
-
Can I combine different small batch assembly methods for my product?
- Yes, it’s possible to combine different assembly methods to create a complete product. For example, you may use 3D printing for certain components, CNC machining for others, and manual assembly to put everything together. Collaborating with a versatile assembly partner can help you find the most suitable combination of methods for your specific product.
Conclusion
Small batch assembly is a critical aspect of modern manufacturing, enabling businesses to bring innovative products to market quickly and cost-effectively. By exploring the various options available, from in-house assembly to outsourcing and alternative manufacturing methods, you can find the most suitable solution for your specific needs and budget.
Remember to prioritize quality, communication, and collaboration throughout the assembly process to ensure the best possible results. With the right approach and partners, small batch assembly can be an affordable and efficient way to turn your product ideas into reality.
Leave a Reply