Introduction to PCB Vias
Printed Circuit Boards (PCBs) are essential components in modern electronics. They provide a platform for mounting and interconnecting electronic components to create functional circuits. One crucial aspect of PCB design is the use of vias, which are small holes drilled through the board to establish electrical connections between different layers. Among the various types of vias, acid trap vias have gained significant attention due to their unique characteristics and benefits. In this comprehensive guide, we will delve into the world of acid trap PCB vias, exploring their design, manufacturing process, advantages, and best practices.
What are Acid Trap Vias?
Acid trap vias, also known as cup vias or barreled vias, are a specific type of via structure used in PCB fabrication. Unlike traditional through-hole vias that have a uniform diameter throughout the board, acid trap vias feature a larger diameter on one or both ends of the hole. This unique shape resembles a cup or barrel, hence the alternative names.
The key characteristic of acid trap vias is the presence of a conductive plating that covers the walls of the via hole. This plating is typically made of copper and is applied using an electroplating process. The plated walls create a reliable electrical connection between the layers of the PCB, enabling signals to pass through the via with minimal resistance and signal integrity issues.
Advantages of Acid Trap Vias
Acid trap vias offer several advantages over traditional through-hole vias, making them a preferred choice in certain PCB designs. Let’s explore some of the key benefits:
-
Increased Reliability: The plated walls of acid trap vias provide a robust and reliable electrical connection between the layers of the PCB. The larger diameter at the ends of the via helps to anchor the plating securely, reducing the risk of delamination or cracking during the manufacturing process or in harsh operating conditions.
-
Improved Signal Integrity: Acid trap vias minimize the discontinuity in the signal path, resulting in improved signal integrity. The smooth transition between the via and the connecting traces reduces reflections and impedance mismatches, which is particularly important for high-speed and high-frequency signals.
-
Enhanced Manufacturability: The unique shape of acid trap vias facilitates better plating coverage during the electroplating process. The larger diameter at the ends of the via allows for a more uniform distribution of the plating solution, resulting in a consistent and reliable plating thickness throughout the via.
-
Reduced Drill Breakout: Drill breakout occurs when the drill bit exits the bottom side of the PCB, potentially damaging the copper traces or pads. Acid trap vias help to mitigate this issue by providing a larger target area for the drill bit to exit, reducing the chances of breakout and improving the overall manufacturing yield.
-
Compatibility with High-Density Designs: Acid trap vias are well-suited for high-density PCB designs where space is limited. The larger diameter at the ends of the via allows for tighter via-to-via spacing without compromising the electrical integrity of the connections.
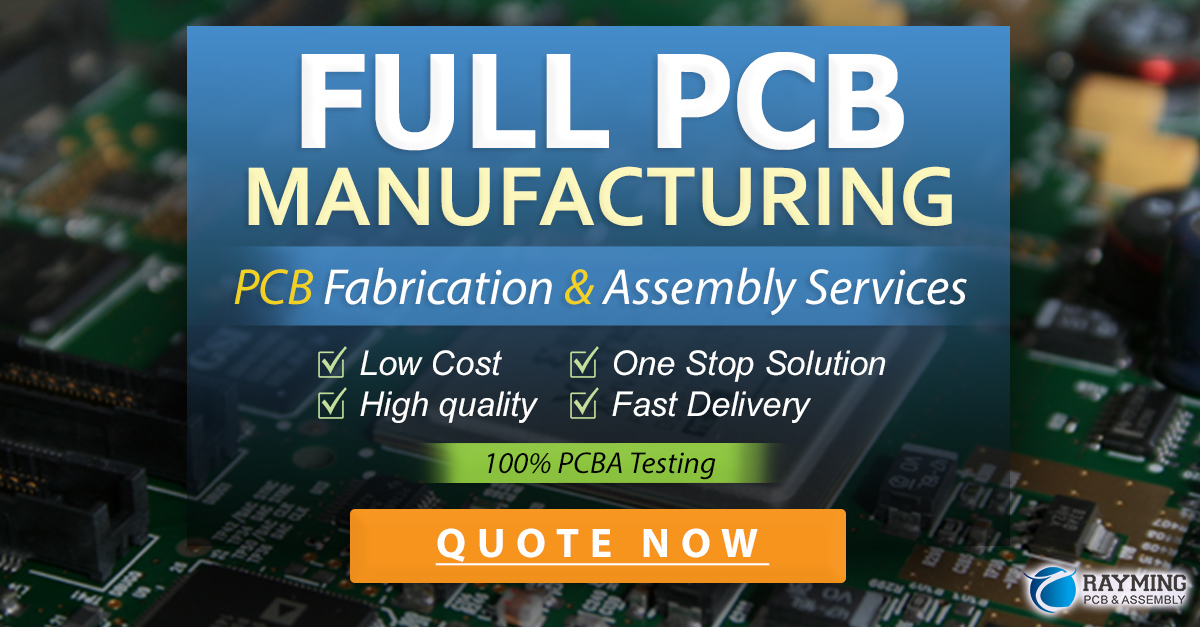
Manufacturing Process of Acid Trap Vias
The manufacturing process of acid trap vias involves several steps to achieve the desired shape and electrical characteristics. Let’s take a closer look at the key stages:
-
Drilling: The first step in creating acid trap vias is drilling holes through the PCB substrate. The drilling process is typically performed using high-speed CNC machines equipped with specialized drill bits. The diameter of the drill bit determines the size of the via hole.
-
Plating: Once the holes are drilled, the PCB undergoes an electroplating process to deposit a conductive layer, usually copper, onto the walls of the via holes. The plating process involves several sub-steps, including:
- Cleaning: The drilled holes are thoroughly cleaned to remove any debris and ensure proper adhesion of the plating.
- Activation: A thin layer of a catalytic material, such as palladium, is applied to the walls of the via holes to promote the electroplating process.
-
Electroplating: The PCB is immersed in an electroplating bath containing a copper sulfate solution. An electrical current is applied, causing the copper ions to adhere to the walls of the via holes, forming a uniform plating layer.
-
Etching: After plating, the PCB undergoes an etching process to remove the excess copper from the surface of the board, leaving only the desired copper traces and pads. The etching process can be done using various methods, such as chemical etching or plasma etching.
-
Finishing: Finally, the PCB may undergo additional finishing processes, such as applying a solder mask or surface finish, to protect the copper traces and improve solderability.
Here’s a table summarizing the manufacturing process of acid trap vias:
Step | Description |
---|---|
Drilling | Holes are drilled through the PCB substrate |
Plating | Conductive layer (copper) is deposited onto the via walls |
Etching | Excess copper is removed from the PCB surface |
Finishing | Additional protective and functional layers are applied |
Design Considerations for Acid Trap Vias
When designing PCBs with acid trap vias, there are several important considerations to keep in mind to ensure optimal performance and manufacturability. Let’s discuss some key design guidelines:
-
Via Diameter: The diameter of the acid trap via should be carefully selected based on the requirements of the PCB design. Factors such as the desired electrical characteristics, the thickness of the PCB, and the manufacturing capabilities of the PCB fabricator should be taken into account. Typically, acid trap vias have a larger diameter compared to traditional through-hole vias to accommodate the plating process.
-
Via Placement: The placement of acid trap vias should be strategically planned to minimize the impact on signal integrity and to ensure proper electrical connections between the layers of the PCB. Vias should be placed away from sensitive signal traces and should be evenly distributed to avoid clustering, which can lead to manufacturing challenges.
-
Pad Size: The pads surrounding the acid trap vias should be sized appropriately to provide sufficient space for the plating process and to ensure reliable soldering of components. The pad size should also consider the current carrying capacity and the thermal dissipation requirements of the via.
-
Aspect Ratio: The aspect ratio of an acid trap via refers to the ratio of the via depth to its diameter. A higher aspect ratio indicates a deeper via relative to its diameter. It is important to maintain an appropriate aspect ratio to ensure proper plating coverage and to avoid manufacturing issues such as drill wander or plating voids.
-
Clearance and Spacing: Adequate clearance and spacing should be maintained between acid trap vias and adjacent traces, components, and other vias. This helps to prevent short circuits, signal crosstalk, and manufacturing defects. The specific clearance and spacing requirements may vary depending on the PCB manufacturing process and the design rules provided by the PCB fabricator.
Here’s a table summarizing the key design considerations for acid trap vias:
Consideration | Description |
---|---|
Via Diameter | Select appropriate diameter based on design and manufacturing requirements |
Via Placement | Place vias strategically to minimize signal integrity issues |
Pad Size | Size pads appropriately for plating and soldering |
Aspect Ratio | Maintain appropriate ratio of via depth to diameter |
Clearance and Spacing | Ensure adequate clearance and spacing between vias and other elements |
Best Practices for Acid Trap Via Design
To optimize the performance and reliability of acid trap vias in your PCB design, consider the following best practices:
-
Collaborate with PCB Fabricator: Engage in early collaboration with your PCB fabricator to discuss their capabilities, design rules, and recommendations for acid trap via design. They can provide valuable insights and guidance based on their manufacturing processes and experience.
-
Use Simulation Tools: Utilize PCB simulation tools to analyze the electrical behavior of acid trap vias in your design. These tools can help you optimize the via placement, size, and spacing to minimize signal integrity issues and ensure optimal performance.
-
Follow Industry Standards: Adhere to industry standards and guidelines for via design, such as the IPC standards (e.g., IPC-2221, IPC-6012). These standards provide detailed specifications and requirements for various aspects of PCB design, including via dimensions, spacing, and manufacturing tolerances.
-
Document Design Specifications: Clearly document the design specifications for acid trap vias in your PCB layout files and fabrication drawings. Include information such as via diameter, pad size, plating requirements, and any specific manufacturing instructions. This helps to ensure accurate communication with the PCB fabricator and reduces the risk of manufacturing errors.
-
Perform Design Reviews: Conduct thorough design reviews to validate the placement and design of acid trap vias in your PCB layout. Involve relevant stakeholders, such as electrical engineers, PCB designers, and manufacturing experts, to identify potential issues and optimize the design for manufacturability and reliability.
Frequently Asked Questions (FAQ)
-
What is the difference between acid trap vias and traditional through-hole vias?
Acid trap vias have a larger diameter at one or both ends of the via hole, resembling a cup or barrel shape. They feature plated walls that provide a reliable electrical connection between the layers of the PCB. Traditional through-hole vias, on the other hand, have a uniform diameter throughout the board and may not have plated walls. -
What are the benefits of using acid trap vias in PCB design?
Acid trap vias offer several benefits, including increased reliability, improved signal integrity, enhanced manufacturability, reduced drill breakout, and compatibility with high-density designs. They provide a robust and reliable electrical connection between the layers of the PCB while minimizing signal integrity issues. -
How are acid trap vias manufactured?
The manufacturing process of acid trap vias involves drilling holes through the PCB substrate, electroplating the walls of the via holes with a conductive layer (usually copper), etching away the excess copper from the PCB surface, and applying additional finishing processes such as solder mask or surface finish. -
What factors should be considered when designing acid trap vias?
When designing acid trap vias, important factors to consider include via diameter, via placement, pad size, aspect ratio, and clearance and spacing. These factors influence the electrical performance, manufacturability, and reliability of the vias in the PCB design. -
How can I ensure the optimal performance and reliability of acid trap vias in my PCB design?
To ensure optimal performance and reliability of acid trap vias, collaborate with your PCB fabricator, use simulation tools to analyze the electrical behavior, follow industry standards and guidelines, clearly document design specifications, and perform thorough design reviews. These best practices help to minimize issues and optimize the design for manufacturability and reliability.
Conclusion
Acid trap vias are a valuable tool in PCB design, offering numerous advantages over traditional through-hole vias. By understanding the design considerations, manufacturing process, and best practices associated with acid trap vias, you can leverage their benefits to create robust and reliable PCB designs.
When designing PCBs with acid trap vias, it is crucial to collaborate with your PCB fabricator, follow industry standards, and utilize simulation tools to optimize the design for performance and manufacturability. By adhering to best practices and carefully considering factors such as via diameter, placement, pad size, aspect ratio, and clearance, you can ensure the successful implementation of acid trap vias in your PCB projects.
As technology continues to advance and electronics become more compact and complex, the use of acid trap vias will likely remain a key strategy in PCB design. By staying informed about the latest developments and techniques in acid trap via design, you can stay ahead of the curve and create PCBs that meet the demanding requirements of modern electronic devices.
Leave a Reply