Introduction to PCB Prototyping
PCB prototyping is an essential step in the development of electronic devices. It involves creating a physical representation of the designed circuit board to test its functionality, identify any flaws, and make necessary improvements before mass production. In this article, we will discuss eight crucial matters you need to pay attention to when it comes to PCB prototyping.
1. Design Verification
The first matter to consider in PCB prototyping is design verification. It is essential to ensure that the design of your PCB is accurate and meets all the required specifications. This includes checking the schematic, component placement, routing, and any other design aspects. Verifying the design helps to identify any errors or potential issues early in the prototyping process, saving time and resources.
Design Verification Checklist
Item | Description |
---|---|
Schematic Review | Check the schematic for accuracy and completeness |
Component Placement | Verify the placement of components on the PCB layout |
Routing | Ensure proper routing of traces and vias |
Design Rule Check (DRC) | Run DRC to identify any design rule violations |
Electrical Rule Check (ERC) | Perform ERC to detect electrical issues in the design |
2. Component Selection
Choosing the right components for your PCB Prototype is crucial. It is important to select components that are readily available, reliable, and meet the required specifications. Consider factors such as package size, power rating, and temperature range when selecting components. It is also advisable to have backup options in case of component shortages or obsolescence.
Component Selection Factors
Factor | Consideration |
---|---|
Availability | Choose components that are readily available and have multiple suppliers |
Reliability | Select components with proven reliability and quality |
Specifications | Ensure components meet the required electrical and mechanical specifications |
Package Size | Consider the package size and footprint of components for optimal board layout |
Power Rating | Choose components with appropriate power ratings for the application |
Temperature Range | Select components that can operate within the expected temperature range |
3. PCB Fabrication
The fabrication process is a critical aspect of PCB prototyping. It involves the actual manufacturing of the PCB based on the designed layout. When selecting a PCB fabrication service, consider factors such as lead time, cost, quality, and capabilities. It is important to communicate clearly with the fabrication house regarding your requirements and specifications to ensure a smooth and accurate fabrication process.
PCB Fabrication Considerations
Consideration | Description |
---|---|
Lead Time | Choose a fabrication service that can meet your prototyping timeline |
Cost | Consider the cost of fabrication and any additional services required |
Quality | Ensure the fabrication house has a track record of producing high-quality PCBs |
Capabilities | Verify that the fabrication service can handle your PCB’s specifications and requirements |
Communication | Maintain clear communication with the fabrication house regarding your expectations and requirements |
4. Assembly and Soldering
Once the PCB is fabricated, the next step is to assemble and solder the components onto the board. This process requires careful attention to detail and proper techniques to ensure a reliable and functional prototype. Consider the following aspects when it comes to assembly and soldering:
- Component Placement: Ensure that components are placed accurately and in the correct orientation on the PCB.
- Soldering Technique: Use appropriate soldering techniques, such as hand soldering or reflow soldering, depending on the components and board design.
- Solder Joint Quality: Inspect the solder joints for proper formation, wetting, and absence of defects like bridging or cold joints.
- Cleaning: Clean the PCB after soldering to remove any flux residue or contaminants that may affect the board’s performance.
Soldering Defects and Their Causes
Defect | Cause |
---|---|
Bridging | Excessive solder, improper soldering technique |
Cold Joint | Insufficient heat, poor solder wetting |
Tombstoning | Uneven heating, component misalignment |
Solder Balls | Excessive solder, contamination |
Insufficient Solder | Inadequate solder, poor solder wetting |
5. Testing and Debugging
After assembly, it is crucial to thoroughly test and debug the PCB prototype to ensure its functionality and performance. This involves applying power to the board, verifying the operation of individual components, and testing the overall system. Use appropriate test equipment, such as multimeters, oscilloscopes, and logic analyzers, to diagnose and troubleshoot any issues that may arise.
Common Testing Methods
Method | Description |
---|---|
Visual Inspection | Visually examine the PCB for any obvious defects or assembly issues |
Continuity Test | Check for proper electrical connections between components and traces |
Power-On Test | Apply power to the board and verify proper voltage levels and current consumption |
Functional Test | Test the functionality of individual components and subsystems |
System Test | Evaluate the overall performance and functionality of the complete system |
6. Prototype Iterations
PCB prototyping is often an iterative process. Based on the results of testing and debugging, you may need to make modifications to the design, components, or assembly process. It is important to document any changes made and maintain version control to track the progress of your prototype. Be prepared to go through multiple iterations until you achieve a fully functional and optimized PCB prototype.
7. Documentation
Proper documentation is essential throughout the PCB prototyping process. Maintain detailed records of the design files, component specifications, assembly instructions, and test results. This documentation will serve as a reference for future iterations, troubleshooting, and eventual mass production. It also helps in communicating the design intent and requirements to team members and manufacturers.
Documentation Checklist
Item | Description |
---|---|
Schematic | Updated schematic with any modifications made during prototyping |
PCB Layout | Final PCB layout files, including Gerber files and drill files |
Bill of Materials (BOM) | Complete list of components used in the prototype, including part numbers and quantities |
Assembly Instructions | Step-by-step instructions for assembling the PCB prototype |
Test Procedures | Detailed procedures for testing and debugging the prototype |
Test Results | Recorded results of various tests performed on the prototype |
Change Log | Documentation of any modifications made during the prototyping process |
8. Collaboration and Communication
Effective collaboration and communication are key to successful PCB prototyping. Involve all relevant stakeholders, such as designers, engineers, manufacturers, and end-users, in the prototyping process. Regularly communicate progress, challenges, and updates to ensure everyone is on the same page. Foster a collaborative environment where ideas can be shared, and feedback can be incorporated to improve the prototype.
Frequently Asked Questions (FAQ)
-
What is the purpose of PCB prototyping?
PCB prototyping is done to create a physical representation of the designed circuit board to test its functionality, identify any flaws, and make necessary improvements before mass production. -
How do I select the right components for my PCB prototype?
When selecting components for your PCB prototype, consider factors such as availability, reliability, specifications, package size, power rating, and temperature range. It is also advisable to have backup options in case of component shortages or obsolescence. -
What should I look for when choosing a PCB fabrication service?
When selecting a PCB fabrication service, consider factors such as lead time, cost, quality, and capabilities. Ensure that the fabrication house can meet your prototyping timeline, produce high-quality PCBs, and handle your PCB’s specifications and requirements. -
What are some common soldering defects to watch out for during PCB assembly?
Common soldering defects include bridging (excessive solder or improper soldering technique), cold joints (insufficient heat or poor solder wetting), tombstoning (uneven heating or component misalignment), solder balls (excessive solder or contamination), and insufficient solder (inadequate solder or poor solder wetting). -
Why is documentation important in PCB prototyping?
Proper documentation serves as a reference for future iterations, troubleshooting, and eventual mass production. It helps in communicating the design intent and requirements to team members and manufacturers. Maintain detailed records of the design files, component specifications, assembly instructions, and test results throughout the prototyping process.
Conclusion
PCB prototyping is a critical step in the development of electronic devices. By paying attention to the eight matters discussed in this article – design verification, component selection, PCB fabrication, assembly and soldering, testing and debugging, prototype iterations, documentation, and collaboration and communication – you can ensure a successful and efficient prototyping process. Remember to be thorough, attentive to detail, and open to feedback and improvements throughout the prototyping journey.
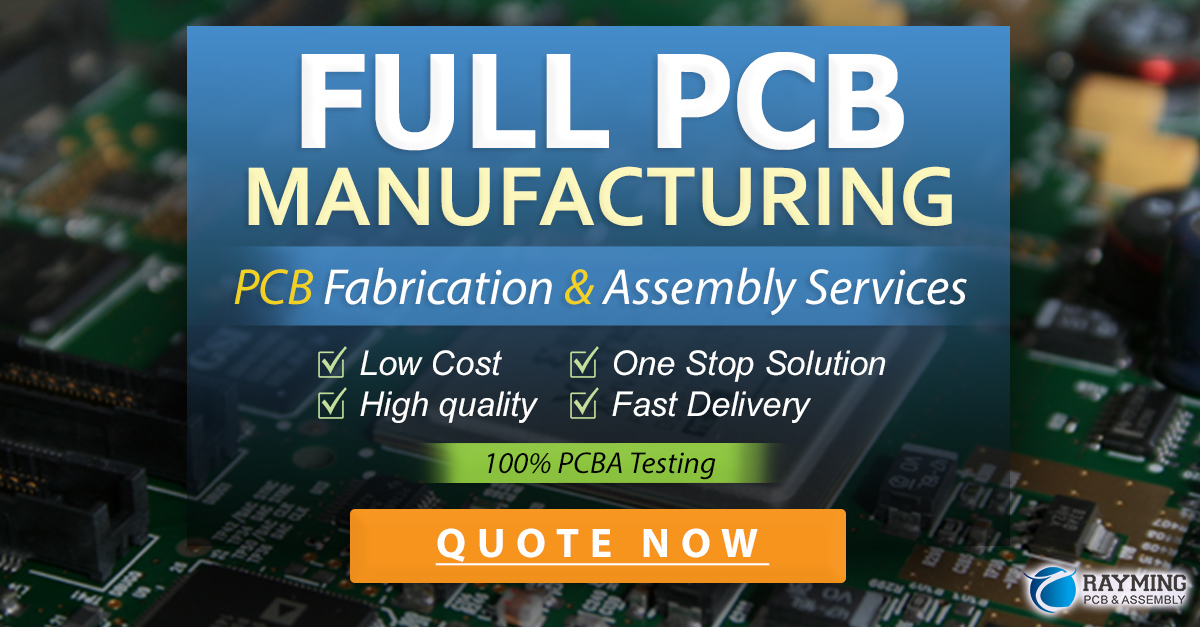
Leave a Reply