What is FR4?
FR4 is a composite material made of woven fiberglass cloth impregnated with an epoxy resin. The “FR” in FR4 stands for “Flame Retardant,” indicating its ability to resist the spread of flames in case of a fire. The number “4” represents the specific grade of the material, which is determined by the composition of the epoxy resin and the type of fiberglass used.
FR4 is the most common substrate material for PCBs due to its excellent mechanical, electrical, and thermal properties. It offers good insulation, high strength, and dimensional stability, making it suitable for a wide range of applications, from consumer electronics to industrial equipment.
Thermal Conductivity of FR4
Definition and Importance
Thermal conductivity is a material property that describes its ability to conduct heat. It is defined as the rate at which heat is transferred through a material per unit thickness, per unit area, and per unit temperature difference. The thermal conductivity of a material is expressed in watts per meter-kelvin (W/mK) or watts per meter-degree Celsius (W/m°C).
In the context of PCBs, thermal conductivity is crucial for effectively dissipating heat generated by electronic components. As electronic devices become more compact and powerful, the heat generated by components increases, which can lead to performance issues, reduced reliability, and even failure if not managed properly. A material with higher thermal conductivity allows heat to be transferred more efficiently, helping to maintain the temperature of the components within safe operating limits.
Typical Values and Comparison with Other Materials
The thermal conductivity of FR4 is relatively low compared to other materials used in electronics. The typical thermal conductivity of FR4 ranges from 0.25 to 0.4 W/mK, depending on the specific composition and manufacturing process.
To put this into perspective, let’s compare the thermal conductivity of FR4 with other common materials:
Material | Thermal Conductivity (W/mK) |
---|---|
FR4 | 0.25 – 0.4 |
Aluminum | 205 |
Copper | 401 |
Thermal Interface Materials (TIMs) | 1 – 10 |
Air | 0.026 |
As evident from the table, FR4 has a significantly lower thermal conductivity than metals like aluminum and copper, which are often used for heat sinks and thermal management solutions. However, FR4 is still a better thermal conductor than air, which is a poor conductor of heat.
Factors Affecting FR4 Thermal Conductivity
Several factors can influence the thermal conductivity of FR4, including:
Manufacturing Process
The manufacturing process of FR4 can impact its thermal conductivity. The quality and consistency of the fiberglass weave, the ratio of resin to fiberglass, and the curing process can all affect the thermal properties of the material. Variations in the manufacturing process can lead to differences in thermal conductivity between different batches of FR4.
Resin Composition
The composition of the epoxy resin used in FR4 can also affect its thermal conductivity. Different types of epoxy resins have varying thermal properties, and the addition of fillers or other additives can modify the thermal conductivity of the material.
Fiberglass Content
The fiberglass content in FR4 plays a role in its thermal conductivity. Fiberglass itself has a relatively low thermal conductivity, and increasing the fiberglass content in the composite can decrease the overall thermal conductivity of FR4. However, the fiberglass content also affects other properties like mechanical strength and dimensional stability, so a balance must be struck between thermal performance and other requirements.
Thickness and Copper Coverage
The thickness of the FR4 substrate and the amount of copper coverage on the PCB can also impact thermal conductivity. Thicker FR4 substrates provide more insulation and can limit heat transfer, while higher copper coverage can improve heat spreading across the board. The design and layout of the PCB must consider these factors to optimize thermal management.
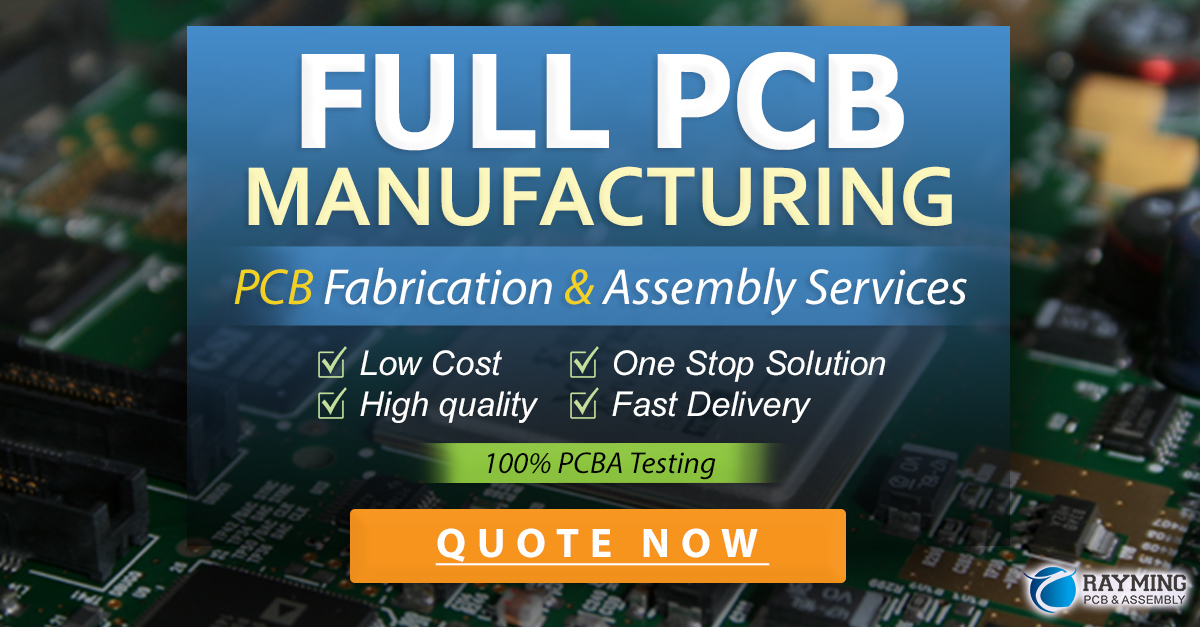
Methods to Improve FR4 Thermal Conductivity
While the inherent thermal conductivity of FR4 is relatively low, several methods can be employed to enhance heat dissipation in PCBs:
Thermal Vias
Thermal vias are plated through-holes that are strategically placed on the PCB to transfer heat from the components to the other side of the board or to a heat sink. By creating a low-resistance thermal path, thermal vias can effectively conduct heat away from hot spots on the PCB.
Metal Core PCBs
Metal core PCBs (MCPCBs) are a variation of traditional PCBs that incorporate a metal substrate, typically aluminum, as the base layer. The metal substrate has a much higher thermal conductivity than FR4, allowing for better heat dissipation. MCPCBs are often used in applications with high power densities or where thermal management is critical.
Thermal Interface Materials
Thermal interface materials (TIMs) are materials that are applied between the PCB and a heat sink or other cooling solution to enhance thermal transfer. TIMs, such as thermal pads, thermal pastes, or thermal adhesives, help to fill the microscopic air gaps between the surfaces, improving thermal conductivity and heat dissipation.
PCB Design Optimization
Proper PCB design and layout can also contribute to improved thermal management. This includes optimizing component placement to avoid hot spots, using wider traces for high-current paths, and incorporating thermal relief pads for heat-generating components. Simulation tools can be used to analyze the thermal behavior of the PCB and identify areas for improvement.
Frequently Asked Questions (FAQ)
-
Q: What is the typical thermal conductivity range of FR4?
A: The typical thermal conductivity of FR4 ranges from 0.25 to 0.4 W/mK, depending on the specific composition and manufacturing process. -
Q: How does the thermal conductivity of FR4 compare to other materials used in electronics?
A: FR4 has a significantly lower thermal conductivity compared to metals like aluminum (205 W/mK) and copper (401 W/mK), but it is still a better thermal conductor than air (0.026 W/mK). -
Q: Can the manufacturing process affect the thermal conductivity of FR4?
A: Yes, the manufacturing process can impact the thermal conductivity of FR4. Factors such as the quality and consistency of the fiberglass weave, the ratio of resin to fiberglass, and the curing process can all affect the thermal properties of the material. -
Q: What are some methods to improve the thermal conductivity of FR4 in PCBs?
A: Some methods to improve the thermal conductivity of FR4 in PCBs include using thermal vias, incorporating metal core substrates (MCPCBs), applying thermal interface materials (TIMs), and optimizing the PCB design and layout. -
Q: How can proper PCB design contribute to better thermal management?
A: Proper PCB design can contribute to better thermal management by optimizing component placement to avoid hot spots, using wider traces for high-current paths, incorporating thermal relief pads for heat-generating components, and utilizing simulation tools to analyze and improve the thermal behavior of the PCB.
Conclusion
FR4 thermal conductivity is a critical property that affects the performance and reliability of electronic devices. While FR4 has a relatively low thermal conductivity compared to other materials, understanding the factors that influence its thermal behavior and employing various methods to enhance heat dissipation can help to ensure the proper functioning and longevity of PCBs.
By considering the manufacturing process, resin composition, fiberglass content, and PCB design, engineers can optimize the thermal management of FR4-based PCBs. Techniques such as using thermal vias, metal core substrates, thermal interface materials, and design optimization can significantly improve the thermal performance of the PCB.
As electronic devices continue to advance in terms of power density and miniaturization, the importance of effective thermal management will only continue to grow. A comprehensive understanding of FR4 thermal conductivity and the strategies to enhance it will be essential for designing reliable and high-performance electronic systems.
Leave a Reply