Main Components of a Custom Drone Board
At the heart of any custom drone board are the following critical components:
1. Flight Controller Chip
The flight controller is the main processor that runs the software and algorithms to keep the drone stable and flying as commanded. Some of the most popular flight controller chips used in custom drone builds include:
Chip | Description |
---|---|
STM32F4 | High-performance ARM Cortex-M4 microcontroller commonly used in flight controllers like the Pixhawk and Naze32. |
STM32F7 | Higher-end ARM Cortex-M7 microcontroller with faster processing and more memory, used in advanced flight controllers. |
ATmega2560 | 8-bit AVR microcontroller used in simpler flight controllers like the Arduino-based MultiWii and APM boards. |
The flight controller chip interfaces with all the drone’s sensors, runs the stabilization loops and PID controllers, processes commands from the pilot’s transmitter, and sends outputs to the electronic speed controllers (ESCs) and motors.
2. Inertial Measurement Unit (IMU)
The IMU is a critical sensor that measures the drone’s angular velocity and linear acceleration using a combination of gyroscopes and accelerometers. This data is fused together by the flight controller to estimate the drone’s attitude (roll, pitch, yaw) and perform auto-leveling. Some of the most commonly used IMU chips in drone boards include:
IMU | DOF | Description |
---|---|---|
MPU6000 | 6 | Basic 6-axis gyro + accelerometer, widely used in older flight controllers. |
MPU6050 | 6 | Upgraded version of MPU6000 with better temperature stability and built-in 16-bit ADCs. |
MPU9250 | 9 | 9-axis IMU that combines gyro, accelerometer and magnetometer in a single chip. Used in Pixhawk controllers. |
BMI055 | 6 | High-end 6-axis gyro + accelerometer with excellent vibration rejection, used in advanced controllers. |
Having a high-quality, low-noise IMU is essential for a drone to maintain stable flight. Most custom drone boards include built-in vibration damping for the IMU.
3. Barometer
A barometric pressure sensor allows the drone to estimate its altitude above ground level for auto-takeoff, landing and altitude hold flight modes. The most common barometer used in custom drone boards is the MS5611, which offers high resolution and a wide measurement range.
4. GPS Module
For autonomous waypoint navigation and position hold, a custom drone board needs to include a GPS module. The most popular option is the Ublox NEO-M8N, which provides high accuracy position and velocity measurements. The GPS module interfaces with the flight controller via a serial UART connection.
5. Magnetometer
A 3-axis magnetometer measures Earth’s magnetic field to provide a compass heading reference to the flight controller. This is needed for autonomous flights and yaw control in windy conditions. The most commonly used magnetometer chip is the HMC5883L. Some drone boards may use a higher-end 9-axis IMU like the MPU9250 that includes a built-in magnetometer.
6. RC Inputs
A custom drone board needs a way to receive control signals and commands from the pilot’s radio transmitter. The most common RC input protocols are:
-
PWM (Pulse Width Modulation) – Each RC channel is connected to a separate pin on the flight controller, which measures the width of the incoming pulses. Supports up to 8 channels.
-
PPM (Pulse Position Modulation) – The RC channels are encoded into a single signal wire, allowing for more than 8 channels over a single pin. Requires a PPM encoder module.
-
SBUS – A digital serial protocol that can send up to 16 channels over a single signal wire. Commonly used with FrSky receivers.
The choice of RC input depends on the transmitter and receiver being used and the number of channels needed (e.g. a drone with GPS and a gimbal may need 8+ channels).
7. Power Module
A power distribution board is used to safely power the flight controller and ESCs from the drone’s main battery pack (usually 3S or 4S LiPo). It includes voltage regulators to step down the battery voltage to 5V for the flight controller and other low-voltage components. The power module also includes current and voltage sensors so the flight controller can monitor the battery’s health and remaining capacity.
Additional Features and Sensors
Beyond the core components, a custom drone board may include additional sensors and interfaces such as:
- Optical flow sensor – Measures the drone’s velocity relative to the ground for position hold without GPS.
- Rangefinder – Ultrasonic or laser distance sensor for precision auto-landing.
- Airspeed sensor – Pitot tube sensor for measuring airspeed, used in fixed-wing drones.
- Video input – For connecting FPV cameras and video downlink transmitters.
- Audio buzzer – For audio warnings and feedback.
- Status LEDs – To visually indicate the armed/disarmed status and flight mode.
- SD card slot – For logging flight data and parameters.
- USB port – For connecting to a computer for configuration and firmware updates.
The choice of which additional sensors to include depends on the specific requirements and intended use case for the custom drone build.
Custom Drone Board Firmware
The final key component of a custom drone board is the firmware that runs on the flight controller. This firmware implements all the stabilization and control algorithms, sensor fusion, RC input decoding, and autonomous flight features. The most popular open-source firmware options for custom drone boards are:
1. Betaflight
Betaflight is a highly optimized firmware for racing and freestyle drones. It offers excellent flight performance, a wide range of configuration options, and an intuitive user interface. Betaflight supports a variety of flight controllers and is known for its active development and frequent feature updates.
2. ArduPilot
ArduPilot is a versatile autopilot firmware that supports a wide range of vehicles beyond just multirotors, including fixed-wing planes, helicopters, rovers, and boats. It offers advanced autonomous flight modes, mission planning, and integration with ground control station software. ArduPilot runs on the Pixhawk series of flight controllers.
3. PX4
PX4 is a professional-grade autopilot firmware that offers a complete ecosystem of drone software, including a ground control station (QGroundControl), simulation tools, and developer APIs. PX4 is known for its reliability, safety features, and extensive documentation. It is commonly used in commercial and industrial drone applications.
4. INAV
INAV (INertial NAVigation) is a fork of Cleanflight firmware that adds GPS and barometer support for autonomous flying. It is a good choice for long-range and outdoor drones that need position hold and waypoint navigation capabilities.
5. Kiss
Kiss is a racing drone firmware known for its ease of use, smooth flight feel, and responsive controls. It has a smaller user base than Betaflight but is popular among some professional pilots. Kiss offers a polished user interface and supports a limited selection of flight controllers.
The choice of firmware depends on the type of drone being built, the desired flight characteristics, and the level of autonomous flight capabilities needed. Many custom drone boards are compatible with multiple firmware options, allowing users to switch between them as needed.
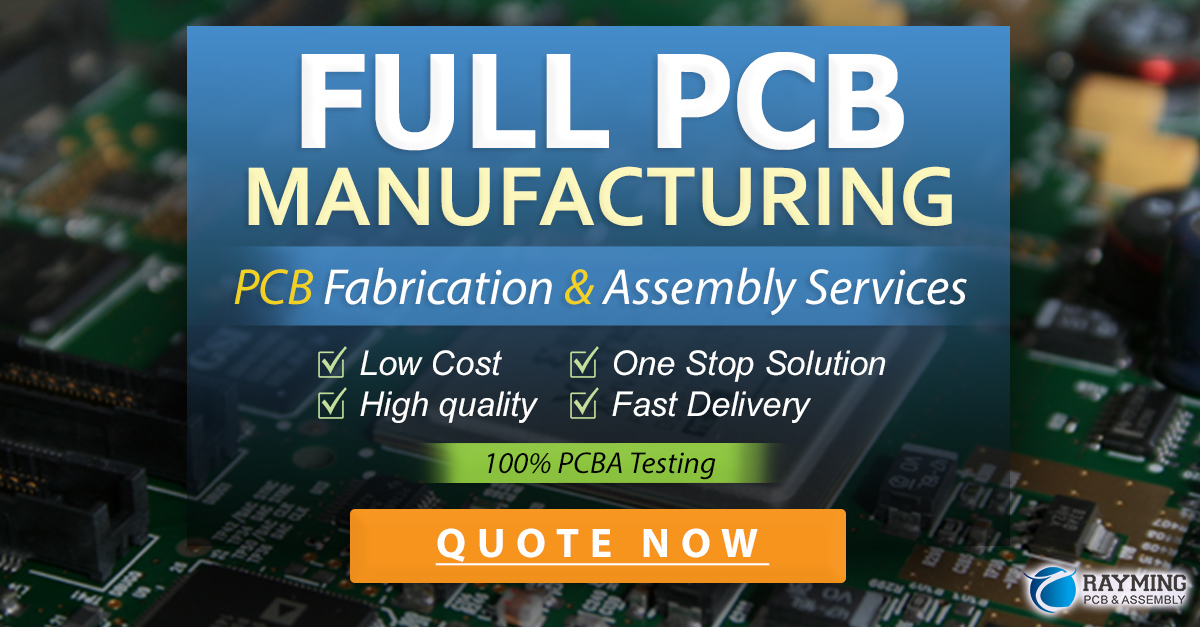
Design Considerations for Custom Drone Boards
When designing a custom drone board, there are several key factors to consider:
- Size and form factor – The board needs to fit within the desired frame size and mounting pattern. Smaller drones may require more compact boards.
- Weight – Minimizing the board’s weight is important for maximizing flight time and performance, especially in racing drones.
- Connectivity – Ensure the board has sufficient I/O pins and connectors for all the required sensors, RC input, and other peripherals.
- Power – Choose voltage regulators and power components that can handle the expected current draw of the motors and other high-power devices.
- Reliability – Use high-quality components and implement proper circuit protection (e.g. reverse polarity protection, over-current protection) to ensure reliable operation.
- Cost – Select components that balance performance and cost based on the target budget for the drone build.
- Compatibility – Make sure the board is compatible with the desired firmware and supports the necessary sensors and features for the intended use case.
PCB Layout and Assembly
Once the schematic design of the custom drone board is finalized, the next step is to create the PCB (printed circuit board) layout. Key considerations for the PCB layout include:
- Component placement – Arrange the components in a logical and space-efficient manner, taking into account signal routing and potential EMI (electromagnetic interference) issues.
- Grounding – Use proper grounding techniques, such as ground planes and star grounding, to minimize noise and ensure stable operation.
- Trace widths – Size the PCB traces appropriately based on the expected current for each signal. High-current traces for the battery and motor outputs need to be wider.
- Mounting holes – Include mounting holes that match the desired frame pattern and provide sufficient mechanical strength.
- Connector placement – Position the connectors in an accessible manner that allows for easy wiring and cable management.
After the PCB layout is complete, the board can be manufactured and assembled. Many online PCB fabrication services offer affordable low-volume production runs for custom designs. The components can be hand-soldered or assembled using automated pick-and-place machines for higher volumes.
Testing and Quality Control
Before using a custom drone board in a build, it is important to thoroughly test it to ensure proper functionality and reliability. Key tests to perform include:
- Continuity – Check for any short circuits or open connections using a multimeter.
- Power-up – Apply power to the board and verify that all the voltage rails are at the expected levels.
- Sensor communication – Connect the board to a computer and verify that all the sensors are detected and communicating properly using the firmware’s configuration tools.
- RC input – Test the RC input connection by checking that the board responds to transmitter stick movements.
- Motor outputs – Connect the ESCs and motors and perform a motor test to ensure that each motor spins up and responds to throttle correctly.
- Flight testing – Perform cautious incremental flight tests to validate the board’s performance and tune the stabilization parameters as needed.
By thoroughly testing the custom drone board before putting it into service, potential issues can be caught early and addressed before they cause failures or crashes during flight.
Frequently Asked Questions (FAQ)
1. What is the difference between a flight controller and a custom drone board?
A flight controller refers specifically to the main processor chip that runs the stabilization and control algorithms, while a custom drone board is the complete PCB assembly that includes the flight controller along with all the necessary sensors, power components, and peripherals.
2. Can I use a custom drone board with any frame and motors?
In general, a well-designed custom drone board should be compatible with a wide range of frames and motors, as long as they match the size, mounting pattern, and power requirements of the board. However, it is important to ensure that the frame and motors are appropriate for the intended use case and are compatible with the selected firmware.
3. How do I choose the right firmware for my custom drone board?
The choice of firmware depends on the type of drone you are building and your desired flight characteristics and features. For racing and freestyle drones, Betaflight and Kiss are popular choices. For autonomous and long-range drones, ArduPilot and PX4 offer advanced navigation and mission planning capabilities. INAV is a good middle ground for GPS-enabled drones that still prioritize smooth flight performance.
4. What tools do I need to assemble and configure a custom drone board?
To assemble a custom drone board, you will need basic soldering equipment, including a soldering iron, solder, and tweezers. For configuring the board and updating the firmware, you will need a computer with a USB port and the appropriate configuration software for your selected firmware (e.g. Betaflight Configurator, Mission Planner, QGroundControl).
5. How much does it cost to build a custom drone with a custom board?
The cost of building a custom drone with a custom board can vary widely depending on the components used and the intended use case. A basic racing drone build with a custom board can cost around $200-300, while a high-end professional drone with advanced sensors and features can easily exceed $1000. The custom board itself may cost anywhere from $50 to $200 or more, depending on the complexity and features included. Budget $100 to $300 for a well-equipped board suitable for most DIY builds.
In conclusion, the core of a custom drone board revolves around the central flight controller chip, essential sensors like the IMU, and the firmware that ties everything together. By understanding the key components and design considerations involved in creating a custom drone board, you can unlock the full potential of your DIY drone builds and tailor them to your specific needs and preferences. Whether you are building a nimble racing drone, a stable aerial photography platform, or a fully autonomous mapping drone, a well-designed custom board is the foundation of a successful and rewarding project.
Leave a Reply