Introduction to PCBs
Printed Circuit Boards (PCBs) are the backbone of modern electronics. They are used in almost every electronic device, from smartphones and laptops to medical equipment and aerospace systems. PCBs are designed to mechanically support and electrically connect electronic components using conductive tracks, pads, and other features etched from copper sheets laminated onto a non-conductive substrate.
Types of PCBs
There are several types of PCBs, each with its own unique characteristics and applications:
-
Single-sided PCBs: These PCBs have conductive tracks on only one side of the substrate. They are the simplest and most cost-effective type of PCB, suitable for low-complexity circuits.
-
Double-sided PCBs: These PCBs have conductive tracks on both sides of the substrate, allowing for more complex circuits and higher component density compared to single-sided PCBs.
-
Multi-layer PCBs: These PCBs consist of multiple layers of conductive tracks and insulating substrates, enabling even higher component density and more complex circuits. They are commonly used in advanced electronic devices.
-
Flexible PCBs: These PCBs are made from flexible materials, allowing them to bend and conform to various shapes. They are often used in wearable electronics and applications where space is limited.
-
Rigid-Flex PCBs: These PCBs combine the benefits of rigid and flexible PCBs, featuring both rigid and flexible sections. They are used in applications that require both stability and flexibility.
What is HDI?
High Density Interconnect (HDI) is a type of PCB that offers higher component density and more complex circuitry than traditional PCBs. HDI PCBs are characterized by their fine line width and spacing, small vias, and high layer count. These features allow for the miniaturization of electronic devices and improved signal integrity.
Advantages of HDI PCBs
HDI PCBs offer several advantages over traditional PCBs:
-
Miniaturization: HDI PCBs enable the design of smaller, more compact electronic devices, which is crucial in today’s market where consumers demand ever-smaller gadgets.
-
Improved signal integrity: The fine line width and spacing of HDI PCBs reduce signal interference and crosstalk, resulting in better signal integrity and overall performance.
-
Higher component density: HDI PCBs can accommodate more components per unit area, allowing for more complex circuits and functionality in a smaller footprint.
-
Reduced power consumption: The shorter signal paths in HDI PCBs lead to reduced power consumption, which is essential for battery-powered devices and energy-efficient systems.
-
Cost-effective: Although HDI PCBs may have a higher initial cost compared to traditional PCBs, they can be more cost-effective in the long run due to their ability to reduce the overall size and complexity of electronic devices.
HDI PCB Design Considerations
Designing HDI PCBs requires careful consideration of several factors:
-
Material selection: Choose high-quality, high-performance materials that can withstand the demands of HDI manufacturing processes and ensure reliable performance.
-
Layout and routing: Optimize the layout and routing of components and traces to minimize signal interference and maximize performance.
-
Via design: Use micro vias and buried vias to maximize space utilization and minimize signal path length.
-
Manufacturing process: Select a reputable PCB manufacturer with experience in HDI fabrication to ensure high-quality results.
HDI PCB Applications
HDI PCBs are used in a wide range of applications, including:
-
Smartphones and tablets: The miniaturization and high functionality demands of modern mobile devices make HDI PCBs an ideal choice.
-
Wearable electronics: HDI PCBs are essential for creating compact, lightweight, and flexible wearable devices.
-
Medical devices: HDI PCBs are used in advanced medical equipment, such as implantable devices and diagnostic tools, where reliability and miniaturization are critical.
-
Aerospace and defense: HDI PCBs are employed in high-performance aerospace and defense systems, where weight reduction and signal integrity are paramount.
-
Automotive electronics: As vehicles become more technologically advanced, HDI PCBs play a crucial role in enabling sophisticated features and functions.
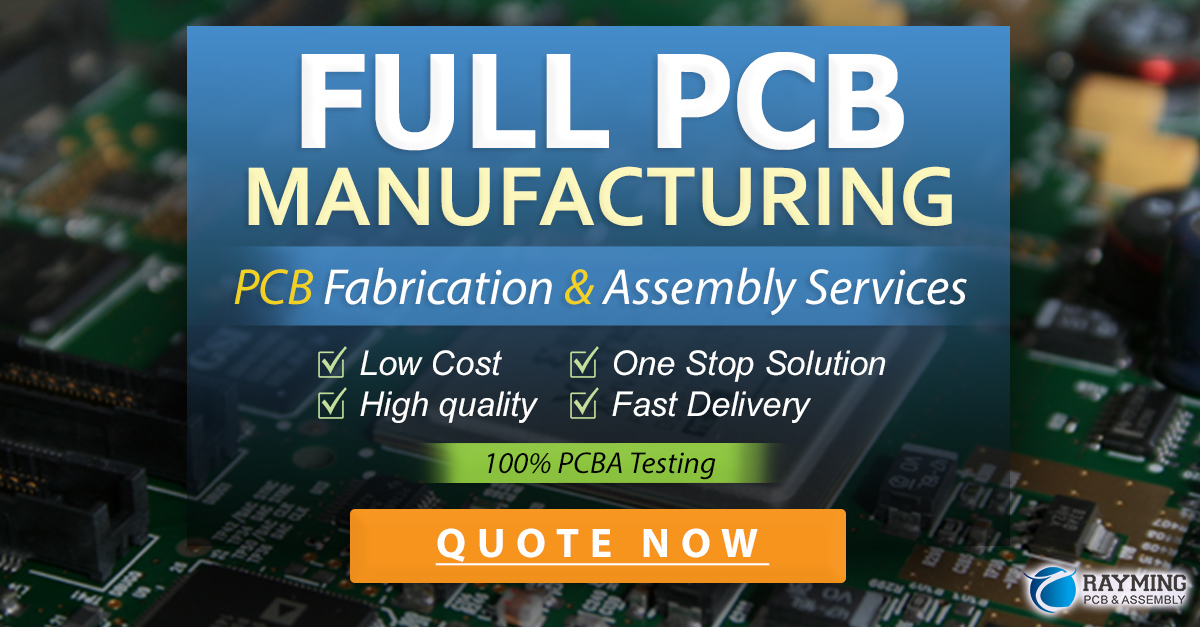
HDI PCB Manufacturing Process
The manufacturing process for HDI PCBs involves several steps:
-
Material preparation: The substrate material is cut to size, and the copper foil is laminated onto the substrate.
-
Drilling: Micro vias and through-holes are drilled into the substrate using laser or mechanical drilling techniques.
-
Patterning: The desired circuit pattern is transferred onto the copper foil using photolithography or direct imaging methods.
-
Etching: The unwanted copper is removed using chemical etching, leaving behind the desired conductive tracks and pads.
-
Lamination: Multiple layers of patterned substrates are laminated together to form the complete HDI PCB stack-up.
-
Surface finish: A protective surface finish, such as ENIG (Electroless Nickel Immersion Gold) or HASL (Hot Air Solder Leveling), is applied to the exposed copper surfaces to prevent oxidation and improve solderability.
-
Electrical testing: The completed HDI PCB undergoes rigorous electrical testing to ensure proper functionality and adherence to design specifications.
Comparing HDI PCBs with Traditional PCBs
Feature | HDI PCBs | Traditional PCBs |
---|---|---|
Line width and spacing | Fine (≤ 3 mils) | Coarse (≥ 4 mils) |
Via size | Small (≤ 6 mils) | Large (≥ 8 mils) |
Layer count | High (≥ 8) | Low (≤ 6) |
Component density | High | Low |
Signal integrity | Excellent | Good |
Power consumption | Low | Moderate |
Cost | Higher | Lower |
Applications | Advanced | General |
Frequently Asked Questions (FAQ)
-
Q: What is the main difference between HDI PCBs and traditional PCBs?
A: The main difference lies in the line width, spacing, via size, and layer count. HDI PCBs have finer features, smaller vias, and higher layer counts, enabling higher component density and better signal integrity compared to traditional PCBs. -
Q: Are HDI PCBs more expensive than traditional PCBs?
A: Yes, HDI PCBs typically have a higher initial cost due to the advanced manufacturing processes and materials required. However, they can be more cost-effective in the long run by enabling the miniaturization and simplification of electronic devices. -
Q: What are the main applications of HDI PCBs?
A: HDI PCBs are widely used in applications that require high functionality, miniaturization, and reliability, such as smartphones, wearable electronics, medical devices, aerospace and defense systems, and automotive electronics. -
Q: What are the key design considerations for HDI PCBs?
A: When designing HDI PCBs, it is essential to carefully consider material selection, layout and routing optimization, via design, and the choice of a reputable manufacturer with experience in HDI fabrication. -
Q: What are the main advantages of using HDI PCBs?
A: The main advantages of HDI PCBs include miniaturization, improved signal integrity, higher component density, reduced power consumption, and cost-effectiveness in the long run.
Conclusion
HDI PCBs are a game-changer in the world of electronics, offering numerous advantages over traditional PCBs. Their ability to enable the miniaturization of electronic devices, improve signal integrity, and increase component density makes them an ideal choice for a wide range of advanced applications. As technology continues to evolve and the demand for smaller, more powerful devices grows, HDI PCBs will undoubtedly play an increasingly critical role in shaping the future of electronics.
When designing and manufacturing HDI PCBs, it is crucial to partner with experienced professionals who can guide you through the process and ensure the highest quality results. By understanding the unique characteristics and benefits of HDI PCBs and following best practices in design and manufacturing, you can unlock the full potential of this innovative technology and create electronic devices that push the boundaries of what is possible.
Leave a Reply