What is a Hydrogen Sensor?
A hydrogen sensor is a device that detects the presence of hydrogen gas in the surrounding environment. It is designed to measure the concentration of hydrogen and trigger an alarm or initiate safety measures when the levels exceed a certain threshold. Hydrogen sensors are critical in preventing accidents and ensuring the safe handling and storage of hydrogen.
Types of Hydrogen Sensors
There are several types of hydrogen sensors available in the market, each with its unique working principle and advantages. Let’s take a closer look at some of the most common types:
1. Catalytic Hydrogen Sensors
Catalytic hydrogen sensors, also known as pellistor sensors, work on the principle of catalytic combustion. They consist of two coils: a reference coil and a sensing coil. The sensing coil is coated with a catalyst that promotes the combustion of hydrogen. When hydrogen is present, it burns on the sensing coil, causing a change in resistance. This change is measured and converted into a hydrogen concentration reading.
Advantages:
– Wide measurement range
– Robust and durable
– Suitable for harsh environments
Disadvantages:
– Susceptible to poisoning by certain substances
– Requires oxygen for operation
– Consumes hydrogen during detection
2. Electrochemical Hydrogen Sensors
Electrochemical hydrogen sensors operate based on the electrochemical oxidation of hydrogen. They consist of an anode, a cathode, and an electrolyte. When hydrogen enters the sensor, it reacts with the electrolyte and generates an electrical current proportional to the hydrogen concentration. This current is then measured and converted into a hydrogen reading.
Advantages:
– High selectivity and sensitivity
– Low power consumption
– Compact and portable
Disadvantages:
– Limited lifetime due to electrolyte depletion
– Affected by temperature and humidity variations
– Narrow measurement range
3. Semiconductor Hydrogen Sensors
Semiconductor hydrogen sensors, also called metal oxide sensors, utilize the change in electrical conductivity of a metal oxide material in the presence of hydrogen. When hydrogen interacts with the metal oxide surface, it reduces the oxide, causing a decrease in resistance. This change in resistance is measured and correlated to the hydrogen concentration.
Advantages:
– Fast response time
– Long lifetime
– Low cost
Disadvantages:
– Cross-sensitivity to other reducing gases
– Requires high operating temperatures
– Affected by humidity and temperature fluctuations
4. Optical Hydrogen Sensors
Optical hydrogen sensors rely on the interaction between hydrogen and a specialized material that changes its optical properties in the presence of hydrogen. These sensors typically use fiber optics or plasmonic materials to detect the change in refractive index, absorption, or luminescence caused by hydrogen adsorption. The optical signal is then processed to determine the hydrogen concentration.
Advantages:
– Non-contact measurement
– Immune to electromagnetic interference
– Suitable for remote monitoring
Disadvantages:
– Complex and expensive
– Sensitive to environmental factors
– Limited measurement range
Working Principles of Hydrogen Sensors
To better understand how hydrogen sensors operate, let’s dive into the working principles behind each type:
1. Catalytic Hydrogen Sensors
Catalytic hydrogen sensors rely on the catalytic combustion of hydrogen on the surface of the sensing coil. The sensing coil is typically made of a platinum wire coated with a catalyst, such as palladium or platinum. When hydrogen comes into contact with the catalyst, it undergoes an exothermic combustion reaction, releasing heat. This heat increases the temperature of the sensing coil, causing a change in its electrical resistance. The reference coil, which is not exposed to hydrogen, serves as a baseline for comparison. The difference in resistance between the sensing coil and the reference coil is proportional to the hydrogen concentration.
2. Electrochemical Hydrogen Sensors
Electrochemical hydrogen sensors operate on the principle of electrochemical oxidation. The sensor consists of three main components: an anode, a cathode, and an electrolyte. The anode is typically made of a catalytic material, such as platinum, while the cathode is a porous material that allows hydrogen to diffuse through. The electrolyte is usually an aqueous solution of sulfuric acid or potassium hydroxide.
When hydrogen enters the sensor, it diffuses through the porous cathode and reaches the electrolyte. At the anode, hydrogen undergoes an oxidation reaction, releasing electrons. These electrons flow through an external circuit, generating an electrical current. The magnitude of the current is proportional to the concentration of hydrogen present. The cathode serves as a counter electrode, completing the electrochemical cell.
3. Semiconductor Hydrogen Sensors
Semiconductor hydrogen sensors exploit the change in electrical conductivity of a metal oxide material in the presence of hydrogen. The most commonly used metal oxides are tin dioxide (SnO2) and tungsten trioxide (WO3). These metal oxides are n-type semiconductors, meaning they have a high concentration of free electrons.
When hydrogen interacts with the metal oxide surface, it reduces the oxide, releasing electrons into the conduction band. This increase in free electrons leads to a decrease in the electrical resistance of the material. The change in resistance is measured using an electrical circuit and correlated to the hydrogen concentration. Semiconductor hydrogen sensors typically operate at elevated temperatures (200-400°C) to enhance the sensitivity and selectivity of the sensor.
4. Optical Hydrogen Sensors
Optical hydrogen sensors rely on the interaction between hydrogen and a specialized material that exhibits changes in its optical properties when exposed to hydrogen. There are several types of optical hydrogen sensors, each utilizing a different sensing mechanism:
-
Fiber optic sensors: These sensors use a hydrogen-sensitive coating on the tip of an optical fiber. When hydrogen interacts with the coating, it changes the refractive index or absorption properties of the coating. This change alters the light transmitted through the fiber, which is detected and analyzed to determine the hydrogen concentration.
-
Plasmonic sensors: Plasmonic hydrogen sensors exploit the unique optical properties of metal nanostructures, such as gold or palladium. When hydrogen adsorbs onto the metal surface, it changes the plasmonic resonance frequency of the nanostructures. This shift in resonance is detected optically and correlated to the hydrogen concentration.
-
Luminescent sensors: Luminescent hydrogen sensors use materials that exhibit a change in luminescence intensity or wavelength in the presence of hydrogen. These materials, such as rare-earth-doped oxides or metal-organic frameworks, are excited by an external light source. The luminescence emission is then monitored and analyzed to determine the hydrogen concentration.
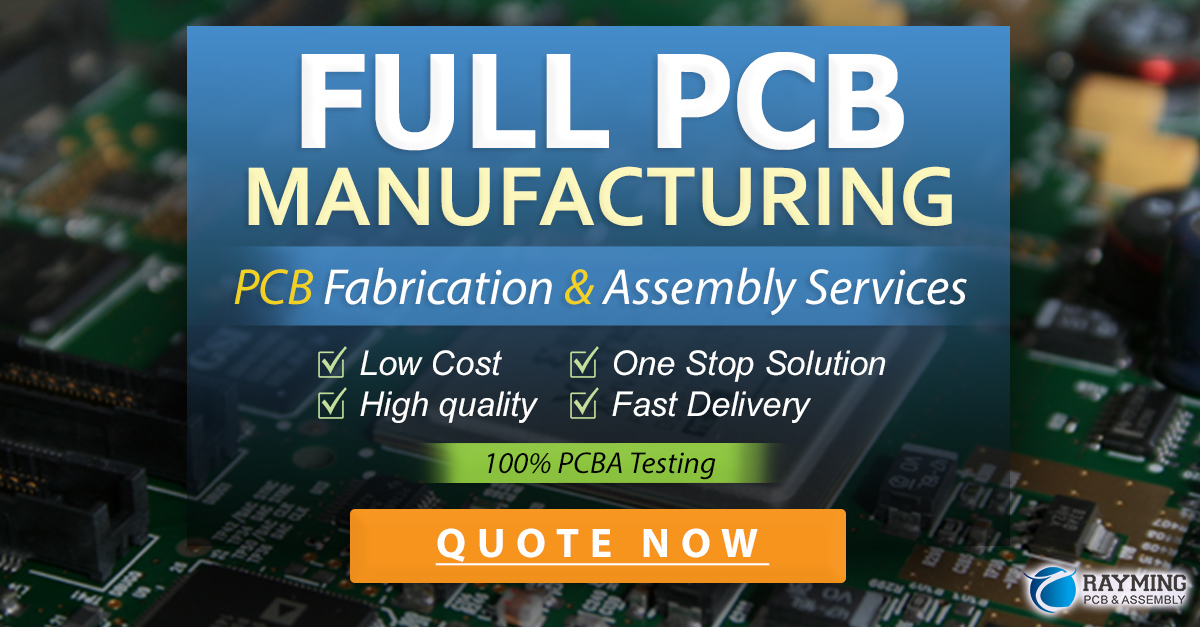
Applications of Hydrogen Sensors
Hydrogen sensors find applications in various industries and fields where hydrogen is used or produced. Some of the key applications include:
1. Fuel Cell Vehicles
Hydrogen fuel cell vehicles rely on hydrogen as their primary fuel source. Hydrogen sensors are crucial in ensuring the safe operation of these vehicles. They are used to detect any leaks in the hydrogen storage and delivery systems, preventing potential accidents. Hydrogen sensors are typically installed in the engine compartment, fuel cell stack, and hydrogen storage areas to provide comprehensive monitoring.
2. Industrial Processes
Many industrial processes involve the use or production of hydrogen. Refineries, chemical plants, and steel mills are examples of industries where hydrogen is widely used. Hydrogen sensors are employed to monitor the concentration of hydrogen in process streams, storage tanks, and pipelines. They help detect leaks, prevent explosions, and ensure the safety of personnel and equipment.
3. Hydrogen Fueling Stations
As the adoption of hydrogen fuel cell vehicles increases, the need for hydrogen fueling stations grows. Hydrogen sensors play a vital role in ensuring the safe operation of these stations. They are used to monitor the hydrogen concentration in the dispensing area, storage tanks, and distribution lines. In case of a leak or abnormal hydrogen levels, the sensors trigger alarms and initiate safety measures, such as shutting off the hydrogen supply.
4. Aerospace Applications
Hydrogen is used as a fuel in some aerospace applications, such as rocket engines and spacecraft fuel cells. Hydrogen sensors are employed to monitor the hydrogen concentration in the fuel systems, ensuring the safe operation of these critical components. They help detect leaks and prevent potential hazards during launch and space missions.
5. Laboratory Safety
Laboratories that work with hydrogen or handle hydrogen-containing materials require hydrogen sensors for safety purposes. These sensors are installed in the lab environment to detect any accidental releases of hydrogen. They provide early warning and allow for prompt evacuation and emergency response measures.
Future Developments in Hydrogen Sensor Technology
As the demand for hydrogen sensors continues to grow, researchers and manufacturers are focusing on developing advanced sensor technologies with improved performance and features. Some of the future developments in hydrogen sensor technology include:
1. Miniaturization
The trend towards miniaturization is driving the development of smaller and more compact hydrogen sensors. Microfabrication techniques, such as MEMS (Micro-Electro-Mechanical Systems), are being used to create miniaturized sensor elements. These compact sensors can be easily integrated into portable devices, wearable safety gear, and IoT (Internet of Things) networks for real-time monitoring.
2. Wireless Connectivity
Wireless connectivity is becoming an essential feature in modern sensor systems. Hydrogen sensors with wireless capabilities allow for remote monitoring and data transmission. This eliminates the need for physical wiring and enables the deployment of sensors in hard-to-reach or hazardous locations. Wireless hydrogen sensors can be integrated into IoT platforms, enabling centralized monitoring and control.
3. Enhanced Selectivity
One of the challenges faced by hydrogen sensors is cross-sensitivity to other gases or environmental factors. Researchers are working on developing sensors with enhanced selectivity to minimize false alarms and improve accuracy. This involves the use of advanced materials, such as nanostructured metal oxides or molecularly imprinted polymers, that exhibit high specificity towards hydrogen.
4. Integration with Machine Learning
Machine learning algorithms can be applied to hydrogen sensor data to improve the accuracy and reliability of the sensors. By training machine learning models on large datasets of sensor readings, it is possible to identify patterns, detect anomalies, and predict potential failures. This integration of machine learning with hydrogen sensors enables predictive maintenance, reducing downtime and enhancing safety.
5. Energy Harvesting
Hydrogen sensors that are deployed in remote or inaccessible locations often face challenges in terms of power supply. Energy harvesting technologies, such as piezoelectric, thermoelectric, or photovoltaic cells, can be integrated with hydrogen sensors to enable self-powered operation. These sensors can harvest energy from ambient sources, such as vibrations, temperature gradients, or light, eliminating the need for battery replacements or external power sources.
Frequently Asked Questions (FAQ)
1. What is the importance of hydrogen sensors in ensuring safety?
Hydrogen sensors play a crucial role in ensuring safety by detecting the presence of hydrogen gas in the surrounding environment. Hydrogen is highly flammable and explosive, and even small leaks can lead to dangerous situations. Hydrogen sensors provide early warning of hydrogen leaks, allowing for prompt action to be taken to prevent accidents, fires, or explosions. They are essential in industries and applications where hydrogen is used or produced, such as fuel cell vehicles, industrial processes, and hydrogen fueling stations.
2. How do I choose the right hydrogen sensor for my application?
Choosing the right hydrogen sensor depends on several factors, including the measurement range, sensitivity, selectivity, response time, and environmental conditions. Consider the following aspects when selecting a hydrogen sensor:
- Measurement range: Ensure that the sensor can detect hydrogen concentrations within the expected range of your application.
- Sensitivity: Determine the minimum hydrogen concentration that needs to be detected and choose a sensor with appropriate sensitivity.
- Selectivity: Consider the presence of other gases or environmental factors that may interfere with the sensor’s performance and select a sensor with high selectivity towards hydrogen.
- Response time: Evaluate the required response time for your application and choose a sensor that can provide timely detection.
- Environmental conditions: Consider the operating temperature, humidity, and pressure range of your application and select a sensor that can withstand those conditions.
It is also important to consider factors such as sensor lifetime, calibration requirements, and cost when making a selection. Consult with sensor manufacturers or experts in the field to determine the most suitable hydrogen sensor for your specific application.
3. What are the maintenance requirements for hydrogen sensors?
Hydrogen sensors require regular maintenance to ensure their proper functioning and reliability. The specific maintenance requirements may vary depending on the type of sensor and the manufacturer’s recommendations. However, some general maintenance practices include:
-
Calibration: Hydrogen sensors need to be periodically calibrated to ensure accurate readings. Calibration involves exposing the sensor to known concentrations of hydrogen and adjusting the sensor’s response accordingly. The calibration frequency depends on the sensor type and the application requirements.
-
Cleaning: Dust, dirt, or other contaminants can accumulate on the sensor surface over time, affecting its performance. Regular cleaning of the sensor using appropriate methods, such as compressed air or gentle wiping, can help maintain its sensitivity and accuracy.
-
Sensor replacement: Hydrogen sensors have a limited lifetime, and their performance may degrade over time. It is important to replace the sensor as per the manufacturer’s recommended schedule or when a significant drift in sensor readings is observed.
-
Environmental control: Ensure that the sensor is operated within its specified temperature, humidity, and pressure range. Extreme environmental conditions can affect the sensor’s performance and lifespan.
-
Storage: When not in use, store the hydrogen sensor in a clean, dry, and safe environment as per the manufacturer’s guidelines to prevent damage or contamination.
Regular maintenance and adherence to the manufacturer’s recommendations can help extend the life of hydrogen sensors and ensure their reliable operation.
4. Are hydrogen sensors intrinsically safe?
Intrinsic safety is a critical consideration when using hydrogen sensors in potentially explosive environments. Intrinsically safe sensors are designed to limit the electrical energy available in the sensor circuitry, preventing the ignition of flammable gases or vapors.
Not all hydrogen sensors are intrinsically safe by default. It is important to select hydrogen sensors that are certified as intrinsically safe for use in hazardous areas. These sensors are designed with special protective circuits and enclosures that prevent the occurrence of sparks or thermal energy that could ignite flammable hydrogen mixtures.
When using hydrogen sensors in potentially explosive atmospheres, it is crucial to follow the manufacturer’s guidelines and adhere to the relevant safety standards and regulations, such as IEC 60079 or ATEX directives. Intrinsically safe sensors should be used in conjunction with appropriate safety barriers, cable glands, and enclosures to ensure overall system safety.
It is always recommended to consult with safety experts and refer to the sensor manufacturer’s specifications to determine the suitability of a hydrogen sensor for use in intrinsically safe applications.
5. How often should hydrogen sensors be calibrated?
The calibration frequency of hydrogen sensors depends on several factors, including the sensor type, the application requirements, and the manufacturer’s recommendations. However, as a general guideline, hydrogen sensors should be calibrated at least once every six months to ensure accurate and reliable readings.
Some specific considerations for calibration frequency include:
-
Regulatory requirements: Certain industries or applications may have specific regulatory requirements for sensor calibration intervals. It is important to adhere to these requirements to maintain compliance.
-
Environmental conditions: Harsh environmental conditions, such as extreme temperatures, humidity, or the presence of contaminants, can affect sensor performance and may require more frequent calibration.
-
Sensor drift: Over time, hydrogen sensors may experience a gradual drift in their readings. Regular calibration helps compensate for this drift and maintain the sensor’s accuracy.
-
Criticality of the application: In applications where the consequences of a hydrogen leak or explosion are severe, more frequent calibration may be necessary to ensure the highest level of safety.
It is recommended to establish a calibration schedule based on the manufacturer’s guidelines and the specific requirements of your application. Keeping a log of calibration dates and results can help track sensor performance and identify any potential issues or trends.
In addition to regular calibration, it is important to perform bump tests or functional checks on hydrogen sensors to verify their response to hydrogen gas between calibration intervals. These tests involve exposing the sensor to a known concentration of hydrogen and ensuring that it responds appropriately.
Conclusion
Hydrogen sensors are indispensable safety instruments in the growing hydrogen economy. They play a vital role in detecting and monitoring hydrogen leaks, preventing accidents, and ensuring the safe handling and storage of hydrogen. With various types of sensors available, each with its unique working principles and advantages, it is important to select the right sensor for the specific application.
As hydrogen continues to gain prominence as a clean energy source, the demand for reliable and advanced hydrogen sensors will only increase. Future developments in sensor technology, such as miniaturization, wireless connectivity, enhanced selectivity, integration with machine learning, and energy harvesting, will further enhance the capabilities and applications of hydrogen sensors.
By understanding the importance of hydrogen sensors, their working principles, and the best practices for maintenance and calibration, we can ensure the safe and widespread adoption of hydrogen technologies. As we move towards a sustainable energy future, hydrogen sensors will continue to play a critical role in enabling the safe and efficient use of this promising energy carrier.
Leave a Reply