Flex Circuit Design
Flexible circuits, also known as flex circuits or flexible printed circuit boards (PCBs), have gained popularity in recent years due to their versatility and ability to fit into tight spaces. When designing a flex circuit, there are several critical factors to consider to ensure optimal performance, reliability, and cost-effectiveness.
In this article, we will explore nine essential factors that designers should keep in mind when working on flex circuit design.
1. Flexibility Requirements
One of the primary reasons for using flex circuits is their ability to bend and flex. However, the degree of flexibility required can vary depending on the application. Some designs may only need a one-time bend during installation, while others may require continuous flexing throughout their lifespan.
Consider the following aspects when determining flexibility requirements:
- Static vs. dynamic flexing
- Bend radius
- Number of flex cycles
- Flexing direction (single or multiple planes)
By understanding the flexibility needs of your application, you can select the appropriate materials, thickness, and design features to ensure reliable performance.
2. Material Selection
Choosing the right materials is crucial for the success of your flex circuit design. The most common base material for flex circuits is polyimide, which offers excellent thermal and chemical stability, as well as good mechanical properties.
Other materials to consider include:
- Polyester (PET): Lower cost and suitable for less demanding applications
- Liquid Crystal Polymer (LCP): High-performance material with low moisture absorption and excellent electrical properties
- Polytetrafluoroethylene (PTFE): Offers superior chemical resistance and low dielectric constant
When selecting materials, also consider the copper type (electrodeposited or rolled annealed) and thickness, as well as the adhesive used to bond the layers together.
3. Conductor Thickness and Width
The thickness and width of the copper conductors in your flex circuit design will impact its electrical performance, flexibility, and manufacturability. Thinner conductors allow for greater flexibility but may have higher resistance and current-carrying limitations.
Copper Thickness (oz) | Copper Thickness (μm) | Typical Applications |
---|---|---|
1/3 | 12 | High-density designs, ultra-thin assemblies |
1/2 | 18 | General-purpose flex circuits |
1 | 35 | Power circuits, high-current applications |
When designing conductor widths, consider the current-carrying requirements, voltage drop, and spacing between adjacent traces to minimize crosstalk and electromagnetic interference (EMI).
4. Bend Radius and Strain Relief
To ensure the long-term reliability of your flex circuit, it’s essential to design with the appropriate bend radius and strain relief features. The minimum bend radius is typically determined by the thickness of the materials and the number of layers in the circuit.
As a general rule, the minimum bend radius should be at least six times the total thickness of the flex circuit. However, for dynamic flexing applications, a larger bend radius may be necessary to minimize stress on the conductors.
Strain relief features, such as stiffeners and adhesive support, can be added to the design to distribute stress and prevent damage to the conductors at the transition points between the flexible and rigid portions of the circuit.
5. Shielding and Grounding
Proper shielding and grounding are essential for minimizing EMI and ensuring signal integrity in flex circuit designs. Some common shielding and grounding techniques include:
- Copper shielding: A thin layer of copper on one or both sides of the flex circuit to provide EMI shielding
- Conductive adhesives: Used to bond the shielding layer to the flex circuit and provide a low-impedance ground path
- Ground planes: Solid copper planes used to provide a low-impedance ground reference and reduce EMI
- Via stitching: A series of closely spaced vias along the edge of the flex circuit to provide a continuous ground connection
When designing shielding and grounding features, consider the frequency range of the signals, the sensitivity of the components, and the EMI environment in which the flex circuit will operate.
6. Panelization and Routing
Panelization and routing are important aspects of flex circuit design that impact manufacturability and cost. Panelization involves arranging multiple flex circuits on a single panel to maximize material utilization and minimize waste.
When panelizing flex circuits, consider the following:
- Panel size and material utilization
- Spacing between individual circuits
- Tooling and registration holes
- Depaneling methods (e.g., scoring, routing, or punching)
Routing refers to the process of cutting the outline of the flex circuit and any internal cutouts or openings. When designing the routing pattern, consider the minimum feature size, spacing between features, and the capabilities of the manufacturing process.
7. Coverlay and Stiffener Placement
Coverlay and stiffeners are additional layers added to the flex circuit to provide insulation, protection, and mechanical support. Coverlays are typically made from polyimide or polyester and are laminated over the conductors to provide electrical insulation and environmental protection.
Stiffeners, usually made from polyimide, FR-4, or metal, are used to add rigidity to specific areas of the flex circuit, such as connector locations or component mounting areas.
When placing coverlay and stiffeners, consider the following:
- Coverlay openings for component pads and test points
- Stiffener shape and size to provide adequate support without compromising flexibility
- Adhesive selection for bonding the coverlay and stiffeners to the flex circuit
8. Component Selection and Placement
Selecting and placing components on a flex circuit requires careful consideration to ensure reliability and manufacturability. When choosing components, opt for surface mount devices (SMDs) whenever possible, as they are better suited for flex circuits than through-hole components.
Consider the following factors when selecting and placing components:
- Component packaging and size
- Placement orientation and spacing
- Pad size and shape
- Soldering or bonding process
In general, it’s best to place components on the neutral axis of the flex circuit to minimize stress during flexing. Additionally, consider using adhesives or underfill materials to provide additional mechanical support for components in high-stress areas.
9. Testing and Validation
Testing and validation are critical steps in the flex circuit design process to ensure that the circuit meets its electrical, mechanical, and environmental requirements. Some common testing methods include:
- Continuity and insulation resistance testing
- Impedance and capacitance testing
- Flexing and bend radius testing
- Thermal cycling and shock testing
- Vibration and acceleration testing
Develop a comprehensive testing plan that covers all relevant aspects of your flex circuit design, and work with your manufacturing partner to ensure that the testing is performed accurately and consistently.
Flex Circuit Design FAQ
- What are the advantages of using flex circuits over traditional rigid PCBs?
Flex circuits offer several advantages, including: - Reduced size and weight
- Improved reliability and durability
- Enhanced design flexibility and conformity to irregular shapes
-
Elimination of connectors and wires, leading to lower assembly costs
-
Can flex circuits be used in high-temperature environments?
Yes, flex circuits can be designed to withstand high temperatures by selecting appropriate materials, such as polyimide or PTFE, which have excellent thermal stability. However, it’s essential to consider the temperature ratings of the components and the overall assembly when designing for high-temperature applications. -
How do I determine the appropriate copper thickness for my flex circuit design?
The copper thickness should be selected based on the electrical requirements, such as current-carrying capacity and voltage drop, as well as the mechanical requirements for flexibility and durability. Thinner copper (1/3 or 1/2 oz) is often used for high-density, ultra-flexible designs, while thicker copper (1 oz) is used for power circuits and high-current applications. -
Can flex circuits be used in dynamic flexing applications?
Yes, flex circuits can be designed for dynamic flexing applications, such as hinges or rotating joints. However, designing for dynamic flexing requires careful consideration of the bend radius, material selection, and strain relief features to ensure long-term reliability. -
How do I specify the bend radius for my flex circuit design?
The bend radius is typically specified as a multiple of the total thickness of the flex circuit. As a general rule, the minimum bend radius should be at least six times the total thickness. However, for dynamic flexing applications or designs with multiple layers, a larger bend radius may be necessary. Consult with your manufacturing partner to determine the appropriate bend radius for your specific application.
Conclusion
Designing a flex circuit requires careful consideration of multiple factors, including flexibility requirements, material selection, conductor thickness and width, bend radius and strain relief, shielding and grounding, panelization and routing, coverlay and stiffener placement, component selection and placement, and testing and validation.
By understanding these factors and working closely with your manufacturing partner, you can create a flex circuit design that meets your application’s specific requirements while ensuring reliability, manufacturability, and cost-effectiveness.
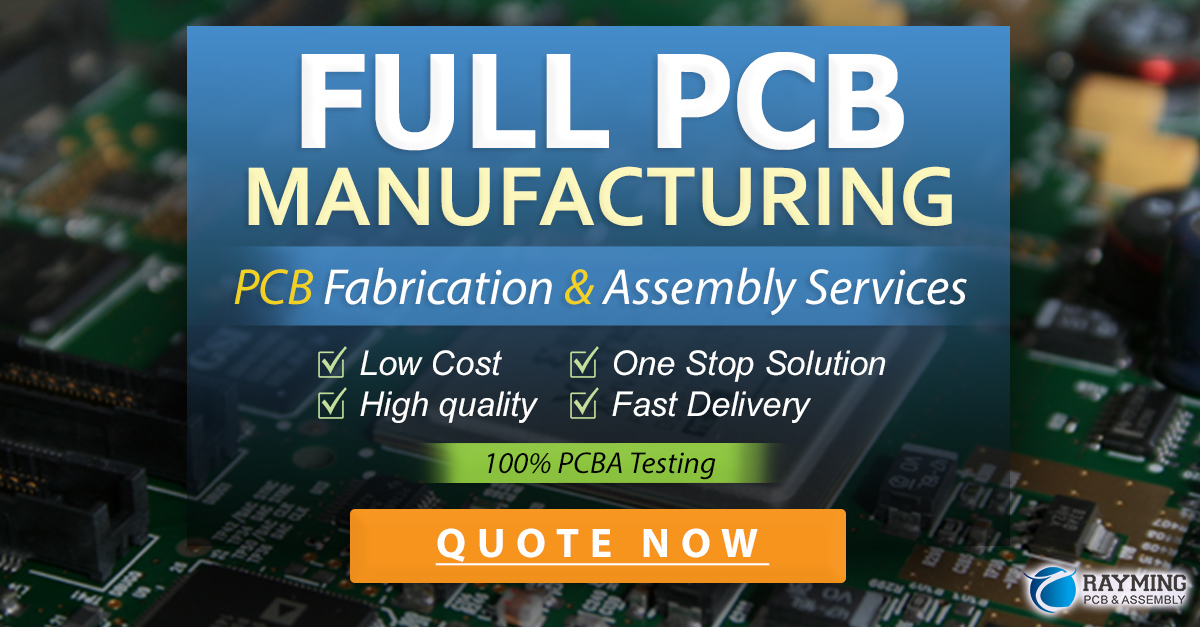
Leave a Reply