Introduction to PCB Fabrication
Printed Circuit Board (PCB) fabrication is the process of creating printed circuit boards used in electronic devices. PCBs provide the physical structure and electrical connections for components like resistors, capacitors, and integrated circuits. The PCB fabrication process turns a design into a functional board ready for assembly.
In this comprehensive guide, we’ll cover everything you need to know about PCB fabrication, from the basics of how PCBs work to advanced fabrication techniques and troubleshooting common issues. Whether you’re an electrical engineer designing boards or just curious to learn more, read on to gain a thorough understanding of the PCB fabrication process.
How PCBs Work
The Structure of a PCB
A printed circuit board consists of several layers:
Layer | Description |
---|---|
Substrate | The base material, typically FR4 fiberglass |
Copper | Thin copper foil laminated to the substrate |
Solder Mask | Insulating layer that covers the copper, leaving pads exposed |
Silkscreen | Text and symbols printed on the solder mask |
The combination of these layers allows a PCB to provide electrical connections and physical mounting points for components.
PCB Design Considerations
Before a PCB can be fabricated, it must be designed. Key considerations during the design phase include:
- Schematic capture – Creating the initial circuit diagram
- Component selection – Choosing parts that meet electrical and physical requirements
- Layout – Arranging components and routing traces
- Design for manufacturing – Ensuring the board can be reliably and cost-effectively produced
PCB design software like Altium, Eagle, or KiCad is used to create the schematic and layout files needed for fabrication.
The PCB Fabrication Process
Step 1: PCB Printing
The first step in PCB fabrication is printing the copper pattern onto the substrate material. There are several methods for transferring the pattern:
Method | Description |
---|---|
Silk Screen Printing | Copper ink is pushed through a fine mesh screen onto the substrate |
Photoengraving | Photoresist is exposed and etched to create the copper pattern |
PCB Milling | A CNC mill removes copper to isolate traces |
The choice of printing method depends on factors like resolution, throughput, and cost. Photoengraving is most common for commercial fabrication.
Step 2: Etching
After the copper pattern is printed, unwanted copper is removed through etching. The board is immersed in an etchant solution, typically ferric chloride or ammonium persulfate. These chemicals dissolve copper not protected by etch resist.
Etching can be done manually in tanks or automatically in conveyorized etching machines. Variables like etchant temperature, concentration, and agitation affect the etch rate and quality.
Step 3: Drilling
Once etched, holes are drilled through the PCB for component leads and vias. There are two main drilling methods:
Method | Description |
---|---|
Mechanical Drilling | High-speed spindles drill through the board |
Laser Drilling | Holes are ablated with a focused laser beam |
Mechanical drilling with carbide drill bits is standard for larger holes (>0.2 mm). Laser drilling enables smaller microvias.
Step 4: Plating
After drilling, the holes are plated with copper to provide electrical connections between layers. There are two types of plating:
Method | Description |
---|---|
Electroless Copper (ENIG) | Copper is deposited via an autocatalytic chemical reaction |
Electrolytic Plating | Copper is deposited by passing current through an electrolyte bath |
ENIG is used as a seed layer for electrolytic plating, which builds up additional copper thickness. Hot air solder leveling (HASL) or lead-free HASL is then applied to protect the copper and aid solderability.
Step 5: Solder Mask Application
The next step is applying solder mask, which insulates and protects the copper traces. Solder mask is typically a polymer ink that is silkscreened and cured.
Liquid photoimageable (LPI) solder masks offer higher resolution than traditional screen printed masks. The solder mask is exposed and developed to reveal the copper pads.
Step 6: Silkscreen
Finally, the silkscreen layer is applied to print text and symbols on the PCB. Silkscreen ink is usually epoxy-based for durability.
The silkscreen adds labels, logos, and component identifiers to aid assembly and troubleshooting. White is the most common color, but other colors are available.
Step 7: Surface Finish
An additional surface finish may be applied to the exposed copper pads to enhance solderability and protect against oxidation. Common finishes include:
Finish | Composition |
---|---|
HASL | Tin-lead alloy |
Lead-free HASL | Tin-copper or tin-silver-copper alloy |
ENIG | Electroless nickel/immersion gold |
OSP | Organic solderability preservative |
The choice of finish depends on factors like lead-free requirements, flatness, cost, and shelf life.
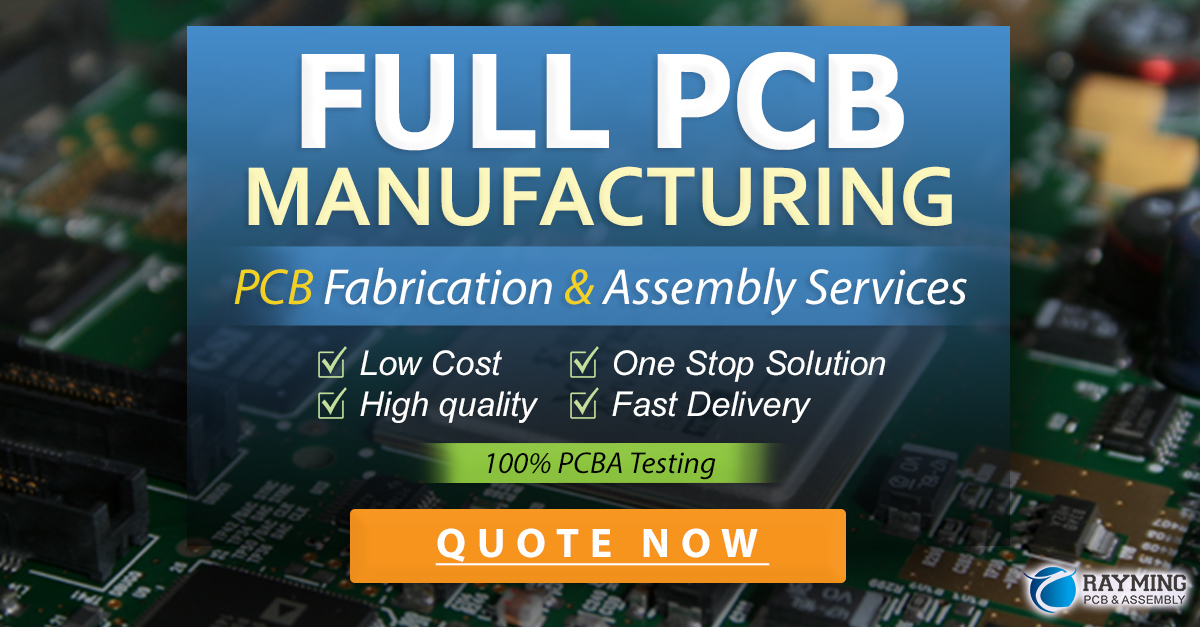
PCB Materials
PCBs can be fabricated from a variety of materials, each with different properties and applications.
FR4
FR4 is the most common material for rigid PCBs. It is a fiberglass-reinforced epoxy laminate with good mechanical and electrical properties.
CEM-1/CEM-3
CEM-1 and CEM-3 are composite epoxy materials used for lower-cost consumer electronics. They have lower glass transition temperatures than FR4.
Polyimide
Polyimide (PI) is a high-temperature polymer used for flexible PCBs and high-reliability applications. It maintains its properties up to 260°C.
PTFE
Polytetrafluoroethylene (PTFE) is used for high-frequency PCBs due to its low dielectric constant and dissipation factor. It is often used in RF/microwave designs.
Aluminum
Aluminum PCBs are used for high-power applications that require heat dissipation, such as LED lighting. The aluminum substrate acts as a heatsink.
Advanced PCB Fabrication Techniques
HDI
High Density Interconnect (HDI) PCBs use small vias and fine traces to achieve higher routing density. They enable smaller form factors and increased functionality.
HDI boards often incorporate microvias and sequential lamination. They require advanced fabrication capabilities and tighter tolerances.
Rigid-Flex
Rigid-flex PCBs combine rigid and flexible substrates in a single assembly. They allow 3D packaging and eliminate connectors between boards.
Rigid-flex fabrication requires specialized materials and processes to laminate and route the flexible layers. Factors like bend radius and stiffener design are critical.
Embedded Components
Embedded PCBs have passive components like resistors and capacitors built into the substrate layers. This saves space and improves electrical performance.
Embedded components are fabricated by printing resistive/capacitive inks or laminating thin film components within the PCB stackup. Precise process control is essential.
PCB Fabrication Tolerances and Specifications
Fabrication tolerances and specifications are key to ensuring PCBs are manufactured consistently and perform as intended. Key parameters include:
Parameter | Definition | Typical Tolerance |
---|---|---|
Trace width/spacing | The width of copper traces and spacing between them | ±0.1 mm |
Hole size | The diameter of drilled holes | ±0.05 mm |
Annular ring | The copper pad surrounding a hole | 0.15 mm minimum |
Solder mask alignment | Registration of solder mask to copper features | ±0.05 mm |
Tighter tolerances may be achievable but can increase cost and lead time. It’s important to design within standard fabrication capabilities unless absolutely necessary.
IPC, the Association Connecting Electronics Industries, publishes standards for PCB design and fabrication. The most relevant standards are:
- IPC-6012: Qualification and Performance Specification for Rigid PCBs
- IPC-6013: Qualification and Performance Specification for Flexible/Rigid-Flex PCBs
- IPC-A-600: Acceptability of Printed Boards
These standards define quality requirements and acceptance criteria for PCBs. Many fabricators are certified to these standards and can provide conformance testing.
PCB Fabrication Troubleshooting
Even with careful design and process control, issues can arise during PCB fabrication. Some common problems and their causes include:
Problem | Possible Causes |
---|---|
Shorts/opens | Copper residue, solder mask defects, damaged traces |
Plating voids | Contamination, inadequate cleaning, poor plating adhesion |
Misregistration | Artwork distortion, misaligned layers, stretching/shrinkage |
Delamination | Moisture, excessive heat, poor lamination bonding |
Troubleshooting these issues requires a systematic approach and an understanding of the fabrication process. Techniques like visual inspection, continuity testing, and microsectioning can help identify root causes.
Partnering with an experienced, reputable PCB fabricator can minimize issues and ensure a smooth production process. Look for a fabricator with a proven track record, robust quality control, and good communication.
FAQ
What is the typical turnaround time for PCB fabrication?
Turnaround time depends on the complexity of the design and the fabricator’s capacity. Simple 2-layer boards can be manufactured in as little as 24 hours, while complex HDI or rigid-flex assemblies may take several weeks. Rush services are available for a premium.
What files are needed for PCB fabrication?
Fabricators typically require Gerber files, which describe the copper patterns, drill holes, and solder mask. Drill files (Excellon format) and a Bill of Materials (BOM) may also be needed. Some fabricators accept native CAD files (e.g. Altium, Eagle) but Gerbers are the industry standard.
How much does PCB fabrication cost?
PCB fabrication cost depends on factors like board size, layer count, materials, and quantity. Small prototype runs can cost a few dollars per board, while large volume production can be much less than a dollar per unit. Get quotes from multiple fabricators and consider total cost of ownership, not just piece price.
What are the most common PCB sizes?
Common PCB sizes correspond to standard panel sizes used in fabrication. These include:
- 100 x 100 mm
- 200 x 150 mm
- 300 x 300 mm
- 450 x 350 mm
Smaller boards are often panelized to fill up a standard panel size. Custom sizes are possible but may affect cost and yield.
How do I choose a PCB fabricator?
When selecting a PCB fabricator, consider:
- Capabilities (e.g. HDI, flex, RF)
- Quality certifications (e.g. ISO 9001, IPC)
- Experience and references
- Pricing and lead times
- Technical support and communication
Look for a fabricator that specializes in your type of product and has a culture of continuous improvement. Building a strong relationship with your fabricator can pay dividends in terms of quality, reliability, and cost.
Conclusion
PCB fabrication is a complex process that turns design files into functional circuit boards. By understanding the steps involved, the key parameters and tolerances, and common pitfalls, you can ensure successful manufacture of your PCB designs.
While we’ve covered the fundamentals here, PCB fabrication is a deep topic with many nuances and specialty applications. Continued learning and collaboration with experienced professionals is essential to stay at the forefront of this critical technology.
With the right design practices, materials choices, and fabrication partner, you can bring your electronic product visions to life through the power of PCBs. So get out there and start creating!
Leave a Reply