What are Halogen-free PCBs?
Halogen-free PCBs are printed circuit boards that do not contain any halogenated flame retardants (HFRs) or other halogenated materials. Common halogens used in PCBs include chlorine (Cl) and bromine (Br). These substances can be harmful to the environment and human health when released during PCB manufacturing, use, or disposal.
Halogen-free PCBs, on the other hand, use alternative flame retardants that are safer and more environmentally friendly. Some common halogen-free flame retardants include:
- Aluminum hydroxide
- Magnesium hydroxide
- Phosphorus compounds
- Nitrogen compounds
By using these alternative materials, halogen-free PCBs reduce the risk of toxic gas emissions during fires and minimize the environmental impact of electronic waste.
Advantages of Halogen-free PCBs
1. Environmental Friendliness
One of the main advantages of halogen-free PCBs is their environmental friendliness. When exposed to high temperatures, traditional PCBs containing halogens can release toxic gases like dioxins and furans, which are harmful to the environment and human health. Halogen-free PCBs eliminate this risk, making them a greener choice for electronics manufacturing.
2. Improved Safety
In addition to being more environmentally friendly, halogen-free PCBs also offer improved safety for users. In the event of a fire, halogen-free PCBs produce less smoke and toxic fumes compared to traditional PCBs. This reduces the risk of smoke inhalation and other health hazards associated with burning electronics.
3. Compliance with Environmental Regulations
Many countries and regions have implemented strict regulations on the use of hazardous substances in electronics, such as the Restriction of Hazardous Substances (RoHS) directive in the European Union. Halogen-free PCBs comply with these regulations, making them a necessary choice for companies that want to sell their products in these markets.
4. Better Thermal Stability
Halogen-free PCBs often exhibit better thermal stability compared to traditional PCBs. This means they can withstand higher temperatures without degrading or losing their mechanical and electrical properties. This is particularly important for applications that involve high-temperature environments, such as automotive electronics or industrial equipment.
5. Improved Reliability
The improved thermal stability of halogen-free PCBs also contributes to their overall reliability. By resisting thermal degradation, halogen-free PCBs are less likely to experience failures or malfunctions over time. This can help extend the lifespan of electronic devices and reduce maintenance costs.
Factors to Consider When Buying Halogen-free PCBs
When purchasing halogen-free PCBs, there are several key factors to consider to ensure you get the best product for your needs:
1. Material Selection
Halogen-free PCBs can be made from a variety of materials, each with its own properties and benefits. Some common halogen-free PCB materials include:
Material | Description | Advantages |
---|---|---|
FR-4 | A composite material made from woven fiberglass cloth with an epoxy resin binder. | Good mechanical strength, electrical insulation, and thermal stability. Widely available and affordable. |
Polyimide | A high-performance polymer known for its excellent thermal and chemical resistance. | Can withstand extreme temperatures (up to 400°C) and harsh chemicals. Ideal for demanding applications. |
PTFE | Polytetrafluoroethylene, a fluoropolymer with outstanding electrical and thermal properties. | Very low dielectric constant and dissipation factor. Excellent chemical resistance and thermal stability. |
Consider the specific requirements of your application, such as temperature range, dielectric constant, and mechanical strength, when selecting a halogen-free PCB material.
2. Manufacturing Process
The manufacturing process used to produce halogen-free PCBs can impact their quality and performance. Some key aspects to consider include:
- Lamination: Ensure the manufacturer uses a reliable lamination process to bond the layers of the PCB together without voids or delamination.
- Drilling: Check that the manufacturer uses high-quality drill bits and optimized drilling parameters to create clean, precise holes in the PCB.
- Plating: Look for manufacturers that use advanced plating techniques, such as electroless nickel immersion gold (ENIG) or immersion silver, to ensure good solderability and conductivity.
3. Supplier Reputation and Certifications
When choosing a halogen-free PCB supplier, it’s important to consider their reputation and certifications. Look for suppliers with:
- ISO 9001 certification for quality management
- ISO 14001 certification for environmental management
- UL recognition for safety and reliability
- RoHS compliance certification
Working with a reputable supplier that has these certifications can give you confidence in the quality and reliability of their halogen-free PCBs.
4. Cost and Lead Time
Of course, cost and lead time are also important factors to consider when buying halogen-free PCBs. While halogen-free PCBs may have a slightly higher cost compared to traditional PCBs due to the specialized materials and processes involved, the long-term benefits in terms of environmental friendliness, safety, and reliability can outweigh the initial investment.
Lead time can vary depending on the complexity of your PCB design and the manufacturer’s capacity. Be sure to communicate your timeline requirements clearly with your supplier and plan accordingly.
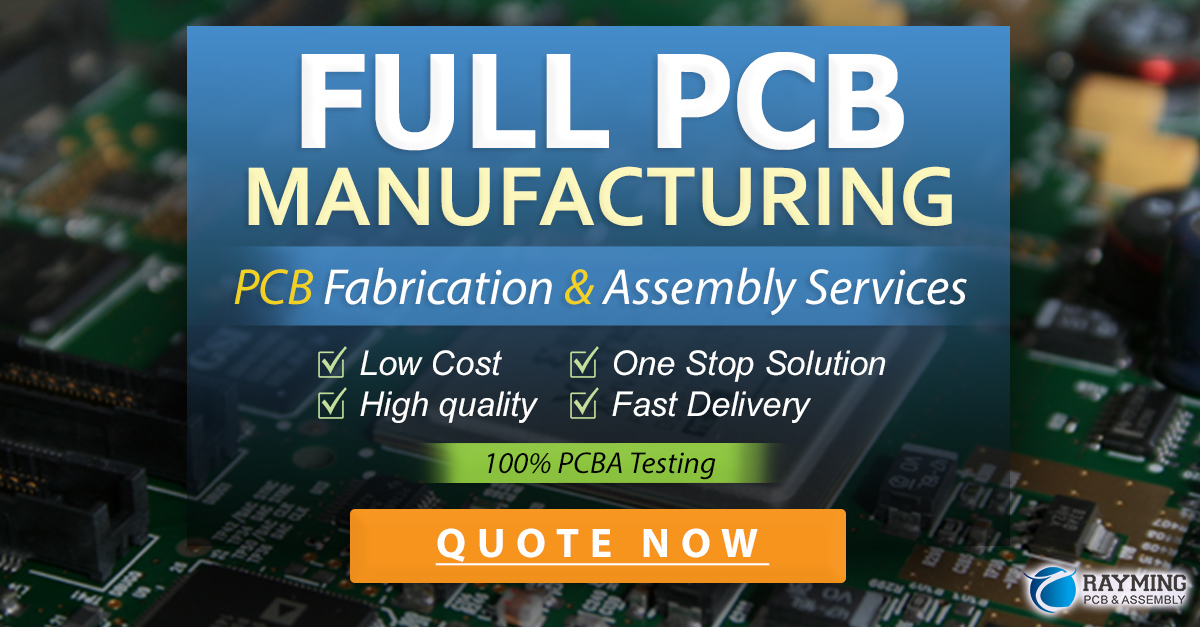
Frequently Asked Questions (FAQ)
1. Are halogen-free PCBs more expensive than traditional PCBs?
Halogen-free PCBs may have a slightly higher cost compared to traditional PCBs due to the specialized materials and processes involved. However, the long-term benefits in terms of environmental friendliness, safety, and reliability often outweigh the initial investment.
2. Can halogen-free PCBs be used for all applications?
Halogen-free PCBs are suitable for a wide range of applications, from consumer electronics to industrial equipment. However, some specialized applications may require specific materials or properties that halogen-free PCBs cannot provide. It’s important to carefully consider the requirements of your application when deciding whether to use halogen-free PCBs.
3. How can I ensure the quality of the halogen-free PCBs I purchase?
To ensure the quality of your halogen-free PCBs, look for reputable suppliers with certifications such as ISO 9001, ISO 14001, UL recognition, and RoHS compliance. Clearly communicate your requirements and specifications to your supplier, and consider requesting samples or prototypes before placing a large order.
4. What impact do halogen-free PCBs have on the environment?
Halogen-free PCBs have a lower environmental impact compared to traditional PCBs containing halogens. They reduce the risk of toxic gas emissions during manufacturing, use, and disposal, and comply with environmental regulations like the RoHS directive. By choosing halogen-free PCBs, you can help minimize the environmental footprint of your electronics products.
5. Are there any disadvantages to using halogen-free PCBs?
The main disadvantage of halogen-free PCBs is their potentially higher cost compared to traditional PCBs. Additionally, some halogen-free materials may have slightly different properties compared to their halogenated counterparts, which could require adjustments to your design or manufacturing process. However, for most applications, the benefits of halogen-free PCBs outweigh these minor drawbacks.
Conclusion
In conclusion, halogen-free PCBs offer a more environmentally friendly, safer, and reliable alternative to traditional PCBs containing halogens. By considering factors such as material selection, manufacturing process, supplier reputation, and cost, you can make an informed decision when purchasing halogen-free PCBs for your electronics projects. Embrace the benefits of halogen-free PCBs and contribute to a greener, more sustainable future for the electronics industry.
Leave a Reply