Introduction to PCBs
A printed circuit board, or PCB, is the foundational building block of most modern electronic devices. PCBs are flat boards made of insulating materials like fiberglass, with conductive copper traces printed onto them in a precise pattern. Electronic components like resistors, capacitors, and integrated circuits are then soldered onto the PCB to create a complete circuit.
PCBs allow circuits to be manufactured in a standardized, repeatable way. They mechanically support and electrically connect electronic components using conductive pathways, tracks or signal traces etched from copper sheets laminated onto a non-conductive substrate.
Advantages of Using PCBs
There are many benefits to using printed circuit boards in electronic devices:
- Compact size – PCBs allow circuits to be much smaller and more densely packed compared to other wiring methods
- Reliability – Printed circuits are less prone to loose connections and physical failures
- Repeatability – PCBs enable the mass production of identical circuit assemblies
- Lower cost – Once the PCB design is finalized, boards can be manufactured quickly and cheaply in large quantities
- Automated assembly – Components can be mounted and soldered onto PCBs using automated pick-and-place machines and wave/reflow soldering
PCB Composition and Materials
A typical printed circuit board consists of several layers:
Layer | Description |
---|---|
Silkscreen | White text labels and symbols printed on the PCB for assembly and testing |
Solder Mask | Insulating layer covering the copper traces, with openings for solder pads |
Copper Traces | Thin conductive copper lines that form the circuit interconnects |
Substrate | The rigid insulating board material, often FR-4 fiberglass |
Copper Planes | Thin copper layers used for power/ground planes and shielding |
The most common PCB substrate material is FR-4, a glass-reinforced epoxy laminate. FR-4 offers good insulation, mechanical strength, and temperature resistance at a low cost. Other specialized PCB materials include:
- High Tg FR-4 – Improved version of standard FR-4 with higher glass transition temp for better thermal stability
- Polyimide – Flexible PCB material that withstands high temps and repeated bending
- Metal Core – Aluminum or copper base for better heat dissipation
- Teflon – Low-loss, moisture resistant material for high frequency RF circuits
- Ceramic – Aluminum oxide or aluminum nitride for high-power LED lighting
Copper Weights and Trace Dimensions
The amount of copper on a PCB is specified by its weight in ounces per square foot. Most PCBs use 1 oz/ft² copper, which is about 35 μm thick. High-current or high-frequency boards may use 2 or 3 oz/ft² copper for lower resistance and inductance.
Copper traces can range in width from a few mils (thousandths of an inch) for low-current signals up to 100 mils or more for high-current power traces. Common PCB trace widths and their current carrying capacity are shown below:
Trace Width (mils) | Max Current at 10°C rise (amps) |
---|---|
10 | 0.5 |
20 | 1.0 |
50 | 2.5 |
100 | 6.0 |
Types of Printed Circuit Boards
PCBs can be categorized based on several criteria, such as number of layers, substrate flexibility, or component mounting method. The most common types of PCBs include:
Single-Layer and Double-Layer PCBs
The simplest PCBs have just one layer of copper traces on a rigid substrate. These single-layer or single-sided PCBs are used for basic, low-density circuits. Double-layer or double-sided PCBs have copper on both sides of the substrate, allowing more traces to fit in the same area.
Multi-Layer PCBs
For more complex, high-density circuits, multi-layer PCBs are used. These boards have three or more layers of copper, separated by insulating layers. The inner layers are used for signal routing, power/ground planes, or shielding. Multi-layer PCBs enable very compact, dense circuit layouts but are more expensive to manufacture.
Flexible and Rigid-Flex PCBs
Flexible PCBs are made with thin, flexible polymer substrates like polyimide that allow the board to bend and flex. This makes them ideal for applications with moving parts or tight space constraints. Rigid-flex PCBs combine rigid and flexible sections for the best of both worlds – stable mounting points for components along with flex regions to fit into cramped spaces.
Through-Hole and Surface Mount PCBs
PCBs can also be categorized by the type of components they use. Through-hole PCBs use components with long leads that are inserted through drilled holes in the board and soldered on the opposite side. Surface-mount PCBs use smaller components that are soldered directly onto pads on the surface of the board, allowing for much higher density. Many PCBs use a mix of both through-hole and surface-mount components.
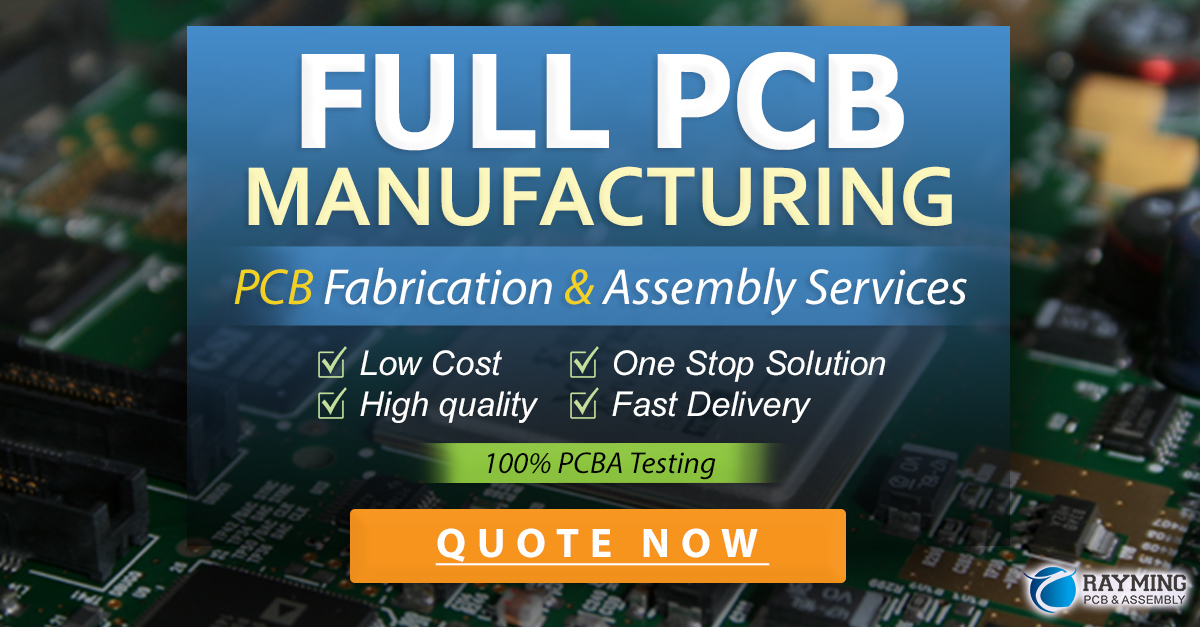
PCB Design and Manufacturing Process
Creating a new PCB involves several steps, from schematic design to final assembly:
-
Schematic Capture – The circuit is first drawn as a schematic diagram, showing how all the components are connected.
-
Board Layout – The schematic is then turned into a physical PCB layout, with the location of components and routing of traces.
-
Design Rule Check (DRC) – The PCB layout is checked against a set of design rules to catch any errors or potential manufacturing issues.
-
Gerber File Generation – The PCB layout is exported as a set of Gerber files, which describe each layer of the board in a machine-readable format.
-
PCB Fabrication – The Gerber files are sent to a PCB manufacturer, who makes the bare PCB based on those specifications.
-
Component Sourcing – The electronic components and PCB are ordered from suppliers.
-
PCB Assembly – The components are placed and soldered onto the PCB, either by hand or using automated assembly machines.
-
Testing and Inspection – The assembled boards are tested and inspected to ensure proper functionality before shipping.
PCB Design Software
PCB design is typically done with the aid of specialized electronic design automation (EDA) software. Some popular PCB design programs include:
- Autodesk EAGLE
- Altium Designer
- KiCad EDA
- OrCAD PCB Designer
- Mentor Graphics PADS
These programs provide schematic capture, board layout, and simulation tools to help design reliable, manufacturable PCBs.
Fabrication Options and Costs
There are many PCB fabrication houses that can manufacture boards from Gerber files. Costs vary depending on the board specs, but can range from around $10 for a small prototype board up to thousands of dollars for a large, complex production run.
Some factors that affect PCB fabrication cost include:
- Board size – Larger boards are more expensive
- Number of layers – More layers add to the cost
- Smallest trace/space – Finer pitch features require more expensive processes
- Plated through-holes – Adding PTH makes drilling and plating more complex
- Solder mask and silkscreen – Custom colors and double-sided printing add cost
- Quantity – Higher volumes have lower per-board cost but higher setup fees
Many PCB fab houses have online quoting tools to estimate the cost of a specific board design. Some popular online PCB fabricators include OSH Park, JLCPCB, Seeed Studio, and PCBWay.
Common PCB Applications
Printed circuit boards are used in virtually every electronic device, from consumer gadgets to industrial equipment. Some common applications of PCBs include:
- Consumer electronics – PCBs are found in smartphones, laptops, TVs, gaming consoles, and wearables
- Automotive – Modern vehicles contain dozens of PCBs for engine control, infotainment, driver assist, and more
- Medical devices – PCBs are used in diagnostic equipment, patient monitors, imaging systems, and implantable devices
- Industrial controls – PCBs are key to PLCs, motor drives, sensors, and automation equipment
- Power electronics – High-power PCBs are used in power supplies, converters, inverters, and renewable energy systems
- Telecommunications – PCBs are integral to networking equipment, base stations, satellites, and fiber optic systems
- Aerospace and defense – Rugged, high-reliability PCBs are used in aircraft, spacecraft, and military hardware
PCB Design Considerations and Best Practices
Designing reliable, manufacturable printed circuit boards requires careful attention to many factors:
Schematic Best Practices
- Use consistent naming conventions for components and nets
- Include power/ground symbols and decoupling capacitors
- Add test points and programming headers for debugging
- Provide proper connectivity for unused pins (pull-up/down resistors, etc.)
Board Layout Best Practices
- Place decoupling capacitors close to IC power pins
- Provide solid power and ground planes for low impedance
- Route sensitive signals (clocks, analog, RF) away from noisy signals
- Use sufficient trace width for expected current
- Keep high-speed traces as short as possible and route on outer layers
- Avoid 90° trace corners that can cause signal reflections
- Follow manufacturer’s recommendations for component footprints and land patterns
Electromagnetic Compatibility (EMC)
PCBs can both emit and be susceptible to electromagnetic interference (EMI). Some ways to improve PCB electromagnetic compatibility include:
- Separate analog/digital sections and signals
- Provide shielding around sensitive circuits
- Use bypass capacitors to shunt high-frequency noise
- Minimize ground loops and provide low-impedance return paths
- Avoid splitting ground/power planes with signals
Thermal Management
High-power components can generate significant heat that must be dissipated to avoid damage. Some PCB thermal management techniques include:
- Provide adequate copper area for heat-generating parts
- Use large ground planes and thermal vias to spread heat
- Choose PCB materials with high thermal conductivity
- Provide heatsinks, fans, or other cooling solutions
- Monitor board temperatures during testing
Design for Manufacturing (DFM)
To ensure PCBs can be manufactured reliably and cost-effectively, designers should adhere to some basic DFM guidelines:
- Keep traces and spaces above the fabricator’s minimum specs
- Provide sufficient clearance around holes and board edges
- Avoid acute angles in copper features
- Use standard drill sizes and minimize hole count
- Panelize boards to maximize material usage
- Follow fab house design guides and stackup recommendations
Frequently Asked Questions (FAQ)
1. What is the difference between a breadboard and a PCB?
A breadboard is a temporary prototyping tool for building circuits without soldering. Components are plugged into a grid of holes that are internally connected in a specific pattern. PCBs are permanent, custom-designed boards with copper traces providing the electrical connections. Breadboards are used for quick proof-of-concept circuits, while PCBs are used for final products.
2. Can I make my own PCB at home?
Yes, it is possible to make simple PCBs at home using methods like toner transfer or photo etching. These involve transferring a printed circuit pattern onto a copper-clad board and then chemically etching away the unmasked copper. However, homemade PCBs are typically limited to single or double layer boards and lack professional features like solder mask and silkscreen.
3. How much does it cost to have a PCB made?
The cost of manufacturing a PCB depends on many factors, including the number of layers, board size, quantity, and turnaround time. Simple 2-layer PCBs can cost as little as $1-2 per board in volume, while complex multi-layer boards may cost $100 or more each. For prototypes or small runs, expect to pay around $30-100 for a handful of boards.
4. What software do I need to design a PCB?
To design a PCB, you will need schematic capture and board layout software. Some popular options are Autodesk EAGLE, KiCad, Altium Designer, and OrCAD PCB Designer. These programs range from free open-source tools up to expensive professional suites. Choose a package that fits your needs and budget and has an active user community for support.
5. How do I choose the right PCB material for my project?
The choice of PCB material depends on the electrical, mechanical, and environmental requirements of your application. For most common uses, standard FR-4 glass-reinforced epoxy is a good choice. If your PCB will be subjected to high temperatures or repeated flexing, you may need a special material like high-Tg FR-4 or flexible polyimide. For high-frequency circuits, low-loss materials like Teflon or Rogers laminates are often used.
Conclusion
Printed circuit boards are the backbone of modern electronics, enabling the creation of compact, reliable, and mass-producible devices. From basic single-layer boards to complex multi-layer assemblies, PCBs come in many forms to suit different applications. Designing and manufacturing PCBs requires specialized knowledge and tools, but the process is well-established and accessible to both professionals and hobbyists. By understanding the fundamentals of PCB materials, layout, and assembly, engineers and makers can create custom circuits that power the world around us.
Leave a Reply