Introduction to PTC Thermistors
PTC (Positive Temperature Coefficient) thermistors are temperature-sensitive resistors whose resistance increases significantly with rising temperature. Unlike traditional resistors that maintain a relatively stable resistance across a wide temperature range, PTC thermistors exhibit a sharp increase in resistance once they reach a specific temperature threshold, known as the Curie point or switching temperature.
This unique property makes PTC thermistors ideal for various applications in electronic circuits, including:
- Over-current protection
- Over-temperature protection
- Temperature sensing and control
- Inrush current limiting
- Self-regulating heating elements
How PTC Thermistors Work
PTC thermistors are typically made from polycrystalline ceramic materials, such as barium titanate or lead titanate, which have a perovskite crystal structure. At temperatures below the Curie point, the material exhibits a low, stable resistance. However, as the temperature rises and reaches the Curie point, the resistance increases dramatically, often by several orders of magnitude.
This sudden increase in resistance is attributed to the material’s ferroelectric properties. Below the Curie point, the ceramic material has a ferroelectric phase, where electric dipoles within the crystal structure are aligned, allowing for easy current flow. As the temperature rises above the Curie point, the material undergoes a phase transition to a paraelectric state, where the electric dipoles become disordered, resulting in a higher resistance.
The Curie point of a PTC thermistor can be tailored by adjusting the composition of the ceramic material during manufacturing. This allows for the production of PTC thermistors with specific switching temperatures to suit various applications.
Key Characteristics of PTC Thermistors
Resistance-Temperature Relationship
The resistance-temperature relationship of a PTC thermistor is highly nonlinear and is typically characterized by three distinct regions:
- Low-temperature region: Below the Curie point, the resistance remains relatively stable and low.
- Switching region: As the temperature approaches the Curie point, the resistance begins to increase rapidly. This region is characterized by a steep positive temperature coefficient.
- High-temperature region: Above the Curie point, the resistance continues to increase but at a slower rate compared to the switching region.
The resistance-temperature curve of a PTC thermistor can be approximated using the Steinhart-Hart equation:
1/T = A + B ln(R) + C [ln(R)]³
Where:
– T is the absolute temperature in Kelvin
– R is the resistance of the thermistor at temperature T
– A, B, and C are constants specific to the thermistor material and are determined through calibration
Switching Temperature (Curie Point)
The switching temperature, or Curie point, is the temperature at which the resistance of the PTC thermistor begins to increase rapidly. This temperature is determined by the composition of the ceramic material and can be customized during manufacturing to suit specific applications.
Common switching temperatures for PTC thermistors range from 60°C to 180°C, although some specialized devices may have switching temperatures outside this range.
Resistance Ratio
The resistance ratio is the ratio of the PTC thermistor’s resistance at a specified high temperature (usually 25°C above the switching temperature) to its resistance at a low temperature (typically 25°C). This ratio quantifies the magnitude of the resistance change that occurs when the thermistor reaches its switching temperature.
Resistance ratios for PTC thermistors can vary from a few hundred to several thousand, depending on the material composition and design.
Response Time
The response time of a PTC thermistor is the time required for the device to reach a specified percentage (usually 63.2% or 90%) of its final resistance value after a step change in temperature. Response times are influenced by factors such as the thermistor’s size, shape, and thermal mass, as well as the surrounding environment.
Typical response times for PTC thermistors range from a few seconds to several minutes, depending on the specific device and application.
Applications of PTC Thermistors
Over-Current Protection
PTC thermistors are commonly used as resettable fuses for over-current protection in electronic circuits. When the current flowing through the thermistor exceeds a specified threshold, the device heats up due to Joule heating. As the temperature rises above the switching point, the resistance increases dramatically, effectively limiting the current flow and protecting the circuit from damage.
Once the fault condition is removed and the thermistor cools down below its switching temperature, its resistance returns to its low value, allowing normal circuit operation to resume. This self-resetting behavior eliminates the need for manual fuse replacement, making PTC thermistors a convenient and cost-effective solution for over-current protection.
Over-Temperature Protection
PTC thermistors can also be used for over-temperature protection in electronic devices. By placing a PTC thermistor in close proximity to temperature-sensitive components, such as batteries or power transistors, the thermistor can detect excessive heat generation and limit current flow to prevent thermal runaway or damage.
When the temperature of the protected component rises above the PTC thermistor’s switching point, the increased resistance of the thermistor reduces the current flow, allowing the component to cool down. This temperature-dependent current limiting action helps maintain a safe operating temperature for the protected device.
Temperature Sensing and Control
The temperature-dependent resistance of PTC thermistors makes them suitable for temperature sensing and control applications. By incorporating a PTC thermistor into a voltage divider or Wheatstone bridge circuit, the temperature can be measured by monitoring the voltage across the thermistor.
PTC thermistors can be used in various temperature sensing and control applications, such as:
- Temperature monitoring in electronic devices
- Thermal management in power electronics
- Environmental temperature sensing
- Temperature compensation in precision circuits
To achieve accurate temperature measurements, the thermistor must be calibrated, and the Steinhart-Hart equation coefficients must be determined for the specific device.
Inrush Current Limiting
PTC thermistors are often employed as inrush current limiters in power supply circuits. During the initial power-up of capacitive loads, such as switch-mode power supplies or large capacitor banks, a high inrush current can occur, potentially damaging components or causing voltage drops in the supply line.
By placing a PTC thermistor in series with the load, the high initial current causes the thermistor to heat up rapidly, increasing its resistance and limiting the inrush current. As the capacitive load charges and the current decreases, the thermistor cools down, and its resistance returns to a low value, allowing normal operation to continue.
This inrush current limiting action helps protect components from excessive current stress and improves the overall reliability of the power supply circuit.
Self-Regulating Heating Elements
PTC thermistors can be used as self-regulating heating elements in various applications, such as:
- Battery warmers
- Automotive air intake heaters
- Consumer appliances (e.g., hair dryers, coffee makers)
- Industrial process heating
When a voltage is applied across a PTC thermistor, it generates heat due to Joule heating. As the temperature of the thermistor increases, its resistance rises, limiting the current flow and, consequently, the heat generation. This self-regulating behavior allows the thermistor to maintain a relatively constant temperature without the need for external temperature control circuitry.
Self-regulating PTC heating elements offer several advantages over traditional fixed-resistance heating elements, including:
- Overheating protection: The PTC thermistor automatically limits the temperature to a safe level, preventing thermal runaway and damage.
- Simplified control: The self-regulating nature of PTC thermistors eliminates the need for complex temperature control systems.
- Energy efficiency: PTC thermistors consume less power as they approach their equilibrium temperature, resulting in energy savings compared to fixed-resistance heating elements.
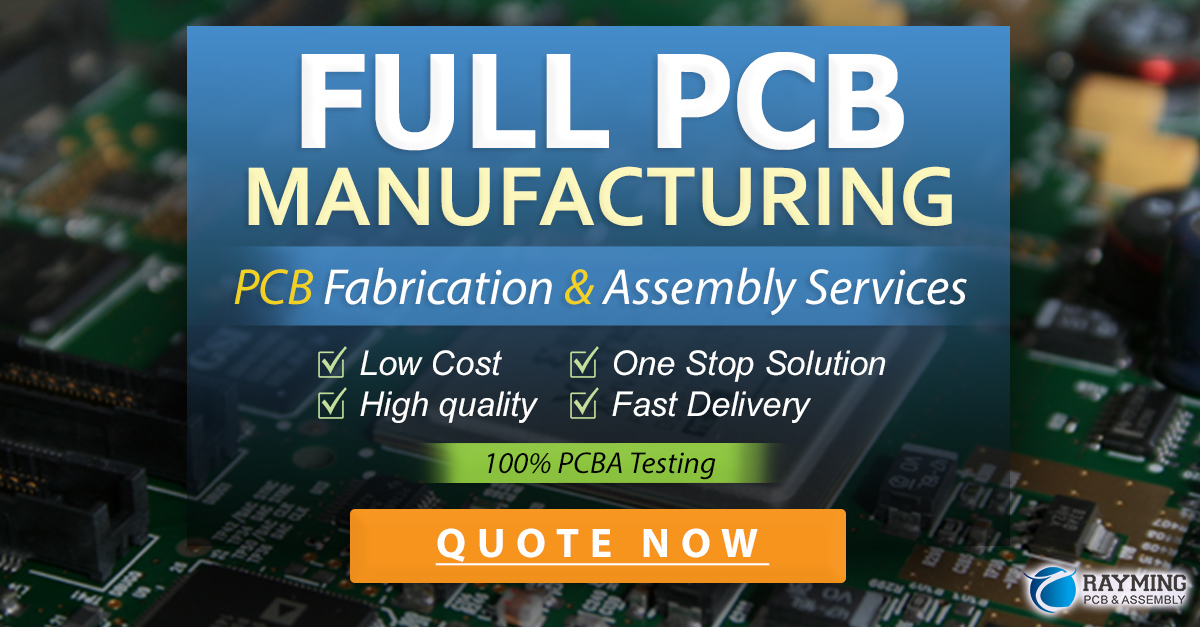
Selecting the Right PTC Thermistor
When choosing a PTC thermistor for a specific application, several key parameters must be considered:
-
Switching temperature: Select a thermistor with a switching temperature suitable for the application’s temperature range and protection requirements.
-
Resistance ratio: Consider the resistance ratio required to achieve the desired current limiting or temperature sensing performance.
-
Voltage and current ratings: Ensure that the thermistor can handle the maximum voltage and current expected in the application.
-
Package type: Choose a package type (e.g., leaded, surface-mount, or customized) that is compatible with the circuit layout and assembly process.
-
Response time: Consider the required response time for the application, and select a thermistor with an appropriate size and thermal mass.
-
Environmental factors: Take into account the operating environment, including temperature range, humidity, and potential exposure to contaminants, and select a thermistor with suitable environmental ratings.
Consulting manufacturer datasheets and application notes can help in selecting the most appropriate PTC thermistor for a given application. In some cases, custom-designed PTC thermistors may be necessary to meet specific performance or dimensional requirements.
Table 1: Comparison of Common PTC Thermistor Switching Temperatures
Switching Temperature | Typical Applications |
---|---|
60°C | Battery protection, over-temperature protection |
80°C | Over-current protection, inrush current limiting |
100°C | Temperature sensing, self-regulating heating |
120°C | Over-temperature protection, thermal cutoffs |
150°C | High-temperature sensing, industrial applications |
Table 2: Resistance Ratio Examples for PTC Thermistors
Resistance Ratio | Typical Applications |
---|---|
100:1 | Temperature sensing, inrush current limiting |
1000:1 | Over-current protection, self-regulating heating |
10000:1 | High-sensitivity temperature sensing, thermal cutoffs |
Frequently Asked Questions (FAQ)
- What is the main difference between a PTC thermistor and an NTC thermistor?
-
A PTC (Positive Temperature Coefficient) thermistor exhibits an increase in resistance with rising temperature, while an NTC (Negative Temperature Coefficient) thermistor exhibits a decrease in resistance with rising temperature.
-
Can PTC thermistors be used as temperature sensors?
-
Yes, PTC thermistors can be used as temperature sensors. Their resistance change with temperature allows them to be used in temperature measurement and control applications, although they are less commonly used than NTC thermistors for this purpose due to their highly nonlinear response.
-
How do PTC thermistors protect against over-current conditions?
-
When the current flowing through a PTC thermistor exceeds a certain threshold, the device heats up due to Joule heating. As the temperature rises above the switching point, the resistance increases dramatically, limiting the current flow and protecting the circuit from damage.
-
Are PTC thermistors resettable?
-
Yes, PTC thermistors are resettable. Once the fault condition is removed and the thermistor cools down below its switching temperature, its resistance returns to its low value, allowing normal circuit operation to resume without the need for manual replacement.
-
What factors should be considered when selecting a PTC thermistor for a specific application?
- When selecting a PTC thermistor, consider factors such as the required switching temperature, resistance ratio, voltage and current ratings, package type, response time, and environmental conditions. Consult manufacturer datasheets and application notes to choose the most suitable PTC thermistor for your application.
Conclusion
PTC thermistors are versatile temperature-sensitive resistors that play crucial roles in electronic circuit protection and temperature sensing applications. Their unique characteristic of exhibiting a sharp increase in resistance above a specific temperature threshold makes them ideal for over-current protection, over-temperature protection, temperature sensing, inrush current limiting, and self-regulating heating.
By understanding the key characteristics and applications of PTC thermistors, engineers and designers can effectively utilize these devices to enhance the reliability, safety, and performance of electronic circuits. Proper selection of PTC thermistors based on factors such as switching temperature, resistance ratio, and environmental considerations is essential for achieving optimal results in specific applications.
As technology advances and new challenges arise in the electronics industry, PTC thermistors will continue to be valuable components in ensuring the protection and proper functioning of electronic devices across a wide range of industries and applications.
Leave a Reply