Introduction to PCBA Defects
Printed Circuit Board Assembly (PCBA) is a complex process that involves multiple steps and components. Despite advancements in technology and manufacturing processes, PCBA defects can still occur, leading to reduced product quality, increased production costs, and delays in time-to-market. Identifying and addressing these defects is crucial for ensuring the reliability and functionality of the final product.
In this article, we will discuss seven common PCBA manufacturing defects and their solutions. By understanding these defects and implementing the appropriate measures, manufacturers can minimize their occurrence and improve the overall quality of their PCBAs.
Common PCBA Defects
1. Solder Bridges
Solder bridges, also known as shorts, occur when excess solder connects two or more adjacent pins or pads on a PCBA, causing an unintended electrical connection. This defect can lead to short circuits, malfunctions, and even permanent damage to the components.
Causes of Solder Bridges
- Excessive solder paste application
- Improper solder paste stencil design
- Incorrect solder paste viscosity
- Inadequate cleaning of the stencil between prints
- Improper placement of components
Solutions for Solder Bridges
- Optimize solder paste stencil design:
- Ensure proper aperture size and shape
- Maintain adequate spacing between pads
- Use stepped stencils for fine-pitch components
- Control solder paste application:
- Regularly maintain and calibrate solder paste printers
- Monitor solder paste viscosity and replace as needed
- Implement solder paste inspection (SPI) systems
- Improve cleaning processes:
- Regularly clean solder paste stencils
- Use appropriate cleaning solutions and methods
- Enhance component placement accuracy:
- Use high-precision pick-and-place machines
- Implement vision systems for component alignment
- Conduct regular maintenance and calibration of placement equipment
2. Cold Solder Joints
Cold solder joints occur when the solder fails to melt and flow properly, resulting in a weak and unreliable connection between the component and the PCB pad. These joints are characterized by a dull, grainy appearance and can cause intermittent connections or complete failure of the affected component.
Causes of Cold Solder Joints
- Insufficient heat during the soldering process
- Contaminated or oxidized PCB pads or component leads
- Improper solder paste composition or quality
- Inadequate flux activity
- Excessive cooling rate after soldering
Solutions for Cold Solder Joints
- Optimize reflow soldering profile:
- Ensure proper preheat, soak, and reflow temperatures
- Maintain appropriate ramp rates and dwell times
- Monitor and control the cooling rate
- Improve PCB and component quality:
- Use high-quality PCBs with proper surface finish
- Ensure components are free from contamination and oxidation
- Store components and PCBs in a controlled environment
- Use appropriate solder paste and flux:
- Select solder paste with the correct alloy composition and particle size
- Choose flux with adequate activity level for the application
- Regularly monitor and control solder paste quality
- Enhance soldering process control:
- Implement in-line monitoring systems for reflow ovens
- Conduct regular maintenance and calibration of soldering equipment
- Use nitrogen reflow ovens to reduce oxidation
3. Tombstoning
Tombstoning, also known as drawbridging, is a defect that occurs when a surface-mount component stands up on one end during the reflow soldering process. This defect is most commonly seen with small, lightweight components such as chip resistors and capacitors.
Causes of Tombstoning
- Uneven heating of the component during reflow
- Imbalanced solder paste volume on component pads
- Incorrect component placement or alignment
- Inadequate or excessive solder paste
- Improper reflow profile
Solutions for Tombstoning
- Balance solder paste volume:
- Ensure equal amounts of solder paste on component pads
- Optimize solder paste stencil design for even paste distribution
- Improve component placement accuracy:
- Use high-precision pick-and-place machines
- Implement vision systems for component alignment
- Ensure proper centering of components on pads
- Optimize reflow soldering profile:
- Ensure even heating across the PCB
- Maintain appropriate ramp rates and dwell times
- Minimize temperature gradients during reflow
- Use appropriate components and PCB design:
- Select components with balanced terminations
- Design PCB pads with the proper size and shape for the component
- Consider using solder thieves or anchor pads to balance solder volume
4. Lifted Leads
Lifted leads occur when the leads of a through-hole component are not properly soldered to the PCB, causing the lead to lift away from the board. This defect can result in intermittent or open connections, compromising the reliability of the assembly.
Causes of Lifted Leads
- Insufficient solder fillets
- Contamination or oxidation of component leads or PCB holes
- Improper lead forming or trimming
- Mechanical stress during handling or testing
- Thermal stress during soldering or operation
Solutions for Lifted Leads
- Ensure proper soldering process:
- Use appropriate soldering iron temperature and tip size
- Apply sufficient solder to create a proper fillet
- Maintain appropriate dwell time for solder flow
- Improve PCB and component quality:
- Ensure PCB holes are clean and free from contamination
- Use components with properly formed and trimmed leads
- Consider using pre-tinned component leads
- Minimize mechanical stress:
- Handle PCBAs with care during assembly and testing
- Use appropriate fixtures and supports to prevent component movement
- Manage thermal stress:
- Optimize soldering temperature and dwell time
- Use thermal relief pads for high-thermal-mass components
- Consider using strain relief features in PCB design
5. Solder Balls
Solder balls are small, spherical balls of solder that can form during the reflow soldering process. These balls can cause short circuits, bridging, or other reliability issues if they come into contact with other components or conductive surfaces.
Causes of Solder Balls
- Excessive solder paste application
- Improper solder paste composition or quality
- Ineffective cleaning of the solder paste stencil
- Incorrect reflow profile or cooling rate
- Contamination or oxidation of the PCB surface
Solutions for Solder Balls
- Control solder paste application:
- Optimize solder paste stencil design for proper paste volume
- Regularly maintain and calibrate solder paste printers
- Implement solder paste inspection (SPI) systems
- Use appropriate solder paste:
- Select solder paste with the correct alloy composition and particle size
- Ensure solder paste is free from contamination and stored properly
- Improve stencil cleaning:
- Regularly clean solder paste stencils
- Use appropriate cleaning solutions and methods
- Consider using automated stencil cleaning systems
- Optimize reflow soldering profile:
- Ensure proper preheat, soak, and reflow temperatures
- Maintain appropriate ramp rates and dwell times
- Control the cooling rate to minimize solder ball formation
- Maintain PCB cleanliness:
- Ensure PCBs are free from contamination and oxidation
- Use appropriate cleaning processes before solder paste application
6. Component Misalignment
Component misalignment occurs when a surface-mount component is not properly aligned with its intended pads on the PCB. This defect can lead to poor solder joints, reduced electrical performance, and potential short circuits.
Causes of Component Misalignment
- Incorrect component placement during pick-and-place process
- Poor solder paste print quality or inconsistent paste volume
- Warped or distorted PCBs
- Inadequate support or fixturing during reflow soldering
- Improper component packaging or handling
Solutions for Component Misalignment
- Enhance pick-and-place process:
- Use high-precision pick-and-place machines
- Implement vision systems for component alignment
- Regularly calibrate and maintain placement equipment
- Improve solder paste printing:
- Optimize solder paste stencil design for consistent paste volume
- Regularly maintain and calibrate solder paste printers
- Implement solder paste inspection (SPI) systems
- Ensure PCB quality:
- Use high-quality, flat PCBs
- Implement PCB warpage monitoring and control measures
- Provide adequate support during reflow:
- Use appropriate fixturing and support materials
- Ensure even heating and cooling during reflow soldering
- Handle components properly:
- Use appropriate component packaging and handling methods
- Ensure components are free from damage or distortion
7. Insufficient Solder
Insufficient solder refers to a condition where there is not enough solder to create a proper joint between the component and the PCB pad. This defect can result in weak or open connections, leading to reliability issues and potential failures.
Causes of Insufficient Solder
- Inadequate solder paste volume
- Improper solder paste stencil design
- Solder paste contamination or degradation
- Incorrect reflow profile or insufficient heat
- Oxidation or contamination of PCB pads or component leads
Solutions for Insufficient Solder
- Optimize solder paste application:
- Ensure proper solder paste stencil design for adequate paste volume
- Regularly maintain and calibrate solder paste printers
- Implement solder paste inspection (SPI) systems
- Maintain solder paste quality:
- Store solder paste under appropriate conditions
- Monitor solder paste shelf life and replace as needed
- Ensure solder paste is free from contamination
- Optimize reflow soldering profile:
- Ensure sufficient heat is applied during reflow
- Maintain appropriate ramp rates and dwell times
- Consider using nitrogen reflow ovens to reduce oxidation
- Ensure PCB and component cleanliness:
- Use high-quality PCBs with clean and properly finished pads
- Ensure components are free from contamination and oxidation
- Implement appropriate cleaning processes before soldering
Data Visualization
To better understand the impact of PCBA defects on manufacturing processes, consider the following table:
Defect | Occurrence Rate | Impact on Yield | Rework Time |
---|---|---|---|
Solder Bridges | 2-5% | High | Moderate |
Cold Solder Joints | 1-3% | High | High |
Tombstoning | 0.5-2% | Moderate | Low |
Lifted Leads | 1-2% | Moderate | High |
Solder Balls | 1-3% | Low | Low |
Component Misalignment | 1-2% | Moderate | Moderate |
Insufficient Solder | 2-4% | High | Moderate |
This table provides a general overview of the occurrence rates, impact on yield, and rework time associated with each defect. However, actual values may vary depending on the specific manufacturing processes, equipment, and materials used.
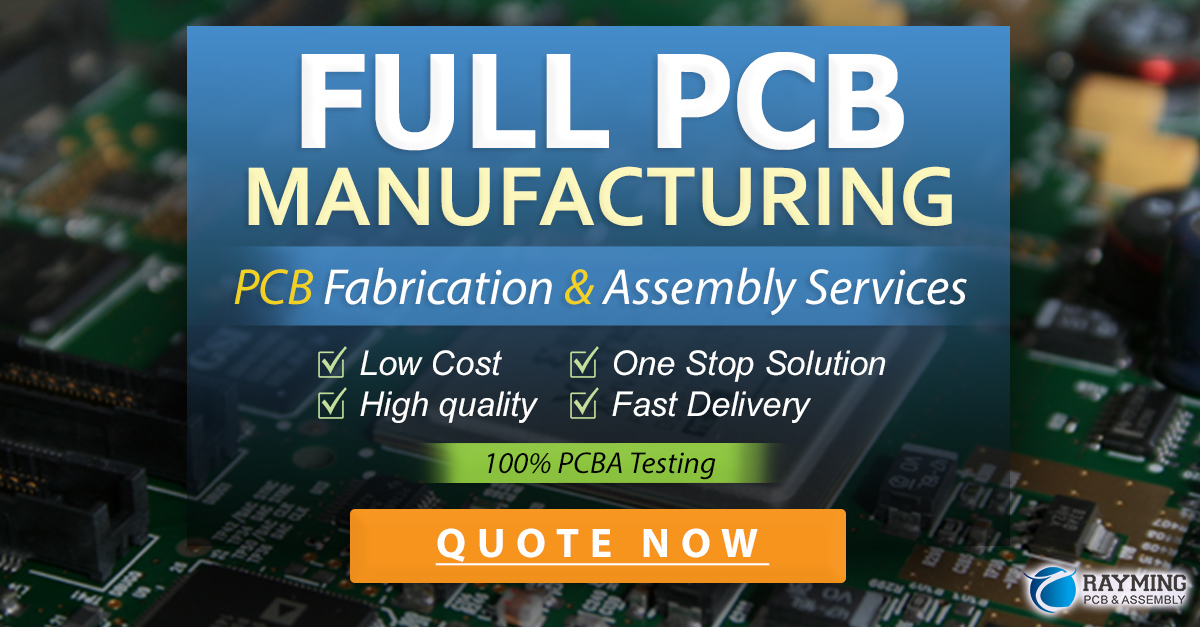
Frequently Asked Questions (FAQ)
- What are the most common causes of PCBA defects?
- Improper solder paste application
- Incorrect reflow soldering profiles
- Poor component placement accuracy
- Contamination or oxidation of PCBs or components
-
Inadequate cleaning processes
-
How can PCBA defects be prevented?
- Implementing robust process controls and monitoring systems
- Regularly maintaining and calibrating manufacturing equipment
- Using high-quality materials and components
- Providing proper training and guidance to production staff
-
Conducting thorough inspections and testing at various stages of production
-
What are the consequences of PCBA defects?
- Reduced product quality and reliability
- Increased production costs due to rework and scrap
- Delayed time-to-market
- Potential damage to brand reputation
-
Increased risk of product recalls or warranty claims
-
What role does solder paste play in PCBA defects?
- Solder paste is a critical material in the PCBA process, responsible for forming the electrical and mechanical connections between components and the PCB
- Improper solder paste application, composition, or storage can lead to various defects such as solder bridges, cold solder joints, and solder balls
-
Ensuring the quality and consistency of solder paste is essential for minimizing PCBA defects
-
How can automated inspection systems help reduce PCBA defects?
- Automated inspection systems, such as solder paste inspection (SPI), automated optical inspection (AOI), and X-ray inspection (AXI), can quickly and accurately detect various defects
- These systems provide real-time feedback, allowing for early identification and correction of issues before they propagate through the production process
- Automated inspection systems can also collect valuable data for process optimization and continuous improvement initiatives
Conclusion
PCBA manufacturing defects can have significant impacts on product quality, production costs, and time-to-market. By understanding the common defects, their causes, and potential solutions, manufacturers can take proactive steps to minimize their occurrence and improve overall PCBA quality.
Implementing robust process controls, using high-quality materials, and regularly maintaining equipment are essential for preventing defects. Additionally, leveraging automated inspection systems and data analysis can help identify issues early and drive continuous improvement efforts.
By addressing PCBA defects through a combination of best practices, advanced technologies, and a commitment to quality, manufacturers can ensure the reliability and performance of their products while reducing costs and improving customer satisfaction.
Leave a Reply