Introduction to PCB
A Printed Circuit Board, or PCB, is the foundation of modern electronic devices. It is a flat board made of insulating material, such as fiberglass or plastic, with conductive pathways etched or printed onto its surface. These pathways, known as traces, connect various electronic components like resistors, capacitors, and integrated circuits, allowing them to function together as a complete electronic system.
PCBs have revolutionized the electronics industry by providing a reliable, compact, and cost-effective way to mass-produce electronic devices. They are found in almost every electronic device we use today, from smartphones and computers to medical equipment and aerospace technology.
History of PCBs
The concept of printed circuits dates back to the early 20th century. In 1903, Albert Hanson, a German inventor, filed a patent for a method of creating conductive patterns on an insulating substrate. However, it wasn’t until the 1940s that printed circuits began to gain widespread use.
During World War II, the U.S. military required a more reliable and efficient method of producing electronic devices for warfare. In 1943, Paul Eisler, an Austrian engineer, developed a process for etching conductive pathways onto a non-conductive base material, which became the foundation for modern PCB manufacturing.
In the 1950s and 1960s, PCB technology advanced rapidly, with the introduction of double-sided boards, plated through-holes, and multi-layer boards. These innovations allowed for more complex circuits and higher component densities, paving the way for the miniaturization of electronic devices.
Types of PCBs
There are several types of PCBs, each with its own unique characteristics and applications.
Single-layer PCB
A single-layer PCB has conductive traces on only one side of the insulating substrate. These boards are the simplest and most cost-effective type of PCB, making them ideal for low-complexity circuits and prototypes.
Double-layer PCB
Double-layer PCBs have conductive traces on both sides of the insulating substrate, allowing for more complex circuits and higher component densities compared to single-layer boards. The two layers are connected using through-hole technology or vias.
Multi-layer PCB
Multi-layer PCBs consist of three or more conductive layers separated by insulating layers. These boards offer the highest component density and complexity, making them suitable for advanced electronic devices like smartphones, computers, and medical equipment.
PCB Type | Layers | Complexity | Cost | Applications |
---|---|---|---|---|
Single-layer | 1 | Low | Low | Simple circuits, prototypes |
Double-layer | 2 | Medium | Medium | More complex circuits, higher component density |
Multi-layer | 3+ | High | High | Advanced electronic devices, high component density |
Flexible PCB
Flexible PCBs, or flex circuits, are made using flexible insulating materials like polyimide or PEEK. These boards can bend and fold, making them ideal for applications where space is limited or where the device requires movement, such as in wearable electronics or aerospace technology.
Rigid-Flex PCB
Rigid-flex PCBs combine the benefits of both rigid and flexible PCBs. They consist of rigid PCB sections connected by flexible PCB sections, allowing for three-dimensional packaging and improved reliability in applications that require both stability and flexibility.
PCB Manufacturing Process
The PCB manufacturing process involves several steps, each critical to ensuring the quality and reliability of the final product.
Design and Layout
The first step in PCB manufacturing is designing the circuit and creating the PCB layout using specialized software. The layout includes the placement of components, routing of traces, and the creation of solder pads and vias.
Printing and Etching
Once the layout is finalized, the design is printed onto the copper-clad insulating substrate using a photoresist process. The exposed areas of the photoresist are then developed and removed, leaving behind the desired conductive pattern. The unwanted copper is etched away using a chemical solution, leaving only the conductive traces.
Drilling and Plating
Holes are drilled into the board to accommodate through-hole components and vias. These holes are then plated with a conductive material, typically copper, to create electrical connections between layers.
Solder Mask and Silkscreen
A solder mask, usually green in color, is applied to the board to protect the copper traces from oxidation and to prevent solder bridges during the assembly process. A silkscreen layer is then added to provide text and symbols for component identification and assembly guidance.
Surface Finishing
The exposed copper pads are coated with a surface finish, such as HASL (Hot Air Solder Leveling), ENIG (Electroless Nickel Immersion Gold), or OSP (Organic Solderability Preservative), to protect the copper from oxidation and to improve solderability.
Electrical Testing
Finally, the manufactured PCBs undergo electrical testing to ensure that all connections are correct and that the board functions as intended. This step helps to identify any manufacturing defects or design issues before the boards are assembled with components.
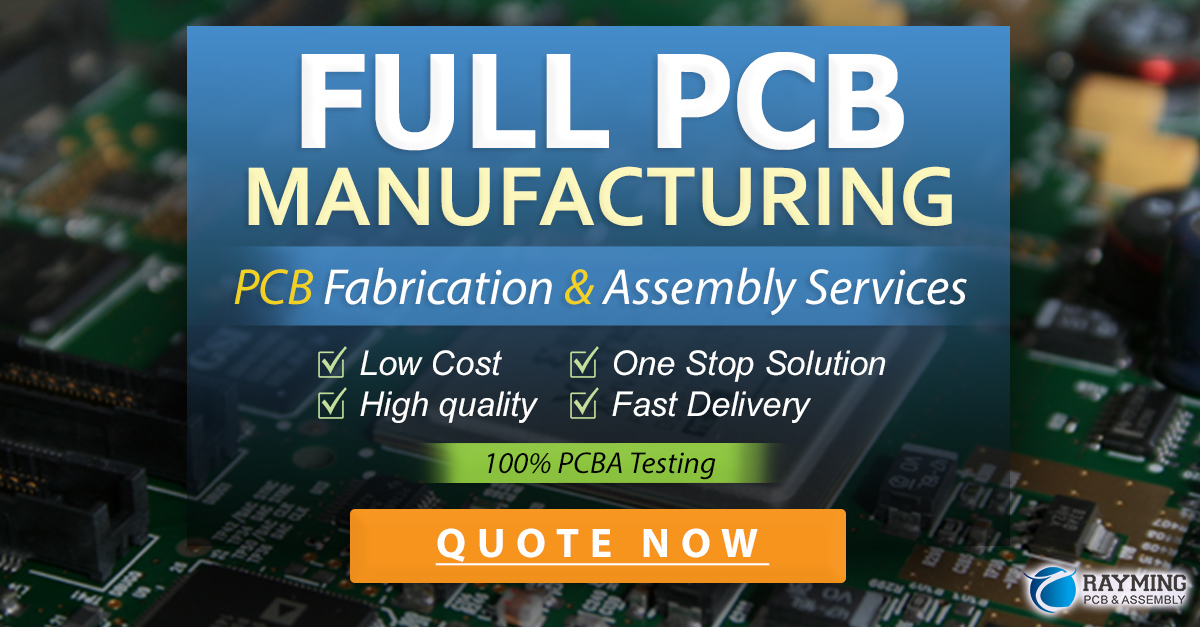
PCB Assembly
Once the PCBs are manufactured, they are ready for assembly. The assembly process involves soldering electronic components onto the board.
Through-Hole Assembly
Through-hole assembly involves inserting component leads through holes in the PCB and soldering them to the pads on the opposite side of the board. This method is typically used for larger components or in applications where high mechanical strength is required.
Surface Mount Assembly
Surface mount assembly, or SMT, involves placing components directly onto pads on the surface of the PCB and soldering them in place. SMT allows for smaller components and higher component densities compared to through-hole assembly.
Assembly Method | Component Size | Component Density | Mechanical Strength |
---|---|---|---|
Through-Hole | Larger | Lower | Higher |
Surface Mount (SMT) | Smaller | Higher | Lower |
Manual vs. Automated Assembly
PCB assembly can be done manually or using automated equipment. Manual assembly is suitable for low-volume production or prototypes, while automated assembly, using pick-and-place machines and reflow ovens, is more efficient for high-volume production.
PCB Design Considerations
When designing a PCB, several factors must be considered to ensure optimal performance, reliability, and manufacturability.
Component Placement
Components should be placed in a logical manner, considering factors such as signal integrity, heat dissipation, and mechanical constraints. Proper component placement can minimize the length of traces, reduce electromagnetic interference, and improve the overall performance of the circuit.
Trace Routing
Traces should be routed to minimize signal interference and to ensure proper signal timing. Factors such as trace width, spacing, and impedance must be considered to maintain signal integrity and to prevent issues like crosstalk and reflections.
Power and Ground Planes
Proper power and ground plane design is essential for minimizing noise and ensuring stable power delivery to components. Techniques such as power plane partitioning and the use of decoupling capacitors can help to reduce power supply noise and improve overall system stability.
Thermal Management
Thermal management is critical for ensuring the long-term reliability of electronic components. PCB designers must consider factors such as component power dissipation, ambient temperature, and available cooling methods when designing the board layout and selecting components.
Design for Manufacturing (DFM)
Design for Manufacturing, or DFM, involves designing the PCB with the manufacturing process in mind. This includes considering factors such as minimum trace width and spacing, hole sizes, and soldermask and silkscreen requirements. By adhering to DFM guidelines, designers can ensure that their boards are manufacturable and can help to reduce production costs and lead times.
Advantages of PCBs
PCBs offer several advantages over other electronic assembly methods, such as point-to-point wiring or wire-wrap.
Reliability
PCBs provide a stable and reliable platform for electronic components, with well-defined connections and a solid mechanical structure. This reliability is essential for applications where failure is not an option, such as in medical devices or aerospace systems.
Cost-effectiveness
PCBs enable the mass production of electronic devices at a lower cost compared to other assembly methods. The automated manufacturing process and the ability to produce high volumes of identical boards make PCBs a cost-effective choice for electronic product development.
Miniaturization
PCBs allow for the miniaturization of electronic devices by enabling high component densities and compact packaging. This is particularly important in applications where space is limited, such as in smartphones, wearables, and IoT devices.
Consistency
The automated PCB manufacturing process ensures that each board is identical, with consistent electrical and mechanical properties. This consistency is essential for ensuring the quality and reliability of the final product.
Applications of PCBs
PCBs are used in a wide range of applications across various industries.
Consumer Electronics
PCBs are the foundation of modern consumer electronics, such as smartphones, laptops, televisions, and home appliances. The compact size, reliability, and cost-effectiveness of PCBs have enabled the rapid growth and innovation in the consumer electronics industry.
Automotive Electronics
PCBs play a critical role in automotive electronics, powering systems such as engine control units, infotainment systems, and advanced driver assistance systems (ADAS). The harsh operating environment in vehicles requires PCBs that can withstand extreme temperatures, vibrations, and moisture.
Medical Devices
PCBs are used in a variety of medical devices, from patient monitors and imaging equipment to implantable devices like pacemakers and neurostimulators. The reliability and precision of PCBs are essential in medical applications, where patient safety and device performance are paramount.
Industrial Automation
PCBs are used in industrial automation systems, such as programmable logic controllers (PLCs), sensors, and motor drives. The rugged construction and reliable performance of PCBs make them suitable for the demanding conditions found in industrial environments.
Aerospace and Defense
PCBs are used in a range of aerospace and defense applications, from satellites and aircraft to military communications and radar systems. The high reliability and performance requirements in these applications demand specialized PCB materials and manufacturing techniques.
Future of PCBs
As electronic devices continue to advance and evolve, so too will PCB technology. Some of the key trends and developments shaping the future of PCBs include:
Advanced Materials
New PCB materials, such as high-frequency laminates and thermally conductive substrates, are being developed to meet the demands of emerging applications like 5G communications and high-power electronics.
Embedded Components
Embedding components, such as resistors, capacitors, and even active devices, within the PCB substrate can help to further reduce the size and improve the performance of electronic devices.
3D Printing
Additive manufacturing techniques, like 3D printing, are being explored as a means of producing PCBs with complex geometries and unique material properties.
Artificial Intelligence
AI-driven design tools and optimization algorithms are being developed to help streamline the PCB design process and to enable the creation of more efficient and high-performance designs.
As these and other technologies continue to advance, PCBs will remain at the heart of electronic device development, enabling new innovations and shaping the future of the electronics industry.
Frequently Asked Questions (FAQ)
1. What is the difference between a PCB and a PCBA?
A PCB, or Printed Circuit Board, is the bare board without any electronic components attached. A PCBA, or Printed Circuit Board Assembly, is a PCB that has been populated with electronic components and is ready for use in an electronic device.
2. What are the most common PCB materials?
The most common PCB materials are FR-4, a glass-reinforced epoxy laminate, and polyimide, a flexible polymer material. Other materials, such as high-frequency laminates and metal-core substrates, are used in specialized applications.
3. What is the difference between through-hole and surface mount components?
Through-hole components have leads that are inserted into holes drilled in the PCB and soldered to pads on the opposite side of the board. Surface mount components are placed directly onto pads on the surface of the PCB and soldered in place. Surface mount components are generally smaller and allow for higher component densities compared to through-hole components.
4. What is the purpose of a solder mask on a PCB?
The solder mask is a protective layer applied to the copper traces on a PCB. It serves to protect the copper from oxidation, prevent solder bridges during assembly, and provide electrical insulation between adjacent traces.
5. How are PCBs tested for reliability?
PCBs undergo a variety of tests to ensure reliability, including visual inspection, automated optical inspection (AOI), in-circuit testing (ICT), and functional testing. Environmental stress tests, such as thermal cycling and humidity exposure, may also be performed to validate the board’s performance under various operating conditions.
Leave a Reply