Understanding Flexible PCB Materials
Flexible PCBs are typically made from a combination of a flexible polymer substrate and conductive traces. The most common materials used for the substrate include:
- Polyimide (PI)
- Polyester (PET)
- Flexible Copper Clad Laminate (FCCL)
- Liquid Crystal Polymer (LCP)
Each material has its own unique properties, advantages, and limitations, which we will discuss in detail throughout this article.
Polyimide (PI)
Polyimide is the most widely used material for flexible PCBs due to its excellent thermal stability, chemical resistance, and mechanical strength. It can withstand temperatures up to 300°C and has a low coefficient of thermal expansion (CTE), making it suitable for high-reliability applications. PI is also known for its high dielectric strength and good insulation properties.
Advantages of Polyimide
- High temperature resistance
- Excellent chemical resistance
- Good mechanical strength
- Low CTE
- High dielectric strength
Disadvantages of Polyimide
- Higher cost compared to other materials
- Requires specialized processing techniques
- Limited flexibility compared to other materials
Polyester (PET)
Polyester, particularly polyethylene terephthalate (PET), is another popular choice for flexible PCBs. PET is known for its good electrical properties, high flexibility, and low cost. It is commonly used in consumer electronics, such as keyboards, cameras, and mobile phones.
Advantages of Polyester
- High flexibility
- Good electrical properties
- Low cost
- Easily available
- Suitable for high-volume production
Disadvantages of Polyester
- Lower temperature resistance compared to polyimide
- Limited chemical resistance
- Lower mechanical strength than polyimide
Flexible Copper Clad Laminate (FCCL)
Flexible Copper Clad Laminate (FCCL) is a composite material consisting of a flexible polymer substrate, such as polyimide or polyester, bonded to a thin layer of copper foil. FCCLs are available in various thicknesses and copper weights, allowing designers to choose the most suitable combination for their specific application.
Advantages of FCCL
- Combines the benefits of the polymer substrate and copper foil
- Wide range of thicknesses and copper weights available
- Good thermal and electrical conductivity
- Suitable for fine-pitch circuitry
Disadvantages of FCCL
- Higher cost compared to bare polymer substrates
- Requires careful handling during processing to avoid damaging the copper layer
Liquid Crystal Polymer (LCP)
Liquid Crystal Polymer (LCP) is a high-performance thermoplastic material that offers exceptional electrical, thermal, and mechanical properties. LCP has a very low moisture absorption rate, making it suitable for applications exposed to harsh environments. It also has a low dielectric constant and dissipation factor, which are desirable for high-frequency applications.
Advantages of LCP
- Excellent electrical properties
- Low moisture absorption
- High thermal stability
- Good chemical resistance
- Suitable for high-frequency applications
Disadvantages of LCP
- Higher cost compared to other materials
- Limited availability and processing options
- Requires specialized design considerations
Factors to Consider When Choosing Flexible PCB Materials
When selecting the right material for your flexible PCB, several factors must be considered to ensure optimal performance and reliability. These factors include:
- Application requirements
- Environmental conditions
- Electrical properties
- Mechanical properties
- Cost and availability
Application Requirements
The first step in choosing the right flexible PCB material is to understand the specific requirements of your application. Consider the following aspects:
- Operating temperature range
- Bending and flexing requirements
- Space constraints
- Required lifespan
- Electrical performance needs
Based on these requirements, you can narrow down your material choices to those that best suit your application.
Environmental Conditions
The environment in which your flexible PCB will operate plays a crucial role in material selection. Consider the following environmental factors:
- Temperature extremes
- Humidity levels
- Chemical exposure
- UV radiation
- Mechanical stress
Choose a material that can withstand the environmental conditions your PCB will be exposed to, ensuring reliable performance and longevity.
Electrical Properties
The electrical properties of the flexible PCB material directly impact the performance of your circuit. Consider the following electrical properties when making your selection:
- Dielectric constant
- Dissipation factor
- Insulation resistance
- Dielectric strength
- Electrical conductivity
Select a material that meets your electrical performance requirements, such as low dielectric constant for high-frequency applications or high insulation resistance for sensitive circuits.
Mechanical Properties
The mechanical properties of the flexible PCB material determine its ability to withstand physical stress and maintain structural integrity. Consider the following mechanical properties:
- Tensile strength
- Elongation
- Tear resistance
- Flexural strength
- Dimensional stability
Choose a material that offers the necessary mechanical strength and flexibility for your application, ensuring reliable performance under the expected physical stresses.
Cost and Availability
Cost and availability are practical considerations that cannot be overlooked when selecting a flexible PCB material. Consider the following factors:
- Material cost per unit area
- Minimum order quantities
- Lead times
- Availability of processing options
- Compatibility with existing manufacturing processes
Strike a balance between performance, cost, and availability to ensure your material choice is both technically and economically viable.
Comparing Flexible PCB Materials
To help you make an informed decision, let’s compare the key properties of the most common flexible PCB materials:
Property | Polyimide (PI) | Polyester (PET) | FCCL | LCP |
---|---|---|---|---|
Temperature Resistance | High | Moderate | High | High |
Chemical Resistance | Excellent | Limited | Good | Good |
Mechanical Strength | High | Moderate | High | High |
Flexibility | Moderate | High | Moderate | Moderate |
Dielectric Constant | 3.5 | 3.2 | 3.5-4.5 | 2.9-3.2 |
Dissipation Factor | 0.002 | 0.015 | 0.02 | 0.002 |
Cost | High | Low | Moderate | High |
This comparison should serve as a general guide, but it’s essential to consult with your PCB manufacturer or material supplier for more detailed information specific to your application.
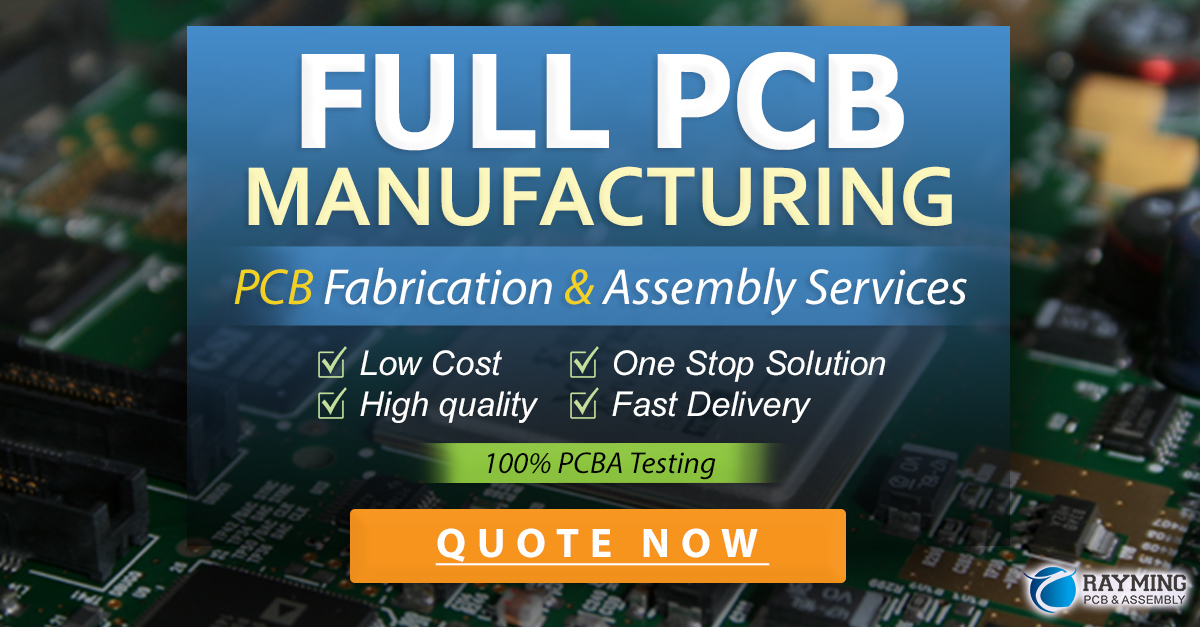
Frequently Asked Questions (FAQ)
-
Q: What is the most common material used for flexible PCBs?
A: Polyimide (PI) is the most widely used material for flexible PCBs due to its excellent thermal stability, chemical resistance, and mechanical strength. -
Q: Which flexible PCB material is best for high-frequency applications?
A: Liquid Crystal Polymer (LCP) is an excellent choice for high-frequency applications due to its low dielectric constant and dissipation factor. -
Q: Can I use polyester (PET) for high-temperature applications?
A: Polyester has limited temperature resistance compared to polyimide and may not be suitable for high-temperature applications. It is best to use polyimide or LCP for such applications. -
Q: Which flexible PCB material offers the highest flexibility?
A: Polyester (PET) offers the highest flexibility among the common flexible PCB materials, making it suitable for applications requiring frequent bending or folding. -
Q: How do I choose the right thickness and copper weight for my flexible PCB?
A: The choice of thickness and copper weight depends on your specific application requirements, such as electrical performance, mechanical stability, and space constraints. Consult with your PCB manufacturer or design team to determine the optimal combination for your needs.
Conclusion
Choosing the right material for your flexible PCB is a critical decision that directly impacts the performance, reliability, and durability of your electronic device. By understanding the unique properties, advantages, and limitations of each material and considering the specific requirements of your application, you can make an informed choice that ensures optimal results.
Remember to factor in environmental conditions, electrical and mechanical properties, cost, and availability when making your selection. Consult with your PCB manufacturer or material supplier for expert guidance and support throughout the design and manufacturing process.
By following the information and guidelines provided in this article, you can confidently navigate the world of flexible PCB materials and choose the best option for your needs, enabling you to create innovative, reliable, and high-performance electronic devices.
Leave a Reply