What are Gold Finger PCBs?
Gold finger PCBs, also known as edge connector PCBs or contact fingers, are printed circuit boards with gold-plated contact pads along one edge. These gold fingers allow the PCB to be plugged into a socket or slot for easy connection and disconnection. The gold plating provides excellent conductivity, durability, and corrosion resistance for a reliable electrical connection.
Gold finger PCBs are commonly used in various applications such as:
- Computer memory modules (RAM)
- Graphics cards
- Expansion cards
- Motherboards
- Industrial control systems
- Telecommunications equipment
Advantages of Gold Finger PCBs
High Conductivity
Gold is an excellent conductor of electricity, making it an ideal choice for the contact fingers on PCBs. The high conductivity ensures a low-resistance connection, minimizing signal loss and improving overall system performance.
Durability and Wear Resistance
Gold-plated fingers are highly durable and resistant to wear and tear. The gold plating protects the underlying copper from oxidation and corrosion, ensuring a reliable connection even after numerous insertion and removal cycles. This durability is particularly important in applications where frequent plugging and unplugging is required.
Corrosion Resistance
Gold is a noble metal that does not readily react with other substances, making it resistant to corrosion. This property is crucial for maintaining a stable connection in harsh environments where the PCB may be exposed to moisture, chemicals, or other corrosive agents.
Ease of Use
Gold finger PCBs offer a simple and convenient way to connect and disconnect PCBs without the need for soldering or additional connectors. The edge connector design allows for quick installation and removal, making maintenance and upgrades easier.
Manufacturing Process
The manufacturing process for gold finger PCBs involves several steps to ensure high quality and reliability:
-
PCB Fabrication: The PCB is fabricated using standard processes, including substrate selection, copper foil lamination, drilling, and plating.
-
Nickel Plating: A layer of nickel is plated onto the contact fingers to provide a barrier between the copper and the gold plating. Nickel helps improve the adhesion of the gold and prevents the formation of intermetallic compounds that can weaken the connection.
-
Gold Plating: The contact fingers are selectively plated with a thin layer of gold, typically using an electroplating process. The gold plating thickness is usually between 2 and 30 microinches (0.05 to 0.76 micrometers), depending on the application requirements.
-
Surface Finish: The remaining exposed copper on the PCB is coated with a surface finish, such as HASL (Hot Air Solder Leveling), ENIG (Electroless Nickel Immersion Gold), or OSP (Organic Solderability Preservative), to protect the copper and improve solderability.
-
Electrical Testing: The completed gold finger PCB undergoes electrical testing to ensure proper connectivity and functionality.
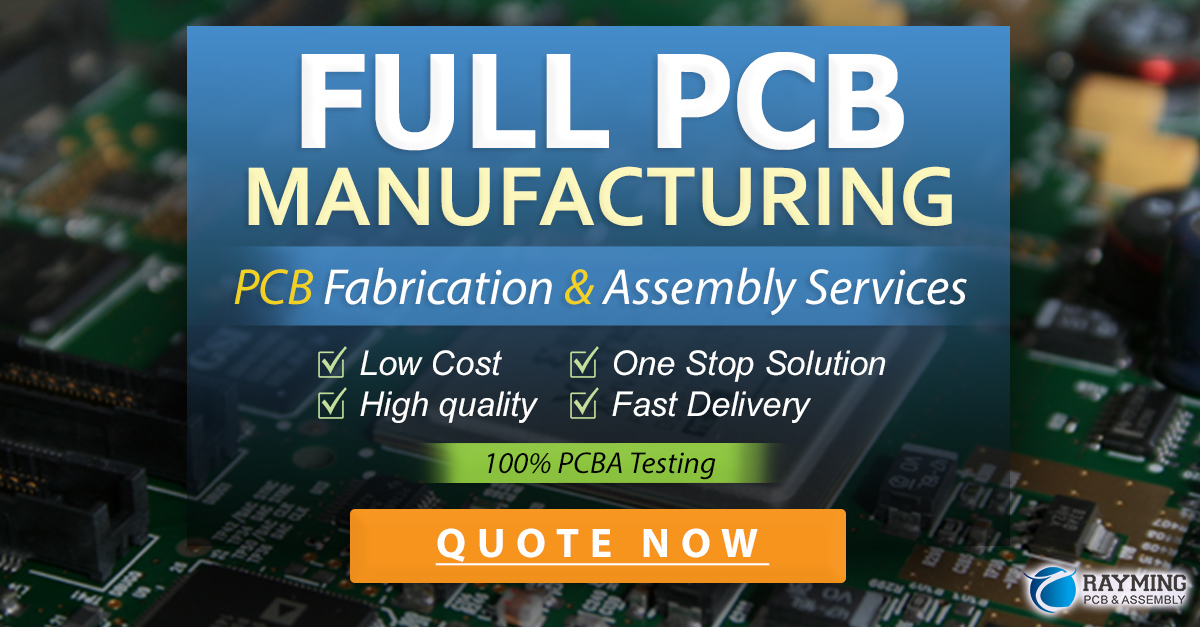
Design Considerations
When designing a gold finger PCB, several factors must be considered to ensure optimal performance and reliability:
Contact Finger Dimensions
The dimensions of the contact fingers, including the pitch (distance between the center of each finger), width, and length, must be carefully designed to match the corresponding socket or slot. Standard pitches for gold finger PCBs include:
Pitch | Application |
---|---|
1.27 mm | DDR2, DDR3, DDR4 SDRAM memory modules |
2.54 mm | PCI, PCIe expansion cards |
3.96 mm | DIMM memory modules |
Gold Plating Thickness
The gold plating thickness should be selected based on the application requirements, such as the expected number of mating cycles and the operating environment. Thicker gold plating offers better wear resistance and durability but increases the overall cost of the PCB.
Gold Thickness | Mating Cycles | Application |
---|---|---|
2-5 µin | < 50 | Consumer electronics |
5-15 µin | 50-200 | Industrial, telecom |
15-30 µin | > 200 | High-reliability, military, aerospace |
Pad and Trace Geometry
The pad and trace geometry near the contact fingers should be optimized to minimize signal loss and ensure a robust connection. This includes:
- Properly sizing the pads to accommodate the contact finger dimensions and tolerances
- Maintaining appropriate trace widths and spacing to minimize crosstalk and impedance mismatch
- Using teardrop-shaped pads at the finger-trace junction to reduce stress concentrations and improve structural integrity
Mechanical Support
Gold finger PCBs should be designed with adequate mechanical support to prevent damage during handling and insertion/removal. This can be achieved by:
- Incorporating stiffeners or thicker substrates to reduce PCB Warpage and bending
- Using guide features, such as notches or chamfers, to ensure proper alignment during mating
- Providing strain relief for cables or wires connected to the PCB
Testing and Quality Control
To ensure the quality and reliability of gold finger PCBs, several testing and inspection methods are employed:
-
Visual Inspection: The PCBs are visually inspected for any defects, such as scratches, dents, or discoloration on the gold fingers.
-
Dimensional Verification: The contact finger dimensions, pitch, and alignment are measured using optical or mechanical gauges to ensure conformance to the specified tolerances.
-
Plating Thickness Measurement: The gold plating thickness is measured using X-ray fluorescence (XRF) or cross-sectioning methods to verify compliance with the specified requirements.
-
Electrical Testing: The PCB is subjected to electrical tests, such as continuity, insulation resistance, and high-potential (hipot) testing, to ensure proper connectivity and isolation between the contact fingers and other circuits.
-
Functional Testing: The gold finger PCB is tested in its intended application or a simulated environment to verify its functionality and performance under various operating conditions.
By implementing strict quality control measures, manufacturers can ensure that gold finger PCBs meet the required specifications and perform reliably in their intended applications.
Frequently Asked Questions (FAQ)
-
Q: What is the difference between gold fingers and edge connectors?
A: Gold fingers refer to the gold-plated contact pads on the edge of a PCB, while edge connectors refer to the socket or slot that the gold fingers plug into. The terms are often used interchangeably because they work together to form a connection between two PCBs. -
Q: Can gold finger PCBs be repaired if the gold plating is damaged?
A: In most cases, damaged gold plating cannot be easily repaired. The gold plating is typically thin and selectively applied to the contact fingers, making it difficult to repair without affecting the surrounding areas. If the damage is extensive, the PCB may need to be replaced. -
Q: Are gold finger PCBs more expensive than regular PCBs?
A: Yes, gold finger PCBs are generally more expensive than regular PCBs due to the additional processing steps required, such as nickel and gold plating. The cost also depends on the gold plating thickness and the number of fingers on the PCB. -
Q: Can gold finger PCBs be used for high-frequency applications?
A: Yes, gold finger PCBs can be used for high-frequency applications, such as PCIe and DDR memory interfaces. However, special attention must be paid to the design of the pads, traces, and ground planes to minimize signal integrity issues, such as reflections and crosstalk. -
Q: What are the environmental concerns associated with gold finger PCBs?
A: Gold plating processes can have environmental impacts due to the use of chemicals and the generation of waste. However, responsible manufacturers employ eco-friendly plating processes and proper waste management practices to minimize the environmental footprint. Additionally, gold finger PCBs can contribute to the longevity and reliability of electronic devices, reducing the need for frequent replacements and electronic waste.
Conclusion
Gold finger PCBs play a crucial role in providing reliable, durable, and easy-to-use connections between printed circuit boards. The gold-plated contact fingers offer excellent conductivity, wear resistance, and corrosion resistance, making them suitable for a wide range of applications, from consumer electronics to industrial and military systems.
By understanding the manufacturing process, design considerations, and testing requirements for gold finger PCBs, engineers and manufacturers can ensure that their products meet the highest standards of quality and performance. As technology continues to advance, the demand for robust and efficient connection solutions like gold finger PCBs will only grow, driving innovation and improvements in the electronics industry.
Leave a Reply