Introduction to Mouse Bites PCB Fabrication
Mouse bites, also known as break-away tabs or snap-off rails, is a PCB fabrication technique used to panelize individual printed circuit boards into larger panels for more efficient manufacturing. This method involves creating perforated lines between each individual PCB on the panel, allowing them to be easily separated after assembly.
The mouse bites technique offers several advantages in PCB production:
- Increased efficiency by assembling multiple PCBs simultaneously
- Reduced manufacturing costs compared to assembling individual boards
- Easier handling of smaller PCBs during the assembly process
- Simplified depaneling process after assembly
In this comprehensive guide, we will explore the mouse bites PCB fabrication technique in detail, including its advantages, design considerations, manufacturing process, and best practices for successful implementation.
Advantages of Using Mouse Bites in PCB Fabrication
Efficient Manufacturing Process
One of the primary benefits of using mouse bites in PCB fabrication is the increased efficiency in the manufacturing process. By panelizing individual PCBs into larger panels, manufacturers can assemble multiple boards simultaneously, reducing the time and effort required compared to assembling each board separately.
This efficiency is particularly valuable for high-volume production runs, where the time saved can translate into significant cost reductions and faster turnaround times.
Cost Reduction
The mouse bites technique can also lead to cost savings in PCB manufacturing. By assembling multiple boards on a single panel, manufacturers can optimize material usage, reducing waste and lowering the overall cost per board.
Additionally, the increased efficiency in the assembly process results in lower labor costs, as fewer manual operations are required to produce the same number of PCBs.
Easier Handling of Small PCBs
Smaller PCBs can be challenging to handle during the assembly process, as they require precise placement and soldering of components. By panelizing small PCBs using mouse bites, manufacturers can create larger, more manageable panels that are easier to work with.
This not only simplifies the assembly process but also reduces the risk of errors and damage to the individual boards.
Simplified Depaneling Process
After the assembly of the panelized PCBs is complete, the individual boards need to be separated from the panel. The mouse bites technique simplifies this depaneling process by creating perforated lines between each PCB, allowing them to be easily snapped off the panel.
This method eliminates the need for specialized depaneling equipment and reduces the risk of damage to the individual boards during separation.
Design Considerations for Mouse Bites PCBs
Placement and Spacing of Mouse Bites
When designing a PCB panel with mouse bites, it is essential to consider the placement and spacing of the perforations. The mouse bites should be positioned to ensure a clean break when separating the individual boards while maintaining the structural integrity of the panel during the assembly process.
A general guideline is to place mouse bites at intervals of 1-2mm along the edges of each individual PCB, with a minimum of three mouse bites per side. The spacing between each mouse bite should be consistent to ensure even stress distribution during depaneling.
Material Selection
The choice of PCB material is crucial when using the mouse bites technique. The material should have the right balance of flexibility and brittleness to allow for clean breaks along the perforated lines without causing damage to the individual boards.
Common materials suitable for mouse bites PCBs include:
- FR-4: A widely used PCB material with good mechanical and electrical properties
- Polyimide: A flexible material that can withstand high temperatures and stresses
- Aluminum: Offers excellent thermal conductivity and mechanical stability
Panelization Layout
When designing the panelization layout for mouse bites PCBs, consider the following factors:
- Board orientation: Arrange the individual PCBs on the panel to maximize material usage and minimize waste.
- Tooling holes: Include tooling holes in the panel design to ensure proper alignment during the assembly process.
- Fiducial marks: Add fiducial marks to the panel to aid in the automated assembly of components.
- Depaneling rails: Incorporate depaneling rails along the edges of the panel to provide additional support during the assembly process and to facilitate the separation of individual boards.
Here’s an example of a panelization layout for mouse bites PCBs:
Panel Element | Description |
---|---|
Individual PCBs | Arranged in a grid pattern for optimal material usage |
Mouse Bites | Placed at consistent intervals along the edges of each PCB |
Tooling Holes | Located at the corners of the panel for alignment during assembly |
Fiducial Marks | Placed near each individual PCB for automated component placement |
Depaneling Rails | Added along the outer edges of the panel for support and easy separation |
Design Rule Checks (DRC)
Before finalizing the PCB panel design, it is essential to perform Design Rule Checks (DRC) to ensure that the layout complies with the manufacturing capabilities and guidelines. DRC helps identify potential issues such as:
- Insufficient spacing between mouse bites
- Inadequate clearance between PCBs and panel edges
- Violations of minimum hole sizes and trace widths
By addressing these issues early in the design phase, manufacturers can avoid costly delays and rework during production.
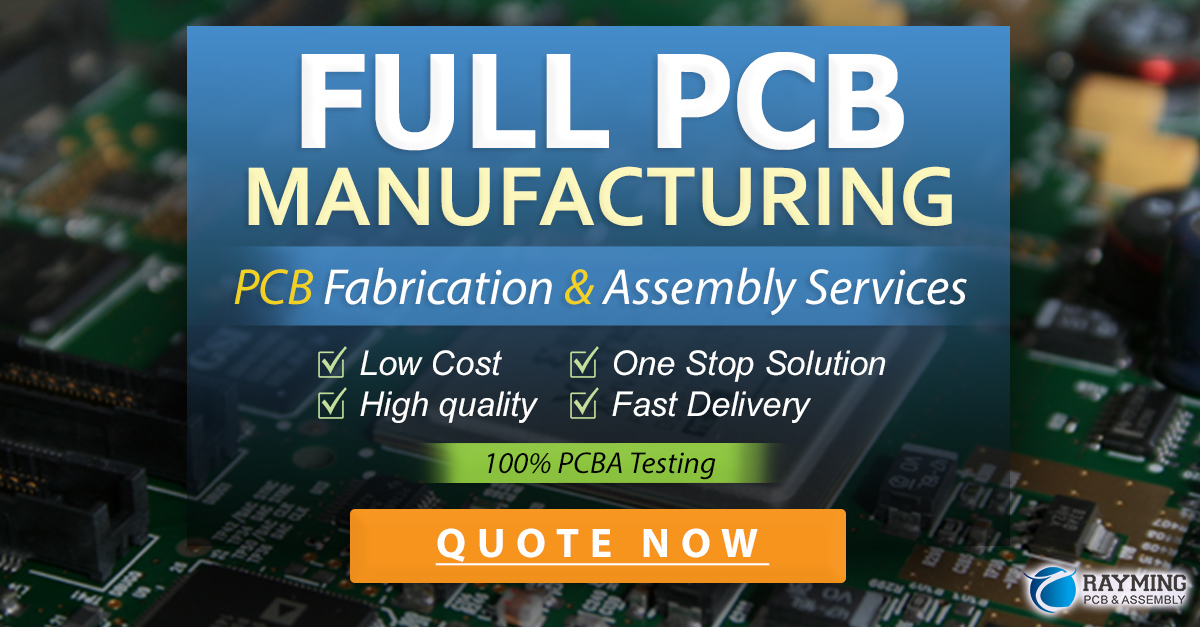
Manufacturing Process for Mouse Bites PCBs
PCB Fabrication
The manufacturing process for mouse bites PCBs begins with the fabrication of the PCB panel. This involves the following steps:
- Material selection and preparation
- Applying the copper layer and etching the circuit pattern
- Drilling holes for components and vias
- Applying solder mask and silkscreen layers
- Creating the mouse bites and depaneling rails
Component Assembly
Once the PCB panel is fabricated, the next step is to assemble the components onto each individual board. This process typically involves:
- Solder paste application using a stencil
- Automated pick-and-place of components
- Reflow soldering to permanently attach the components
- Inspection and testing of the assembled boards
Depaneling
After the assembly process is complete, the individual PCBs are separated from the panel using the mouse bites. This is typically done by manually breaking the boards along the perforated lines, although some manufacturers may use specialized depaneling equipment for more precise and controlled separation.
It is important to handle the panels carefully during depaneling to avoid damaging the individual PCBs or components.
Quality Control and Testing
The final step in the manufacturing process is quality control and testing. This involves:
- Visual inspection of the separated PCBs for any signs of damage or defects
- Electrical testing to ensure proper functionality and performance
- Packaging and labeling of the finished products
By implementing strict quality control measures, manufacturers can ensure that the mouse bites PCBs meet the required specifications and standards.
Best Practices for Successful Mouse Bites PCB Implementation
Collaborate with Experienced PCB Manufacturers
To ensure the successful implementation of mouse bites PCBs, it is essential to partner with experienced PCB manufacturers who have a proven track record in this fabrication technique. Look for manufacturers who:
- Have expertise in designing and fabricating mouse bites PCBs
- Offer guidance and support throughout the design and manufacturing process
- Use high-quality materials and advanced manufacturing equipment
- Provide comprehensive quality control and testing services
Optimize Design for Manufacturing
When designing mouse bites PCBs, it is crucial to optimize the layout for manufacturing. This involves:
- Following the manufacturer’s design guidelines and specifications
- Ensuring adequate spacing and clearance between PCBs and panel elements
- Minimizing the number of unique PCB designs on a single panel
- Incorporating design features that facilitate easy depaneling and handling
By optimizing the design for manufacturing, you can reduce the risk of production issues and improve the overall efficiency of the fabrication process.
Consider Alternative Panelization Techniques
While mouse bites are a popular and effective panelization technique, they may not be suitable for all PCB designs or applications. In some cases, alternative methods such as v-scoring or tab routing may be more appropriate.
It is essential to evaluate the specific requirements of your PCB project and consult with your manufacturing partner to determine the best panelization approach.
Conduct Thorough Testing and Validation
Before mass production, it is crucial to conduct thorough testing and validation of the mouse bites PCB design. This may involve:
- Producing prototype panels to assess the manufacturability and depaneling process
- Conducting environmental and stress tests to evaluate the reliability of the PCBs
- Performing functional testing to ensure that the assembled boards meet the required specifications
By investing time and resources in testing and validation, you can identify and address any potential issues early in the development cycle, reducing the risk of costly delays or product failures.
Frequently Asked Questions (FAQ)
1. What is the minimum spacing required between mouse bites?
The minimum spacing between mouse bites depends on the specific PCB material and thickness. As a general guideline, a spacing of 1-2mm is recommended, but it is essential to consult with your PCB manufacturer for their specific requirements.
2. Can mouse bites be used for flexible PCBs?
Yes, mouse bites can be used for flexible PCBs, such as those made from polyimide material. However, the design and spacing of the mouse bites may need to be adjusted to account for the flexibility of the material and to ensure clean breaks during depaneling.
3. Are there any limitations to the size of PCBs that can be panelized using mouse bites?
The size of PCBs that can be panelized using mouse bites is primarily limited by the manufacturing capabilities of the PCB fabricator. Most manufacturers can accommodate panel sizes up to 18″ x 24″ (457mm x 610mm), but larger sizes may be possible depending on the specific equipment and processes used.
4. How does the choice of PCB material affect the mouse bites technique?
The choice of PCB material can significantly impact the success of the mouse bites technique. The material should have the right balance of flexibility and brittleness to allow for clean breaks along the perforated lines without causing damage to the individual boards. FR-4, polyimide, and aluminum are common materials suitable for mouse bites PCBs.
5. Can mouse bites be used for high-density PCB designs?
Yes, mouse bites can be used for high-density PCB designs, but careful consideration must be given to the placement and spacing of the perforations to ensure adequate clearance between components and the board edges. It is essential to work closely with your PCB manufacturer to optimize the design for manufacturability and reliability.
Conclusion
Mouse bites PCB fabrication is a powerful technique for optimizing the production of printed circuit boards. By panelizing individual PCBs with perforated break-away tabs, manufacturers can improve efficiency, reduce costs, and simplify the assembly and depaneling processes.
To successfully implement mouse bites PCBs, it is essential to consider key design factors such as material selection, panelization layout, and spacing of the perforations. Collaborating with experienced PCB manufacturers, optimizing designs for manufacturability, and conducting thorough testing and validation can help ensure the success of your mouse bites PCB projects.
As technology continues to advance and the demand for high-quality, cost-effective PCBs grows, the mouse bites technique will likely remain a valuable tool in the PCB fabrication industry. By understanding the principles and best practices outlined in this guide, you can unlock the benefits of mouse bites PCBs and take your PCB designs to the next level.
Leave a Reply