Introduction to PCB Shields
PCB shields, also known as electromagnetic interference (EMI) shields or radio frequency (RF) shields, are essential components in electronic devices that protect sensitive circuits from unwanted electromagnetic interference. These shields are designed to enclose and protect specific areas of a printed circuit board (PCB), preventing external EMI from affecting the shielded components and minimizing the EMI emitted by the device itself.
In today’s increasingly connected world, where electronic devices are ubiquitous, PCB shields play a critical role in ensuring the proper functioning and reliability of these devices. From smartphones and laptops to medical equipment and automotive electronics, PCB shields are found in a wide range of applications.
Why Are PCB Shields Important?
PCB shields serve several crucial purposes in electronic devices:
-
EMI Protection: The primary function of PCB shields is to protect sensitive electronic components from electromagnetic interference. EMI can come from various sources, such as nearby electronic devices, power lines, or even the components within the same device. By enclosing susceptible components within a conductive shield, PCB shields effectively block external EMI, preventing it from interfering with the shielded components’ operation.
-
Emission Reduction: PCB shields also help reduce the electromagnetic emissions generated by the electronic components within the device. Many electronic devices must comply with strict EMI regulations set by government agencies, such as the Federal Communications Commission (FCC) in the United States or the European Conformity (CE) marking in the European Union. By containing EMI emissions, PCB shields help devices meet these regulatory requirements.
-
Signal Integrity: In high-speed electronic circuits, signal integrity is of utmost importance. PCB shields can help maintain signal integrity by preventing crosstalk between adjacent components or traces. By isolating sensitive components within a shielded enclosure, PCB shields minimize the interference between signals, ensuring clean and reliable signal transmission.
-
Heat Dissipation: In some cases, PCB shields can also serve as heat sinks, helping to dissipate heat generated by the electronic components. By providing a thermal path for heat to escape, PCB shields can contribute to the overall thermal management of the device, preventing overheating and extending the lifespan of the components.
Types of PCB Shields
PCB shields come in various types, each with its own characteristics and applications. The most common types of PCB shields include:
-
One-Piece Shields: One-piece shields, also known as single-piece shields, are the simplest type of PCB shields. They consist of a single piece of conductive material, typically metal, that is formed into a box-like shape to cover the desired area of the PCB. One-piece shields are cost-effective and easy to install, making them a popular choice for many applications.
-
Two-Piece Shields: Two-piece shields consist of a frame and a removable cover. The frame is soldered onto the PCB, surrounding the area to be shielded, while the cover snaps onto the frame, completing the shielding enclosure. Two-piece shields offer the advantage of easy access to the shielded components for testing, debugging, or repairs.
-
Custom Shields: In some cases, standard one-piece or two-piece shields may not provide the desired level of shielding or fit the specific shape of the PCB. In such situations, custom shields can be designed and manufactured to meet the unique requirements of the application. Custom shields can be made from various materials and can incorporate features such as ventilation holes, mounting points, or even integrated heatsinks.
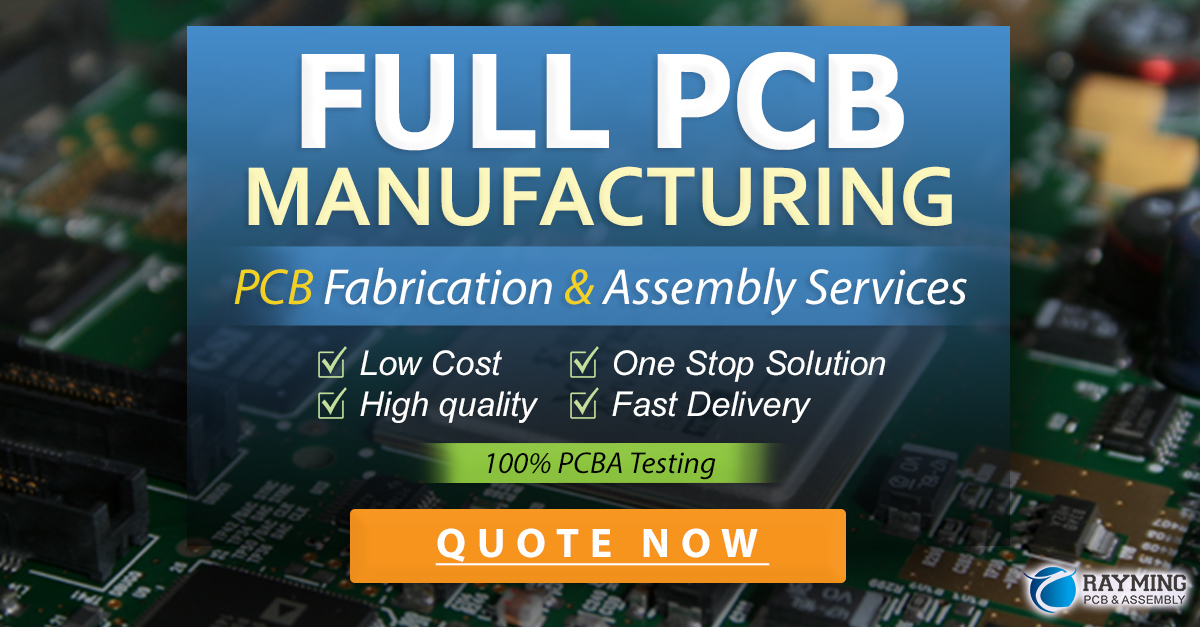
Materials Used for PCB Shields
PCB shields can be made from a variety of conductive materials, each with its own advantages and disadvantages. The most common materials used for PCB shields include:
-
Aluminum: Aluminum is a popular choice for PCB shields due to its lightweight, good conductivity, and low cost. It is easily formed into various shapes and provides effective shielding against EMI. However, aluminum shields may not be suitable for applications that require high levels of shielding effectiveness or in environments with extreme temperatures.
-
Steel: Steel PCB shields offer excellent mechanical strength and durability. They are often used in applications that require robust shielding, such as in industrial or automotive environments. Steel shields can be plated with other metals, such as nickel or tin, to improve their corrosion resistance and conductivity.
-
Copper: Copper shields provide the highest level of shielding effectiveness among the common materials used for PCB shields. Copper has excellent electrical conductivity and can effectively block even high-frequency EMI. However, copper shields are more expensive than aluminum or steel shields and may be more challenging to form into complex shapes.
-
Conductive Plastics: In some applications, conductive plastics can be used as an alternative to metal shields. These plastics are typically filled with conductive particles, such as carbon or metal fibers, to provide EMI shielding. Conductive plastic shields are lightweight, cost-effective, and offer good shielding performance, although not as high as metal shields.
Design Considerations for PCB Shields
When designing PCB shields, several key factors must be considered to ensure optimal shielding performance and compatibility with the overall device design. These factors include:
-
Shielding Effectiveness: The primary goal of PCB shields is to provide effective EMI shielding. The shielding effectiveness depends on various factors, such as the material used, the thickness of the shield, the size and shape of any openings or seams, and the frequency range of the EMI. Designers must carefully select the appropriate material and design parameters to achieve the desired level of shielding effectiveness.
-
Grounding: Proper grounding is essential for PCB shields to function effectively. The shield must be electrically connected to the PCB’s ground plane to provide a low-impedance path for EMI currents to flow. Designers must ensure that the shield is securely attached to the PCB and that there is sufficient contact between the shield and the ground plane.
-
Thermal Management: PCB shields can impact the thermal performance of the device by trapping heat generated by the shielded components. Designers must consider the thermal requirements of the components and incorporate features such as ventilation holes or thermal interface materials to facilitate heat dissipation.
-
Mechanical Considerations: PCB shields must be designed to withstand the mechanical stresses encountered during assembly, handling, and operation of the device. Factors such as shield thickness, material properties, and mounting methods must be carefully considered to ensure the shield’s structural integrity and reliability.
-
Cost and Manufacturing: The cost and manufacturability of PCB shields are important considerations in the design process. Designers must balance the shielding requirements with the cost constraints and manufacturing capabilities. Factors such as material selection, shield complexity, and assembly processes can significantly impact the overall cost and feasibility of the shield design.
PCB Shield Installation and Assembly
The installation and assembly of PCB shields involve several key steps to ensure proper shielding performance and reliability. These steps include:
-
Surface Preparation: Before installing the shield, the PCB surface must be properly prepared. This typically involves cleaning the surface to remove any contaminants or debris that could interfere with the shield’s electrical contact or adhesion.
-
Shield Placement: The shield is then placed over the area of the PCB to be shielded. For one-piece shields, the shield is simply positioned over the components, while for two-piece shields, the frame is first soldered onto the PCB.
-
Soldering: In most cases, the shield is soldered onto the PCB to establish a secure electrical and mechanical connection. Soldering can be done using various methods, such as hand soldering, wave soldering, or reflow soldering, depending on the shield design and manufacturing process.
-
Inspection: After soldering, the shield installation must be inspected to ensure proper alignment, contact, and soldering quality. Any defects or issues must be addressed before proceeding with further assembly steps.
-
Cover Installation (for two-piece shields): For two-piece shields, the cover is snapped onto the frame after the PCB has been tested and debugged. The cover completes the shielding enclosure and provides additional mechanical protection for the shielded components.
Testing and Validation of PCB Shields
To ensure that PCB shields meet the desired shielding performance and regulatory requirements, thorough testing and validation must be conducted. Some common testing methods for PCB shields include:
-
EMI Testing: EMI testing involves measuring the electromagnetic emissions from the device to ensure compliance with relevant EMI standards and regulations. This can be done using specialized equipment such as EMI receivers, antennas, and shielded chambers.
-
Shielding Effectiveness Testing: Shielding effectiveness testing measures the ability of the shield to attenuate EMI. This can be done using various methods, such as the modified MIL-STD-285 method or the IEEE STD 299 method, which involve placing a transmitting antenna inside the shield and measuring the signal attenuation outside the shield.
-
Mechanical Testing: Mechanical testing is performed to evaluate the shield’s structural integrity and ability to withstand the expected mechanical stresses during assembly and operation. This can include tests such as vibration testing, shock testing, and pull testing to ensure that the shield remains securely attached to the PCB.
-
Environmental Testing: In some cases, PCB shields may need to be tested under various environmental conditions to ensure their performance and reliability. This can include tests such as temperature cycling, humidity testing, and salt spray testing, depending on the intended application and operating environment of the device.
Troubleshooting Common PCB Shield Issues
Despite careful design and assembly, PCB shields may sometimes encounter issues that can affect their shielding performance or overall device functionality. Some common issues and troubleshooting tips include:
-
Poor Shielding Effectiveness: If the shield is not providing the desired level of EMI attenuation, several factors could be responsible. These include insufficient shield coverage, improper grounding, gaps or seams in the shield, or inadequate material selection. To troubleshoot, designers should review the shield design, ensure proper grounding, and check for any physical damage or defects in the shield.
-
Overheating: If the shielded components are overheating, it could indicate insufficient heat dissipation through the shield. This can be addressed by incorporating ventilation holes, using thermal interface materials, or redesigning the shield to improve airflow and heat transfer.
-
Mechanical Damage: PCB shields can be subjected to mechanical stresses during assembly, handling, or operation, which can cause damage such as dents, cracks, or deformation. If mechanical damage is observed, the shield may need to be replaced, or the assembly process may need to be reviewed to identify and address the root cause of the damage.
-
Corrosion: In some environments, PCB shields can be susceptible to corrosion, which can degrade their shielding performance and overall reliability. Corrosion can be addressed by selecting appropriate materials, such as corrosion-resistant plating or coatings, and ensuring proper storage and handling of the shields.
Frequently Asked Questions (FAQ)
-
Q: What is the difference between one-piece and two-piece PCB shields?
A: One-piece shields are a single piece of conductive material formed into a box-like shape to cover the desired area of the PCB. Two-piece shields consist of a frame soldered onto the PCB and a removable cover that snaps onto the frame. Two-piece shields offer easier access to the shielded components for testing and debugging. -
Q: Can PCB shields be custom-designed for specific applications?
A: Yes, custom PCB shields can be designed and manufactured to meet the unique requirements of specific applications. Custom shields can be made from various materials and can incorporate features such as ventilation holes, mounting points, or integrated heatsinks. -
Q: How do PCB shields help with EMI compliance?
A: PCB shields help electronic devices comply with EMI regulations by reducing the electromagnetic emissions generated by the shielded components. By containing EMI emissions, PCB shields help devices meet the strict requirements set by regulatory agencies such as the FCC or CE. -
Q: What are the most common materials used for PCB shields?
A: The most common materials used for PCB shields are aluminum, steel, copper, and conductive plastics. Aluminum is lightweight and cost-effective, steel offers excellent mechanical strength, copper provides the highest shielding effectiveness, and conductive plastics are lightweight and offer good shielding performance. -
Q: How can I ensure proper grounding of PCB shields?
A: To ensure proper grounding, the PCB shield must be electrically connected to the PCB’s ground plane. This can be achieved by soldering the shield to the PCB, ensuring sufficient contact between the shield and the ground plane. Designers must also consider the shield’s mounting method and any potential gaps or seams that could affect grounding.
Conclusion
PCB shields play a critical role in protecting sensitive electronic components from electromagnetic interference and ensuring the proper functioning and reliability of electronic devices. By understanding the types of shields, materials, design considerations, installation processes, and testing methods, engineers and designers can effectively incorporate PCB shields into their designs to meet EMI shielding requirements and regulatory standards.
As electronic devices continue to evolve and become more complex, the importance of PCB shields will only continue to grow. By staying up-to-date with the latest advancements in shielding technologies and best practices, designers can create robust and reliable electronic devices that are well-protected against the ever-present challenges of electromagnetic interference.
Leave a Reply