Introduction to Pulse-Width Modulation (PWM)
Pulse-Width Modulation (PWM) is a powerful technique used in various applications, from motor control to digital communications. It allows for efficient control of power delivery, signal encoding, and even creating analog-like behavior using digital means. In this comprehensive guide, we’ll dive deep into the fundamentals of PWM, exploring its principles, applications, and implementation.
What is Pulse-Width Modulation?
Pulse-Width Modulation is a method of encoding a message or controlling power delivery by varying the width of pulses in a pulse train. In PWM, the pulse width (also known as the duty cycle) is modulated, while the frequency remains constant. By adjusting the duty cycle, we can control the average power delivered to a load or convey information.
Key Components of PWM
To understand PWM, it’s essential to familiarize yourself with its key components:
- Pulse Train: A series of pulses that alternate between high and low states.
- Pulse Width: The duration of the “on” state within a single pulse cycle.
- Period: The time it takes to complete one full cycle of the pulse train.
- Duty Cycle: The percentage of time the signal is in the high state within one period.
- Frequency: The number of pulse cycles per second, measured in Hertz (Hz).
By manipulating these components, PWM allows for precise control and communication in various systems.
How Does PWM Work?
Now that we’ve covered the basics, let’s explore how PWM actually works.
Generating PWM Signals
PWM signals are typically generated using a microcontroller or a dedicated PWM controller. These devices have built-in timers and comparators that enable the creation of precise PWM waveforms. The microcontroller sets the desired frequency and duty cycle, and the PWM controller generates the corresponding pulse train.
Adjusting the Duty Cycle
The duty cycle is a crucial parameter in PWM. It represents the proportion of time the signal is in the high state within one period. By adjusting the duty cycle, we can control the average power delivered to a load or convey information.
For example, consider a PWM signal with a 50% duty cycle. This means that the signal is high for half of the period and low for the other half. If we increase the duty cycle to 75%, the signal will be high for three-quarters of the period, resulting in a higher average power delivery.
Filtering PWM Signals
PWM signals are essentially digital waveforms with abrupt transitions between high and low states. However, in many applications, such as motor control or audio amplification, a smooth analog signal is desired. To achieve this, PWM signals are often filtered using low-pass filters.
A low-pass filter attenuates high-frequency components while allowing low-frequency components to pass through. When applied to a PWM signal, the filter smooths out the sharp edges, resulting in an analog-like waveform. The cutoff frequency of the filter should be carefully chosen based on the PWM frequency and the desired smoothness of the output signal.
Applications of PWM
PWM finds applications in a wide range of fields. Let’s explore some of the most common uses of PWM.
Motor Control
PWM is extensively used in motor control applications. By adjusting the duty cycle of the PWM signal, we can control the speed and torque of DC motors. This technique is commonly employed in robotics, automotive systems, and industrial automation.
In motor control, the PWM signal is used to drive power electronic devices, such as MOSFETs or IGBTs, which regulate the power delivered to the motor windings. By varying the duty cycle, we can control the average voltage applied to the motor, thus adjusting its speed and torque.
LED Dimming
PWM is also widely used for LED dimming. Unlike traditional incandescent bulbs, LEDs have a non-linear relationship between voltage and brightness. PWM offers a simple and efficient solution for controlling LED brightness.
By applying a PWM signal to an LED, we can control its perceived brightness. The human eye perceives the average light intensity, so by rapidly switching the LED on and off with different duty cycles, we can create the illusion of different brightness levels. This technique is commonly used in LED lighting systems, displays, and backlighting applications.
Audio Amplification
PWM is employed in Class D audio amplifiers, which offer high efficiency and compact size compared to traditional analog amplifiers. In Class D amplification, the audio signal is converted into a PWM signal, which is then used to drive the output stage.
The PWM signal switches the output transistors on and off rapidly, creating a high-frequency square wave. This square wave is then filtered using a low-pass filter to reconstruct the original audio signal. Class D amplifiers are commonly found in portable audio devices, home theater systems, and automotive audio applications.
Digital Communications
PWM is used in various digital communication protocols, such as infrared (IR) remote control and power line communication (PLC). In these applications, PWM is employed to encode digital data onto a carrier signal.
For example, in IR remote control, the PWM signal represents the binary data to be transmitted. The pulse width determines the logic level (0 or 1) of each bit. The receiver decodes the PWM signal by measuring the pulse widths and reconstructing the original digital data.
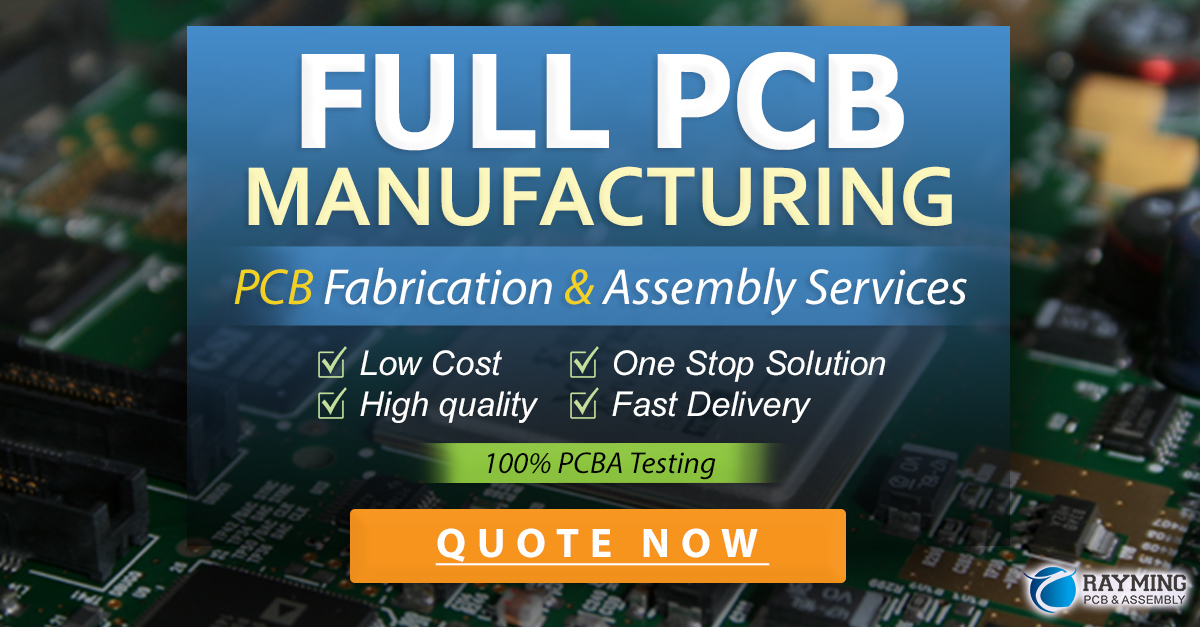
Implementing PWM
Now that we’ve explored the applications of PWM, let’s delve into the practical aspects of implementing PWM in your projects.
Microcontroller-based PWM
Microcontrollers, such as Arduino or STM32, often have built-in PWM capabilities. These microcontrollers provide dedicated PWM pins and timers that simplify the generation of PWM signals.
To generate PWM using a microcontroller, you typically need to follow these steps:
- Configure the PWM timer: Set the desired frequency and resolution of the PWM signal.
- Set the duty cycle: Specify the desired duty cycle for each PWM channel.
- Enable the PWM output: Activate the PWM signal on the corresponding pins.
Most microcontroller development environments, such as Arduino IDE or STM32CubeIDE, provide libraries and functions that abstract the low-level details of PWM configuration, making it easier to implement PWM in your projects.
Dedicated PWM Controllers
For more advanced applications or when using microcontrollers without built-in PWM capabilities, dedicated PWM controller chips can be employed. These chips, such as the TLC5940 or PCA9685, offer multiple PWM channels and programmable features.
Dedicated PWM controllers communicate with the microcontroller using serial interfaces like SPI or I2C. The microcontroller sends commands to the PWM controller to set the desired frequency, duty cycle, and other parameters. The PWM controller then generates the corresponding PWM signals on its output pins.
Using dedicated PWM controllers can offload the PWM generation task from the microcontroller, freeing up its resources for other tasks. They also provide additional features like output cascading, programmable current control, and built-in error protection.
Software-based PWM
In some cases, PWM can be implemented purely in software without relying on hardware timers. Software-based PWM involves toggling the output pins of the microcontroller at precise intervals to generate the desired PWM waveform.
Software-based PWM is typically achieved using timer interrupts or busy-wait loops. The microcontroller’s firmware is responsible for managing the timing and toggling the output pins accordingly. While software-based PWM offers flexibility, it may have limitations in terms of frequency range and resolution compared to hardware-based solutions.
Best Practices and Considerations
When working with PWM, there are several best practices and considerations to keep in mind:
-
Frequency Selection: Choose an appropriate PWM frequency based on your application requirements. Higher frequencies are suitable for smooth analog-like behavior, while lower frequencies may be sufficient for simple on/off control.
-
Resolution: Consider the resolution of your PWM signal, which determines the granularity of the duty cycle adjustments. Higher resolution allows for finer control but may require more hardware resources.
-
Filtering: If a smooth analog output is desired, use appropriate low-pass filters to remove the high-frequency components of the PWM signal. The filter design should take into account the PWM frequency and the desired cutoff frequency.
-
Load Considerations: Ensure that the PWM controller or microcontroller can handle the current requirements of the load. Consider using external drivers or power stages for high-current applications.
-
Electromagnetic Interference (EMI): PWM signals can generate EMI due to their sharp transitions. Take necessary precautions, such as proper grounding, shielding, and filtering, to minimize EMI and ensure compliance with regulatory standards.
-
Timing Accuracy: Pay attention to the timing accuracy of your PWM implementation, especially when precise control is required. Use hardware timers or dedicated PWM controllers for better timing accuracy compared to software-based solutions.
Frequently Asked Questions (FAQ)
-
What is the difference between PWM and analog signals?
PWM is a digital technique that generates a pulse train with varying pulse widths, while analog signals have continuous values. PWM can be used to approximate analog behavior by controlling the average power or intensity. -
Can PWM be used for analog-to-digital conversion?
Yes, PWM can be used as a simple form of analog-to-digital conversion. By measuring the pulse width of a PWM signal, we can determine the corresponding analog value. However, dedicated analog-to-digital converters (ADCs) offer higher resolution and accuracy. -
How do I choose the right PWM frequency for my application?
The choice of PWM frequency depends on the specific requirements of your application. Higher frequencies are suitable for smooth analog-like behavior and reducing audible noise in motor control. Lower frequencies may be sufficient for simple on/off control or when using filters with lower cutoff frequencies. -
Can I generate multiple PWM signals with different frequencies using a single microcontroller?
Yes, most microcontrollers have multiple PWM channels that can be configured independently. Each channel can generate PWM signals with different frequencies and duty cycles. However, the number of available PWM channels and the range of frequencies may vary depending on the specific microcontroller. -
How do I interface a PWM controller with a microcontroller?
PWM controllers typically communicate with microcontrollers using serial interfaces like SPI or I2C. The microcontroller sends commands to the PWM controller to set the desired frequency, duty cycle, and other parameters. Refer to the datasheet of the specific PWM controller for detailed interfacing instructions.
Conclusion
Pulse-Width Modulation (PWM) is a versatile technique with a wide range of applications, from motor control and LED dimming to audio amplification and digital communications. By understanding the principles and implementation of PWM, you can harness its power to control and communicate effectively in your projects.
Remember to consider factors such as frequency selection, resolution, filtering, load requirements, and timing accuracy when working with PWM. By following best practices and leveraging the capabilities of microcontrollers and dedicated PWM controllers, you can successfully integrate PWM into your designs.
PWM offers a powerful tool for bridging the gap between the digital and analog domains, enabling efficient control and communication in various systems. With its flexibility and simplicity, PWM continues to be a fundamental technique in the world of electronics and embedded systems.
Leave a Reply