Introduction to PCBA Equipment
PCBA (Printed Circuit Board Assembly) equipment refers to the various machines and tools used in the process of assembling electronic components onto a printed circuit board (PCB) to create a functional electronic device. PCBA is a complex process that involves several stages, each requiring specific equipment to ensure the accuracy, reliability, and efficiency of the assembly process.
In this comprehensive guide, we will explore the essential PCBA equipment, their functions, and their roles in the PCBA process. Whether you are a seasoned professional or new to the world of electronics manufacturing, understanding PCBA equipment is crucial for ensuring the success of your projects.
The PCBA Process Overview
Before diving into the specific equipment used in PCBA, let’s briefly overview the PCBA process to understand the context in which these machines operate.
-
PCB Design and Fabrication: The PCBA process begins with designing the PCB using specialized software and then fabricating the bare board according to the design specifications.
-
Solder Paste Application: Solder paste, a mixture of tiny solder particles and flux, is applied to the PCB’s surface where components will be placed.
-
Component Placement: Electronic components are precisely placed onto the solder paste-covered PCB pads using pick-and-place machines.
-
Reflow Soldering: The PCB with placed components undergoes reflow soldering, where the board is heated to melt the solder paste and create permanent electrical connections between the components and the PCB.
-
Inspection and Testing: The assembled PCBA undergoes various inspection and testing procedures to ensure proper functionality and quality.
Now that we have a basic understanding of the PCBA process let’s explore the key equipment used in each stage.
PCB Design and Fabrication Equipment
PCB Design Software
PCB design software is used to create the electronic schematic and layout of the PCB. Some popular PCB design software include:
- Altium Designer
- KiCad
- Eagle
- OrCAD
These software tools allow designers to create complex PCB designs, simulate circuit behavior, and generate manufacturing files for PCB fabrication.
PCB Fabrication Equipment
PCB fabrication involves several processes, each requiring specialized equipment. Some key PCB fabrication equipment include:
-
Exposure Machine: Used to transfer the PCB layout pattern onto the photoresist-coated copper clad laminate.
-
Etching Machine: Removes unwanted copper from the laminate, leaving behind the desired circuit pattern.
-
Drilling Machine: Creates holes in the PCB for through-hole components and vias.
-
Plating Equipment: Applies additional copper plating to the PCB holes and surface to improve conductivity and protect the copper from oxidation.
PCB Fabrication Process | Equipment Used |
---|---|
Exposure | Exposure Machine |
Etching | Etching Machine |
Drilling | Drilling Machine |
Plating | Plating Equipment |
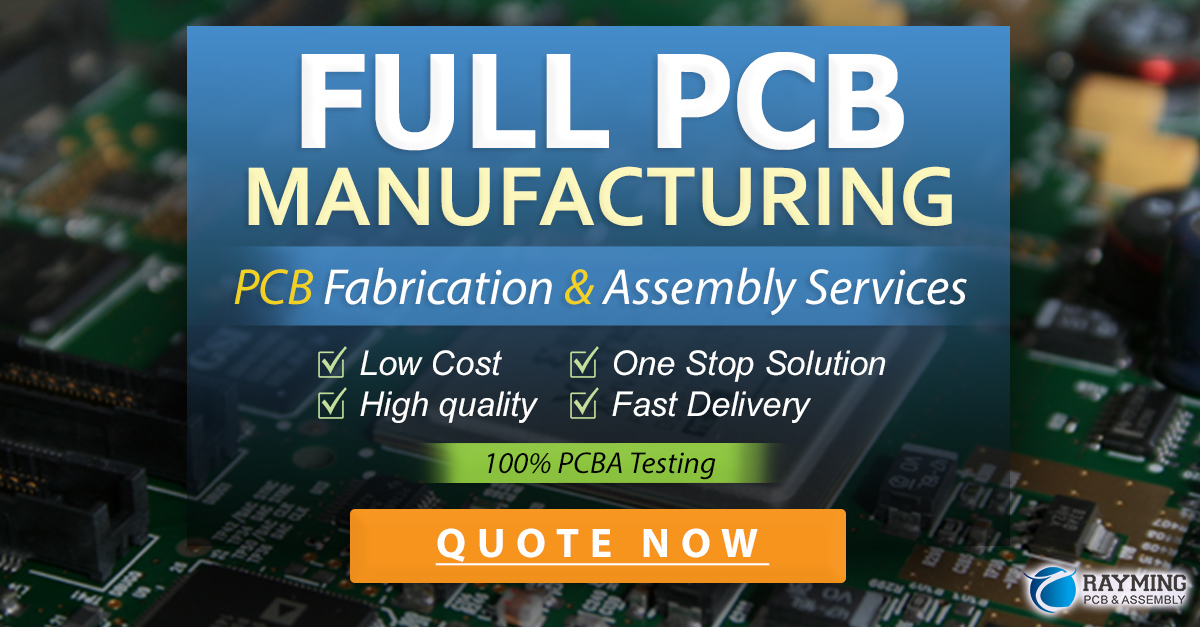
Solder Paste Application Equipment
Solder Paste Printer
A solder paste printer is used to apply solder paste onto the PCB pads accurately. There are two main types of solder paste printers:
-
Stencil Printer: Uses a stencil with openings that match the PCB pad layout. Solder paste is squeegeed across the stencil, depositing the paste onto the pads.
-
Jet Printer: Uses a print head to dispense solder paste directly onto the PCB pads, offering more flexibility and control over the paste application.
Solder Paste Inspection (SPI) Equipment
After solder paste application, SPI equipment is used to inspect the quality and accuracy of the deposited solder paste. SPI machines use 2D or 3D imaging to assess the paste volume, height, and alignment, ensuring that the paste application meets the required specifications.
Component Placement Equipment
Pick-and-Place Machine
A pick-and-place (PnP) machine is the heart of the component placement process. PnP machines use computer-controlled nozzles to pick up components from feeders and place them accurately onto the solder paste-covered PCB pads. PnP machines come in various types and sizes, depending on the production volume, component types, and placement accuracy requirements.
PnP Machine Type | Characteristics |
---|---|
High-Speed | – Fastest placement rates (50,000+ CPH) – Suitable for high-volume production – Handles a wide range of component sizes |
Mid-Range | – Moderate placement rates (10,000-50,000 CPH) – Suitable for medium-volume production – Offers a balance between speed and flexibility |
Desktop | – Lowest placement rates (1,000-10,000 CPH) – Suitable for low-volume or prototype production – Most affordable and compact option |
*CPH: Components Per Hour
Component Feeders
Component feeders are used to store and supply components to the pick-and-place machine. The most common types of feeders include:
-
Tape and Reel Feeders: Components are packaged in a carrier tape wound onto a reel. The tape is fed into the pick-and-place machine, which picks the components from the pockets in the tape.
-
Tray Feeders: Components are stored in trays with pockets that match the component size and shape. The pick-and-place machine picks the components directly from the tray pockets.
-
Tube Feeders: Components are stored in tubes, and the pick-and-place machine picks them from the tube end.
Reflow Soldering Equipment
Reflow Oven
A reflow oven is used to melt the solder paste and create permanent electrical connections between the components and the PCB. Reflow ovens use a controlled heating process that follows a specific temperature profile to ensure proper solder joint formation. The two main types of reflow ovens are:
-
Convection Reflow Oven: Uses forced hot air circulation to heat the PCB and melt the solder paste evenly.
-
Infrared (IR) Reflow Oven: Uses infrared heating elements to heat the PCB and melt the solder paste. IR ovens can be further classified into short wave, medium wave, and long wave ovens based on the wavelength of the IR radiation used.
Nitrogen Reflow System
A nitrogen reflow system is an optional addition to a reflow oven that introduces nitrogen gas into the oven during the soldering process. The nitrogen atmosphere helps to reduce oxidation and improve solder joint quality, especially for lead-free solder alloys that are more susceptible to oxidation.
Inspection and Testing Equipment
Automated Optical Inspection (AOI)
AOI machines use high-resolution cameras and advanced image processing algorithms to inspect the assembled PCB for defects such as missing components, misaligned components, solder bridges, and insufficient solder. AOI inspection can be performed at various stages of the PCBA process, including post-solder paste application, post-component placement, and post-reflow soldering.
X-Ray Inspection
X-ray inspection machines use X-rays to inspect solder joints and other hidden features that are not visible to the naked eye or AOI machines. X-ray inspection is particularly useful for examining solder joints under Ball Grid Array (BGA) and Quad Flat No-lead (QFN) packages.
In-Circuit Testing (ICT)
ICT is a type of electrical testing that verifies the proper assembly and functionality of the PCBA. ICT machines use a bed-of-nails fixture that makes contact with specific test points on the PCB to test for short circuits, open circuits, resistance, capacitance, and other electrical characteristics.
Functional Testing
Functional testing involves powering up the assembled PCBA and testing its performance under real-world operating conditions. Functional testing equipment varies depending on the specific requirements of the electronic device being tested but may include power supplies, signal generators, oscilloscopes, and custom test fixtures.
FAQ
- Q: What is the difference between a stencil printer and a jet printer for solder paste application?
A: A stencil printer uses a stencil with openings that match the PCB pad layout to apply solder paste, while a jet printer uses a print head to dispense solder paste directly onto the pads. Jet printers offer more flexibility and control over paste application but are generally slower than stencil printers.
- Q: What factors should I consider when choosing a pick-and-place machine?
A: When choosing a pick-and-place machine, consider factors such as production volume, component types and sizes, placement accuracy requirements, and budget. High-speed machines are suitable for high-volume production, while desktop machines are more affordable and suitable for low-volume or prototype production.
- Q: What are the advantages of using a nitrogen reflow system?
A: A nitrogen reflow system introduces nitrogen gas into the reflow oven during the soldering process, which helps to reduce oxidation and improve solder joint quality. This is particularly beneficial when using lead-free solder alloys that are more susceptible to oxidation.
- Q: Why is X-ray inspection important in PCBA?
A: X-ray inspection is important for examining solder joints and other hidden features that are not visible to the naked eye or AOI machines. It is particularly useful for inspecting solder joints under Ball Grid Array (BGA) and Quad Flat No-lead (QFN) packages, which are difficult to inspect using other methods.
- Q: What is the purpose of functional testing in PCBA?
A: Functional testing involves powering up the assembled PCBA and testing its performance under real-world operating conditions. The purpose of functional testing is to ensure that the assembled PCB functions as intended and meets the specified performance requirements of the electronic device.
Conclusion
PCBA equipment plays a critical role in the successful assembly of electronic devices. From PCB design and fabrication to solder paste application, component placement, reflow soldering, and inspection and testing, each stage of the PCBA process relies on specialized equipment to ensure accuracy, reliability, and efficiency.
Understanding the various types of PCBA equipment and their functions is essential for anyone involved in electronics manufacturing. By carefully selecting and utilizing the appropriate equipment for each stage of the PCBA process, manufacturers can optimize their production processes, improve product quality, and reduce costs.
As technology continues to advance, PCBA equipment will undoubtedly evolve to keep pace with the increasing complexity and miniaturization of electronic devices. Staying up-to-date with the latest developments in PCBA equipment and processes will be crucial for maintaining a competitive edge in the rapidly changing world of electronics manufacturing.
Leave a Reply