Introduction to PCB Surface Finishing
Printed Circuit Boards (PCBs) are essential components in modern electronics, providing a platform for electrical components to be mounted and interconnected. To ensure optimal performance and longevity, PCBs undergo a surface finishing process that protects the exposed copper traces from oxidation and enhances the solderability of the board. Two popular surface finishing methods are Hot Air Solder Leveling (HASL) and Electroless Nickel Immersion Gold (ENIG). In this article, we will explore the characteristics, advantages, and disadvantages of both HASL and ENIG, helping you choose the right surface treatment method for your PCB project.
What is HASL?
Overview of Hot Air Solder Leveling (HASL)
Hot Air Solder Leveling (HASL) is a widely used PCB surface finishing method that involves applying a layer of molten solder to the exposed copper traces and pads. The process is carried out by dipping the PCB into a bath of molten solder, which is typically a tin-lead alloy. After the PCB is removed from the solder bath, hot air is used to level the solder surface, ensuring a smooth and even finish.
The HASL Process
- PCB Cleaning: The PCB is thoroughly cleaned to remove any contaminants or oxidation from the copper surface.
- Flux Application: A thin layer of flux is applied to the PCB to promote solder adhesion and prevent oxidation during the process.
- Solder Dipping: The PCB is dipped into a bath of molten solder, typically at a temperature of 240-260°C, for a few seconds.
- Hot Air Leveling: After the PCB is removed from the solder bath, hot air is used to blow away excess solder and level the surface, creating a smooth finish.
- Cooling: The PCB is allowed to cool, and the solder solidifies, forming a protective layer over the copper traces and pads.
Advantages of HASL
- Cost-effective: HASL is one of the most economical PCB surface finishing methods, making it a popular choice for budget-conscious projects.
- Excellent solderability: The solder coating provided by HASL ensures excellent solderability, making it easier to attach components to the PCB during assembly.
- Good shelf life: HASL-finished PCBs have a relatively long shelf life, as the solder coating protects the copper from oxidation.
- Suitable for wave soldering: HASL is compatible with wave soldering, a common assembly method for through-hole components.
Disadvantages of HASL
- Uneven surface: Due to the nature of the hot air leveling process, HASL-finished PCBs may have an uneven surface, which can cause issues with fine-pitch components or high-density designs.
- Thermal shock: The high temperature of the molten solder bath can cause thermal shock to the PCB, potentially leading to warping or delamination.
- Environmental concerns: Traditional HASL processes use lead-based solder, which poses environmental and health risks. Lead-free alternatives are available but may have different performance characteristics.
- Incompatible with some components: HASL may not be suitable for certain surface-mount components, such as Ball Grid Arrays (BGAs) or fine-pitch devices, due to the uneven surface finish.
What is ENIG?
Overview of Electroless Nickel Immersion Gold (ENIG)
Electroless Nickel Immersion Gold (ENIG) is a high-performance PCB surface finishing method that involves depositing a layer of nickel followed by a thin layer of gold onto the exposed copper traces and pads. The nickel layer acts as a barrier, preventing copper migration and providing a smooth surface, while the gold layer ensures excellent solderability and protects the nickel from oxidation.
The ENIG Process
- PCB Cleaning: The PCB is thoroughly cleaned to remove any contaminants or oxidation from the copper surface.
- Microetching: The copper surface is microetched to improve adhesion of the subsequent layers.
- Electroless Nickel Plating: The PCB is immersed in an electroless nickel plating bath, where a thin layer of nickel (typically 3-6 μm) is deposited onto the copper surface through an autocatalytic chemical reaction.
- Immersion Gold Plating: After the nickel layer is deposited, the PCB is immersed in an immersion gold plating bath, where a thin layer of gold (typically 0.05-0.1 μm) is deposited onto the nickel surface through a displacement reaction.
- Rinsing and Drying: The PCB is rinsed with deionized water and dried, completing the ENIG process.
Advantages of ENIG
- Flat and uniform surface: ENIG provides a flat and uniform surface finish, making it suitable for fine-pitch components and high-density PCB designs.
- Excellent solderability: The gold layer in ENIG ensures excellent solderability, making it easy to attach components to the PCB during assembly.
- Long shelf life: ENIG-finished PCBs have a long shelf life, as the gold layer protects the nickel from oxidation, preserving solderability.
- Suitable for various assembly methods: ENIG is compatible with multiple assembly methods, including wave soldering, reflow soldering, and solder paste printing.
- RoHS compliant: ENIG is a lead-free and RoHS-compliant surface finishing method, making it an environmentally friendly choice.
Disadvantages of ENIG
- Higher cost: ENIG is more expensive than HASL due to the use of gold and the more complex processing steps involved.
- Black pad syndrome: In some cases, ENIG-finished PCBs may suffer from “black pad syndrome,” where the nickel layer becomes oxidized, leading to poor solderability and weak solder joints.
- Gold embrittlement: If the gold layer is too thick, it can cause embrittlement of the solder joint, leading to reliability issues.
- Potential for nickel corrosion: In harsh environments, the nickel layer in ENIG may be susceptible to corrosion, compromising the integrity of the surface finish.
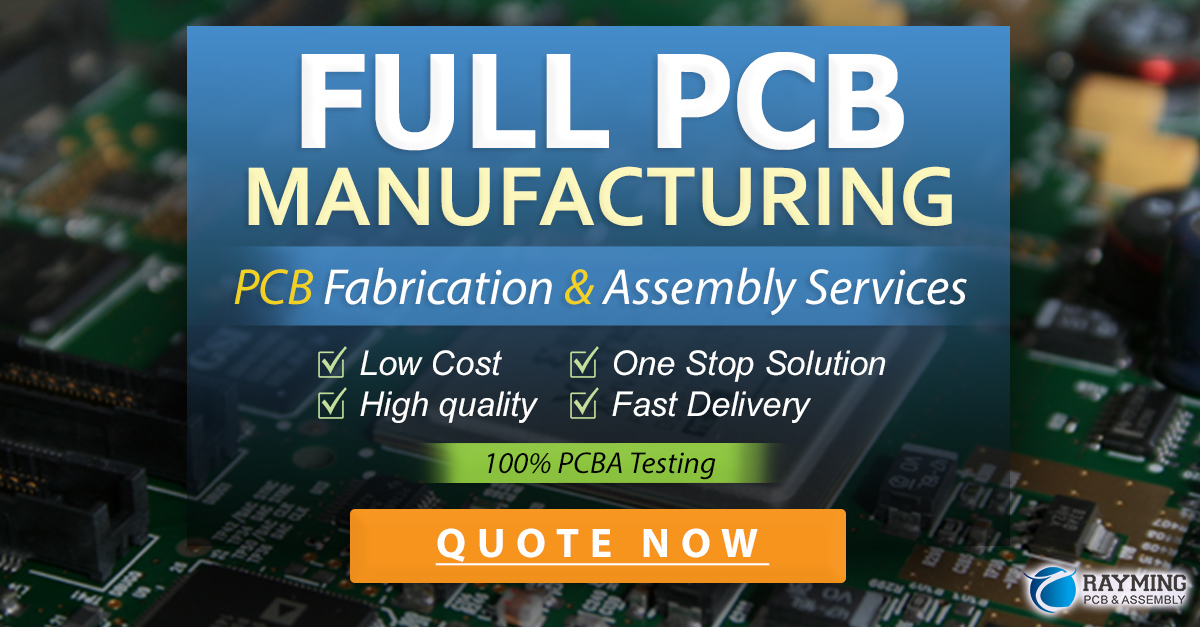
Comparing HASL and ENIG
Performance Comparison
Characteristic | HASL | ENIG |
---|---|---|
Surface Flatness | Uneven | Flat and uniform |
Solderability | Excellent | Excellent |
Shelf Life | Good | Excellent |
Fine-pitch Compatibility | Limited | Excellent |
High-density Compatibility | Limited | Excellent |
Assembly Methods | Wave soldering | Wave, reflow, and solder paste |
Environmental Impact | Lead-based (traditional) | RoHS compliant |
Cost Comparison
HASL is generally more cost-effective than ENIG, making it a popular choice for projects with tight budgets. The lower cost of HASL can be attributed to the simpler processing steps and the use of less expensive materials. On the other hand, ENIG involves the use of gold and more complex processing steps, resulting in a higher overall cost.
However, it is essential to consider the total cost of ownership when comparing HASL and ENIG. While HASL may have a lower upfront cost, the potential for rework and reliability issues due to the uneven surface finish may lead to increased costs in the long run. ENIG, despite its higher initial cost, offers a more consistent and reliable surface finish, which can reduce the need for rework and improve overall product quality.
Choosing Between HASL and ENIG
Factors to Consider
When deciding between HASL and ENIG for your PCB project, consider the following factors:
- Budget: If cost is a primary concern, HASL may be the more suitable choice. However, if performance and reliability are critical, the higher cost of ENIG may be justified.
- PCB Design: For high-density designs or those with fine-pitch components, ENIG is the better option due to its flat and uniform surface finish. HASL may be sufficient for simpler designs with larger components.
- Assembly Method: HASL is compatible with wave soldering, while ENIG is suitable for various assembly methods, including wave soldering, reflow soldering, and solder paste printing.
- Environmental Regulations: If your project must comply with RoHS or other environmental regulations, ENIG is the clear choice, as it is lead-free and compliant with these standards.
- Shelf Life: If your PCBs need to be stored for an extended period before assembly, ENIG offers a longer shelf life due to the gold layer’s protection against oxidation.
Decision Matrix
To help you make an informed decision, use the following decision matrix:
Factor | HASL | ENIG |
---|---|---|
Budget | ++ | + |
PCB Design | + | ++ |
Assembly Method | + | ++ |
Environmental Regulations | – | ++ |
Shelf Life | + | ++ |
++: Highly suitable
+: Suitable
-: Not suitable
Based on your project’s specific requirements, assign weights to each factor and evaluate the suitability of HASL and ENIG accordingly. This will help you determine the best surface finishing method for your PCB project.
FAQs
-
Q: Can HASL be used for lead-free soldering?
A: Yes, lead-free alternatives to traditional HASL are available, such as Substitute-Tin (SN) HASL and Nickel-Palladium-Gold (NiPdAu) HASL. However, these alternatives may have different performance characteristics compared to lead-based HASL. -
Q: How does the shelf life of HASL compare to that of ENIG?
A: ENIG-finished PCBs have a longer shelf life than HASL-finished PCBs. The gold layer in ENIG protects the nickel from oxidation, preserving solderability for an extended period. HASL-finished PCBs have a good shelf life, but the exposed solder surface may oxidize over time, reducing solderability. -
Q: Is ENIG suitable for high-temperature applications?
A: Yes, ENIG is suitable for high-temperature applications. The nickel layer in ENIG provides a robust barrier against copper migration, and the gold layer ensures excellent solderability even at elevated temperatures. -
Q: Can HASL be used for fine-pitch components?
A: While HASL can be used for fine-pitch components, it may not be the ideal choice. The uneven surface finish of HASL can cause issues with the placement and soldering of fine-pitch components. ENIG, with its flat and uniform surface finish, is better suited for fine-pitch applications. -
Q: Is it possible to combine HASL and ENIG on the same PCB?
A: Yes, it is possible to use a combination of HASL and ENIG on the same PCB, a process known as selective surface finishing. This allows you to take advantage of the benefits of both surface finishing methods in different areas of the PCB. However, selective surface finishing may increase the overall cost and complexity of the PCB manufacturing process.
Conclusion
Choosing the right surface treatment method for your PCB project is crucial for ensuring optimal performance, reliability, and cost-effectiveness. HASL and ENIG are two popular surface finishing methods, each with its own advantages and disadvantages. HASL offers a cost-effective solution with excellent solderability, while ENIG provides a flat and uniform surface finish that is suitable for high-density designs and fine-pitch components.
When deciding between HASL and ENIG, consider factors such as budget, PCB design, assembly method, environmental regulations, and shelf life. By weighing these factors against your project’s specific requirements, you can determine the most suitable surface finishing method for your PCB.
Ultimately, the choice between HASL and ENIG depends on your project’s unique needs and priorities. By understanding the characteristics, advantages, and disadvantages of each method, you can make an informed decision that balances performance, reliability, and cost-effectiveness.
Leave a Reply