What is a PCB Protective Coating?
A PCB protective coating is a layer of material applied to the surface of a printed circuit board to shield it from environmental hazards such as moisture, dust, chemicals, and extreme temperatures. These coatings act as a barrier between the sensitive electronic components and the external environment, ensuring the PCB’s long-term reliability and functionality.
The Importance of PCB Protection
PCBs are exposed to various environmental factors that can cause damage and affect their performance. Some of the most common threats include:
- Moisture: Humidity and condensation can lead to corrosion, short circuits, and electrical failures.
- Dust and debris: Airborne particles can accumulate on the PCB surface, causing insulation issues and short circuits.
- Chemicals: Exposure to harsh chemicals can degrade the PCB materials and cause corrosion.
- Extreme temperatures: High temperatures can cause thermal stress, while low temperatures can lead to condensation and moisture-related problems.
By applying a protective coating, you can minimize the impact of these environmental factors and extend the lifespan of your PCBs.
Types of PCB Protective Coatings
There are several types of PCB protective coatings available, each with its own unique properties and advantages. The most common types include:
1. Conformal Coatings
Conformal coatings are thin, flexible layers of polymer material that conform to the contours of the PCB surface. They provide excellent protection against moisture, dust, and chemicals while maintaining the PCB’s electrical properties. Some popular conformal coating materials include:
- Acrylic: Offers good moisture and chemical resistance, easy to apply and repair.
- Silicone: Provides excellent high-temperature stability and flexibility.
- Polyurethane: Delivers superior abrasion and chemical resistance.
- Epoxy: Offers high dielectric strength and resistance to solvents.
2. Potting Compounds
Potting compounds are thicker, more rigid materials that encapsulate the entire PCB or specific components. They provide excellent mechanical protection and thermal insulation, making them ideal for high-stress environments. Common potting materials include:
- Epoxy: Offers high strength, adhesion, and chemical resistance.
- Silicone: Provides good thermal stability and flexibility.
- Polyurethane: Delivers excellent shock and vibration absorption.
3. Parylene Coatings
Parylene is a unique polymer coating that is applied through a vapor deposition process, resulting in a thin, pinhole-free, and conformal coating. It offers exceptional barrier properties against moisture, chemicals, and gases, making it ideal for medical devices and other sensitive applications.
Choosing the Right PCB Protective Coating
When selecting a PCB protective coating, consider the following factors:
- Environmental conditions: Choose a coating that can withstand the specific environmental hazards your PCB will be exposed to.
- Application method: Consider the ease of application and the equipment required for each coating type.
- Reworkability: Some coatings, such as silicone and acrylic, are easier to remove for repairs or modifications.
- Cost: Balance the cost of the coating with the level of protection required for your application.
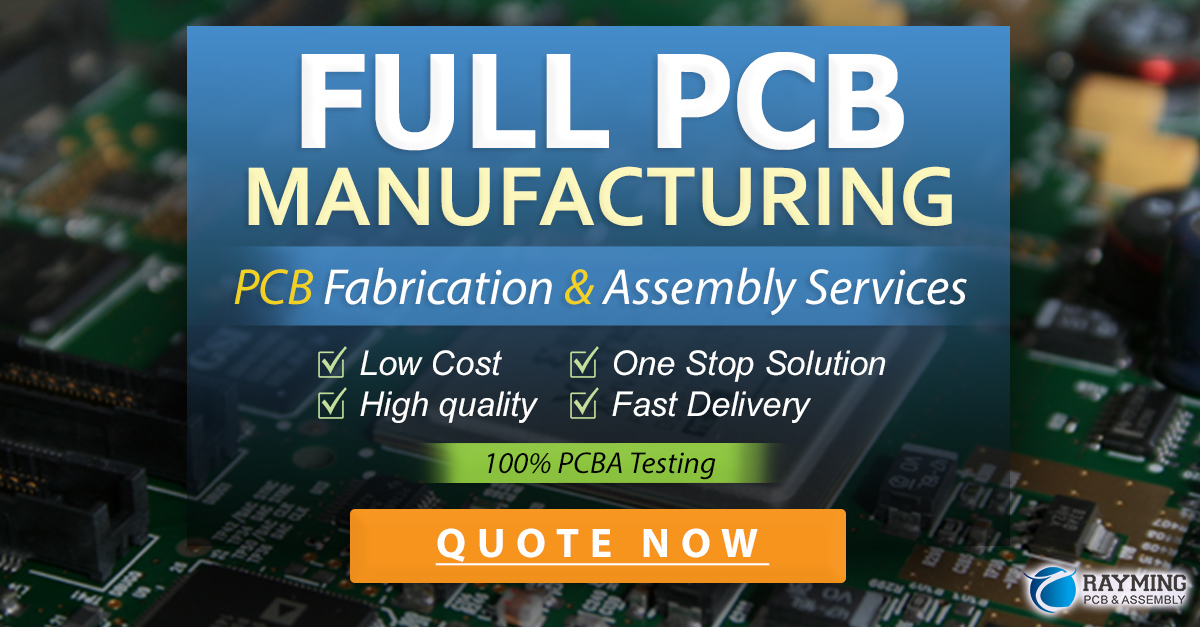
Applying PCB Protective Coatings
The application process for PCB protective coatings varies depending on the type of coating and the specific requirements of your project. However, some general steps include:
- Clean the PCB surface to remove any contaminants or debris.
- Mask off any areas that should not be coated, such as connectors or test points.
- Apply the coating using the appropriate method (e.g., spraying, dipping, or brushing).
- Allow the coating to cure according to the manufacturer’s instructions.
- Inspect the coated PCB for any defects or inconsistencies.
It’s essential to follow the manufacturer’s guidelines and use the proper equipment and safety precautions when applying PCB protective coatings.
Benefits of Using PCB Protective Coatings
Implementing PCB protective coatings offers several key benefits:
- Increased reliability: By shielding the PCB from environmental hazards, protective coatings help ensure the long-term reliability and functionality of your electronic devices.
- Extended lifespan: Protective coatings can significantly extend the lifespan of your PCBs, reducing the need for frequent replacements and repairs.
- Improved performance: By maintaining the PCB’s electrical properties and preventing damage, protective coatings help optimize the performance of your electronic devices.
- Cost savings: Investing in PCB protection can save you money in the long run by reducing maintenance costs and minimizing downtime caused by PCB failures.
PCB Shield: A Comprehensive Solution
PCB Shield is a term that encompasses the various types of protective coatings and enclosures designed to safeguard printed circuit boards from environmental hazards. By combining the right coating materials with proper application techniques, PCB Shield offers a comprehensive solution for ensuring the long-term reliability and performance of your electronic devices.
Some key advantages of using PCB Shield include:
- Customizable protection: PCB Shield can be tailored to meet the specific requirements of your application, taking into account factors such as environmental conditions, performance needs, and budget constraints.
- Versatile application: With a wide range of coating materials and application methods available, PCB Shield can be used in various industries, from consumer electronics to aerospace and defense.
- Proven effectiveness: PCB Shield has been extensively tested and proven to provide excellent protection against moisture, dust, chemicals, and extreme temperatures, making it a reliable choice for safeguarding your PCBs.
Frequently Asked Questions (FAQ)
-
Q: How do I know if my PCB needs a protective coating?
A: If your PCB will be exposed to environmental hazards such as moisture, dust, chemicals, or extreme temperatures, it’s highly recommended to use a protective coating. Additionally, if your device requires high reliability or has a long expected lifespan, a protective coating can help ensure its long-term performance. -
Q: Can I apply a PCB protective coating myself?
A: While it’s possible to apply some protective coatings yourself, it’s generally recommended to have a professional do it, especially for more complex coatings like parylene. This ensures proper application and minimizes the risk of defects or inconsistencies. -
Q: Will a PCB protective coating affect the PCB’s electrical properties?
A: Most protective coatings are designed to maintain the PCB’s electrical properties, but it’s essential to choose a coating that is compatible with your specific PCB materials and design. Some coatings, such as conformal coatings, are thin enough to have minimal impact on electrical properties. -
Q: Can a PCB protective coating be removed for repairs or modifications?
A: Some protective coatings, such as silicone and acrylic conformal coatings, can be easily removed for repairs or modifications. Others, like potting compounds, are more difficult to remove and may require specialized equipment or techniques. -
Q: How long does a PCB protective coating last?
A: The lifespan of a PCB protective coating depends on various factors, including the type of coating, the environmental conditions, and the application method. In general, a well-applied protective coating can last several years, significantly extending the lifespan of your PCB.
Conclusion
PCB protective coatings, or PCB Shields, are essential for ensuring the long-term reliability and performance of your electronic devices. By shielding your PCBs from environmental hazards like moisture, dust, chemicals, and extreme temperatures, these coatings help extend the lifespan of your circuits and minimize the risk of failures.
When choosing a PCB protective coating, consider factors such as environmental conditions, application method, reworkability, and cost. By selecting the right coating and applying it properly, you can enjoy the benefits of increased reliability, extended lifespan, improved performance, and cost savings.
Remember, investing in PCB protection is an investment in the future of your electronic devices. By taking proactive steps to safeguard your PCBs, you can ensure their long-term functionality and avoid costly repairs or replacements down the line.
As technology continues to advance, the importance of PCB protective coatings will only continue to grow. Whether you’re designing consumer electronics, industrial equipment, or medical devices, incorporating PCB shields into your design process is a smart choice that will pay dividends in the long run.
So, don’t leave your circuits vulnerable to the elements. Embrace the power of PCB protective coatings and give your electronic devices the shield they need to perform at their best, day in and day out.
Table 1: Comparison of Common PCB Protective Coatings
Coating Type | Moisture Resistance | Chemical Resistance | Temperature Range | Reworkability |
---|---|---|---|---|
Acrylic | Good | Good | -40°C to 120°C | Easy |
Silicone | Excellent | Good | -40°C to 200°C | Easy |
Polyurethane | Excellent | Excellent | -40°C to 120°C | Moderate |
Epoxy | Excellent | Excellent | -40°C to 150°C | Difficult |
Parylene | Excellent | Excellent | -200°C to 150°C | Difficult |
Table 2: PCB Protective Coating Application Methods
Application Method | Advantages | Disadvantages |
---|---|---|
Spray Coating | Fast, easy to automate | Overspray, uneven coverage |
Dip Coating | Full coverage, consistent thickness | Slow, excess material waste |
Brush Coating | Localized application, low cost | Labor-intensive, inconsistent coverage |
Vapor Deposition (Parylene) | Uniform, pinhole-free coverage | Expensive equipment, slow process |
Leave a Reply