Introduction to PCB Optimization for High Current Motor Control Applications
Printed Circuit Boards (PCBs) are essential components in modern electronics, providing a platform for interconnecting electronic components and ensuring reliable operation. When it comes to high current motor control applications, PCB optimization becomes crucial to ensure efficient power delivery, minimize losses, and maintain system stability. In this article, we will delve into the key aspects of optimizing PCBs for high current motor controls, covering topics such as component selection, layout techniques, thermal management, and testing considerations.
The Importance of PCB Optimization in Motor Control Systems
Motor control systems often require high currents to drive powerful motors, making PCB optimization a critical factor in ensuring reliable and efficient operation. Poorly designed PCBs can lead to several issues, including:
- Excessive power losses due to high resistance traces
- Electromagnetic interference (EMI) affecting sensitive circuitry
- Thermal management problems leading to component failure
- Signal integrity issues resulting in erratic motor behavior
By optimizing the PCB design, engineers can mitigate these challenges and create robust motor control systems that deliver optimal performance.
Key Considerations for High Current PCB Design
Selecting the Right Components
Power MOSFETs and IGBTs
Power MOSFETs and IGBTs are commonly used switching devices in motor control applications. When selecting these components, consider the following factors:
- Voltage and current ratings: Ensure the devices can handle the required voltage and current levels with a sufficient safety margin.
- On-resistance (RDS(on)): Lower RDS(on) values minimize conduction losses and improve efficiency.
- Switching speed: Faster switching speeds reduce switching losses but may increase EMI.
- Package type: Select packages that provide good thermal performance and low parasitic inductance.
Gate Drivers
Gate drivers are essential for controlling the switching of power MOSFETs and IGBTs. Consider the following when choosing gate drivers:
- Drive current capability: Ensure the gate driver can provide sufficient current to quickly charge and discharge the gate capacitance of the switching devices.
- Isolation: Use isolated gate drivers when required to protect control circuitry and improve noise immunity.
- Propagation delay: Minimize propagation delay to ensure accurate timing and reduce switching losses.
Passive Components
Passive components, such as capacitors and inductors, play a crucial role in filtering, energy storage, and noise suppression. Consider the following factors:
- Voltage and current ratings: Select components with appropriate ratings to handle the expected voltage and current levels.
- Equivalent Series Resistance (ESR): Low ESR values minimize power losses and improve overall efficiency.
- Thermal performance: Choose components with good thermal characteristics to prevent overheating and ensure long-term reliability.
PCB Layout Techniques
Power and Ground Planes
Using dedicated power and ground planes is essential for minimizing resistance, reducing EMI, and improving signal integrity. Consider the following guidelines:
- Use thick copper layers for power and ground planes to minimize resistance and improve current carrying capacity.
- Provide adequate clearance between power and ground planes to prevent voltage breakdown.
- Use multiple vias to connect power and ground planes to component pads, minimizing inductance and improving current distribution.
Component Placement
Proper component placement is crucial for optimizing PCB performance. Follow these guidelines:
- Place power components close to their respective power and ground planes to minimize trace lengths and reduce inductance.
- Position sensitive analog and digital circuitry away from high current paths to minimize crosstalk and EMI.
- Consider the thermal characteristics of components and place them in a manner that promotes efficient heat dissipation.
Trace Routing
Trace routing plays a significant role in determining the performance of high current PCBs. Consider the following techniques:
- Use wide traces for high current paths to minimize resistance and improve current carrying capacity.
- Minimize trace lengths to reduce inductance and improve signal integrity.
- Avoid sharp corners and use curved traces to reduce current crowding and minimize electromagnetic radiation.
- Provide sufficient spacing between traces to prevent crosstalk and ensure proper isolation.
Thermal Management Strategies
Copper Pour and Thickening
Copper pour and thickening techniques help improve heat dissipation and reduce thermal stress on components. Consider the following:
- Use large copper pours for power components to increase the surface area for heat dissipation.
- Thicken copper traces in high current paths to improve thermal conductivity and reduce temperature rise.
- Provide thermal vias to transfer heat from components to the PCB’s backside for improved cooling.
Heatsinks and Cooling Solutions
For components with high power dissipation, additional cooling solutions may be necessary. Consider the following options:
- Attach heatsinks to power components to increase the surface area for heat dissipation and improve thermal performance.
- Use thermal interface materials (TIMs) to ensure good thermal contact between components and heatsinks.
- Implement forced air cooling or liquid cooling solutions for demanding applications with high power densities.
PCB Material Selection
The choice of PCB material can significantly impact thermal management. Consider the following:
- Use high thermal conductivity materials, such as aluminum or copper-clad laminates, to improve heat spreading and dissipation.
- Select PCB substrates with low thermal resistance to minimize temperature gradients across the board.
- Consider using metal core PCBs (MCPCBs) for applications with extreme thermal requirements.
Testing and Validation
Power Integrity Analysis
Performing power integrity analysis is crucial to ensure reliable operation of high current PCBs. Consider the following techniques:
- Conduct DC voltage drop analysis to identify areas of high resistance and potential voltage sag.
- Perform AC impedance analysis to evaluate the power delivery network’s stability and identify resonance issues.
- Use simulation tools to predict and optimize the PCB’s power distribution performance.
Thermal Analysis
Thermal analysis helps identify hot spots and ensure components operate within their specified temperature ranges. Consider the following methods:
- Perform thermal simulations to predict temperature distributions and identify areas requiring additional cooling.
- Use thermal imaging cameras to capture real-time temperature data during testing and validation.
- Monitor component temperatures using thermocouples or embedded temperature sensors.
EMC Testing
Electromagnetic compatibility (EMC) testing is essential to ensure the PCB does not cause interference to other systems and complies with relevant standards. Consider the following:
- Conduct conducted and radiated emissions tests to measure the PCB’s electromagnetic emissions.
- Perform susceptibility tests to evaluate the PCB’s immunity to external electromagnetic disturbances.
- Implement EMI shielding and filtering techniques to mitigate electromagnetic interference.
Frequently Asked Questions (FAQ)
1. What are the most critical factors to consider when optimizing a high current PCB for motor controls?
The most critical factors include selecting appropriate components (power MOSFETs, IGBTs, gate drivers, and passive components), implementing proper PCB layout techniques (power and ground planes, component placement, and trace routing), and employing effective thermal management strategies (copper pour, heatsinks, and PCB material selection).
2. How can I minimize power losses in high current PCBs?
To minimize power losses, consider using components with low on-resistance (RDS(on)) and low equivalent series resistance (ESR), implementing wide traces for high current paths, minimizing trace lengths, and using thick copper layers for power and ground planes.
3. What are the benefits of using dedicated power and ground planes in high current PCBs?
Dedicated power and ground planes help minimize resistance, reduce electromagnetic interference (EMI), and improve signal integrity. They provide a low-impedance path for current flow and help distribute current evenly across the PCB.
4. How can I ensure proper thermal management in high current PCBs?
Proper thermal management can be achieved by using copper pour and thickening techniques to increase the surface area for heat dissipation, attaching heatsinks to power components, using thermal interface materials, and selecting PCB materials with high thermal conductivity. In some cases, forced air cooling or liquid cooling solutions may be necessary.
5. What types of testing and validation should be performed on high current PCBs for motor controls?
Essential testing and validation for high current PCBs include power integrity analysis (DC voltage drop and AC impedance analysis), thermal analysis (thermal simulations and temperature monitoring), and electromagnetic compatibility (EMC) testing (conducted and radiated emissions tests, susceptibility tests, and EMI shielding).
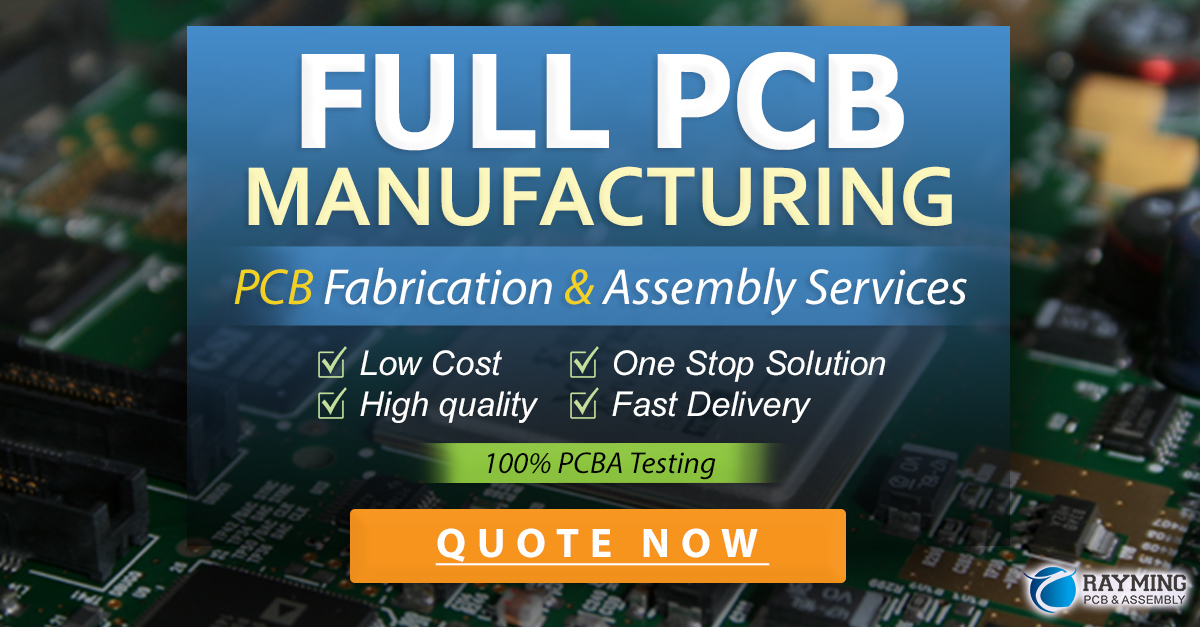
Conclusion
Optimizing high current PCBs for motor control applications requires careful consideration of component selection, layout techniques, thermal management, and testing procedures. By following the guidelines and best practices outlined in this article, engineers can design PCBs that deliver efficient power delivery, maintain system stability, and ensure long-term reliability.
Effective PCB optimization involves selecting components with appropriate ratings and performance characteristics, implementing proper layout techniques such as dedicated power and ground planes, strategic component placement, and optimized trace routing. Thermal management strategies, including copper pour, heatsinks, and PCB material selection, play a crucial role in preventing overheating and ensuring reliable operation.
To validate the performance of high current PCBs, conducting power integrity analysis, thermal analysis, and EMC testing is essential. These testing procedures help identify potential issues and ensure the PCB meets the required specifications and standards.
By prioritizing PCB optimization in motor control systems, engineers can create robust and efficient designs that maximize performance, minimize power losses, and ensure the longevity of the electronic components. As the demands for high-performance motor control systems continue to grow, the importance of well-optimized PCBs will only increase, driving innovation and advancement in this critical area of electronics design.
Leave a Reply