What is BGA PCB Assembly?
BGA PCB assembly involves attaching BGA components to a printed circuit board. BGA packages have an array of solder balls on the bottom side, which are used to make electrical connections to the PCB. During the assembly process, the BGA component is aligned with the corresponding pads on the PCB, and the solder balls are reflowed to establish a reliable connection.
Advantages of BGA PCB Assembly
BGA PCB assembly offers several advantages over other packaging technologies:
- Higher interconnection density: BGA packages can accommodate a large number of interconnections in a small area, enabling the design of complex, high-performance electronic devices.
- Improved electrical performance: The short lead lengths and low inductance of BGA packages result in better signal integrity and reduced electromagnetic interference (EMI).
- Enhanced thermal management: BGA packages have a large surface area for heat dissipation, which helps in managing the thermal performance of the device.
- Smaller package size: BGA technology allows for the creation of smaller, more compact electronic devices, which is particularly important in mobile and wearable applications.
BGA PCB Assembly Process
The BGA PCB assembly process consists of several steps, each requiring specialized equipment and expertise.
1. PCB Design and Fabrication
The first step in BGA PCB assembly is designing and fabricating the printed circuit board. The PCB design must accommodate the specific requirements of the BGA package, including the pad layout, solder mask opening, and via placement. High-quality PCB fabrication is essential to ensure the accuracy and reliability of the final assembly.
2. Solder Paste Printing
Solder paste, a mixture of tiny solder spheres and flux, is applied to the PCB pads using a stencil printing process. The stencil is a thin metal sheet with openings that match the pad layout on the PCB. Solder paste is dispensed onto the stencil and scraped across the surface, depositing the paste onto the pads through the openings.
3. BGA Component Placement
The BGA component is carefully aligned with the pads on the PCB using a pick-and-place machine. Accurate placement is crucial to ensure proper solder ball alignment and prevent defects such as bridging or open connections. Modern pick-and-place machines use vision systems and high-precision motion control to achieve placement accuracies of ±0.025 mm or better.
4. Reflow Soldering
After BGA component placement, the PCB assembly undergoes a reflow soldering process. The assembly is heated in a reflow oven, following a specific temperature profile that allows the solder paste to melt, wet the surfaces of the pads and solder balls, and form a reliable connection upon cooling. Precise control of the reflow profile is essential to prevent defects such as solder ball collapse, pad lifting, or insufficient wetting.
5. Inspection and Testing
Post-reflow inspection and testing are critical to ensure the quality and reliability of the BGA PCB assembly. Automated optical inspection (AOI) systems are commonly used to detect surface-level defects such as missing or misaligned components, solder bridges, or insufficient solder joints. X-ray inspection may be employed to detect hidden defects, such as voids or cracks in the solder joints beneath the BGA package. Electrical testing, including in-circuit testing (ICT) and functional testing, is performed to verify the performance and functionality of the assembled PCB.
Challenges in BGA PCB Assembly
BGA PCB assembly presents several challenges that must be addressed to ensure a reliable and high-quality final product.
1. Thermal Management
BGA packages generate significant amounts of heat during operation, which must be effectively dissipated to prevent performance degradation and premature failure. Proper thermal management requires careful PCB design, including the use of thermal vias, heat spreaders, and heat sinks. The assembly process must also maintain strict control over the reflow temperature profile to prevent damage to the BGA package or PCB.
2. Solder Joint Reliability
The reliability of BGA solder joints is critical to the long-term performance of the electronic device. Factors such as thermal cycling, mechanical stress, and vibration can lead to solder joint fatigue and failure. To mitigate these risks, the assembly process must employ high-quality materials, precise process control, and robust design practices, such as underfill encapsulation or corner bonding.
3. Rework and Repair
Reworking or repairing BGA PCB assemblies can be challenging due to the high interconnection density and the hidden nature of the solder joints. Specialized equipment, such as hot air rework stations and BGA reballing systems, are required to remove and replace defective BGA components without damaging the PCB or neighboring components. Skilled operators with extensive experience are essential for successful BGA Rework and repair.
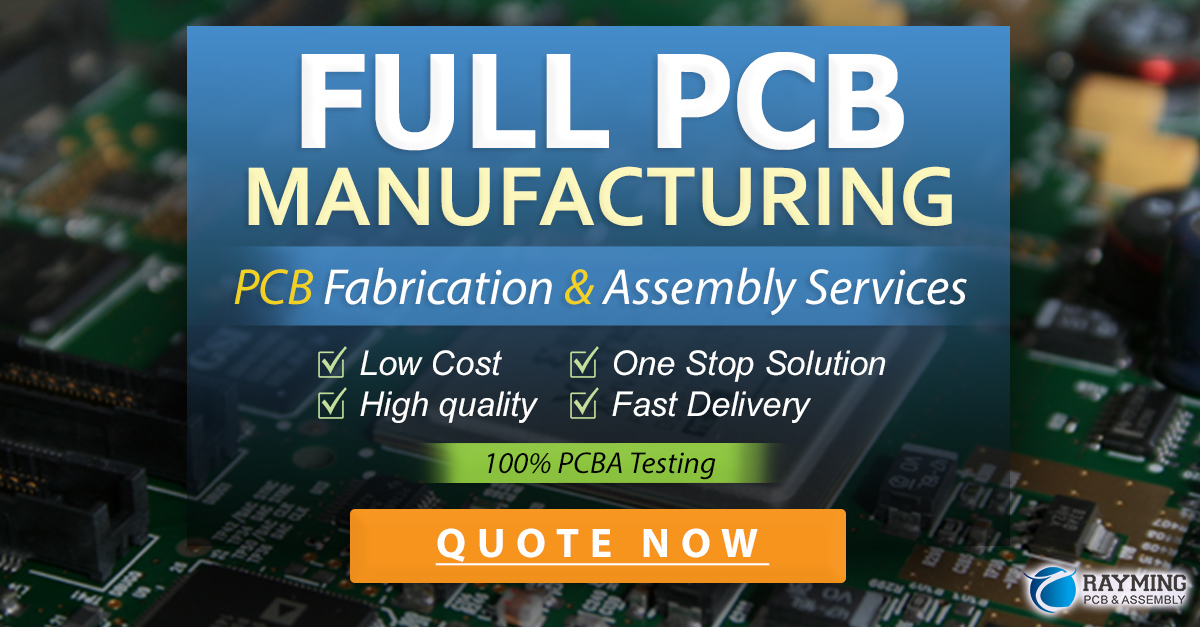
Quality Considerations in BGA PCB Assembly
Ensuring the quality and reliability of BGA PCB assemblies requires a comprehensive approach that encompasses design, materials, processes, and testing.
1. Design for Manufacturing (DFM)
Incorporating DFM principles into the PCB design process can significantly improve the manufacturability and reliability of BGA PCB assemblies. Key DFM considerations include:
- Pad size and shape optimization
- Solder mask opening design
- Via placement and fill requirements
- Thermal management features
Collaborating with experienced BGA PCB assembly service providers during the design phase can help identify and address potential manufacturing challenges early in the development cycle.
2. Material Selection
The choice of materials, including the PCB substrate, solder paste, and BGA package, can significantly impact the quality and reliability of the final assembly. Factors to consider when selecting materials include:
- Thermal expansion compatibility
- Electrical performance requirements
- Environmental resistance (e.g., moisture, corrosion)
- Regulatory compliance (e.g., RoHS, REACH)
Working with reputable suppliers and thoroughly testing materials prior to production can help ensure consistent quality and performance.
3. Process Control
Strict process control is essential to achieving high-quality BGA PCB assemblies. Key process parameters that must be monitored and controlled include:
- Solder paste printing (e.g., stencil thickness, aperture size, print speed)
- BGA component placement (e.g., accuracy, placement force, nozzle type)
- Reflow soldering (e.g., temperature profile, peak temperature, cooling rate)
Implementing statistical process control (SPC) techniques and regularly calibrating equipment can help maintain process consistency and identify potential issues before they impact product quality.
4. Testing and Inspection
Comprehensive testing and inspection are critical to verifying the quality and reliability of BGA PCB assemblies. A typical testing and inspection plan may include:
- Automated optical inspection (AOI)
- X-ray inspection
- In-circuit testing (ICT)
- Boundary scan testing
- Functional testing
- Environmental testing (e.g., thermal cycling, vibration, shock)
Developing and executing a robust testing and inspection strategy can help identify defects, validate performance, and ensure the long-term reliability of the final product.
Choosing a BGA PCB Assembly Service Provider
Selecting the right BGA PCB assembly service provider is crucial to the success of your project. When evaluating potential partners, consider the following factors:
- Technical expertise and experience
- Quality management systems and certifications (e.g., ISO 9001, IPC-A-610)
- Equipment and technology capabilities
- Capacity and scalability
- Supply chain management and sourcing capabilities
- Communication and customer support
- Intellectual property protection and security measures
Engaging with a full-service BGA PCB assembly provider that offers end-to-end support, from design and prototyping through production and testing, can streamline your development process and ensure a high-quality final product.
FAQs
1. What is the difference between BGA and QFN packages?
BGA (Ball Grid Array) and QFN (Quad Flat No-lead) are both surface-mount package types, but they have distinct differences. BGA packages have an array of solder balls on the bottom side for electrical connection, while QFN packages have exposed pads on the bottom surface. BGA packages offer higher interconnection density and better thermal performance, while QFN packages are generally smaller and less expensive. The choice between BGA and QFN depends on the specific requirements of the application, including size, performance, and cost considerations.
2. Can BGA PCBs be reworked or repaired?
Yes, BGA PCBs can be reworked or repaired, but the process is more challenging compared to traditional through-hole or surface-mount components. Specialized equipment, such as hot air rework stations and BGA reballing systems, are required to remove and replace defective BGA components without damaging the PCB or neighboring components. Skilled operators with extensive experience are essential for successful BGA rework and repair. Proper planning, documentation, and training can help minimize the need for rework and ensure the success of repair operations when necessary.
3. What is the typical lead time for BGA PCB assembly services?
The lead time for BGA PCB assembly services varies depending on factors such as PCB complexity, order quantity, and supplier capacity. Typical lead times range from 2-4 weeks for prototyping and small-volume production, to 6-8 weeks or more for high-volume production runs. Rush services may be available for time-critical projects, but they often come at a premium cost. To ensure timely delivery, it is important to communicate your requirements and timeline with your BGA PCB assembly service provider early in the development process and plan accordingly.
4. How can I ensure the long-term reliability of BGA PCB assemblies?
Ensuring the long-term reliability of BGA PCB assemblies requires a comprehensive approach that encompasses design, materials, processes, and testing. Key strategies include:
- Incorporating Design for Manufacturing (DFM) principles to optimize PCB layout and component selection
- Selecting high-quality materials with compatible thermal and mechanical properties
- Implementing strict process controls and statistical process control (SPC) techniques
- Conducting comprehensive testing and inspection, including environmental testing (e.g., thermal cycling, vibration, shock)
- Collaborating with experienced BGA PCB assembly service providers to leverage their expertise and best practices
By adopting a proactive, quality-focused approach throughout the development and production cycle, you can significantly improve the long-term reliability and performance of your BGA PCB assemblies.
5. What are the cost considerations for BGA PCB assembly services?
The cost of BGA PCB assembly services depends on several factors, including:
- PCB complexity and layer count
- BGA package type and size
- Order quantity and production volume
- Material and component costs
- Testing and inspection requirements
- Shipping and logistics
In general, BGA PCB assembly tends to be more expensive than traditional through-hole or surface-mount assembly due to the specialized equipment, materials, and expertise required. However, the higher upfront costs are often offset by the improved performance, reliability, and space savings offered by BGA technology. To optimize costs, consider strategies such as:
- Designing for manufacturability to minimize complexity and reduce assembly time
- Leveraging economies of scale by consolidating orders or increasing production volumes
- Negotiating volume discounts or long-term agreements with suppliers
- Implementing cost-effective testing and inspection strategies, such as automated optical inspection (AOI) and sample-based testing
Working closely with your BGA PCB assembly service provider to understand cost drivers and explore cost-saving opportunities can help you achieve the best balance of performance, reliability, and affordability for your project.
Conclusion
Full coverage BGA PCB assembly services are essential for the development and production of advanced electronic devices. By understanding the benefits, processes, challenges, and quality considerations involved in BGA PCB assembly, you can make informed decisions and collaborate effectively with your service provider to achieve the best possible results.
Successful BGA PCB assembly requires a combination of expert design, high-quality materials, precise process control, and comprehensive testing and inspection. Partnering with an experienced, full-service BGA PCB assembly provider can help you navigate the complexities of the process and ensure the quality, reliability, and performance of your final product.
As BGA technology continues to evolve and new applications emerge, staying informed about best practices and trends in BGA PCB assembly will be crucial to staying competitive in the fast-paced world of electronics manufacturing.
Aspect | Key Considerations |
---|---|
Design | – Pad size and shape optimization – Solder mask opening design – Via placement and fill requirements – Thermal management features |
Materials | – Thermal expansion compatibility – Electrical performance requirements – Environmental resistance – Regulatory compliance |
Processes | – Solder paste printing – BGA component placement – Reflow soldering – Statistical process control (SPC) |
Testing & Inspection | – Automated optical inspection (AOI) – X-ray inspection – In-circuit testing (ICT) – Boundary scan testing – Functional testing – Environmental testing |
By addressing these key aspects and partnering with a reliable BGA PCB assembly service provider, you can unlock the full potential of BGA technology and create innovative, high-performance electronic products that meet the demands of today’s competitive market.
Leave a Reply