What is Black Pad?
Black pad, also known as “black pad syndrome” or “black pad defect”, is a common problem that can occur during the manufacturing process of printed circuit boards (PCBs). It is characterized by a black or dark gray discoloration on the surface of the PCB’s solder pads, which can lead to poor solderability, weak solder joints, and even complete failure of the electrical connection.
The black pad phenomenon is typically associated with the use of electroless nickel/immersion gold (ENIG) surface finish, although it can also occur with other surface finishes such as immersion silver (IAg) and organic solderability preservatives (OSP).
Causes of Black Pad
There are several factors that can contribute to the formation of black pad on PCBs:
Excessive Immersion Gold Thickness
One of the primary causes of black pad is an excessive thickness of the immersion gold layer. When the gold layer is too thick, it can lead to the formation of a brittle intermetallic compound (IMC) layer at the interface between the nickel and gold layers. This IMC layer is prone to cracking and delamination, which can expose the underlying nickel layer to oxidation and corrosion, resulting in the black discoloration.
The recommended thickness for the immersion gold layer is typically between 0.05 and 0.10 microns (2-4 microinches). Thicknesses greater than 0.15 microns (6 microinches) are considered excessive and can significantly increase the risk of black pad formation.
Inadequate Nickel Thickness
Another factor that can contribute to black pad is an inadequate thickness of the electroless nickel layer. The nickel layer serves as a barrier between the copper substrate and the immersion gold layer, preventing the diffusion of copper into the gold layer and the formation of brittle IMCs.
If the nickel layer is too thin, it may not provide sufficient protection against copper diffusion, leading to the formation of a thick IMC layer and an increased risk of black pad. The recommended thickness for the electroless nickel layer is typically between 3 and 6 microns (120-240 microinches).
Contamination and Impurities
Contamination and impurities in the plating baths can also contribute to the formation of black pad. Contaminants such as organic compounds, sulfur, and heavy metals can interfere with the plating process and lead to the formation of weak or porous nickel and gold layers, which are more susceptible to oxidation and corrosion.
To minimize the risk of contamination, it is important to maintain strict control over the purity of the plating baths and to regularly monitor and adjust the bath chemistry as needed.
Improper Rinsing and Drying
Improper rinsing and drying of the PCBs after the plating process can also contribute to the formation of black pad. If the PCBs are not thoroughly rinsed to remove any residual plating solution or if they are not properly dried before the next processing step, it can lead to the formation of contaminants and impurities on the surface of the pads.
To prevent this, it is important to ensure that the PCBs are thoroughly rinsed with deionized water after each plating step and that they are completely dried using a clean, hot air dryer or an oven before proceeding to the next step.
Prevention of Black Pad
There are several steps that can be taken to prevent the formation of black pad on PCBs:
Optimize Immersion Gold Thickness
As mentioned earlier, excessive immersion gold thickness is one of the primary causes of black pad. To prevent this, it is important to optimize the thickness of the gold layer to ensure that it is within the recommended range of 0.05 to 0.10 microns (2-4 microinches).
This can be achieved by carefully controlling the immersion time and temperature during the gold plating process and by regularly monitoring the thickness of the gold layer using X-ray fluorescence (XRF) or other analytical techniques.
Ensure Adequate Nickel Thickness
To prevent the formation of black pad due to inadequate nickel thickness, it is important to ensure that the electroless nickel layer is deposited to the recommended thickness of 3 to 6 microns (120-240 microinches).
This can be achieved by carefully controlling the plating time and temperature during the nickel plating process and by regularly monitoring the thickness of the nickel layer using cross-sectional analysis or other analytical techniques.
Maintain Bath Purity
To prevent contamination and impurities in the plating baths, it is important to maintain strict control over the purity of the bath chemistry. This can be achieved by regularly monitoring the bath composition using analytical techniques such as atomic absorption spectroscopy (AAS) or inductively coupled plasma (ICP) analysis and by adjusting the bath chemistry as needed to maintain the desired composition.
It is also important to use high-purity chemicals and to filter the plating solutions regularly to remove any particulate contaminants.
Improve Rinsing and Drying
To prevent the formation of black pad due to improper rinsing and drying, it is important to ensure that the PCBs are thoroughly rinsed with deionized water after each plating step and that they are completely dried before proceeding to the next step.
This can be achieved by using a multi-stage rinsing process with a final rinse in high-purity deionized water and by using a clean, hot air dryer or an oven to dry the PCBs completely.
Use Alternative Surface Finishes
While ENIG is a popular surface finish for PCBs due to its excellent solderability and shelf life, it is also prone to black pad formation. To reduce the risk of black pad, alternative surface finishes such as immersion silver (IAg) or organic solderability preservatives (OSP) can be used.
IAg is a metal finish that provides good solderability and is less prone to black pad formation than ENIG. OSP is a non-metallic finish that provides a temporary protective coating on the copper pads and is also less prone to black pad formation.
Surface Finish | Advantages | Disadvantages |
---|---|---|
ENIG | Excellent solderability, long shelf life, wire bondable | Prone to black pad formation, higher cost |
IAg | Good solderability, less prone to black pad, lower cost | Shorter shelf life, not suitable for wire bonding |
OSP | Low cost, less prone to black pad, easy to apply | Limited shelf life, not suitable for multiple reflow cycles |
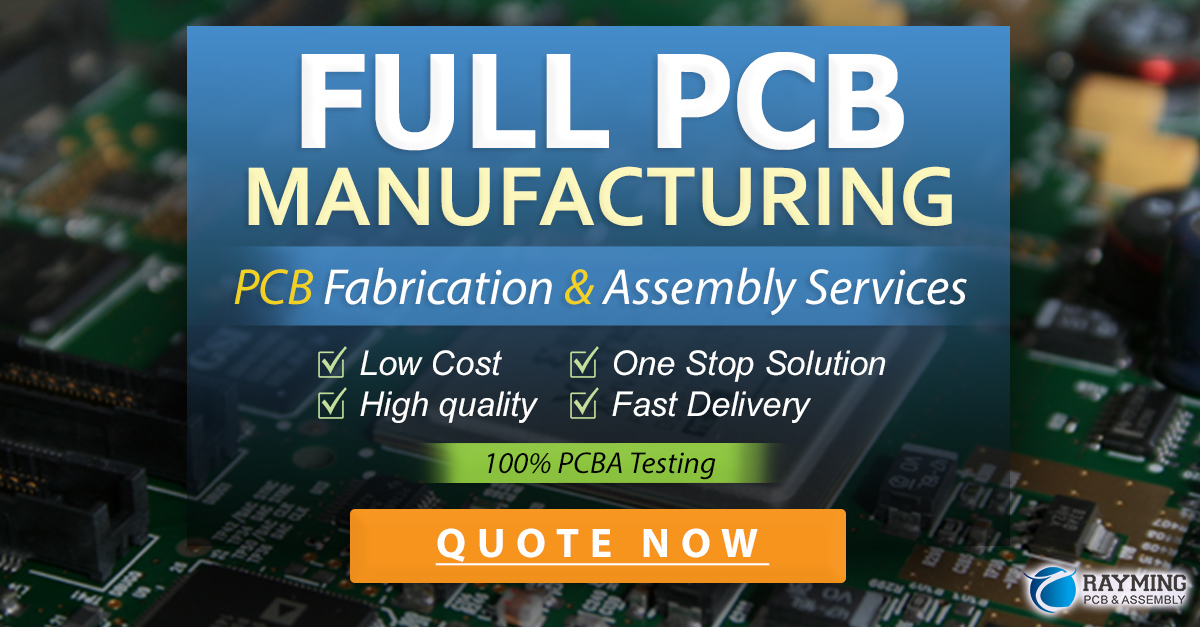
Frequently Asked Questions (FAQ)
1. What is the main cause of black pad formation on PCBs?
The main cause of black pad formation on PCBs is an excessive thickness of the immersion gold layer, which can lead to the formation of a brittle intermetallic compound (IMC) layer at the interface between the nickel and gold layers. This IMC layer is prone to cracking and delamination, exposing the underlying nickel layer to oxidation and corrosion.
2. What is the recommended thickness for the immersion gold layer to prevent black pad?
The recommended thickness for the immersion gold layer to prevent black pad is typically between 0.05 and 0.10 microns (2-4 microinches). Thicknesses greater than 0.15 microns (6 microinches) are considered excessive and can significantly increase the risk of black pad formation.
3. Can black pad formation occur with surface finishes other than ENIG?
While black pad formation is most commonly associated with ENIG surface finish, it can also occur with other surface finishes such as immersion silver (IAg) and organic solderability preservatives (OSP), although the risk is generally lower compared to ENIG.
4. How can contamination and impurities in the plating baths contribute to black pad formation?
Contamination and impurities in the plating baths can interfere with the plating process and lead to the formation of weak or porous nickel and gold layers, which are more susceptible to oxidation and corrosion. To minimize the risk of contamination, it is important to maintain strict control over the purity of the plating baths and to regularly monitor and adjust the bath chemistry as needed.
5. What alternative surface finishes can be used to reduce the risk of black pad formation?
Alternative surface finishes such as immersion silver (IAg) and organic solderability preservatives (OSP) can be used to reduce the risk of black pad formation. IAg provides good solderability and is less prone to black pad formation than ENIG, while OSP provides a temporary protective coating on the copper pads and is also less prone to black pad formation. However, these alternative finishes may have other limitations, such as shorter shelf life or unsuitability for certain applications.
Conclusion
Black pad is a serious problem that can occur during the manufacturing process of PCBs, leading to poor solderability, weak solder joints, and even complete failure of the electrical connection. The main causes of black pad formation include excessive immersion gold thickness, inadequate nickel thickness, contamination and impurities in the plating baths, and improper rinsing and drying.
To prevent black pad formation, it is important to optimize the immersion gold thickness, ensure adequate nickel thickness, maintain bath purity, improve rinsing and drying processes, and consider using alternative surface finishes such as IAg or OSP.
By understanding the causes and implementing appropriate preventive measures, manufacturers can significantly reduce the risk of black pad formation and ensure the reliability and performance of their PCBs.
Leave a Reply