Introduction to CMOS Sensor PCB Layout
CMOS (Complementary Metal-Oxide-Semiconductor) sensors have become increasingly popular in various applications, including digital cameras, smartphones, and industrial imaging systems. Designing a PCB layout for a CMOS sensor requires careful consideration of several factors to ensure optimal performance and image quality. In this article, we will delve into the key aspects of CMOS sensor PCB layout and provide valuable insights to help you master this crucial skill.
Understanding CMOS Sensor Fundamentals
Before diving into PCB layout techniques, it’s essential to understand the basics of CMOS sensors. CMOS sensors consist of an array of pixel elements, each containing a photodiode and readout circuitry. When light falls on the photodiode, it generates an electrical charge proportional to the incident light intensity. The readout circuitry then converts this charge into a digital signal for further processing.
Pixel Architecture
CMOS sensors employ an active pixel sensor (APS) architecture, where each pixel contains its own amplification and readout circuitry. This allows for high-speed readout and low power consumption compared to charge-coupled device (CCD) sensors. The pixel architecture typically includes the following components:
- Photodiode: Converts incident light into an electrical charge
- Reset transistor: Resets the photodiode to a known state before each exposure
- Source follower transistor: Amplifies the photodiode signal
- Row select transistor: Enables the readout of the pixel signal
Sensor Interfaces
CMOS sensors communicate with the host system through various interfaces, depending on the application and data rate requirements. Common interfaces include:
- Parallel interface: Provides a wide data bus for high-speed data transfer
- MIPI CSI-2 interface: A serial interface widely used in mobile devices
- LVDS (Low-Voltage Differential Signaling): Offers high-speed, low-power data transmission
Understanding the pixel architecture and sensor interfaces is crucial for designing an efficient and reliable CMOS sensor PCB layout.
PCB Layout Considerations for CMOS Sensors
When designing a PCB layout for a CMOS sensor, several key considerations must be taken into account to ensure optimal performance and image quality. Let’s explore these considerations in detail.
Power Supply and Decoupling
Providing a clean and stable power supply is critical for CMOS sensor performance. Noise on the power supply can introduce artifacts and degrade image quality. To mitigate this, consider the following:
- Use separate power planes for analog and digital circuitry to minimize crosstalk
- Place decoupling capacitors close to the sensor’s power pins to suppress high-frequency noise
- Use low-ESR (Equivalent Series Resistance) capacitors for effective decoupling
- Implement proper grounding techniques to minimize ground loops and noise coupling
Signal Integrity
Maintaining signal integrity is essential to ensure accurate and reliable data transmission from the CMOS sensor to the host system. Consider the following guidelines:
- Keep signal traces as short as possible to minimize parasitic effects
- Use controlled impedance traces for high-speed signals to prevent reflections and signal distortion
- Implement proper termination techniques, such as series termination for LVDS signals
- Avoid routing sensitive signals near sources of electromagnetic interference (EMI)
Shielding and Grounding
Effective shielding and grounding techniques are crucial for reducing electromagnetic interference (EMI) and ensuring a clean signal environment. Consider the following:
- Use ground planes to provide a low-impedance return path for high-frequency signals
- Implement proper shielding techniques, such as metal shields or grounded guard rings, around sensitive analog circuitry
- Ensure proper grounding of the sensor’s metal housing to the PCB ground plane
- Use star grounding techniques to minimize ground loops and noise coupling
Thermal Management
CMOS sensors generate heat during operation, which can affect performance and image quality. Proper thermal management is essential to ensure reliable operation. Consider the following:
- Provide adequate thermal dissipation paths, such as thermal vias or heat spreaders
- Use copper pour on the PCB to distribute heat evenly
- Consider using a heat sink or other cooling solutions for high-power applications
- Monitor the sensor’s temperature and implement thermal management techniques, such as dynamic power management or active cooling, if necessary
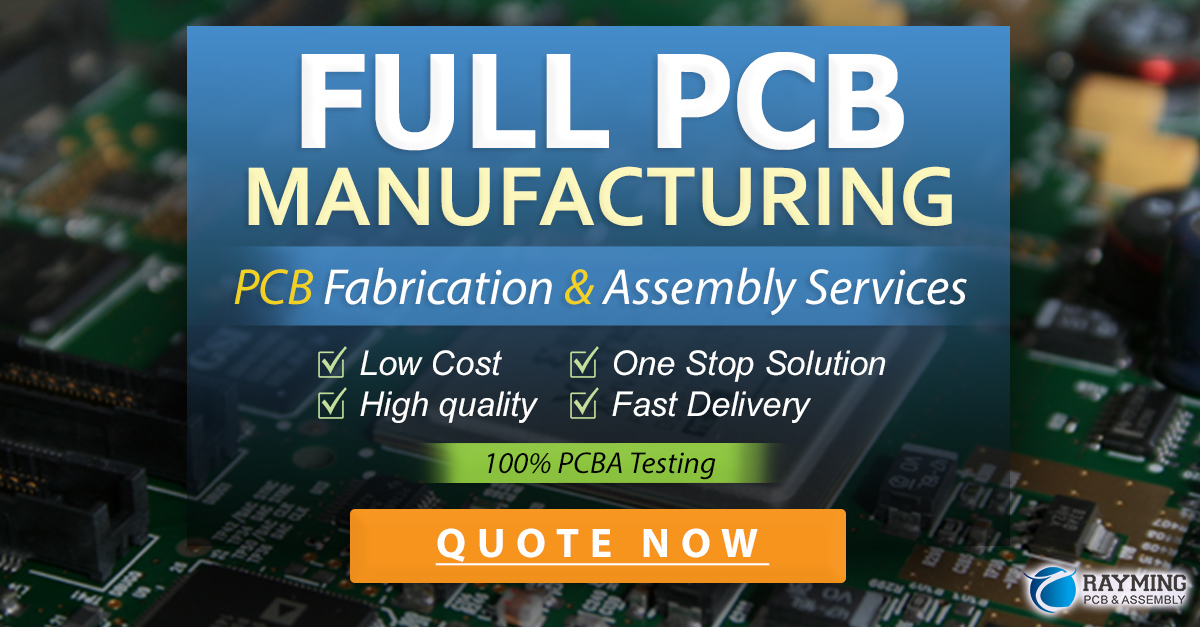
PCB Layout Techniques for CMOS Sensors
Now that we’ve covered the key considerations for CMOS sensor PCB layout, let’s explore some specific layout techniques to optimize performance and image quality.
Component Placement
Proper component placement is crucial for minimizing signal path lengths, reducing noise coupling, and ensuring efficient routing. Consider the following guidelines:
- Place the CMOS sensor as close as possible to the image processing circuitry to minimize signal path lengths
- Position decoupling capacitors as close as possible to the sensor’s power pins
- Separate analog and digital circuitry to minimize crosstalk and noise coupling
- Arrange components in a logical flow to simplify routing and improve signal integrity
Power and Ground Planes
Using dedicated power and ground planes is essential for providing a low-impedance, low-noise power distribution network. Consider the following techniques:
- Use separate power planes for analog and digital circuitry to minimize crosstalk
- Provide a solid, uninterrupted ground plane to minimize ground loops and noise coupling
- Use power and ground planes on adjacent layers to provide a low-impedance path for high-frequency currents
- Implement proper decoupling techniques, such as placing decoupling capacitors close to the sensor’s power pins
Signal Routing
Careful signal routing is essential for maintaining signal integrity and minimizing crosstalk. Consider the following guidelines:
- Route high-speed signals on controlled impedance traces to prevent reflections and signal distortion
- Keep sensitive analog signals away from noisy digital signals to minimize crosstalk
- Use differential routing techniques for high-speed interfaces, such as LVDS, to improve noise immunity
- Avoid routing signals under or near the sensor’s imaging area to prevent optical interference
Shielding Techniques
Effective shielding is crucial for reducing electromagnetic interference (EMI) and ensuring a clean signal environment. Consider the following techniques:
- Use metal shields or grounded guard rings around sensitive analog circuitry to minimize EMI
- Implement proper grounding of the sensor’s metal housing to the PCB ground plane
- Use stitching vias along the edges of the PCB to provide a low-impedance path for high-frequency currents
- Consider using ferrite beads or EMI filters on power and signal lines to suppress high-frequency noise
Testing and Validation
After completing the PCB layout for your CMOS sensor, it’s essential to thoroughly test and validate the design to ensure optimal performance and image quality. Consider the following testing and validation techniques:
Functional Testing
Perform functional testing to verify that the CMOS sensor is operating correctly and producing the expected output. This may include:
- Verifying the sensor’s power-up sequence and initialization
- Checking the sensor’s output data for accuracy and consistency
- Testing the sensor’s response to different light levels and exposure settings
- Verifying the functionality of the sensor’s interfaces and communication protocols
Signal Integrity Analysis
Use signal integrity analysis tools, such as oscilloscopes or network analyzers, to verify the integrity of the sensor’s output signals. This may include:
- Measuring signal rise and fall times to ensure they meet the required specifications
- Checking for signal reflections or distortions caused by improper termination or routing
- Verifying the signal levels and noise margins of the sensor’s interfaces
- Analyzing the frequency response and eye diagrams of high-speed signals
Electromagnetic Compatibility (EMC) Testing
Perform EMC testing to ensure that the CMOS sensor PCB layout meets the required electromagnetic compatibility standards. This may include:
- Conducted emissions testing to verify that the sensor does not generate excessive electromagnetic interference
- Radiated emissions testing to ensure that the sensor does not emit excessive electromagnetic radiation
- Conducted and radiated immunity testing to verify that the sensor is not susceptible to external electromagnetic interference
Thermal Analysis
Conduct thermal analysis to ensure that the CMOS sensor operates within its specified temperature range and that the PCB layout provides adequate thermal management. This may include:
- Measuring the sensor’s temperature under various operating conditions
- Verifying that the temperature remains within the specified limits
- Analyzing the effectiveness of the PCB’s thermal management techniques, such as heat spreading or cooling solutions
Frequently Asked Questions (FAQ)
-
What are the key considerations for CMOS sensor PCB layout?
The key considerations for CMOS sensor PCB layout include power supply and decoupling, signal integrity, shielding and grounding, and thermal management. Addressing these factors ensures optimal performance and image quality. -
How can I minimize noise coupling in my CMOS sensor PCB layout?
To minimize noise coupling, use separate power planes for analog and digital circuitry, implement proper grounding techniques, and use shielding techniques such as metal shields or grounded guard rings around sensitive analog circuitry. -
What are some best practices for routing high-speed signals in a CMOS sensor PCB layout?
When routing high-speed signals, use controlled impedance traces to prevent reflections and signal distortion, keep sensitive analog signals away from noisy digital signals, and use differential routing techniques for interfaces like LVDS to improve noise immunity. -
How can I ensure proper thermal management in my CMOS sensor PCB layout?
To ensure proper thermal management, provide adequate thermal dissipation paths such as thermal vias or heat spreaders, use copper pour on the PCB to distribute heat evenly, consider using a heat sink or other cooling solutions for high-power applications, and monitor the sensor’s temperature during operation. -
What testing and validation techniques should I use for my CMOS sensor PCB layout?
Testing and validation techniques for CMOS sensor PCB layouts include functional testing to verify the sensor’s operation, signal integrity analysis to ensure signal quality, electromagnetic compatibility (EMC) testing to meet EMC standards, and thermal analysis to ensure proper thermal management.
Conclusion
Designing a CMOS sensor PCB layout requires careful consideration of various factors, including power supply and decoupling, signal integrity, shielding and grounding, and thermal management. By following the guidelines and techniques discussed in this article, you can optimize your PCB layout for optimal performance and image quality.
Remember to prioritize proper component placement, use dedicated power and ground planes, implement effective shielding techniques, and follow best practices for signal routing. Additionally, thorough testing and validation, including functional testing, signal integrity analysis, EMC testing, and thermal analysis, are essential to ensure the reliability and performance of your CMOS sensor PCB layout.
By mastering the art of CMOS sensor PCB layout, you can unlock the full potential of these powerful imaging devices and create designs that deliver exceptional image quality and reliable operation. Keep learning, experimenting, and refining your skills to stay at the forefront of this exciting field.
Leave a Reply