What are Edge Connectors?
Edge connectors are a type of electrical connector that is designed to mate with the edge of a PCB. They consist of a plastic housing with a slot that accommodates the PCB, and a series of conductive contact fingers that press against the exposed copper traces on the edge of the board. Edge connectors are commonly used in computer systems, telecommunications equipment, and industrial control devices, among others.
Types of Edge Connectors
There are several types of edge connectors, each designed for specific applications and requirements. Some common types include:
- PCI Express (PCIe) Connectors: Used for connecting expansion cards in computer systems, such as graphics cards, sound cards, and network adapters.
- DIMM (Dual In-line Memory Module) Connectors: Used for connecting memory modules in computers and other electronic devices.
- Card Edge Connectors: A general-purpose connector used in various applications, such as industrial control systems, automotive electronics, and consumer devices.
- High-Speed Edge Connectors: Designed for high-frequency signal transmission, these connectors are used in applications such as telecommunications equipment and data center hardware.
The Importance of Edge Connector Beveling
Edge connector beveling is a process that involves chamfering or rounding the edges of the PCB that will be inserted into the connector. This is done to prevent damage to the contact fingers and ensure a smooth, reliable connection. Without proper beveling, the sharp edges of the PCB can cause scratches or gouges on the contact fingers, leading to poor electrical contact and potential failure of the connector.
Beveling Techniques
There are two primary methods for beveling the edges of a PCB:
-
Mechanical Beveling: This method involves using a specialized machine or tool to grind or sand the edges of the PCB at a specific angle, typically between 30 and 45 degrees. Mechanical beveling is suitable for low-volume production or Prototype Boards.
-
Chemical Beveling: Also known as etching, this method involves using a chemical solution to dissolve the copper and substrate material at the edges of the PCB. Chemical beveling is faster and more precise than mechanical beveling, making it ideal for high-volume production.
Beveling Specifications
The specific beveling requirements for an edge connector will depend on the type of connector and the application. However, some general guidelines include:
- Bevel angle: 30 to 45 degrees
- Bevel width: 0.2 to 0.5 mm
- Bevel depth: 0.1 to 0.3 mm
It is essential to consult the connector manufacturer’s specifications to ensure the proper beveling dimensions are achieved.
Gold Finger Plating
Gold finger plating is the process of applying a thin layer of gold over the contact fingers of an edge connector. This is done to enhance the electrical conductivity, durability, and corrosion resistance of the connector. Gold is an ideal material for this application due to its excellent electrical properties, resistance to oxidation, and compatibility with a wide range of mating surfaces.
Gold Plating Techniques
There are several methods for applying gold plating to the contact fingers of an edge connector:
-
Electroplating: This is the most common method, involving the use of an electric current to deposit gold ions onto the surface of the contact fingers. The thickness of the gold layer can be precisely controlled by adjusting the current and plating time.
-
Electroless Plating: This method uses a chemical reaction to deposit gold onto the surface without the need for an electric current. While less common than electroplating, electroless plating can provide a more uniform coating and is suitable for complex geometries.
-
Immersion Plating: Also known as displacement plating, this method involves immersing the contact fingers in a gold solution, causing a exchange reaction that deposits a thin layer of gold. Immersion plating is typically used for very thin gold layers (less than 0.1 μm) and is not as durable as electroplating or electroless plating.
Gold Plating Specifications
The thickness and composition of the gold plating will depend on the specific application and performance requirements of the edge connector. Some common specifications include:
- Gold purity: 99.9% or higher
- Plating thickness: 0.05 to 2.0 μm (1.3 to 50 μin)
- Nickel underplate: Often used as a barrier layer to prevent diffusion between the gold and the base metal (typically 1 to 5 μm thick)
Application | Typical Gold Thickness |
---|---|
Consumer electronics | 0.05 to 0.2 μm |
Industrial control | 0.2 to 0.8 μm |
Military/aerospace | 0.8 to 2.0 μm |
It is crucial to consult the relevant industry standards and customer specifications to ensure the appropriate gold plating thickness and composition are used for the intended application.
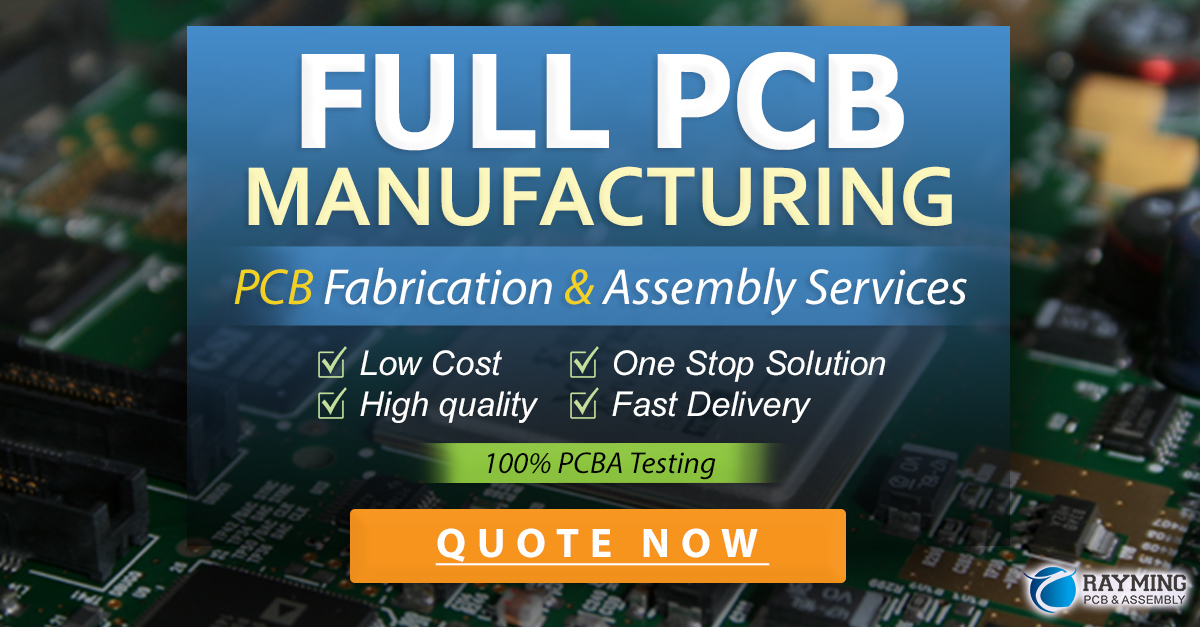
Benefits of Gold Finger Plating
Gold finger plating offers several key benefits for edge connectors:
-
Enhanced electrical conductivity: Gold’s excellent electrical properties ensure reliable signal transmission and low contact resistance.
-
Improved durability: Gold’s hardness and wear resistance help to prevent damage to the contact fingers during repeated mating cycles.
-
Corrosion resistance: Gold’s resistance to oxidation and chemical attack helps to maintain the integrity of the electrical contact over time, even in harsh environments.
-
Compatibility: Gold is compatible with a wide range of mating surfaces, including other gold-plated surfaces, tin-plated surfaces, and bare copper.
Applications of Gold Finger Plating
Gold finger plating is used in a variety of industries and applications where reliable, high-performance edge connectors are required. Some examples include:
-
Consumer electronics: Computers, smartphones, gaming consoles, and other devices that require high-speed data transfer and reliable connectivity.
-
Industrial control systems: Factory automation equipment, process control devices, and test and measurement instruments that demand robust, long-lasting connections.
-
Telecommunications: Network switches, routers, and other equipment that handle high-speed data transmission and require consistent signal integrity.
-
Military and aerospace: Defense and aviation electronics that must withstand extreme temperatures, vibration, and shock while maintaining reliable performance.
Frequently Asked Questions (FAQ)
- Q: What is the difference between gold finger plating and other types of contact plating?
A: Gold finger plating is specifically designed for edge connectors, where the contact fingers must slide against the edge of a PCB. Other types of contact plating, such as tin or silver, may be used for different connector types or applications where the specific properties of gold are not required.
- Q: Can gold finger plating be applied to any type of edge connector?
A: In general, yes. However, the specific plating process and specifications may need to be adapted to suit the connector design and material. It is essential to consult with the connector manufacturer and plating provider to ensure compatibility.
- Q: How does the thickness of the gold plating affect connector performance?
A: Thicker gold plating generally provides better durability and wear resistance, but may also increase the cost of the connector. Thinner plating may be sufficient for less demanding applications or shorter product lifetimes. The optimal plating thickness will depend on the specific requirements of the application.
- Q: What is the role of the nickel underplate in gold finger plating?
A: The nickel underplate serves as a barrier layer between the gold and the base metal (usually copper) of the contact fingers. It prevents the diffusion of copper into the gold layer, which can cause embrittlement and reduced conductivity over time. The nickel layer also provides a harder, more wear-resistant surface for the gold to adhere to.
- Q: How can I ensure the quality and consistency of gold finger plating on my edge connectors?
A: Work with a reputable plating provider that has experience with gold finger plating and a proven quality control process. Specify the required plating thickness, composition, and performance characteristics in your drawings or purchase orders, and request test reports or certificates of conformance to verify that the plating meets your requirements. Consider implementing incoming inspection or periodic testing to monitor the consistency of the plating quality over time.
Conclusion
Edge connector beveling and gold finger plating are essential processes for ensuring the reliability, durability, and performance of edge connectors in a wide range of applications. By properly beveling the edges of the PCB and applying a consistent, high-quality gold plating to the contact fingers, manufacturers can create connectors that provide stable, low-resistance electrical connections and withstand the rigors of repeated mating cycles and harsh operating environments.
As technology continues to advance and the demand for high-speed, high-density interconnects grows, the importance of gold finger plating will only increase. By understanding the principles, techniques, and benefits of this critical process, engineers and designers can make informed decisions when specifying and sourcing edge connectors for their products, ultimately leading to more reliable, efficient, and cost-effective electronic systems.
Leave a Reply