Introduction
Printed Circuit Boards (PCBs) are essential components in modern electronics, providing a platform for electrical connections and mechanical support for various components. One critical aspect of PCB design is ensuring that the traces can handle the required current capacity without overheating or failing. In this article, we will explore ten methods to achieve high-quality PCB trace current capacity, focusing on design techniques, materials, and manufacturing processes.
Understanding PCB Current Capacity
Before diving into the methods, it’s essential to understand what PCB current capacity is and why it matters. Current capacity refers to the maximum amount of current that a PCB trace can safely carry without causing damage or performance issues. Several factors influence current capacity, including:
- Trace width and thickness
- Copper weight
- Temperature rise
- Ambient temperature
- PCB material properties
Exceeding the current capacity of a trace can lead to overheating, which may cause the copper to melt, the PCB substrate to delaminate, or the components to fail prematurely. Therefore, designing PCBs with adequate current capacity is crucial for ensuring reliability and longevity.
Method 1: Increase Trace Width
One of the most straightforward ways to improve PCB trace current capacity is by increasing the trace width. Wider traces have lower resistance and can carry more current without overheating. The relationship between trace width and current capacity is not linear, as doubling the width does not double the current capacity. However, even a small increase in width can significantly improve current handling capabilities.
Trace Width (mm) | Current Capacity (A) |
---|---|
0.5 | 1.0 |
1.0 | 1.8 |
1.5 | 2.5 |
2.0 | 3.0 |
Table 1: Current capacity for different trace widths (1 oz/ft² copper, 10°C temperature rise)
When increasing trace width, designers must consider the available space on the PCB and the potential impact on signal integrity. Wider traces may introduce unwanted capacitance or crosstalk, especially in high-speed designs.
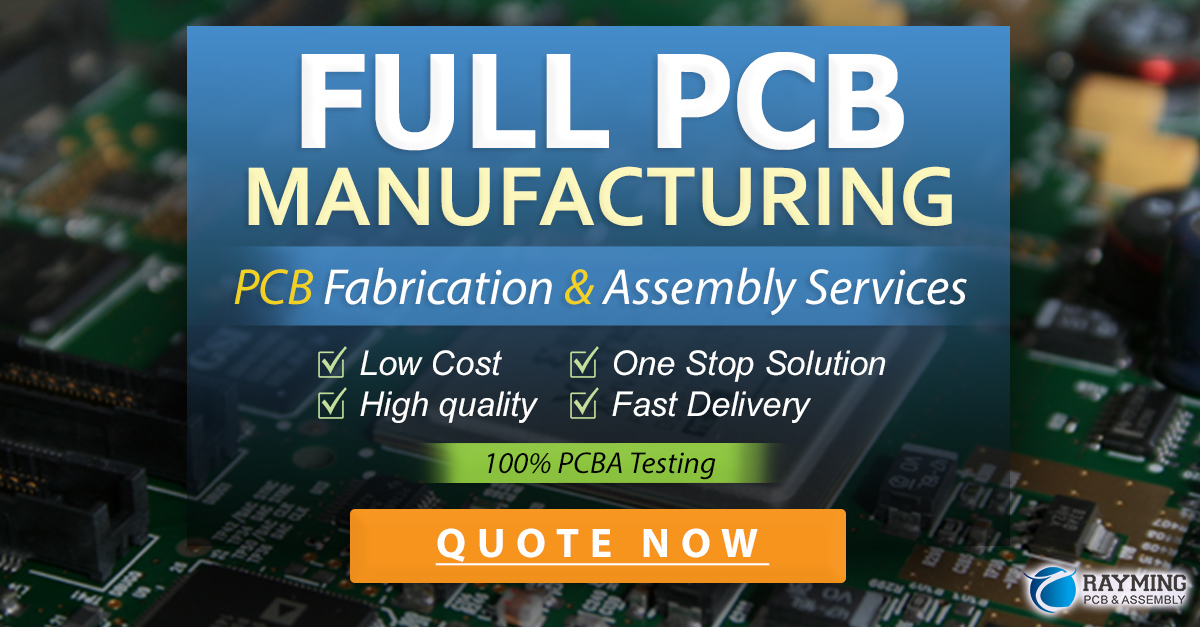
Method 2: Increase Copper Weight
Another method to improve PCB trace current capacity is by increasing the copper weight. Copper weight refers to the thickness of the copper layer on the PCB, typically measured in ounces per square foot (oz/ft²). Standard copper weights include 0.5 oz/ft², 1 oz/ft², and 2 oz/ft², with higher weights available for specialized applications.
Thicker copper layers have lower resistance and can carry more current. Doubling the copper weight roughly increases the current capacity by 40%. However, using higher copper weights also increases the cost and weight of the PCB, and may require adjustments to the manufacturing process.
Copper Weight (oz/ft²) | Current Capacity (A) |
---|---|
0.5 | 0.7 |
1.0 | 1.0 |
2.0 | 1.4 |
Table 2: Current capacity for different copper weights (1 mm trace width, 10°C temperature rise)
Method 3: Use Multiple Copper Layers
For high-current applications, using multiple copper layers can significantly increase the current capacity of PCB traces. By stacking multiple layers of copper and connecting them with vias, designers can create thicker, lower-resistance paths for current to flow.
This technique is particularly useful for power and ground planes, which often carry large currents. By using dedicated layers for power and ground, designers can ensure a low-impedance path for current and minimize voltage drops across the PCB.
When using multiple copper layers, it’s essential to consider the layer stack-up and the placement of vias to minimize inductance and ensure proper current distribution.
Method 4: Optimize Trace Routing
Trace routing plays a significant role in determining the current capacity of PCB traces. By optimizing the routing, designers can minimize the trace length, reduce resistance, and improve current handling capabilities.
Some key considerations for trace routing include:
- Minimizing the number of vias and layer changes
- Avoiding sharp corners and angles
- Using curved traces instead of right angles
- Providing adequate spacing between traces to minimize crosstalk and heat buildup
Proper trace routing not only improves current capacity but also enhances signal integrity and reduces electromagnetic interference (EMI).
Method 5: Use High-temperature PCB Materials
The choice of PCB material can significantly impact the current capacity of traces. Standard FR-4 PCBs have a maximum operating temperature of around 130°C, limiting the amount of current they can carry without overheating.
For high-current applications, using PCB materials with higher glass transition temperatures (Tg) can allow for greater current capacity. Some examples of high-temperature PCB materials include:
- Polyimide (PI): Tg up to 260°C
- High-Tg FR-4: Tg up to 170°C
- Isola 370HR: Tg up to 180°C
These materials can withstand higher temperatures without delaminating or losing their mechanical and electrical properties, enabling higher current capacities.
Method 6: Implement Thermal Management Techniques
Effective thermal management is essential for maintaining high current capacities in PCB traces. As current flows through a trace, it generates heat, which must be dissipated to prevent overheating and damage.
Some thermal management techniques for PCBs include:
- Using thermal vias to conduct heat away from high-current traces
- Incorporating heatsinks or heat spreaders to dissipate heat
- Providing adequate airflow around the PCB
- Using thermally conductive PCB materials, such as metal-core PCBs (MCPCBs)
By implementing these techniques, designers can ensure that PCB traces can handle higher currents without exceeding their temperature limits.
Method 7: Use Copper Pours
Copper pours, also known as copper fills or copper planes, are large areas of copper on a PCB layer that are not used for traces. These pours serve several purposes, including providing a low-impedance path for current, reducing EMI, and improving heat dissipation.
By strategically placing copper pours near high-current traces, designers can help spread the heat generated by the current and reduce the overall temperature rise. Copper pours can also act as a heatsink, conducting heat away from the traces and into the surrounding environment.
When using copper pours, it’s important to consider the spacing between the pour and the traces to avoid unwanted capacitance or shorting.
Method 8: Implement Current Sensing and Protection
In some cases, it may be necessary to actively monitor and protect PCB traces from overcurrent conditions. This is particularly important in power electronics applications, where fault conditions can lead to excessive current flow and damage to the PCB or components.
Current sensing and protection techniques include:
- Using shunt resistors to measure current flow
- Implementing overcurrent protection devices, such as fuses or circuit breakers
- Incorporating current-limiting circuits or regulators
- Using thermal sensors to monitor temperature and trigger protection mechanisms
By implementing these techniques, designers can ensure that PCB traces are protected from overcurrent conditions and can operate safely within their specified limits.
Method 9: Conduct Thorough Testing and Validation
Before finalizing a PCB design, it’s essential to conduct thorough testing and validation to ensure that the traces can handle the required current capacity. This involves both simulation and physical testing to verify the performance under various operating conditions.
Some key aspects of testing and validation include:
- Running thermal simulations to predict temperature rise and identify hot spots
- Performing power integrity simulations to analyze voltage drops and current distribution
- Conducting accelerated life testing to assess the long-term reliability of the PCB
- Measuring the actual current capacity of traces using specialized test equipment
By conducting comprehensive testing and validation, designers can identify and address any issues related to current capacity before the PCB goes into production.
Method 10: Follow Industry Standards and Guidelines
Finally, to ensure high-quality PCB trace current capacity, it’s essential to follow industry standards and guidelines. These standards provide proven design rules and best practices for various aspects of PCB design, including trace sizing, spacing, and routing.
Some relevant industry standards for PCB design include:
- IPC-2221: Generic Standard on Printed Board Design
- IPC-2152: Standard for Determining Current-Carrying Capacity in Printed Board Design
- IPC-6012: Qualification and Performance Specification for Rigid Printed Boards
By adhering to these standards and guidelines, designers can ensure that their PCBs meet the necessary quality and reliability requirements for their intended application.
Frequently Asked Questions (FAQ)
-
What is PCB trace current capacity, and why is it important?
PCB trace current capacity refers to the maximum amount of current that a trace can safely carry without overheating or failing. It is important because exceeding the current capacity can lead to PCB Damage, component failure, and reduced reliability. -
How can I determine the current capacity of a PCB trace?
The current capacity of a PCB trace depends on several factors, including the trace width, copper weight, temperature rise, and ambient temperature. Designers can use industry standards, such as IPC-2152, or specialized software tools to calculate the current capacity for a given set of parameters. -
What are some common methods for improving PCB trace current capacity?
Some common methods for improving PCB trace current capacity include increasing trace width, increasing copper weight, using multiple copper layers, optimizing trace routing, using high-temperature PCB materials, implementing thermal management techniques, and using copper pours. -
How does the choice of PCB material affect current capacity?
The choice of PCB material can significantly impact current capacity, as different materials have varying thermal properties and maximum operating temperatures. Using high-temperature materials, such as polyimide or high-Tg FR-4, can allow for higher current capacities compared to standard FR-4. -
What role does testing and validation play in ensuring high-quality PCB trace current capacity?
Testing and validation are essential for ensuring that PCB traces can handle the required current capacity under various operating conditions. This involves conducting thermal simulations, power integrity simulations, accelerated life testing, and physical measurements to verify performance and identify any issues before the PCB goes into production.
Conclusion
Achieving high-quality PCB trace current capacity is essential for ensuring the reliability and performance of electronic devices. By employing the ten methods discussed in this article, designers can optimize their PCBs to handle the required currents without overheating or failing.
These methods include increasing trace width and copper weight, using multiple copper layers, optimizing trace routing, selecting high-temperature PCB materials, implementing thermal management techniques, using copper pours, implementing current sensing and protection, conducting thorough testing and validation, and following industry standards and guidelines.
By carefully considering these factors and applying the appropriate techniques, designers can create PCBs that meet the demanding requirements of modern electronics applications, from consumer devices to industrial control systems and beyond.
Leave a Reply