What is a High-temperature PCB?
A high-temperature PCB is a printed circuit board that can operate reliably in environments with temperatures exceeding 150°C (302°F). These PCBs are constructed using materials and components that can withstand extreme heat without compromising their electrical and mechanical properties.
High-temperature PCB Applications
High-temperature PCBs find use in various industries and applications, including:
- Aerospace and defense
- Automotive (under-the-hood electronics)
- Oil and gas (downhole drilling)
- Industrial equipment (sensors, actuators)
- Power electronics (solar inverters, motor drives)
Materials for High-temperature PCBs
The choice of materials is crucial for the performance and reliability of high-temperature PCBs. The following table compares the properties of common PCB substrate materials:
Material | Maximum Operating Temperature | Thermal Conductivity (W/mK) | Dielectric Constant @ 1 MHz | CTE (ppm/°C) |
---|---|---|---|---|
FR-4 | 130°C | 0.3 | 4.5 | 14-16 |
Polyimide | 260°C | 0.2 | 3.5 | 12-14 |
Polytetrafluoroethylene (PTFE) | 260°C | 0.2 | 2.1 | 100-120 |
Ceramic (Alumina) | 500°C | 20-30 | 9.8 | 6-8 |
In addition to the substrate material, the choice of copper foil, solder mask, and surface finish also plays a vital role in the performance of high-temperature PCBs.
Copper Foil
High-temperature PCBs typically use copper foils with a thickness of 35 μm or more to minimize the risk of delamination and improve heat dissipation. Electrodeposited (ED) copper foils are preferred over rolled annealed (RA) foils due to their better adhesion to the substrate.
Solder Mask
Solder masks for high-temperature PCBs must withstand extreme heat without cracking, peeling, or discoloring. High-temperature liquid photoimageable (LPI) solder masks, such as those based on polyimide or silicone, are commonly used.
Surface Finish
The surface finish on high-temperature PCBs should provide good solderability, corrosion resistance, and thermal stability. Some popular surface finishes for high-temperature applications include:
- Electroless Nickel Immersion Gold (ENIG)
- Electroless Nickel Electroless Palladium Immersion Gold (ENEPIG)
- Hard Gold (over Nickel)
Design Considerations for High-temperature PCBs
Designing high-temperature PCBs requires careful consideration of thermal management, component selection, and layout optimization.
Thermal Management
Effective thermal management is essential to ensure the reliable operation of high-temperature PCBs. Some strategies for improving heat dissipation include:
- Using thermally conductive substrates (e.g., ceramic, metal-core PCBs)
- Incorporating thermal vias and heat sinks
- Optimizing component placement and trace routing
- Employing forced air or liquid cooling methods
Component Selection
Components used in high-temperature PCBs must be rated for the expected operating temperature range. This includes passive components (resistors, capacitors, inductors) and active components (ICs, transistors, diodes). High-temperature components may use specialized packaging materials and construction techniques to ensure reliability.
Layout Optimization
When designing high-temperature PCBs, engineers should follow best practices for layout optimization, such as:
- Minimizing trace lengths and widths to reduce resistance and heat generation
- Providing adequate spacing between components and traces to improve heat dissipation
- Using thermal relief pads for components to minimize thermal stress
- Employing copper pours and planes to distribute heat evenly across the board
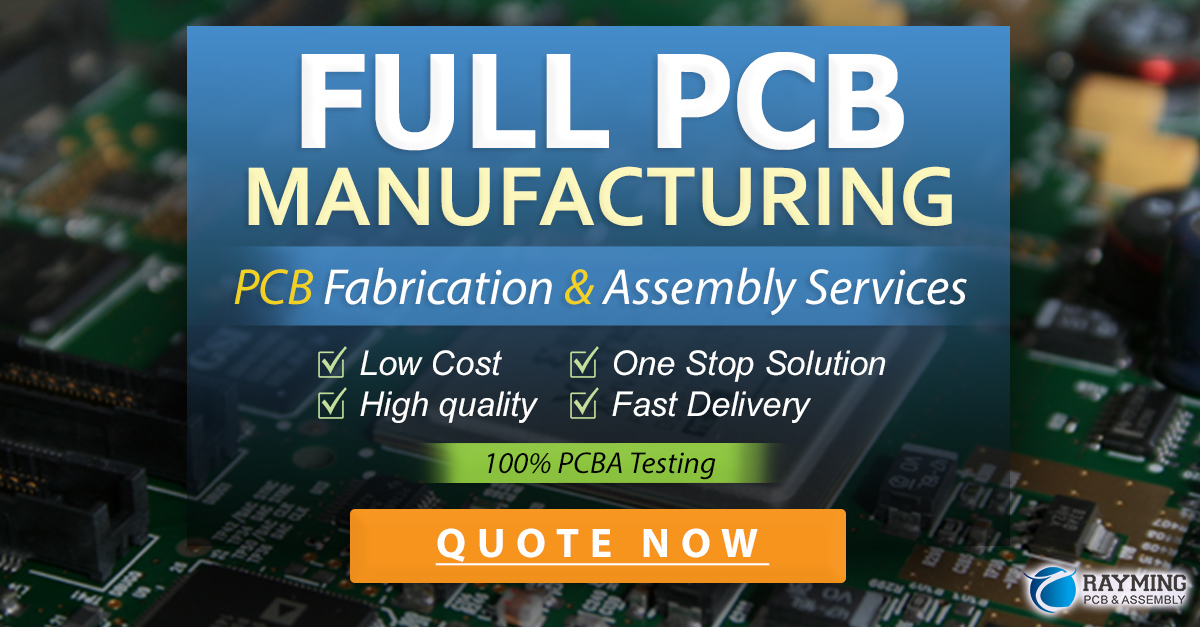
Manufacturing and Assembly of High-temperature PCBs
The manufacturing and assembly processes for high-temperature PCBs require specialized equipment and techniques to ensure the integrity of the materials and components.
PCB Fabrication
High-temperature PCBs are typically fabricated using multilayer lamination processes, with each layer bonded together using high-temperature adhesives. The drilling, plating, and etching processes must be optimized to minimize stress and maintain the integrity of the copper traces and vias.
Solder Paste and Reflow
Solder pastes used for high-temperature PCBs must have a higher melting point and better thermal stability than standard pastes. Some common high-temperature solder alloys include:
- Sn96.5Ag3.0Cu0.5 (SAC305)
- Sn95.5Ag3.8Cu0.7 (SAC387)
- Sn93.6Ag4.7Cu1.7 (SAC405)
The reflow process for high-temperature PCBs requires a carefully controlled temperature profile to ensure proper solder joint formation without damaging the components or substrate.
Inspection and Testing
After assembly, high-temperature PCBs must undergo rigorous inspection and testing to verify their functionality and reliability. Some common testing methods include:
- Thermal cycling
- Burn-in testing
- X-ray inspection
- Electrical testing (continuity, insulation resistance, etc.)
Challenges and Future Trends in High-temperature PCBs
As the demand for high-temperature electronics continues to grow, PCB manufacturers and designers face several challenges and opportunities.
Challenges
- Developing new materials with improved thermal stability and performance
- Optimizing manufacturing processes for high-temperature PCBs
- Ensuring the reliability and longevity of high-temperature components
Future Trends
- Adoption of advanced substrate materials (e.g., silicon carbide, gallium nitride)
- Integration of embedded components and 3D packaging technologies
- Development of self-monitoring and self-healing high-temperature PCBs
Frequently Asked Questions (FAQ)
- What is the maximum operating temperature for high-temperature PCBs?
-
The maximum operating temperature for high-temperature PCBs depends on the materials used. Polyimide and PTFE-based PCBs can operate up to 260°C, while ceramic substrates can withstand temperatures up to 500°C.
-
Can standard PCB components be used in high-temperature applications?
-
Standard PCB components are not suitable for high-temperature applications, as they may fail or degrade rapidly under extreme heat. High-temperature PCBs require specialized components rated for the expected operating temperature range.
-
How does the choice of substrate material affect the thermal performance of high-temperature PCBs?
-
The substrate material plays a crucial role in the thermal performance of high-temperature PCBs. Materials with higher thermal conductivity, such as ceramic (alumina), can dissipate heat more effectively, while materials like polyimide and PTFE provide better electrical insulation but have lower thermal conductivity.
-
What are the key considerations when designing high-temperature PCBs?
-
When designing high-temperature PCBs, engineers must consider factors such as thermal management, component selection, and layout optimization. Effective thermal management strategies, choosing appropriate high-temperature components, and optimizing the layout for heat dissipation are essential for ensuring reliable performance.
-
How are high-temperature PCBs tested for reliability?
- High-temperature PCBs undergo rigorous testing to verify their functionality and reliability. Common testing methods include thermal cycling, burn-in testing, X-ray inspection, and electrical testing. These tests help identify potential issues and ensure that the PCBs can withstand the expected operating conditions.
In conclusion, high-temperature PCBs are essential for applications that require reliable performance under extreme heat. By carefully selecting materials, designing for thermal management, and following best practices in manufacturing and assembly, engineers can create high-temperature PCBs that meet the demanding requirements of various industries. As technology advances, new materials and techniques will continue to push the boundaries of high-temperature electronics, enabling more advanced and reliable systems for the future.
Leave a Reply