Understanding the Basics of Pulse Width Modulation
At its core, Pulse Width Modulation is a method of controlling the power delivered to a load by rapidly switching a power source on and off. By varying the duration of the “on” time relative to the “off” time, PWM effectively adjusts the average power supplied to the load.
Key Components of a PWM Signal
A PWM signal consists of two main components:
-
Duty Cycle: The duty cycle represents the proportion of time the signal is in the “on” state during one period. It is typically expressed as a percentage, ranging from 0% (always off) to 100% (always on).
-
Frequency: The frequency of a PWM signal determines how often the signal repeats itself. It is measured in Hertz (Hz) and represents the number of cycles per second.
Duty Cycle | Description |
---|---|
0% | Signal is always off |
25% | Signal is on for 25% of the period |
50% | Signal is on for half of the period |
75% | Signal is on for 75% of the period |
100% | Signal is always on |
Benefits of Pulse Width Modulation
PWM offers several significant advantages over other power control methods:
1. Efficiency
PWM is highly efficient because the switching devices, such as transistors or MOSFETs, are either fully on or fully off. This minimizes power losses associated with the switching process, resulting in lower heat generation and improved overall system efficiency.
2. Precision Control
By adjusting the duty cycle of the PWM signal, you can achieve precise control over the average power delivered to the load. This allows for fine-tuning of parameters such as brightness, speed, or temperature, depending on the application.
3. Simplicity
Implementing PWM is relatively simple and requires minimal additional components. In most cases, a microcontroller or dedicated PWM controller can generate the necessary signals, making it a cost-effective solution for power control.
Applications of Pulse Width Modulation
PWM finds applications in a wide range of industries and domains, including:
1. LED Dimming
PWM is commonly used to control the brightness of LEDs. By varying the duty cycle of the PWM signal, you can adjust the perceived brightness of the LED. This technique is more efficient and provides a wider dimming range compared to traditional analog dimming methods.
2. Motor Speed Control
In motor control applications, PWM is employed to regulate the speed of DC motors. By adjusting the duty cycle, you can control the average voltage supplied to the motor, thereby changing its speed. PWM-based motor control is widely used in robotics, automotive systems, and industrial automation.
3. Temperature Control
PWM is utilized in temperature control systems, such as in 3D printers or soldering irons. By modulating the power supplied to the heating element using PWM, you can maintain a desired temperature setpoint with high precision.
4. Audio Amplification
In Class D audio amplifiers, PWM is used to convert analog audio signals into high-frequency PWM signals. These PWM signals are then filtered to reconstruct the original audio signal, resulting in high efficiency and reduced heat generation compared to traditional analog amplifiers.
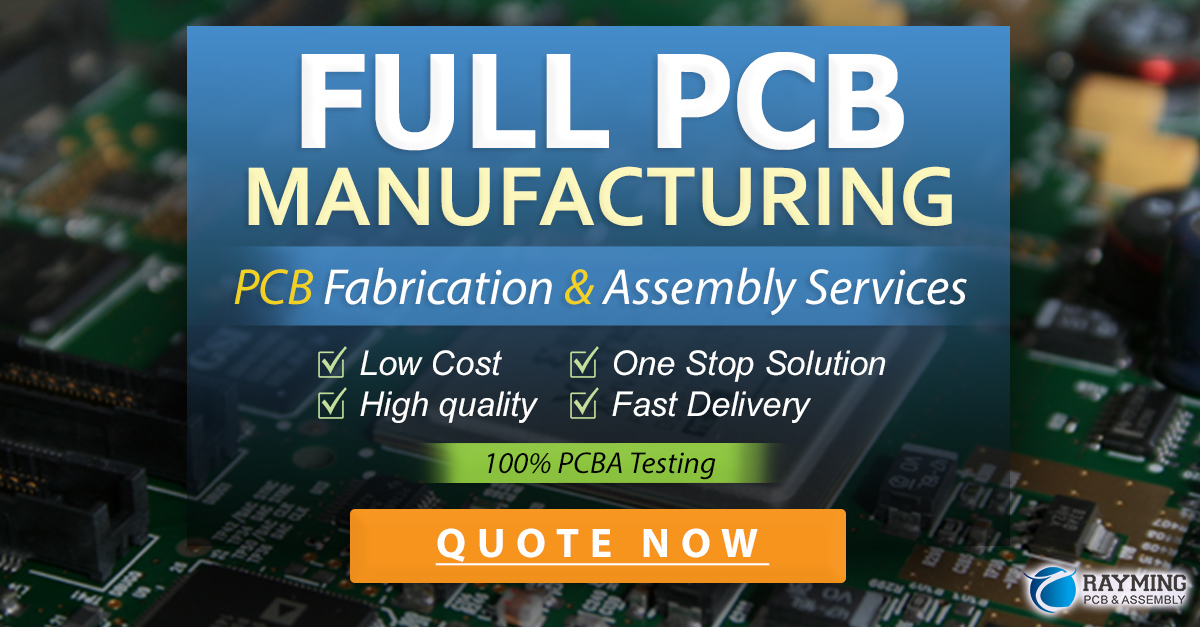
Implementing Pulse Width Modulation
To implement PWM in your projects, you can follow these general steps:
- Select a suitable PWM controller or microcontroller with PWM capabilities.
- Configure the PWM frequency and resolution based on your application requirements.
- Determine the desired duty cycle for your PWM signal.
- Generate the PWM signal using the chosen controller or microcontroller.
- Connect the PWM signal to the load or additional circuitry as needed.
- Adjust the duty cycle dynamically to control the power delivered to the load.
Here’s an example code snippet in Arduino to generate a PWM signal:
const int pwmPin = 9; // PWM output pin
const int pwmFrequency = 1000; // PWM frequency in Hz
const int pwmResolution = 8; // PWM resolution in bits
void setup() {
pinMode(pwmPin, OUTPUT);
analogWriteFrequency(pwmPin, pwmFrequency);
analogWriteResolution(pwmResolution);
}
void loop() {
// Set the duty cycle (0-255 for 8-bit resolution)
analogWrite(pwmPin, 128); // 50% duty cycle
delay(1000);
analogWrite(pwmPin, 64); // 25% duty cycle
delay(1000);
analogWrite(pwmPin, 192); // 75% duty cycle
delay(1000);
}
Advantages and Disadvantages of PWM
While PWM offers numerous benefits, it’s essential to consider both its advantages and disadvantages when deciding whether to use it in your application.
Advantages
- Efficient power delivery
- Precise control over power output
- Simple implementation
- Wide range of applications
- Cost-effective solution
Disadvantages
- Electromagnetic interference (EMI) due to rapid switching
- Audible noise in some applications (e.g., high-frequency PWM in motors)
- Limited power handling capacity of switching devices
- Requires additional filtering for smooth output in certain cases
Frequently Asked Questions (FAQ)
1. What is the difference between PWM and analog control?
PWM is a digital control technique that uses rapid switching to control power, while analog control uses continuous voltage levels. PWM offers better efficiency and precision compared to analog control.
2. Can PWM be used with AC loads?
PWM is primarily used with DC loads. However, it can be used with AC loads in certain cases, such as in inverters or power converters that convert DC to AC using PWM techniques.
3. What factors determine the choice of PWM frequency?
The choice of PWM frequency depends on the application requirements, such as the response time of the load, the desired smoothness of the output, and the switching capabilities of the devices used. Higher frequencies generally result in smoother output but may increase switching losses.
4. How does PWM affect the lifespan of components?
PWM can impact the lifespan of components due to the repeated switching, which can cause thermal stress and mechanical wear. However, proper design and selection of components with appropriate ratings can mitigate these effects and ensure reliable operation.
5. Can PWM be used for communication purposes?
Yes, PWM can be used for communication in certain applications. For example, in some remote control protocols, PWM signals are used to encode and transmit data between the transmitter and receiver.
Conclusion
Pulse Width Modulation is a versatile and efficient technique for controlling power in a wide range of applications. By understanding the principles behind PWM and its benefits, you can harness its potential to achieve precise control, improve efficiency, and simplify your designs.
Whether you’re working on LED lighting, motor control, temperature regulation, or audio amplification, PWM provides a powerful tool to optimize your systems. By following best practices and considering the specific requirements of your application, you can successfully implement PWM and unlock its full potential.
As technology continues to advance, the applications of PWM are likely to expand further, enabling even more innovative solutions across various industries. By staying up-to-date with the latest developments and techniques in PWM, you can stay ahead of the curve and create cutting-edge projects that push the boundaries of what’s possible.
Leave a Reply