Introduction to Vibration Sensors
Vibration sensors are essential components in various industries, enabling the detection and measurement of vibrations in machines, structures, and equipment. These sensors play a crucial role in condition monitoring, predictive maintenance, and ensuring the smooth operation of critical systems. In this comprehensive guide, we will explore the different types of vibration sensors, their working principles, and their diverse applications across industries.
How Do Vibration Sensors Work?
Vibration sensors convert mechanical vibrations into electrical signals that can be processed and analyzed. They typically consist of a sensing element, such as a piezoelectric crystal or a microelectromechanical system (MEMS), which generates an electrical output proportional to the vibration amplitude and frequency. The generated signal is then conditioned, amplified, and transmitted to a data acquisition system or control unit for further analysis and action.
Types of Vibration Sensors
There are several types of vibration sensors available, each with its own unique characteristics and advantages. Let’s explore the most common types:
1. Piezoelectric Accelerometers
Piezoelectric accelerometers are widely used for vibration measurement due to their high sensitivity, wide frequency range, and durability. They utilize the piezoelectric effect, where certain materials generate an electrical charge when subjected to mechanical stress. The main components of a piezoelectric accelerometer include:
- Piezoelectric sensing element (e.g., quartz, ceramic, or polymer)
- Seismic mass
- Housing and mounting base
When vibrations occur, the seismic mass exerts a force on the piezoelectric element, generating an electrical charge proportional to the acceleration. Piezoelectric accelerometers are suitable for a wide range of applications, including:
- Condition monitoring of rotating machinery
- Structural health monitoring
- Aerospace and automotive testing
- Seismic monitoring
2. MEMS Accelerometers
MEMS (Micro-Electro-Mechanical Systems) accelerometers are miniaturized sensors that leverage advanced semiconductor manufacturing techniques. They consist of a small proof mass suspended by springs within a silicon structure. When subjected to vibrations, the proof mass displaces, causing a change in capacitance that is proportional to the acceleration.
MEMS accelerometers offer several advantages, including:
- Small size and low weight
- Low power consumption
- High shock resistance
- Cost-effectiveness
These sensors are commonly used in:
- Consumer electronics (e.g., smartphones, gaming controllers)
- Automotive applications (e.g., airbag deployment, stability control)
- Wearable devices and IoT sensors
3. Velocity Sensors
Velocity sensors, also known as velometers or geophones, measure the velocity of vibrations rather than acceleration. They consist of a coil suspended by springs within a magnetic field. When vibrations occur, the coil moves relative to the magnetic field, inducing an electrical voltage proportional to the velocity.
Velocity sensors are particularly useful for low-frequency vibration measurements and are commonly used in:
- Seismic exploration and geophysical surveys
- Structural health monitoring of buildings and bridges
- Vibration isolation systems
4. Eddy Current Proximity Probes
Eddy current proximity probes are non-contact sensors that measure the displacement and vibration of conductive surfaces. They operate on the principle of electromagnetic induction, where a high-frequency alternating current is passed through a coil, creating a magnetic field. When a conductive surface is brought close to the probe, eddy currents are induced in the surface, altering the coil’s impedance. The change in impedance is proportional to the distance between the probe and the surface.
Eddy current proximity probes are commonly used in:
- Turbomachinery monitoring (e.g., turbines, compressors)
- Shaft vibration and alignment measurements
- Bearing wear monitoring
5. Laser Vibrometers
Laser vibrometers are non-contact sensors that use laser technology to measure vibrations. They work on the principle of laser Doppler vibrometry, where a laser beam is directed at the vibrating surface, and the scattered light is analyzed to determine the vibration velocity and displacement.
Laser vibrometers offer several advantages, including:
- High spatial resolution
- Non-contact measurement
- Ability to measure vibrations on small or inaccessible surfaces
They are commonly used in:
- Automotive and aerospace testing
- Structural dynamics analysis
- Non-destructive testing and quality control
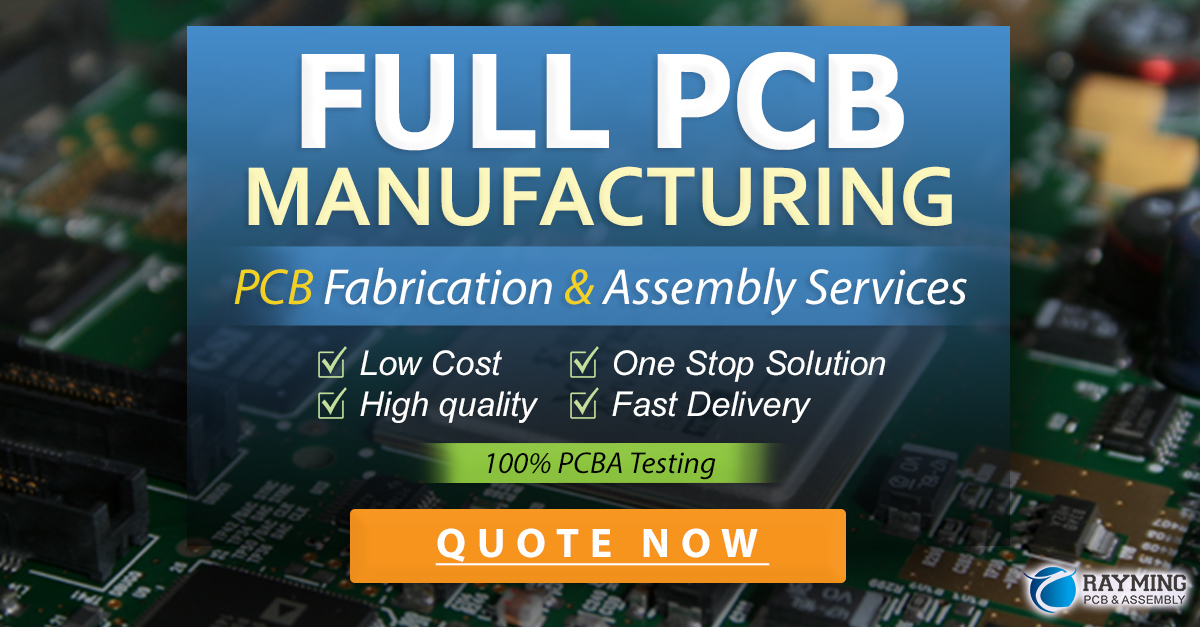
Vibration Sensor Selection Criteria
When selecting a vibration sensor for a specific application, several factors should be considered:
-
Frequency Range: The sensor should have a frequency range that covers the expected vibration frequencies of the application.
-
Sensitivity: The sensor’s sensitivity should be appropriate for the expected vibration amplitudes and the desired measurement resolution.
-
Environmental Conditions: Consider the operating temperature range, humidity, and chemical exposure that the sensor will be subjected to.
-
Mounting and Installation: Evaluate the sensor’s mounting options and ease of installation in the target environment.
-
Signal Conditioning and Output: Ensure that the sensor’s output is compatible with the data acquisition system or control unit.
-
Cost and Maintenance: Consider the initial cost, long-term maintenance requirements, and overall cost of ownership.
Sensor Type | Frequency Range | Sensitivity | Pros | Cons |
---|---|---|---|---|
Piezoelectric Accelerometer | Wide (up to 10 kHz) | High | High sensitivity, wide frequency range, durable | Requires charge amplifier, sensitive to cable noise |
MEMS Accelerometer | Moderate (up to 1 kHz) | Moderate | Small size, low power, cost-effective | Limited frequency range, lower sensitivity |
Velocity Sensor | Low (up to 100 Hz) | High | Suitable for low-frequency measurements | Limited frequency range, sensitive to magnetic interference |
Eddy Current Proximity Probe | Moderate (up to 1 kHz) | High | Non-contact, suitable for harsh environments | Limited to conductive surfaces, short measurement range |
Laser Vibrometer | Wide (up to 100 kHz) | High | Non-contact, high spatial resolution | Expensive, requires line of sight to the target |
Applications of Vibration Sensors
Vibration sensors find applications across various industries, contributing to improved safety, reliability, and efficiency. Some key applications include:
1. Condition Monitoring and Predictive Maintenance
Vibration sensors are extensively used in condition monitoring and predictive maintenance of industrial machinery, such as motors, pumps, compressors, and turbines. By continuously monitoring vibration levels and patterns, potential faults and degradation can be detected early, allowing for timely maintenance interventions. This approach helps prevent unexpected breakdowns, reduces downtime, and extends the lifespan of critical assets.
2. Structural Health Monitoring
Vibration sensors play a vital role in monitoring the structural integrity of buildings, bridges, and other infrastructure. They can detect changes in vibration characteristics that may indicate structural damage, fatigue, or deterioration. By monitoring vibrations over time, engineers can assess the health of structures, plan maintenance activities, and ensure public safety.
3. Automotive and Aerospace Testing
In the automotive and aerospace industries, vibration sensors are used for testing and validation of components and systems. They help evaluate the performance, durability, and reliability of vehicles and aircraft under various operating conditions. Vibration sensors are used in:
- Noise, vibration, and harshness (NVH) testing
- Fatigue and durability testing
- Modal analysis and structural dynamics
4. Consumer Electronics and Wearables
MEMS accelerometers have revolutionized the consumer electronics industry by enabling motion sensing and vibration detection in smartphones, tablets, gaming controllers, and wearable devices. These sensors enable features such as:
- Device orientation detection
- Activity tracking and step counting
- Gesture recognition and motion control
5. Seismic Monitoring and Geophysical Surveys
Vibration sensors, particularly velocity sensors and geophones, are used in seismic monitoring and geophysical surveys. They help detect and measure seismic waves generated by earthquakes, explosions, or artificial sources. The data collected by these sensors is used for:
- Earthquake early warning systems
- Oil and gas exploration
- Geotechnical engineering and site characterization
Frequently Asked Questions (FAQ)
1. What is the difference between an accelerometer and a velocity sensor?
Accelerometers measure the acceleration of vibrations, while velocity sensors measure the velocity of vibrations. Accelerometers are suitable for a wide frequency range and are commonly used for condition monitoring and structural health monitoring. Velocity sensors, on the other hand, are more sensitive to low-frequency vibrations and are often used in seismic monitoring and geophysical surveys.
2. Can vibration sensors be used in harsh environments?
Yes, certain types of vibration sensors are designed to withstand harsh environments. For example, piezoelectric accelerometers with hermetically sealed housings can operate in high-temperature and corrosive environments. Eddy current proximity probes are also suitable for harsh conditions as they are non-contact sensors and can withstand high temperatures and pressures.
3. How do I choose the right vibration sensor for my application?
When selecting a vibration sensor, consider factors such as the frequency range of interest, sensitivity requirements, environmental conditions, mounting options, and compatibility with your data acquisition system. Evaluate the pros and cons of different sensor types and consult with sensor manufacturers or application engineers to determine the most suitable sensor for your specific needs.
4. How often should vibration sensors be calibrated?
The calibration frequency of vibration sensors depends on the application, environmental conditions, and the criticality of the measurements. In general, it is recommended to calibrate sensors annually or as per the manufacturer’s guidelines. However, in critical applications or harsh environments, more frequent calibration may be necessary to ensure accurate and reliable measurements.
5. Can vibration sensors be integrated with IoT platforms?
Yes, vibration sensors can be integrated with IoT (Internet of Things) platforms for remote monitoring and data analytics. Many modern vibration sensors come with built-in wireless connectivity options, such as Wi-Fi, Bluetooth, or LoRaWAN, enabling seamless integration with IoT networks. By combining vibration data with other sensor data and applying advanced analytics, organizations can gain valuable insights into the health and performance of their assets and make data-driven decisions.
Conclusion
Vibration sensors are indispensable tools for monitoring and analyzing vibrations in various industries and applications. From condition monitoring and predictive maintenance to structural health monitoring and consumer electronics, these sensors enable organizations to ensure the safety, reliability, and efficiency of their assets and products.
By understanding the different types of vibration sensors, their working principles, and selection criteria, engineers and technicians can choose the most suitable sensor for their specific requirements. As technology advances, vibration sensors continue to evolve, offering improved performance, miniaturization, and integration with IoT platforms, opening up new possibilities for vibration monitoring and analysis.
Investing in the right vibration sensors and leveraging their capabilities can lead to significant benefits, including reduced downtime, improved safety, and optimized maintenance strategies. As industries strive for increased efficiency and reliability, the role of vibration sensors in driving these advancements will only continue to grow.
Leave a Reply