Introduction to PCB DFM
PCB DFM (Design for Manufacturability) is a crucial aspect of the printed circuit board (PCB) design and fabrication process. It involves designing PCBs in a way that optimizes their manufacturability, reliability, and cost-effectiveness. By incorporating DFM principles early in the design phase, engineers can avoid potential issues during fabrication and assembly, ultimately leading to a more efficient and successful PCB production process.
In this article, we will explore nine key advantages of PCB fabrication assisted by DFM. We will delve into how DFM can enhance the overall quality of PCBs, reduce manufacturing costs, and improve time-to-market. Additionally, we will discuss the role of DFM in ensuring compliance with industry standards and facilitating effective communication between design and manufacturing teams.
Advantage 1: Improved PCB Quality and Reliability
One of the primary benefits of incorporating DFM principles into PCB fabrication is the significant improvement in overall PCB quality and reliability. By adhering to DFM guidelines, designers can minimize the risk of manufacturing defects and ensure that the PCB performs as intended.
Reducing Manufacturing Defects
DFM helps identify and address potential manufacturing issues early in the design phase. This proactive approach allows designers to make necessary adjustments before the PCB enters the fabrication stage, thereby reducing the likelihood of defects such as:
- Insufficient copper thickness
- Incorrect hole sizes
- Inadequate spacing between components
- Improper trace width and spacing
By catching and correcting these issues early, DFM significantly reduces the occurrence of manufacturing defects, resulting in higher-quality PCBs.
Enhancing PCB Reliability
In addition to reducing defects, DFM also contributes to the overall reliability of PCBs. By considering factors such as component placement, thermal management, and signal integrity during the design phase, engineers can create PCBs that are more resilient and less prone to failures.
DFM guidelines help ensure that components are placed in optimal locations, minimizing the risk of thermal stress and signal interference. Additionally, DFM promotes the use of robust materials and manufacturing processes, further enhancing the durability and longevity of the PCBs.
Advantage 2: Cost Reduction and Optimization
Another significant advantage of PCB fabrication assisted by DFM is the potential for cost reduction and optimization. By incorporating DFM principles, designers can streamline the manufacturing process, minimize material waste, and reduce the need for costly rework or repairs.
Streamlining the Manufacturing Process
DFM helps simplify the PCB manufacturing process by promoting design choices that are compatible with standard fabrication techniques. This includes selecting appropriate materials, component packages, and manufacturing tolerances.
By designing PCBs that are easier to manufacture, DFM reduces the complexity of the fabrication process, leading to shorter production times and lower labor costs. Additionally, streamlined manufacturing processes are less prone to errors and delays, further contributing to cost savings.
Minimizing Material Waste
DFM guidelines also emphasize the efficient use of materials, helping to minimize waste and reduce overall material costs. This can be achieved through various strategies, such as:
- Optimizing panel utilization
- Minimizing the use of expensive materials
- Selecting cost-effective component packages
- Reducing the number of layers in the PCB stack-up
By making informed design choices that prioritize material efficiency, engineers can significantly reduce the cost of PCB fabrication without compromising quality or functionality.
Reducing Rework and Repair Costs
Incorporating DFM principles into PCB design can also help minimize the need for costly rework or repairs. By identifying and addressing potential issues early in the design phase, DFM reduces the likelihood of manufacturing defects that would require additional time and resources to correct.
Furthermore, DFM promotes the use of robust design practices that enhance the overall reliability of PCBs. This, in turn, reduces the risk of field failures and the associated costs of repair or replacement.
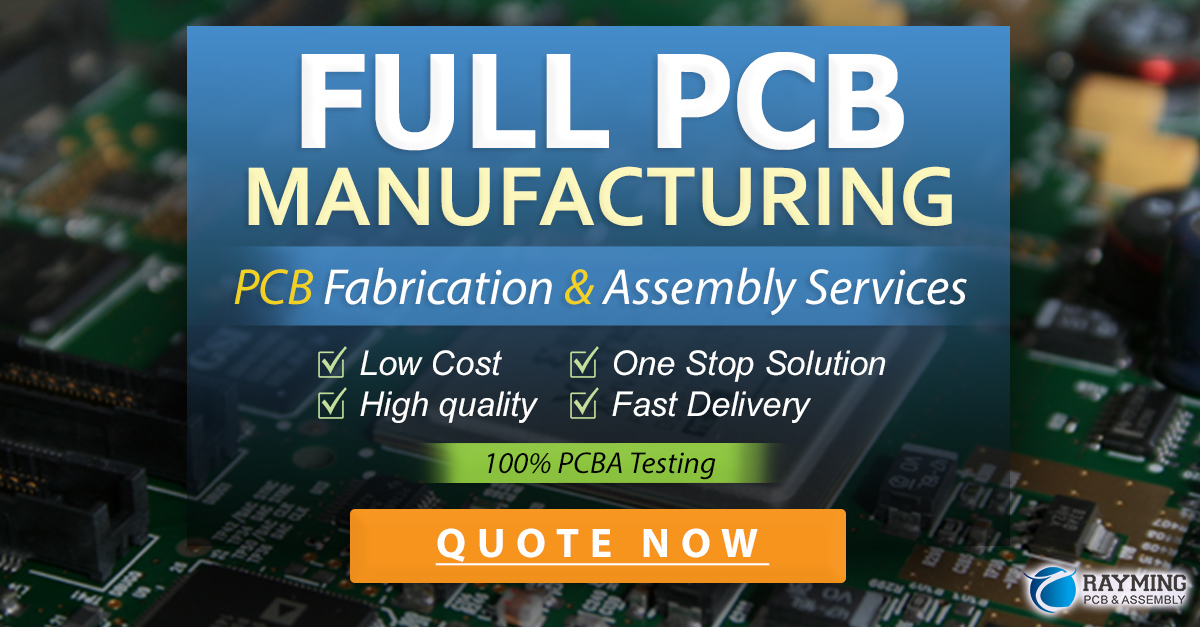
Advantage 3: Faster Time-to-Market
PCB fabrication assisted by DFM can significantly accelerate the time-to-market for electronic products. By streamlining the design and manufacturing processes, DFM helps companies bring their products to market faster, gaining a competitive edge in the industry.
Efficient Design Iteration
DFM facilitates efficient design iteration by providing designers with clear guidelines and best practices. This allows engineers to quickly identify and resolve potential issues, reducing the need for multiple design revisions.
Moreover, DFM-compliant designs are more likely to pass the manufacturability review process on the first attempt, eliminating the need for additional design iterations. This streamlined approach saves valuable time and resources, enabling faster product development cycles.
Reduced Manufacturing Lead Time
By designing PCBs that are optimized for manufacturability, DFM helps reduce the overall manufacturing lead time. DFM-compliant designs are easier to fabricate and assemble, requiring fewer specialized processes or materials.
This simplification of the manufacturing process allows PCB fabrication facilities to produce boards more quickly and efficiently. As a result, companies can receive their PCBs faster, accelerating the overall product development timeline.
Simultaneous Design and Manufacturing Preparation
DFM also enables concurrent design and manufacturing preparation, further reducing time-to-market. By incorporating manufacturability considerations early in the design phase, engineers can ensure that their designs are compatible with the chosen fabrication processes and equipment.
This parallel approach allows manufacturing teams to begin preparing for production while the design is still being finalized. By the time the design is complete, the manufacturing process is already optimized, enabling a seamless transition from design to production.
Advantage 4: Enhanced Communication Between Design and Manufacturing Teams
PCB fabrication assisted by DFM promotes effective communication between design and manufacturing teams. By establishing a common language and understanding of manufacturability requirements, DFM facilitates collaboration and reduces the risk of miscommunication.
Establishing a Common Language
DFM provides a set of standardized guidelines and best practices that both design and manufacturing teams can refer to. This shared knowledge base creates a common language, ensuring that everyone involved in the PCB fabrication process is on the same page.
By using DFM terminology and concepts, designers can effectively communicate their intent to the manufacturing team, while manufacturers can provide clear feedback and suggestions based on their expertise. This mutual understanding streamlines the communication process and minimizes the potential for confusion or misinterpretation.
Collaborative Problem-Solving
DFM also encourages collaborative problem-solving between design and manufacturing teams. When designers incorporate DFM principles into their work, they are more likely to engage with the manufacturing team early in the design process to discuss potential challenges and solutions.
This proactive collaboration allows both teams to leverage their respective knowledge and expertise to identify and address manufacturability issues before they become significant problems. By working together, designers and manufacturers can develop innovative solutions that optimize the PCB fabrication process.
Continuous Improvement
PCB fabrication assisted by DFM promotes a culture of continuous improvement. By regularly reviewing and analyzing the performance of DFM-compliant designs, design and manufacturing teams can identify areas for further optimization.
This ongoing feedback loop allows teams to refine their DFM guidelines and best practices based on real-world experience. As a result, the PCB fabrication process becomes increasingly efficient and effective over time, benefiting both the company and its customers.
Advantage 5: Compliance with Industry Standards
DFM plays a crucial role in ensuring that PCBs comply with relevant industry standards and regulations. By incorporating DFM principles, designers can create boards that meet the stringent requirements of various industries, such as automotive, aerospace, and medical devices.
Designing for Specific Industry Standards
DFM guidelines often incorporate specific industry standards, such as IPC (Association Connecting Electronics Industries) standards for PCB design and manufacturing. These standards provide detailed requirements for various aspects of PCB fabrication, including:
- Material selection
- Conductor width and spacing
- Hole sizes and pad dimensions
- Solder mask and silkscreen specifications
By adhering to these standards, designers can ensure that their PCBs are compatible with industry-accepted manufacturing processes and can withstand the rigors of their intended application.
Meeting Regulatory Requirements
In addition to industry standards, DFM also helps PCBs comply with regulatory requirements. Many industries have specific regulations governing the design and manufacture of electronic products, such as the FDA (Food and Drug Administration) regulations for medical devices or the FAA (Federal Aviation Administration) regulations for aerospace applications.
DFM guidelines take these regulatory requirements into account, providing designers with the necessary information to create PCBs that meet the applicable safety, performance, and reliability standards. By incorporating DFM principles, companies can streamline the regulatory compliance process and avoid costly delays or penalties.
Advantage 6: Improved Product Performance and Functionality
PCB fabrication assisted by DFM not only enhances the manufacturability and reliability of PCBs but also contributes to improved product performance and functionality. By considering factors such as signal integrity, thermal management, and electromagnetic compatibility (EMC) during the design phase, engineers can create PCBs that optimize the overall performance of the final product.
Signal Integrity Optimization
DFM guidelines include best practices for maintaining signal integrity in PCB designs. This involves selecting appropriate materials, controlling impedance, and minimizing signal reflections and crosstalk.
By incorporating these signal integrity considerations into the design process, engineers can ensure that the PCB can handle high-speed signals without compromising performance. This is particularly important in applications such as high-frequency communication systems, where signal quality is critical.
Thermal Management
DFM also addresses thermal management concerns in PCB design. By considering factors such as component placement, copper balance, and thermal vias, designers can create PCBs that effectively dissipate heat and maintain optimal operating temperatures.
Proper thermal management is essential for ensuring the reliability and longevity of electronic products. By incorporating DFM principles, designers can minimize the risk of thermal-related failures and enhance the overall performance of the final product.
EMC Compliance
Electromagnetic compatibility (EMC) is another critical consideration in PCB design. DFM guidelines provide best practices for minimizing electromagnetic interference (EMI) and ensuring that PCBs comply with relevant EMC standards.
By incorporating EMC considerations early in the design phase, engineers can avoid costly redesigns or additional shielding measures later in the product development cycle. This proactive approach helps ensure that the final product meets the necessary EMC requirements and performs reliably in its intended environment.
Advantage 7: Flexibility in PCB Manufacturing
PCB fabrication assisted by DFM offers greater flexibility in the manufacturing process. By designing PCBs that are compatible with a range of manufacturing capabilities and equipment, companies can take advantage of the most suitable fabrication options for their specific needs.
Compatibility with Multiple Manufacturers
DFM guidelines help ensure that PCB designs are compatible with the capabilities of multiple manufacturers. By adhering to industry-standard design rules and best practices, designers can create PCBs that can be fabricated by a variety of PCB manufacturing facilities.
This compatibility provides companies with greater flexibility in selecting a manufacturing partner. They can choose a fabricator based on factors such as cost, lead time, and expertise, without being limited by the specific capabilities of a single manufacturer.
Adaptability to Different Manufacturing Technologies
DFM also enables PCB designs to be adaptable to different manufacturing technologies. As PCB fabrication techniques continue to evolve, DFM guidelines are updated to incorporate new processes and materials.
By staying current with DFM best practices, designers can create PCBs that are compatible with emerging manufacturing technologies. This adaptability allows companies to take advantage of the latest advancements in PCB fabrication, improving product performance and cost-effectiveness.
Advantage 8: Reduced Environmental Impact
PCB fabrication assisted by DFM can help reduce the environmental impact of the manufacturing process. By promoting the efficient use of materials, minimizing waste, and selecting eco-friendly substances, DFM contributes to a more sustainable PCB production process.
Material Optimization and Waste Reduction
As mentioned earlier, DFM guidelines emphasize the efficient use of materials in PCB design. By optimizing panel utilization, minimizing the use of expensive or scarce materials, and reducing the number of layers in the PCB stack-up, designers can significantly reduce material waste.
This material optimization not only leads to cost savings but also minimizes the environmental impact of PCB fabrication. By using fewer resources and generating less waste, companies can reduce their carbon footprint and contribute to a more sustainable manufacturing process.
Eco-Friendly Material Selection
DFM also promotes the selection of eco-friendly materials in PCB design. This includes the use of lead-free solders, halogen-free laminates, and other environmentally friendly substances.
By incorporating these materials into PCB designs, companies can ensure that their products comply with environmental regulations, such as the Restriction of Hazardous Substances (RoHS) directive. Additionally, the use of eco-friendly materials helps minimize the release of harmful substances into the environment during the manufacturing process and at the end of the product’s life cycle.
Advantage 9: Continuous Improvement and Innovation
PCB fabrication assisted by DFM fosters a culture of continuous improvement and innovation. By regularly reviewing and updating DFM guidelines based on new technologies, materials, and best practices, companies can stay at the forefront of PCB design and manufacturing.
Incorporating New Technologies and Materials
DFM guidelines are not static; they evolve to incorporate new technologies and materials that can enhance PCB performance, reliability, and manufacturability. As researchers and engineers develop new techniques and substances, DFM best practices are updated to reflect these advancements.
By staying current with the latest DFM guidelines, designers can leverage these innovations to create cutting-edge PCBs that meet the ever-increasing demands of modern electronic products. This continuous integration of new technologies and materials helps companies maintain a competitive edge in the market.
Encouraging Innovation and Experimentation
DFM also encourages innovation and experimentation in PCB design. By providing a framework for designing manufacturable PCBs, DFM allows engineers to focus on pushing the boundaries of what is possible in terms of functionality and performance.
With the assurance that their designs will be manufacturable, designers can explore new concepts and ideas, knowing that they have the support of a robust DFM process. This freedom to innovate can lead to Breakthrough designs that revolutionize the electronics industry.
Frequently Asked Questions (FAQ)
- What is PCB DFM, and why is it important?
-
PCB DFM (Design for Manufacturability) is a set of guidelines and best practices that help optimize PCB designs for manufacturing. It is important because it ensures that PCBs can be fabricated efficiently, reliably, and cost-effectively, while meeting the required performance and quality standards.
-
How does DFM help reduce manufacturing costs?
-
DFM helps reduce manufacturing costs by streamlining the fabrication process, minimizing material waste, and reducing the need for rework or repairs. By designing PCBs that are compatible with standard manufacturing processes and equipment, DFM enables faster, more efficient production, leading to lower overall costs.
-
Can DFM improve the reliability and performance of PCBs?
-
Yes, DFM can significantly improve the reliability and performance of PCBs. By considering factors such as signal integrity, thermal management, and EMC compliance during the design phase, DFM helps create PCBs that are optimized for their intended application. This results in better-performing, more reliable products.
-
How does DFM contribute to faster time-to-market?
-
DFM contributes to faster time-to-market by streamlining the design and manufacturing processes. DFM-compliant designs require fewer revisions and are easier to manufacture, reducing lead times and enabling concurrent design and manufacturing preparation. This allows companies to bring their products to market more quickly.
-
Is DFM only relevant for large-scale PCB production?
- No, DFM is relevant for PCB production at any scale. Whether a company is producing a small batch of prototypes or a large volume of production boards, incorporating DFM principles can help optimize the fabrication process, improve quality, and reduce costs. DFM is beneficial for any company that wants to create high-quality, reliable PCBs efficiently and cost-effectively.
Conclusion
PCB fabrication assisted by DFM offers numerous advantages that can significantly enhance the quality, reliability, and cost-effectiveness of electronic products. By incorporating DFM principles early in the design phase, companies can streamline the manufacturing process, reduce costs, and improve time-to-market.
DFM also promotes effective communication between design and manufacturing teams, ensures compliance with industry standards and regulations, and contributes to improved product performance and functionality. Additionally, DFM offers greater flexibility in PCB manufacturing, reduces environmental impact, and fosters a culture of continuous improvement and innovation.
As the electronics industry continues to evolve, the importance of DFM in PCB fabrication will only continue to grow. By embracing DFM best practices and staying current with the latest guidelines and technologies, companies can position themselves for success in an increasingly competitive market.
Leave a Reply