Introduction to Decoupling
In the world of electronic circuit design, power supply noise is a common problem that can lead to various issues, such as signal integrity degradation, electromagnetic interference (EMI), and even system malfunctions. To mitigate these problems, designers employ a technique called decoupling, which involves strategically placing capacitors near power pins of integrated circuits (ICs) to provide a stable and clean power supply. In this article, we will delve into the importance of decoupling, the types of decoupling capacitors, and best practices for implementing decoupling in PCB design.
Understanding Power Supply Noise
Sources of Power Supply Noise
Power supply noise can originate from various sources, both internal and external to the PCB. Some common sources include:
- Switching noise from voltage regulators
- Transient currents drawn by digital ICs during switching
- Ripple voltage from AC-to-DC converters
- Electromagnetic interference (EMI) from nearby electronic devices
Effects of Power Supply Noise
Power supply noise can have detrimental effects on the performance and reliability of electronic systems. Some of these effects include:
- Signal integrity degradation
- Increased jitter in clock signals
- False triggering of logic circuits
- Electromagnetic compatibility (EMC) issues
- Reduced signal-to-noise ratio (SNR) in analog circuits
Decoupling Capacitors
Types of Decoupling Capacitors
Decoupling capacitors come in various types, each with its own characteristics and applications. The most common types include:
- Ceramic capacitors
- High-frequency decoupling
- Low equivalent series resistance (ESR)
-
Available in small package sizes
-
Tantalum capacitors
- Medium-frequency decoupling
- Higher capacitance density than ceramic capacitors
-
Suitable for bulk decoupling
-
Electrolytic capacitors
- Low-frequency decoupling
- High capacitance values
- Used for bulk decoupling and voltage regulation
Selecting the Right Decoupling Capacitor
When choosing decoupling capacitors, consider the following factors:
- Frequency range of the noise to be suppressed
- Required capacitance value
- Equivalent series resistance (ESR) and equivalent series inductance (ESL)
- Voltage rating and temperature stability
- Package size and availability
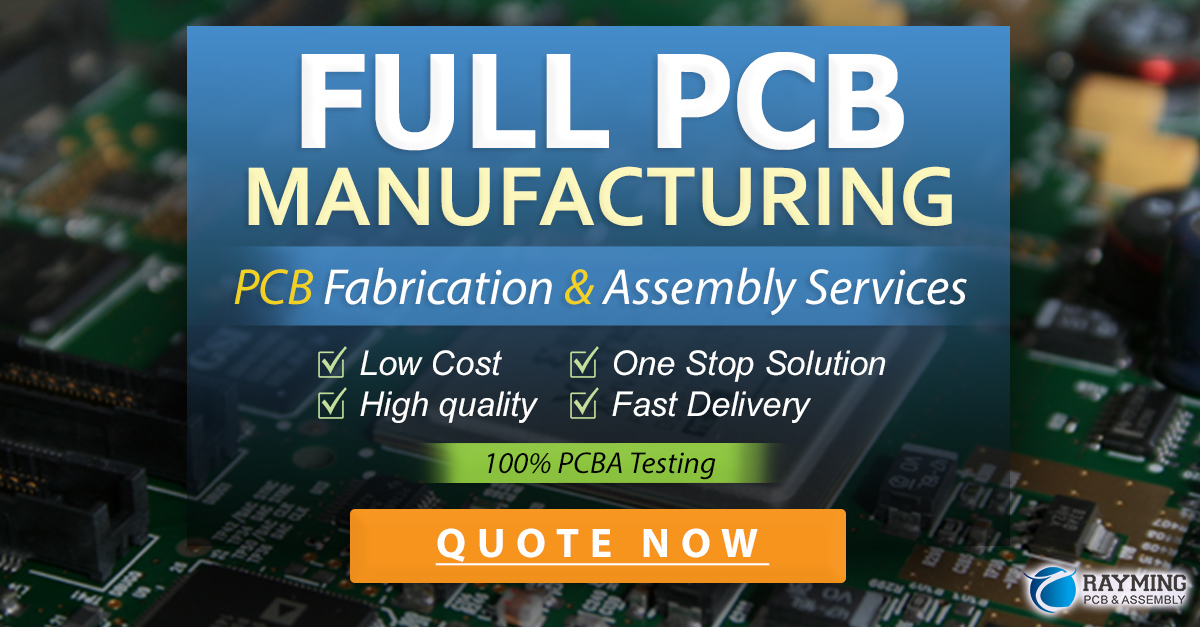
Decoupling Strategies in PCB Design
Placement of Decoupling Capacitors
Proper placement of decoupling capacitors is crucial for effective noise suppression. Follow these guidelines:
- Place decoupling capacitors as close as possible to the power pins of ICs
- Use multiple decoupling capacitors in parallel to reduce ESR and ESL
- Minimize the loop area between the capacitor and the IC power pin
- Use a combination of high-frequency and bulk decoupling capacitors
Power Plane Decoupling
Power planes in multi-layer PCBs can act as inherent decoupling capacitors. To optimize power plane decoupling:
- Use thin dielectric materials between power and ground planes
- Minimize the distance between power and ground planes
- Use multiple power planes for different voltage levels
- Avoid splitting power planes unnecessarily
Decoupling Capacitor Mounting
Proper mounting of decoupling capacitors is essential for optimal performance. Consider these factors:
- Use surface-mount technology (SMT) capacitors for better high-frequency performance
- Orient capacitors to minimize loop inductance
- Use via-in-pad or via-near-pad techniques for better grounding
- Avoid using shared vias for multiple capacitors
Simulation and Analysis
Power Integrity Simulation
Power integrity simulation tools can help optimize decoupling strategies by:
- Predicting resonance frequencies and impedance peaks
- Identifying areas of high current density and voltage drop
- Evaluating the effectiveness of decoupling capacitor placement
- Analyzing the impact of via placement and plane stackup
Electromagnetic Compatibility (EMC) Analysis
EMC analysis tools can help ensure that the PCB design meets electromagnetic compatibility standards by:
- Predicting electromagnetic emissions from the PCB
- Identifying potential EMI coupling paths
- Evaluating the effectiveness of shielding and grounding techniques
- Assessing the impact of decoupling on EMC performance
Case Studies and Examples
Example 1: High-Speed Digital PCB
In a high-speed digital PCB design, decoupling is critical for maintaining signal integrity. Consider the following:
- Use a combination of ceramic and tantalum capacitors for broadband decoupling
- Place decoupling capacitors close to the power pins of high-speed ICs, such as FPGAs and processors
- Use multiple power planes for different voltage levels, with thin dielectrics between them
- Simulate the power delivery network to optimize Decoupling Capacitor Values and placement
Example 2: Mixed-Signal PCB
In a mixed-signal PCB design, decoupling is essential for minimizing noise coupling between analog and digital sections. Consider the following:
- Use separate power planes for analog and digital sections
- Place decoupling capacitors close to the power pins of both analog and digital ICs
- Use ferrite beads or inductors to isolate analog and digital power supplies
- Simulate the power delivery network to ensure adequate decoupling and isolation
Best Practices and Guidelines
Decoupling Capacitor Selection
- Use ceramic capacitors for high-frequency decoupling and tantalum or electrolytic capacitors for bulk decoupling
- Select capacitors with low ESR and ESL to minimize impedance at high frequencies
- Use multiple capacitors in parallel to reduce the effective ESR and ESL
Power Plane Design
- Use thin dielectric materials between power and ground planes to increase the inherent decoupling capacitance
- Minimize the distance between power and ground planes to reduce inductance
- Avoid splitting power planes unnecessarily, as it can create impedance discontinuities
Component Placement and Routing
- Place decoupling capacitors as close as possible to the power pins of ICs
- Orient capacitors to minimize loop inductance and maximize effectiveness
- Route power traces as wide as possible to minimize inductance and resistance
- Avoid routing high-speed signals near power pins or decoupling capacitors
Simulation and Verification
- Perform power integrity simulations to predict resonance frequencies, impedance peaks, and current density
- Simulate the impact of decoupling capacitor placement and values on power supply noise
- Verify the effectiveness of decoupling through measurements and testing
Frequently Asked Questions (FAQ)
- What is the purpose of decoupling capacitors in PCB design?
-
Decoupling capacitors are used to suppress power supply noise and provide a stable, clean power supply to integrated circuits (ICs) on a PCB. They act as local energy reservoirs, supplying current to ICs during transient demands and filtering out high-frequency noise.
-
How do I select the right decoupling capacitor for my design?
-
When selecting decoupling capacitors, consider the frequency range of the noise to be suppressed, the required capacitance value, the equivalent series resistance (ESR) and inductance (ESL), voltage rating, temperature stability, and package size. Use ceramic capacitors for high-frequency decoupling and tantalum or electrolytic capacitors for bulk decoupling.
-
What is the best placement strategy for decoupling capacitors?
-
Place decoupling capacitors as close as possible to the power pins of ICs to minimize loop inductance and maximize effectiveness. Use multiple decoupling capacitors in parallel to reduce ESR and ESL, and minimize the loop area between the capacitor and the IC power pin. Use a combination of high-frequency and bulk decoupling capacitors for optimal performance.
-
How can power planes help with decoupling in multi-layer PCBs?
-
Power planes in multi-layer PCBs can act as inherent decoupling capacitors. To optimize power plane decoupling, use thin dielectric materials between power and ground planes, minimize the distance between power and ground planes, use multiple power planes for different voltage levels, and avoid splitting power planes unnecessarily.
-
What simulation tools can I use to analyze and optimize decoupling in my PCB design?
- Power integrity simulation tools can help optimize decoupling strategies by predicting resonance frequencies and impedance peaks, identifying areas of high current density and voltage drop, evaluating the effectiveness of decoupling capacitor placement, and analyzing the impact of via placement and plane stackup. Electromagnetic compatibility (EMC) analysis tools can help ensure that the PCB design meets electromagnetic compatibility standards by predicting electromagnetic emissions, identifying potential EMI coupling paths, and assessing the impact of decoupling on EMC performance.
Conclusion
Effective power supply noise decoupling is essential for ensuring the proper functioning and reliability of electronic systems. By understanding the sources and effects of power supply noise, selecting the right decoupling capacitors, and implementing optimal decoupling strategies in PCB design, designers can minimize noise, improve signal integrity, and achieve electromagnetic compatibility. Through careful placement of decoupling capacitors, power plane design, and simulation-driven optimization, PCB designers can create robust and reliable electronic systems that perform well in various applications and environments.
Leave a Reply