Introduction
Printed Circuit Boards (PCBs) are the backbone of modern electronics. They provide a platform for mounting and interconnecting electronic components to create a functional circuit. Choosing the right PCB Components is crucial for ensuring the reliability, performance, and cost-effectiveness of your PCB design. In this article, we will discuss 14 important tips for selecting PCB components that will help you make informed decisions and optimize your PCB design.
Tip 1: Understand Your PCB Requirements
Before selecting PCB components, it is essential to have a clear understanding of your PCB requirements. Consider the following factors:
– Functionality: What is the intended purpose of your PCB? What functions does it need to perform?
– Environment: Will your PCB be exposed to harsh environmental conditions such as extreme temperatures, humidity, or vibrations?
– Size and Form Factor: What are the size constraints for your PCB? Does it need to fit into a specific enclosure or follow a particular form factor?
– Power Requirements: What are the power supply requirements for your PCB? How much current will the components draw?
By defining your PCB requirements upfront, you can narrow down your component choices and ensure that they align with your design goals.
Tip 2: Choose Reliable Component Suppliers
The quality and reliability of your PCB components depend greatly on the suppliers you choose. When selecting component suppliers, consider the following:
– Reputation: Look for suppliers with a proven track record of providing high-quality components and excellent customer service.
– Certifications: Ensure that the suppliers have the necessary certifications and comply with industry standards such as ISO, RoHS, and UL.
– Availability: Check if the suppliers have a stable supply chain and can provide the components you need in the required quantities and timeframes.
– Technical Support: Verify if the suppliers offer technical support and have knowledgeable staff who can assist you with component selection and troubleshooting.
Choosing reliable component suppliers will minimize the risk of component failures and ensure the long-term reliability of your PCB.
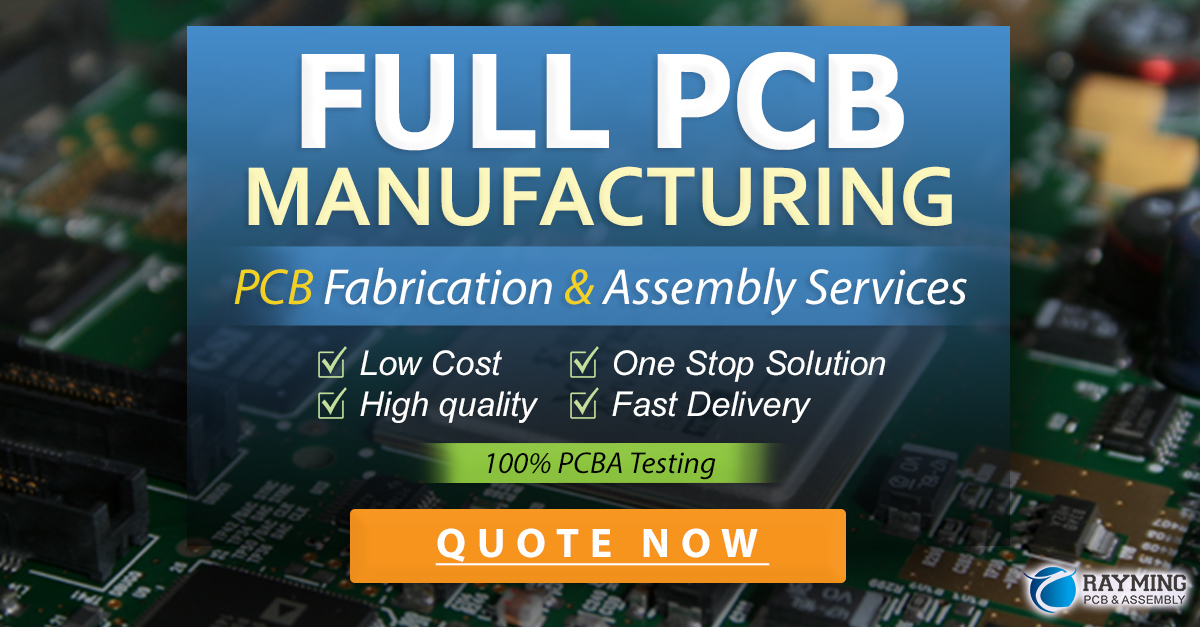
Tip 3: Consider Component Packaging
The packaging of PCB components plays a significant role in their handling, assembly, and overall cost. Common component packaging types include:
– Through-Hole (THT): Components with long leads that are inserted through holes in the PCB and soldered on the opposite side.
– Surface Mount (SMT): Components that are mounted directly on the surface of the PCB using solder pads.
– Ball Grid Array (BGA): Components with an array of solder balls underneath for high-density connections.
Consider the following factors when selecting component packaging:
– Assembly Process: Choose packaging that is compatible with your PCB Assembly process, whether it is manual soldering, reflow soldering, or wave soldering.
– Board Space: SMT and BGA packages offer higher component density and save board space compared to THT packages.
– Cost: SMT and BGA components are generally more cost-effective than THT components due to automated assembly processes.
Packaging Type | Advantages | Disadvantages |
---|---|---|
THT | – Easy to solder manually | – Requires more board space |
– Suitable for high-power components | – Higher assembly costs | |
SMT | – Higher component density | – Requires specialized assembly equipment |
– Automated assembly process | – Smaller component sizes | |
BGA | – High-density connections | – Requires precise placement and soldering |
– Compact package size | – Difficult to rework or replace |
Tip 4: Evaluate Component Specifications
When selecting PCB components, carefully evaluate their specifications to ensure they meet your design requirements. Key specifications to consider include:
– Electrical Ratings: Verify that the component’s voltage, current, and power ratings are suitable for your PCB’s operating conditions.
– Tolerance: Check the component’s tolerance, which indicates the allowable deviation from its nominal value. Tighter tolerances provide better accuracy but may increase cost.
– Temperature Range: Ensure that the component can operate reliably within the expected temperature range of your PCB.
– Frequency Response: For high-frequency applications, consider the component’s frequency response and any associated parasitics.
Reviewing the component’s datasheet and application notes will provide detailed information on its specifications and help you make informed decisions.
Tip 5: Consider Component Availability and Lead Time
Component availability and lead time are crucial factors to consider when selecting PCB components. Some components may have long lead times or be in short supply, which can impact your production schedule and costs. To mitigate these risks:
– Check Availability: Verify the availability of the components you need with your suppliers. Look for alternative sources if necessary.
– Plan Ahead: Place orders for critical components well in advance to account for lead times and potential supply chain disruptions.
– Consider Alternatives: Identify alternative components with similar specifications that can be used as substitutes if needed.
– Manage Inventory: Maintain an appropriate level of component inventory to avoid shortages and minimize the impact of lead times.
By proactively managing component availability and lead times, you can ensure a smooth and timely PCB production process.
Tip 6: Optimize for Manufacturing
Designing your PCB with manufacturing in mind can greatly simplify the assembly process and reduce costs. Consider the following tips:
– Standardize Components: Use standardized components whenever possible to reduce inventory costs and simplify procurement.
– Minimize Variations: Limit the number of different component types and values to streamline the assembly process and reduce the risk of errors.
– Optimize Placement: Place components in a way that facilitates automated assembly, such as using consistent orientation and spacing.
– Consider Testability: Design your PCB with testability in mind, incorporating test points and enabling easy access for inspection and debugging.
Collaborating with your PCB manufacturer and assembly partner early in the design process can provide valuable insights and help optimize your PCB for manufacturing efficiency.
Tip 7: Account for Thermal Management
Thermal management is essential for ensuring the reliable operation and longevity of your PCB components. Consider the following tips:
– Identify Heat Sources: Identify components that generate significant heat, such as power regulators, processors, and high-power devices.
– Provide Adequate Cooling: Incorporate appropriate cooling mechanisms, such as heatsinks, thermal pads, or fans, to dissipate heat effectively.
– Consider Thermal Resistance: Evaluate the thermal resistance of components and choose packages with lower thermal resistance for better heat dissipation.
– Optimize PCB Layout: Design your PCB layout to promote heat dissipation, such as providing sufficient copper pour and avoiding hot spots.
Proper thermal management helps prevent component overheating, improves reliability, and extends the lifespan of your PCB.
Tip 8: Ensure Compatibility
When selecting PCB components, ensure compatibility between different components and with the overall system. Consider the following aspects:
– Voltage Levels: Verify that the voltage levels of components are compatible with each other and with the power supply.
– Logic Families: Ensure that digital components belong to compatible logic families (e.g., TTL, CMOS) to avoid signal integrity issues.
– Interfaces: Check that components have compatible interfaces (e.g., I2C, SPI, UART) for seamless communication.
– Footprint and Pinout: Confirm that the component’s footprint and pinout match the PCB layout and schematic design.
Incompatible components can lead to functional issues, signal degradation, and even damage to the PCB.
Tip 9: Consider Electromagnetic Compatibility (EMC)
Electromagnetic Compatibility (EMC) is crucial for ensuring that your PCB operates reliably without causing or being affected by electromagnetic interference (EMI). Consider the following tips:
– Identify EMI Sources: Identify components and circuits that are potential sources of EMI, such as high-speed digital interfaces, switching regulators, and radio frequency (RF) modules.
– Implement EMI Suppression: Incorporate EMI suppression techniques, such as filtering, shielding, and proper grounding, to minimize EMI emissions and susceptibility.
– Choose EMC-Compliant Components: Select components that are designed for EMC compliance and have appropriate certifications (e.g., FCC, CE).
– Follow EMC Design Guidelines: Adhere to EMC design guidelines, such as proper PCB layout, signal routing, and power supply decoupling, to minimize EMI.
By addressing EMC considerations during component selection and PCB design, you can ensure the electromagnetic compatibility of your PCB and avoid costly EMC issues down the line.
Tip 10: Evaluate Cost and Budget
Cost is a significant factor in PCB Component Selection, and it is essential to strike a balance between performance and budget. Consider the following tips:
– Establish a Budget: Define a realistic budget for your PCB components based on your project requirements and constraints.
– Compare Prices: Compare prices from multiple suppliers to find the best value for your budget. Be cautious of components that are significantly cheaper than others, as they may compromise quality.
– Consider Total Cost of Ownership: Evaluate the total cost of ownership (TCO) of components, including not only the purchase price but also factors such as reliability, maintenance, and potential replacement costs.
– Optimize Component Selection: Look for opportunities to optimize component selection without compromising functionality or reliability. Consider using cheaper alternatives or reducing component counts where possible.
By carefully evaluating cost and budget, you can make informed decisions that balance performance, reliability, and financial feasibility.
Tip 11: Plan for Future Upgrades and Scalability
When selecting PCB components, consider the potential for future upgrades and scalability. Design your PCB with flexibility in mind to accommodate future enhancements or changes. Consider the following tips:
– Choose Versatile Components: Select components that offer flexibility and can be easily adapted to future requirements. For example, choose a microcontroller with sufficient memory and peripherals for future expansion.
– Provide Expansion Options: Include provisions for expansion, such as additional connectors, headers, or breakout boards, to allow for future additions or modifications.
– Consider Modularity: Design your PCB with a modular approach, separating different functional blocks into distinct modules. This allows for easier upgrades or replacements of specific sections without affecting the entire PCB.
– Plan for Software Upgrades: If your PCB includes programmable components, ensure that there is sufficient memory and processing power to accommodate future software upgrades and feature enhancements.
By planning for future upgrades and scalability, you can extend the lifespan of your PCB and adapt it to evolving requirements.
Tip 12: Collaborate with Experts
Collaborating with experts can greatly enhance your PCB component selection process. Seek input from experienced engineers, PCB designers, and component suppliers to make informed decisions. Consider the following:
– Consult with PCB Designers: Engage with experienced PCB designers who can provide valuable insights into component selection, PCB layout, and manufacturing considerations.
– Leverage Supplier Expertise: Utilize the technical support and expertise offered by component suppliers. They can provide recommendations, application notes, and guidance specific to their components.
– Participate in Online Communities: Engage with online communities and forums dedicated to PCB design and electronics. These platforms allow you to tap into the collective knowledge and experiences of other professionals.
– Attend Industry Events: Attend industry events, conferences, and workshops related to PCB design and component selection. These events provide opportunities to learn from experts, discover new technologies, and network with peers.
Collaborating with experts can help you make informed decisions, avoid common pitfalls, and optimize your PCB component selection process.
Tip 13: Prototype and Test
Prototyping and testing are essential steps in validating your PCB component selections and ensuring the overall functionality of your design. Consider the following tips:
– Create Prototypes: Build prototypes of your PCB to verify the functionality and performance of selected components. Prototypes allow you to identify and address any issues early in the development process.
– Perform Thorough Testing: Conduct comprehensive testing of your prototypes, including functional testing, environmental testing (e.g., temperature, humidity), and stress testing. This helps identify any weaknesses or limitations in your component selections.
– Validate Compatibility: Verify the compatibility between different components and ensure that they operate as expected when integrated into the PCB.
– Iterate and Refine: Based on the results of prototyping and testing, iterate and refine your component selections as necessary. Make adjustments to improve performance, reliability, or cost-effectiveness.
Prototyping and testing provide valuable feedback that can help you optimize your PCB component selections and ensure a robust and reliable final product.
Tip 14: Stay Updated with Industry Trends
The electronics industry is constantly evolving, with new technologies, components, and design methodologies emerging regularly. To make informed PCB component selections, it is essential to stay updated with industry trends. Consider the following tips:
– Follow Industry Publications: Subscribe to industry publications, magazines, and newsletters that cover PCB design, components, and electronics trends.
– Attend Trade Shows and Conferences: Participate in trade shows and conferences related to PCB design and electronics manufacturing. These events showcase the latest technologies, products, and industry trends.
– Monitor Supplier Updates: Keep track of updates and new product releases from component suppliers. They often provide information about the latest components, technologies, and application notes.
– Engage with Online Communities: Participate in online forums, social media groups, and communities focused on PCB design and electronics. These platforms provide valuable insights into emerging trends, best practices, and user experiences.
By staying updated with industry trends, you can make informed decisions, adopt new technologies, and ensure that your PCB designs remain competitive and relevant.
Conclusion
Choosing the right PCB components is a critical aspect of PCB design that directly impacts the functionality, reliability, and cost-effectiveness of your final product. By following the 14 important tips discussed in this article, you can navigate the component selection process with confidence and make informed decisions.
Remember to understand your PCB requirements, choose reliable suppliers, consider component packaging and specifications, optimize for manufacturing, ensure compatibility, and evaluate cost and budget. Additionally, plan for future upgrades, collaborate with experts, prototype and test, and stay updated with industry trends.
By applying these tips and best practices, you can streamline your PCB component selection process, minimize risks, and create PCBs that meet your design goals and exceed expectations.
FAQs
1. How do I determine the power supply requirements for my PCB components?
To determine the power supply requirements for your PCB components, follow these steps:
1. Identify the voltage and current requirements of each component based on their datasheets.
2. Calculate the total current draw of all components.
3. Consider the worst-case scenario and add a safety margin to account for any fluctuations or transient conditions.
4. Select a power supply that can provide the required voltage and current with sufficient headroom.
2. What are the advantages of using surface mount (SMT) components over through-hole (THT) components?
SMT components offer several advantages over THT components:
– Higher component density: SMT components have smaller footprints, allowing for more components to be placed on a given PCB area.
– Automated assembly: SMT components are well-suited for automated assembly processes, reducing manufacturing time and costs.
– Improved high-frequency performance: SMT components have shorter leads, reducing parasitic inductance and improving high-frequency performance.
– Lower cost: SMT components are generally more cost-effective than THT components due to automated assembly and reduced material usage.
3. How do I ensure electromagnetic compatibility (EMC) when selecting PCB components?
To ensure EMC when selecting PCB components:
1. Choose components that are designed for EMC compliance and have appropriate certifications (e.g., FCC, CE).
2. Identify potential sources of EMI, such as high-speed digital interfaces, switching regulators, and RF modules.
3. Implement EMI suppression techniques, such as filtering, shielding, and proper grounding, to minimize EMI emissions and susceptibility.
4. Follow EMC design guidelines for PCB layout, signal routing, and power supply decoupling.
4. What should I consider when selecting components for harsh environmental conditions?
When selecting components for harsh environmental conditions, consider the following:
1. Temperature range: Ensure that the components can operate reliably within the expected temperature range of your PCB.
2. Humidity: Choose components that are rated for the expected humidity levels and have appropriate moisture protection.
3. Vibration and shock: Select components that can withstand the expected levels of vibration and shock without damage or performance degradation.
4. Corrosion resistance: Consider components with appropriate coatings or materials that resist corrosion in the intended environment.
5. How can I optimize component selection for cost-effectiveness without compromising performance?
To optimize component selection for cost-effectiveness without compromising performance:
1. Identify components that are critical for performance and prioritize their selection based on specifications and quality.
2. Look for opportunities to use cheaper alternatives for non-critical components without sacrificing functionality or reliability.
3. Standardize components whenever possible to reduce inventory costs and simplify procurement.
4. Consider the total cost of ownership (TCO) of components, including factors such as reliability, maintenance, and potential replacement costs.
5. Collaborate with suppliers and experts to identify cost-effective solutions that meet your performance requirements.
Leave a Reply