Introduction to CCA Electronics
CCA Electronics, or Circuit Card Assembly Electronics, refers to the process of designing, manufacturing, and testing printed circuit boards (PCBs) that are populated with electronic components. These circuit card assemblies are used in a wide range of electronic devices, from consumer electronics to industrial equipment and aerospace systems.
In this comprehensive guide, we will provide you with useful tips and procedure guidance to help you navigate the world of CCA Electronics effectively.
Understanding the Basics of CCA Electronics
Before we dive into the specifics, it’s essential to understand the basic concepts and terminologies used in CCA Electronics.
What is a Printed Circuit Board (PCB)?
A Printed Circuit Board (PCB) is a flat board made of insulating material, such as fiberglass or plastic, with conductive tracks, pads, and other features etched or printed onto its surface. PCBs serve as the foundation for electronic components to be mounted and interconnected, forming a complete electronic circuit.
Types of PCBs
PCBs can be classified into several types based on their construction and the number of conductive layers:
- Single-sided PCBs: These have conductive tracks on only one side of the board.
- Double-sided PCBs: These have conductive tracks on both sides of the board, allowing for more complex circuits and higher component density.
- Multi-layer PCBs: These consist of multiple layers of conductive tracks separated by insulating layers, enabling even more complex circuits and higher component density.
Components Used in CCA Electronics
CCA Electronics involves a wide range of electronic components that are mounted onto the PCBs. Some common components include:
- Resistors
- Capacitors
- Inductors
- Diodes
- Transistors
- Integrated Circuits (ICs)
- Connectors
- Switches
Understanding the function and characteristics of these components is crucial for designing and troubleshooting CCA Electronics.
CCA Electronics Design Process
The CCA Electronics design process involves several key stages, each requiring careful planning and execution.
Schematic Design
The first step in CCA Electronics design is creating a schematic diagram that represents the electronic circuit. This diagram shows the interconnections between the various components and helps to ensure that the circuit will function as intended.
Tips for creating effective schematic diagrams:
- Use clear and consistent symbols for components
- Label all components and nets (connections) clearly
- Use hierarchical design techniques to manage complexity
- Perform thorough error checking and simulation before moving to the next stage
PCB Layout Design
Once the schematic design is complete, the next step is to create the PCB layout. This involves arranging the components on the board and routing the conductive tracks to interconnect them.
Tips for creating effective PCB layouts:
- Consider component placement for optimal signal integrity and manufacturability
- Follow best practices for track widths, spacing, and via sizes
- Use ground planes and power planes to reduce noise and improve signal quality
- Perform design rule checks (DRC) to ensure the layout meets manufacturing constraints
Component Selection and Procurement
Selecting the right components for your CCA Electronics project is critical for ensuring reliability, performance, and cost-effectiveness. When choosing components, consider factors such as:
- Electrical specifications (e.g., voltage rating, current rating, tolerance)
- Package type and size
- Availability and lead time
- Cost and minimum order quantity (MOQ)
- Compliance with relevant standards (e.g., RoHS, REACH)
Establishing a reliable supply chain and maintaining good relationships with component distributors can help streamline the procurement process and avoid delays.
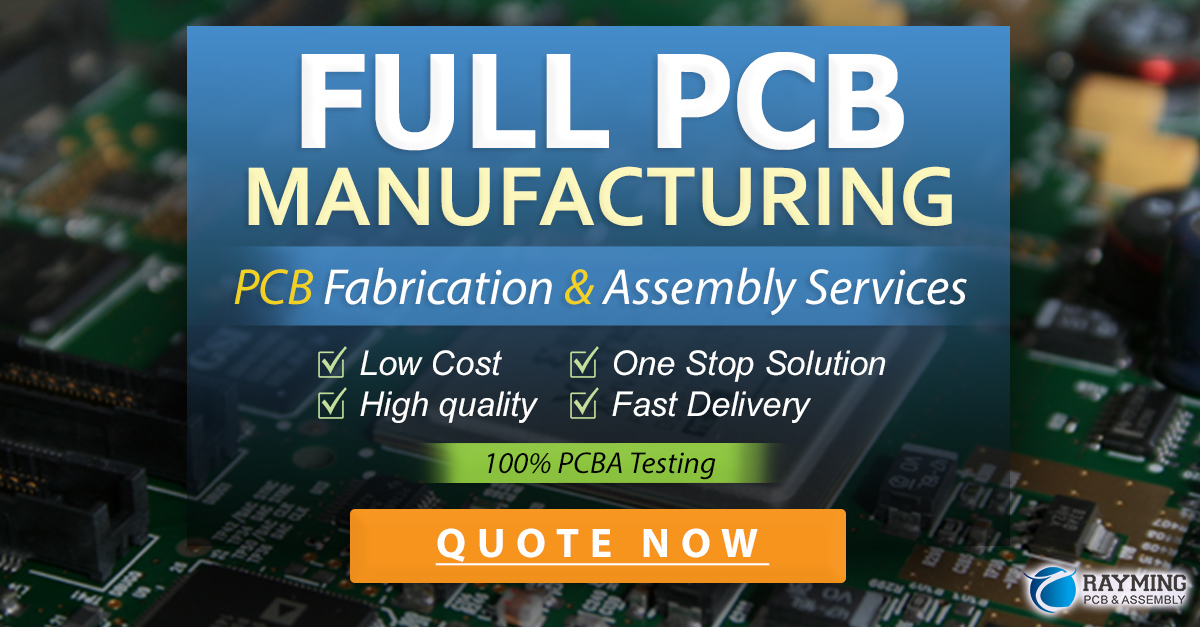
CCA Electronics Manufacturing Process
Once the design is finalized and components are procured, the next stage is the manufacturing of the CCA Electronics.
PCB Fabrication
PCB fabrication involves creating the bare PCB based on the layout design. This process typically includes the following steps:
- Copper clad laminate selection
- Drilling
- Copper plating
- Etching
- Solder mask application
- Silkscreen printing
Tips for successful PCB fabrication:
- Choose the appropriate copper clad laminate based on the application and design requirements
- Ensure the design files (e.g., Gerber files) are accurate and complete
- Communicate clearly with the PCB fabrication house to avoid misunderstandings and delays
PCB Assembly
PCB assembly involves mounting the components onto the fabricated PCB. This process can be done manually for low-volume production or prototyping, or automated using pick-and-place machines for high-volume production.
The main steps in PCB assembly are:
- Solder paste application
- Component placement
- Reflow soldering
- Inspection and testing
Tips for successful PCB assembly:
- Use solder paste with the appropriate specifications (e.g., alloy composition, particle size, viscosity)
- Ensure proper alignment and orientation of components during placement
- Control the reflow soldering process parameters (e.g., temperature profile, time) for optimal solder joint formation
- Perform thorough inspection and testing to identify and correct any defects
CCA Electronics Testing and Validation
Testing and validation are essential steps in ensuring the quality and reliability of CCA Electronics.
In-Circuit Testing (ICT)
In-Circuit Testing involves probing the individual components on the assembled PCB to verify their presence, orientation, and basic functionality. ICT is typically performed using a bed-of-nails fixture and specialized test equipment.
Functional Testing
Functional testing involves verifying that the assembled CCA Electronics performs its intended function under various operating conditions. This may include:
- Power-on testing
- Boundary scan testing
- Firmware/software testing
- Environmental testing (e.g., temperature, humidity, vibration)
Tips for effective testing and validation:
- Develop comprehensive test plans and procedures
- Use automated testing tools and equipment where appropriate
- Document test results and analyze any failures for continuous improvement
- Ensure traceability between design requirements, manufacturing processes, and test results
Common Challenges and Troubleshooting in CCA Electronics
Despite careful design and manufacturing, issues can still arise in CCA Electronics. Some common challenges and troubleshooting tips include:
Soldering Defects
Soldering defects, such as bridging, insufficient solder, or cold solder joints, can cause intermittent or complete failure of the CCA Electronics. To troubleshoot soldering defects:
- Visually inspect the solder joints using a microscope or high-resolution camera
- Use x-ray inspection for hidden or obscured solder joints
- Rework the defective solder joints using appropriate tools and techniques
Component Failures
Component failures can occur due to various reasons, such as manufacturing defects, overstress, or aging. To troubleshoot component failures:
- Use in-circuit testing or functional testing to isolate the faulty component
- Verify the component’s specifications and operating conditions
- Replace the faulty component with a known-good one and retest
Signal Integrity Issues
Signal integrity issues, such as crosstalk, reflections, or ground bounce, can cause noise, distortion, or loss of data in CCA Electronics. To troubleshoot signal integrity issues:
- Use oscilloscopes or logic analyzers to capture and analyze the signal waveforms
- Verify the PCB layout and component placement for proper signal routing and termination
- Implement appropriate filtering, shielding, or grounding techniques to mitigate the issues
Best Practices for CCA Electronics
To ensure the success of your CCA Electronics projects, consider adopting the following best practices:
Design for Manufacturing (DFM)
Design for Manufacturing (DFM) involves designing the CCA Electronics with consideration for the manufacturing processes and constraints. This can help to reduce costs, improve yields, and accelerate time-to-market.
Tips for implementing DFM:
- Follow the PCB fabrication and assembly house’s design rules and guidelines
- Use standard component packages and footprints where possible
- Minimize the use of unique or custom components
- Design for automated assembly processes
Design for Testability (DFT)
Design for Testability (DFT) involves designing the CCA Electronics with features that facilitate testing and diagnosis. This can help to reduce testing time and costs, and improve the overall quality of the product.
Tips for implementing DFT:
- Include test points and test pads for critical signals and components
- Use boundary scan techniques for complex digital circuits
- Provide clear and accessible labeling for components and test points
- Develop comprehensive test plans and procedures during the design phase
Continuous Improvement
Continuous improvement involves regularly reviewing and optimizing the CCA Electronics design, manufacturing, and testing processes based on feedback and data analysis. This can help to identify and eliminate inefficiencies, defects, and waste, leading to higher quality and customer satisfaction.
Tips for implementing continuous improvement:
- Establish key performance indicators (KPIs) and metrics to track progress
- Conduct regular audits and assessments of processes and products
- Encourage employee involvement and feedback for identifying improvement opportunities
- Implement a structured problem-solving approach, such as the 8D methodology
Frequently Asked Questions (FAQ)
- What is the difference between a PCB and a CCA?
-
A PCB is the bare board with conductive tracks and features, while a CCA is a PCB that has been populated with electronic components.
-
How do I choose the right components for my CCA Electronics project?
-
Consider factors such as electrical specifications, package type, availability, cost, and compliance with relevant standards when selecting components. Consult with experienced engineers or component distributors for guidance.
-
What are some common causes of solder joint defects in CCA Electronics?
-
Common causes of solder joint defects include improper solder paste application, component misalignment, incorrect reflow soldering parameters, and contamination of the PCB or components.
-
How can I improve the signal integrity in my CCA Electronics design?
-
Techniques for improving signal integrity include proper PCB layout and routing, use of ground planes and power planes, appropriate termination and filtering, and shielding of sensitive signals.
-
What are the benefits of implementing Design for Manufacturing (DFM) in CCA Electronics?
- Implementing DFM can help to reduce manufacturing costs, improve yields, and accelerate time-to-market by designing the CCA Electronics with consideration for the manufacturing processes and constraints.
Conclusion
CCA Electronics plays a crucial role in the modern world, enabling the development of innovative and reliable electronic devices across various industries. By understanding the basics of CCA Electronics, following best practices in design, manufacturing, and testing, and continuously improving processes, engineers and technicians can create high-quality and cost-effective products that meet customer requirements.
This comprehensive guide has provided you with useful tips and procedure guidance to help you navigate the complexities of CCA Electronics effectively. By applying these principles and staying up-to-date with the latest technologies and trends, you can contribute to the advancement of CCA Electronics and make a positive impact on the electronic devices that shape our lives.
Leave a Reply