Understanding PWM
What is PWM?
PWM is a method of controlling the average power delivered to a load by rapidly switching the power supply on and off. The duration of the “on” time, known as the pulse width, determines the amount of power delivered to the load. By varying the pulse width, we can effectively control the average voltage or current supplied to the load.
PWM Signal Characteristics
A PWM signal is characterized by the following parameters:
- Frequency: The number of pulses per second, measured in Hertz (Hz).
- Duty Cycle: The ratio of the pulse width to the total period, expressed as a percentage.
- Amplitude: The peak voltage level of the PWM signal.
The duty cycle is the key parameter in PWM, as it directly influences the average power delivered to the load. A higher duty cycle means more power, while a lower duty cycle results in less power.
PWM Circuit Components
To design a PWM circuit, you’ll need the following components:
- Microcontroller or PWM Controller: A device that generates the PWM signal based on your desired parameters.
- MOSFET or BJT Transistor: Used as a switch to control the power flow to the load.
- Gate Driver (optional): Provides the necessary drive current to switch the transistor efficiently.
- Passive Components: Resistors, capacitors, and inductors used for filtering, current limiting, and other circuit functions.
Microcontroller or PWM Controller
The heart of a PWM circuit is the microcontroller or dedicated PWM controller. Many microcontrollers, such as Arduino boards or PIC microcontrollers, have built-in PWM capabilities. These devices allow you to easily generate PWM signals with customizable frequency and duty cycle.
If you require more advanced features or higher performance, you can opt for a dedicated PWM controller IC. These controllers often provide additional functionalities like dead-time control, fault protection, and multiple PWM channels.
MOSFET or BJT Transistor
The transistor acts as a switch in the PWM circuit, allowing or blocking the flow of current to the load based on the PWM signal. MOSFETs (Metal-Oxide-Semiconductor Field-Effect Transistors) are commonly used due to their high efficiency and fast switching capabilities. BJTs (Bipolar Junction Transistors) can also be used, especially in low-power applications.
When selecting a transistor, consider the following factors:
- Voltage Rating: Ensure the transistor can handle the maximum voltage applied to the load.
- Current Rating: Choose a transistor that can safely handle the maximum current drawn by the load.
- Switching Speed: Faster switching speeds allow for higher PWM frequencies and better efficiency.
Gate Driver
In some cases, especially when using high-power MOSFETs, a gate driver circuit may be necessary. The gate driver provides the required drive current to charge and discharge the gate capacitance of the transistor quickly, enabling faster switching and reducing power losses.
Gate driver ICs simplify the design process by integrating the necessary components and providing features like over-current protection and isolation.
Passive Components
Passive components play essential roles in a PWM circuit:
- Resistors: Used for current limiting, pull-up/pull-down functions, and voltage dividers.
- Capacitors: Employed for filtering, decoupling, and smoothing the PWM signal.
- Inductors: Utilized in power supply filtering and energy storage.
The values and ratings of these components depend on the specific requirements of your PWM circuit, such as the desired switching frequency, load current, and voltage levels.
PWM Circuit Design Considerations
When designing a PWM circuit, consider the following factors to ensure optimal performance and reliability:
Switching Frequency
The switching frequency of the PWM signal affects several aspects of the circuit, including:
- Efficiency: Higher frequencies generally lead to improved efficiency by reducing the size of the required passive components and minimizing switching losses.
- Electromagnetic Interference (EMI): Faster switching can generate higher levels of EMI, which may require additional filtering or shielding.
- Audible Noise: PWM frequencies above the audible range (typically 20 kHz) are preferred to avoid audible noise from the switching components.
Choose a switching frequency that balances efficiency, EMI, and audible noise considerations based on your application requirements.
Duty Cycle Range
Determine the desired range of duty cycles for your PWM circuit. This range will depend on the specific application and the level of control required over the load.
For example, in LED dimming applications, a wide duty cycle range (e.g., 0-100%) allows for smooth brightness control. In motor control applications, the duty cycle range may be limited to ensure the motor operates within its specified speed range.
Load Characteristics
Consider the electrical characteristics of the load you want to control with the PWM circuit:
- Voltage Rating: Ensure the PWM circuit can handle the maximum voltage required by the load.
- Current Rating: Design the circuit to safely deliver the maximum current demanded by the load.
- Inductive vs. Resistive: Inductive loads, such as motors, require special considerations for flyback diode protection and Snubber Circuits to suppress voltage spikes during switching.
PCB Layout
Proper PCB layout is crucial for the performance and reliability of your PWM circuit. Follow these guidelines:
- Minimize Loop Area: Keep the high-current paths (e.g., power supply, load) as short and wide as possible to minimize inductance and resistance.
- Separate Sensitive Signals: Route sensitive signals, such as the PWM control signal, away from high-current paths to avoid interference.
- Grounding: Use a solid ground plane and properly decouple the power supply to minimize noise and ensure stable operation.
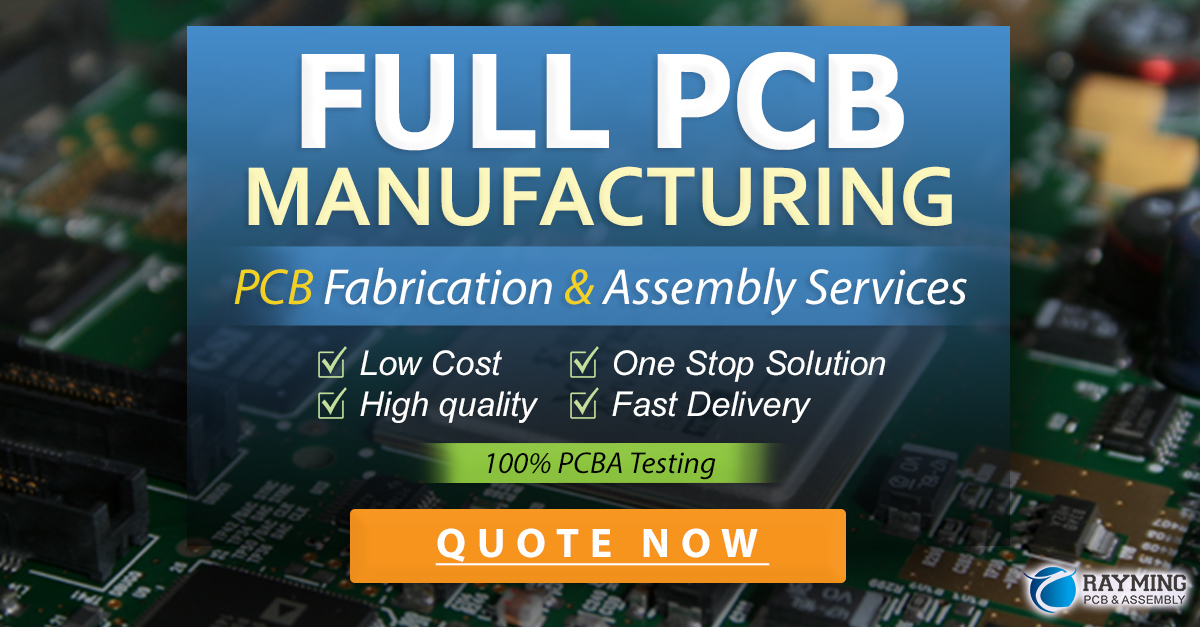
PWM Circuit Example
Let’s walk through a simple PWM circuit example using an Arduino Uno microcontroller and an N-channel MOSFET to control an LED.
Circuit Diagram
Arduino Uno
+-----+
| |
| |
+-----+ 13 +------+
| | | |
| +-----+ |
| |
| +--------+
| |
| | R1
| | 1kΩ
| |
| +---+---+
| | |
+-----+ Gate |
| |
| Q1 |
| IRFZ44|
| |
+---+---+
|
| LED
|
|
===
-
Circuit Components
- Arduino Uno microcontroller
- IRFZ44 N-channel MOSFET (Q1)
- 1kΩ resistor (R1)
- LED
Code Example
const int pwmPin = 13; // PWM output pin
void setup() {
pinMode(pwmPin, OUTPUT);
}
void loop() {
// Fade LED from off to full brightness
for (int brightness = 0; brightness <= 255; brightness++) {
analogWrite(pwmPin, brightness);
delay(10);
}
// Fade LED from full brightness to off
for (int brightness = 255; brightness >= 0; brightness--) {
analogWrite(pwmPin, brightness);
delay(10);
}
}
In this example, the Arduino generates a PWM signal on pin 13, which is connected to the gate of the MOSFET through a 1kΩ resistor. The MOSFET controls the current flow to the LED, effectively dimming it based on the duty cycle of the PWM signal.
The code gradually increases and decreases the brightness of the LED by varying the PWM duty cycle from 0 to 255 (0% to 100%) using the analogWrite()
function.
FAQ
-
Q: What is the difference between PWM and analog control?
A: PWM controls the power delivered to a load by rapidly switching the power on and off, while analog control varies the continuous voltage or current level. PWM is more efficient and easier to implement digitally, making it a popular choice for many applications. -
Q: Can PWM be used for controlling AC loads?
A: Yes, PWM can be used to control AC loads by using a different circuit topology called a “power inverter.” The PWM signal is used to generate a sinusoidal AC waveform by switching the DC power supply on and off at a high frequency. -
Q: How do I choose the right switching frequency for my PWM circuit?
A: The choice of switching frequency depends on factors such as efficiency, EMI, audible noise, and the requirements of your specific application. Higher frequencies generally offer better efficiency and smaller component sizes but may introduce more EMI. Consider the trade-offs and choose a frequency that meets your design goals. -
Q: What is the purpose of a gate driver in a PWM circuit?
A: A gate driver is used to provide the necessary drive current to charge and discharge the gate capacitance of a MOSFET quickly. It helps improve the switching speed and efficiency of the transistor, especially in high-power applications. -
Q: Can I use a PWM circuit to control multiple loads simultaneously?
A: Yes, you can use a PWM circuit to control multiple loads by using multiple PWM channels or by multiplexing a single PWM signal. Each load would require its own transistor and associated circuitry. Ensure that the total current draw of all loads does not exceed the ratings of your PWM controller and power supply.
Conclusion
Designing a PWM circuit involves understanding the principles of PWM, selecting the appropriate components, and considering factors such as switching frequency, duty cycle range, load characteristics, and PCB layout. By following the guidelines and examples provided in this article, you can create a PWM circuit that meets your specific requirements and delivers efficient and reliable power control to your load.
Remember to choose components with suitable ratings, consider the trade-offs between different design parameters, and pay attention to proper PCB layout techniques. With a well-designed PWM circuit, you can unlock the benefits of precise power control in a wide range of applications, from LED dimming to motor speed regulation.
As you embark on your PWM circuit design journey, don’t hesitate to consult additional resources, such as application notes, reference designs, and online communities, for further guidance and inspiration. Happy designing!
Leave a Reply