What is an Encoder?
An encoder is a device that converts the angular position or motion of a shaft or axle into an analog or digital code. It provides feedback to a control system, allowing it to determine the position, velocity, and direction of a moving part. Encoders are widely used in various industries, including automotive, aerospace, manufacturing, and robotics.
Types of Encoders
There are several types of encoders, each with its own unique features and applications. The main categories include:
- Incremental Encoders
- Absolute Encoders
- Linear Encoders
- Rotary Encoders
- Magnetic Encoders
- Optical Encoders
Let’s dive into each type in more detail.
1. Incremental Encoders
Incremental encoders provide information about the relative position and speed of a rotating shaft. They generate a series of pulses as the shaft rotates, allowing the control system to determine the position and velocity by counting the pulses.
Working Principle
Incremental encoders typically consist of a disc with a pattern of alternating transparent and opaque segments, a light source (usually an LED), and a photodetector. As the disc rotates with the shaft, the light beam is interrupted by the segments, generating pulses that are detected by the photodetector.
Most incremental encoders have two output channels, A and B, which are 90 degrees out of phase. This quadrature signal allows the control system to determine the direction of rotation by observing the sequence of pulses on the two channels.
Resolution
The resolution of an incremental encoder is determined by the number of segments on the disc, also known as the pulses per revolution (PPR). Higher PPR values provide greater positioning accuracy and smoother velocity control.
Advantages and Disadvantages
Advantages:
– Lower cost compared to absolute encoders
– Simple and reliable design
– Suitable for high-speed applications
Disadvantages:
– Requires a reference position (homing) at startup
– Cannot provide absolute position information if power is lost
– Susceptible to noise and contamination
Applications
Incremental encoders are commonly used in:
– Motor speed control
– Position tracking in CNC machines
– Rotary tables and indexers
– Conveyor systems
2. Absolute Encoders
Absolute encoders provide a unique digital code for each angular position of the shaft, allowing the control system to determine the absolute position without the need for a reference or homing sequence.
Working Principle
Absolute encoders use a disc with a unique pattern of concentric tracks, each representing a bit in the digital code. The tracks are typically arranged in a Gray code pattern to ensure that only one bit changes between adjacent positions, minimizing errors.
As the disc rotates, the light source and photodetectors read the pattern on the tracks, generating a parallel or serial digital output that represents the absolute angular position of the shaft.
Single-Turn and Multi-Turn Encoders
Absolute encoders can be classified as single-turn or multi-turn:
- Single-turn encoders provide a unique position value for each revolution of the shaft, typically with a resolution of 12 to 16 bits.
- Multi-turn encoders use additional gear stages or electronic counters to track the number of complete revolutions, allowing them to maintain absolute position information even after power cycling.
Advantages and Disadvantages
Advantages:
– Provides absolute position information, even after power loss
– No need for homing or reference position
– Resistant to noise and contamination
Disadvantages:
– Higher cost compared to incremental encoders
– More complex design and electronics
– Limited maximum speed due to the need to read multiple tracks simultaneously
Applications
Absolute encoders are commonly used in:
– Robotics and automation
– Machine tools and CNC machines
– Medical equipment
– Aerospace and defense systems
3. Linear Encoders
Linear encoders provide position feedback for linear motion applications, such as machine tool slides, gantry systems, and measuring machines.
Working Principle
Linear encoders typically consist of a scale (a linear ruler with a precise pattern) and a read head that moves along the scale. The read head contains a light source and photodetectors that read the pattern on the scale, generating an output signal that represents the linear position.
Linear encoders can be incremental or absolute, using similar working principles as their rotary counterparts.
Advantages and Disadvantages
Advantages:
– High accuracy and resolution
– Suitable for long travel distances
– Can be used in harsh environments with proper sealing
Disadvantages:
– Higher cost compared to rotary encoders
– Requires precise alignment between the scale and read head
– Sensitive to contamination and debris
Applications
Linear encoders are commonly used in:
– Machine tools and measuring machines
– Semiconductor manufacturing equipment
– 3D printers and additive manufacturing systems
– Medical imaging and scanning devices
4. Rotary Encoders
Rotary encoders, as the name suggests, provide position and velocity feedback for rotating shafts. They can be incremental or absolute, using the working principles described earlier.
Shaft and Hollow-Shaft Encoders
Rotary encoders can be further classified based on their mechanical design:
- Shaft encoders have a solid shaft that is coupled to the rotating component using a flexible coupling or a belt and pulley system.
- Hollow-shaft encoders have a bore that allows the rotating component to pass through, providing a more compact and direct coupling.
Advantages and Disadvantages
Advantages:
– Wide range of resolutions and accuracies available
– Suitable for various speed and torque requirements
– Can be easily integrated into existing systems
Disadvantages:
– Mechanical coupling introduces additional sources of error and wear
– Limited maximum speed due to the mechanical limitations of the coupling and bearings
– Requires proper alignment and mounting to ensure accurate measurements
Applications
Rotary encoders are commonly used in:
– Motor control and feedback systems
– Rotary tables and indexers
– Packaging and printing machines
– Wind turbines and energy generation systems
5. Magnetic Encoders
Magnetic encoders use magnetic fields to detect the position and velocity of a rotating shaft or linear axis. They offer several advantages over optical encoders, such as resistance to contamination and the ability to operate in harsh environments.
Working Principle
Magnetic encoders typically consist of a magnetic scale (a permanent magnet with alternating north and south poles) and a sensor that detects the changes in the magnetic field as the scale moves. The sensor can be a Hall Effect Sensor, a magnetoresistive sensor, or an inductive sensor.
As the magnetic scale moves relative to the sensor, the sensor generates an output signal that represents the position or velocity of the moving component.
Advantages and Disadvantages
Advantages:
– Resistant to contamination and debris
– Can operate in harsh environments, such as high temperatures and vibrations
– Non-contact sensing, reducing wear and maintenance requirements
Disadvantages:
– Lower resolution compared to optical encoders
– Susceptible to external magnetic fields and interference
– Limited miniaturization due to the size of the magnetic components
Applications
Magnetic encoders are commonly used in:
– Automotive applications, such as throttle position sensing and steering angle measurement
– Industrial automation and process control
– Agricultural and construction equipment
– Elevator and lift systems
6. Optical Encoders
Optical encoders use light to detect the position and velocity of a rotating shaft or linear axis. They offer high resolution and accuracy, making them suitable for precision applications.
Working Principle
Optical encoders consist of a light source (usually an LED), a disc or scale with a precise pattern of transparent and opaque segments, and a photodetector. As the disc or scale moves relative to the light source and photodetector, the light beam is interrupted by the segments, generating an output signal that represents the position or velocity of the moving component.
Optical encoders can be incremental or absolute, using the working principles described earlier.
Advantages and Disadvantages
Advantages:
– High resolution and accuracy
– Wide range of resolutions available
– Non-contact sensing, reducing wear and maintenance requirements
Disadvantages:
– Susceptible to contamination and debris, requiring proper sealing and protection
– Limited operating temperature range due to the sensitivity of the optical components
– Higher cost compared to magnetic encoders
Applications
Optical encoders are commonly used in:
– Precision motion control systems
– Robotics and automation
– Medical and scientific instruments
– Semiconductor manufacturing equipment
Encoder Selection Criteria
When selecting an encoder for a specific application, several factors should be considered:
-
Resolution and Accuracy: Determine the required resolution (incremental encoders) or number of bits (absolute encoders) based on the positioning accuracy and control requirements of the application.
-
Operating Environment: Consider the environmental conditions, such as temperature, humidity, vibration, and contamination, and select an encoder that can withstand these conditions.
-
Speed and Bandwidth: Ensure that the encoder’s maximum speed and bandwidth are sufficient for the application’s requirements, taking into account the control system’s sampling rate and response time.
-
Mechanical Interface: Choose an encoder with a mechanical interface (shaft, hollow-shaft, or linear scale) that is compatible with the application’s mechanical design and mounting requirements.
-
Output Interface: Select an encoder with an output interface (incremental, absolute, parallel, or serial) that is compatible with the control system’s input requirements and communication protocols.
-
Cost and Availability: Consider the cost and availability of the encoder, as well as the associated electronics and cabling, to ensure that the solution is economically feasible and can be easily sourced and maintained.
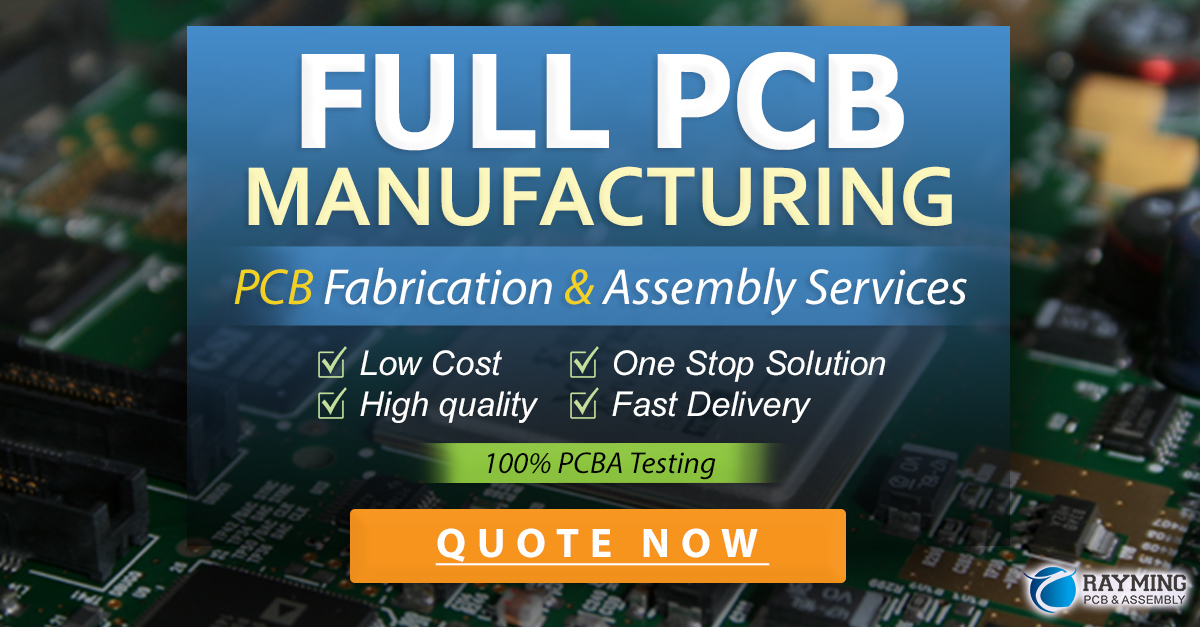
Frequently Asked Questions (FAQ)
- What is the difference between incremental and absolute encoders?
-
Incremental encoders provide relative position information and require a reference position at startup, while absolute encoders provide a unique position value for each angular position and do not require a reference position.
-
Can encoders be used in harsh environments?
-
Yes, certain types of encoders, such as magnetic encoders and properly sealed optical encoders, can operate in harsh environments with high temperatures, vibrations, and contamination.
-
How do I determine the resolution of an encoder for my application?
-
The required resolution depends on the positioning accuracy and control requirements of the application. Consider factors such as the minimum positioning increment, the control system’s sampling rate, and the mechanical system’s response time.
-
What is the advantage of using a hollow-shaft encoder over a shaft encoder?
-
Hollow-shaft encoders provide a more compact and direct coupling to the rotating component, reducing the overall footprint and the potential for misalignment and mechanical errors.
-
Can encoders be used for linear motion applications?
- Yes, linear encoders are specifically designed for linear motion applications, providing position feedback for machine tool slides, gantry systems, and measuring machines.
Conclusion
Encoders play a critical role in various applications, providing precise position and velocity feedback for rotating shafts and linear axes. Understanding the different types of encoders, their working principles, and their advantages and disadvantages is essential for selecting the appropriate encoder for a specific application.
By considering factors such as resolution, operating environment, speed, mechanical interface, output interface, and cost, engineers and system designers can choose the optimal encoder solution to ensure accurate and reliable motion control and monitoring.
As technology advances, encoders continue to evolve, offering higher resolutions, improved resistance to harsh environments, and better integration with digital control systems. With the growing demand for automation and precision in various industries, the importance of encoders in enabling accurate and efficient motion control cannot be overstated.
Leave a Reply