What is Piezoelectricity?
Piezoelectricity is a phenomenon exhibited by certain materials in which an electric charge is generated in response to applied mechanical stress. Conversely, these materials also experience mechanical deformation when exposed to an electric field. This reciprocal relationship between mechanical stress and electrical charge is the foundation of piezoelectric technology.
The piezoelectric effect was first discovered by Pierre and Jacques Curie in 1880 during their study of quartz crystals. They observed that when pressure was applied to the crystals, an electric potential was generated across the material. This groundbreaking discovery laid the foundation for the development of piezoelectric materials and their diverse applications.
Fundamentals of Piezoelectricity
Crystal Structure and Polarization
Piezoelectric materials possess a unique crystal structure that allows for the generation of an electric charge under mechanical stress. These materials are typically composed of polar crystals, which means that their unit cells lack a center of symmetry. This asymmetry gives rise to a net electric dipole moment within the material.
In the absence of an external force, the electric dipoles in a piezoelectric material are randomly oriented, resulting in a neutral charge distribution. However, when mechanical stress is applied, the crystal structure deforms, causing the electric dipoles to align and generate a net electric charge on the surface of the material.
Direct and Inverse Piezoelectric Effect
The piezoelectric effect can be classified into two categories: the direct piezoelectric effect and the inverse piezoelectric effect.
-
Direct Piezoelectric Effect:
In the direct piezoelectric effect, mechanical stress applied to a piezoelectric material generates an electric charge. This effect is used in sensors and energy harvesting applications, where the mechanical energy is converted into electrical energy. -
Inverse Piezoelectric Effect:
The inverse piezoelectric effect occurs when an electric field is applied to a piezoelectric material, causing it to deform or strain. This effect is utilized in actuators and transducers, where an electrical signal is used to control the mechanical behavior of the material.
Piezoelectric Coefficients
Piezoelectric materials are characterized by their piezoelectric coefficients, which quantify the relationship between mechanical stress and electric charge. These coefficients are denoted by the symbols “d” and “g” and are expressed in units of coulomb per newton (C/N) or volt-meter per newton (Vm/N), respectively.
- The “d” coefficient represents the amount of electric charge generated per unit of applied mechanical stress.
- The “g” coefficient represents the amount of mechanical strain produced per unit of applied electric field.
The values of these coefficients vary depending on the specific piezoelectric material and its crystal orientation.
Piezoelectric Materials
Piezoelectric materials can be classified into two main categories: natural and synthetic.
Natural Piezoelectric Materials
Some naturally occurring materials exhibit piezoelectric properties. The most well-known example is quartz, which has been widely used in piezoelectric applications due to its abundance and excellent piezoelectric properties. Other natural piezoelectric materials include:
- Tourmaline
- Rochelle salt
- Topaz
- Cane sugar
While natural piezoelectric materials have been used historically, synthetic materials have gained prominence due to their tailored properties and wider range of applications.
Synthetic Piezoelectric Materials
Synthetic piezoelectric materials are engineered to exhibit enhanced piezoelectric properties and are designed for specific applications. These materials can be categorized into three main groups:
-
Piezoelectric Ceramics:
Piezoelectric ceramics are the most widely used synthetic piezoelectric materials. They are typically based on lead zirconate titanate (PZT) and its derivatives. PZT ceramics exhibit high piezoelectric coefficients, making them suitable for a wide range of applications, including sensors, actuators, and transducers. -
Piezoelectric Polymers:
Piezoelectric polymers, such as polyvinylidene fluoride (PVDF) and its copolymers, offer unique advantages over ceramics. They are flexible, lightweight, and can be easily molded into various shapes. Piezoelectric polymers find applications in flexible sensors, energy harvesting devices, and biomedical applications. -
Piezoelectric Composites:
Piezoelectric composites combine the properties of piezoelectric ceramics and polymers to achieve enhanced performance. These materials consist of a piezoelectric ceramic phase embedded in a polymer matrix. Composites offer improved flexibility, high piezoelectric coefficients, and the ability to tailor their properties for specific applications.
The choice of piezoelectric material depends on the specific requirements of the application, such as the desired piezoelectric coefficients, operating temperature range, and mechanical properties.
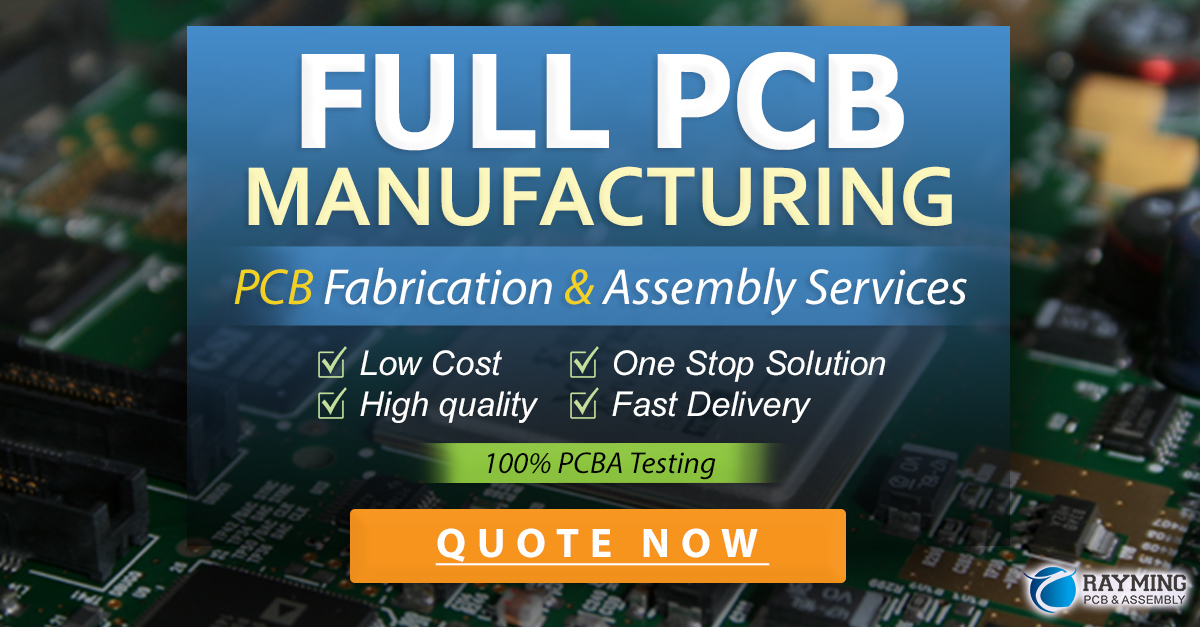
Piezoelectric Applications
Piezoelectric materials have found numerous applications across various industries due to their unique ability to convert between mechanical and electrical energy. Some of the key application areas include:
Sensors
Piezoelectric sensors utilize the direct piezoelectric effect to detect and measure mechanical quantities such as pressure, force, acceleration, and strain. These sensors are widely used in various fields, including:
-
Automotive: Piezoelectric sensors are used in pressure sensors for engine management, tire pressure monitoring systems (TPMS), and crash detection sensors for airbag deployment.
-
Industrial: Piezoelectric sensors are employed in process control, condition monitoring, and structural health monitoring applications.
-
Medical: Piezoelectric sensors find applications in medical devices, such as ultrasound imaging transducers and blood pressure sensors.
Actuators
Piezoelectric actuators leverage the inverse piezoelectric effect to convert electrical energy into precise mechanical motion. These actuators offer high-precision positioning, fast response times, and low power consumption. Some common applications include:
-
Precision positioning: Piezoelectric actuators are used in scanning probe microscopy, atomic force microscopy (AFM), and precision stages for nanopositioning.
-
Vibration control: Piezoelectric actuators are employed in active vibration control systems to suppress unwanted vibrations in structures and machines.
-
Microfluidics: Piezoelectric actuators are used in microfluidic devices for precise control of fluid flow and droplet generation.
Energy Harvesting
Piezoelectric energy harvesting exploits the direct piezoelectric effect to convert ambient mechanical energy, such as vibrations or strain, into electrical energy. This technology has gained attention as a potential power source for low-power electronics and wireless sensor networks. Some applications include:
-
Wearable devices: Piezoelectric energy harvesters can be integrated into clothing or footwear to generate electricity from human motion.
-
Structural health monitoring: Piezoelectric energy harvesters can power wireless sensors for monitoring the health and integrity of structures, such as bridges and buildings.
-
Industrial machinery: Piezoelectric energy harvesters can be attached to industrial machinery to harvest vibration energy and power condition monitoring sensors.
Ultrasonic Transducers
Piezoelectric materials are widely used in ultrasonic transducers, which convert electrical energy into high-frequency mechanical vibrations and vice versa. These transducers find applications in various fields, such as:
-
Medical imaging: Piezoelectric ultrasonic transducers are used in diagnostic ultrasound imaging systems to generate and detect high-frequency sound waves for visualizing internal body structures.
-
Non-destructive testing (NDT): Piezoelectric transducers are employed in NDT techniques, such as ultrasonic testing, to detect flaws and defects in materials and structures.
-
Underwater acoustics: Piezoelectric transducers are used in sonar systems for underwater communication, navigation, and object detection.
Future Prospects and Research Directions
Piezoelectric technology continues to evolve, with ongoing research and development efforts aimed at improving the performance, efficiency, and sustainability of piezoelectric materials and devices. Some key research directions and future prospects include:
Lead-Free Piezoelectric Materials
Conventional piezoelectric ceramics, such as PZT, contain lead, which poses environmental and health concerns. Researchers are actively exploring lead-free piezoelectric materials, such as potassium sodium niobate (KNN) and bismuth sodium titanate (BNT), as eco-friendly alternatives. These materials offer comparable piezoelectric properties while reducing the environmental impact.
Flexible and Stretchable Piezoelectric Materials
The development of flexible and stretchable piezoelectric materials is gaining momentum to meet the demands of emerging applications, such as wearable electronics, soft robotics, and biomedical devices. Researchers are investigating novel materials, such as piezoelectric polymers and composites, that can withstand large deformations while maintaining their piezoelectric properties.
Energy Harvesting Optimization
Piezoelectric energy harvesting has the potential to power wireless sensor networks and low-power electronics. Research efforts are focused on optimizing energy harvesting efficiency, developing advanced circuit designs, and exploring novel piezoelectric materials and device architectures to maximize the energy conversion efficiency and power output.
Integration with Other Technologies
Piezoelectric materials are being integrated with other technologies, such as microelectromechanical systems (MEMS), flexible electronics, and additive manufacturing, to create multifunctional and smart devices. This integration enables the development of compact, low-power, and highly sensitive devices for various applications, including wearable sensors, implantable medical devices, and smart structures.
Frequently Asked Questions (FAQ)
-
What is the main difference between piezoelectric ceramics and polymers?
Piezoelectric ceramics, such as PZT, exhibit high piezoelectric coefficients and are rigid and brittle. In contrast, piezoelectric polymers, like PVDF, are flexible, lightweight, and can be easily molded into various shapes. Ceramics are suitable for high-performance applications, while polymers are preferred for flexible and wearable devices. -
Can piezoelectric materials generate continuous power?
Piezoelectric materials generate electrical energy when subjected to mechanical stress or strain. They are most effective at harvesting energy from dynamic or fluctuating mechanical sources, such as vibrations or intermittent pressure. Continuous power generation would require a constant application of mechanical stress, which may not be practical in many scenarios. -
How do piezoelectric sensors differ from other types of sensors?
Piezoelectric sensors directly convert mechanical quantities, such as pressure, force, or acceleration, into electrical signals without the need for an external power source. They offer high sensitivity, fast response times, and a wide dynamic range. Other types of sensors, such as resistive or capacitive sensors, may require external power and signal conditioning circuits. -
What are the limitations of piezoelectric energy harvesting?
Piezoelectric energy harvesting is limited by the availability and magnitude of the mechanical energy source. The power output of piezoelectric energy harvesters is typically low, in the range of microwatts to milliwatts, which may not be sufficient for powering larger electronic devices. Additionally, the efficiency of energy conversion depends on factors such as the frequency and amplitude of the mechanical input and the impedance matching between the piezoelectric material and the electronic circuitry. -
Are piezoelectric materials safe for medical applications?
Piezoelectric materials used in medical applications, such as ultrasound imaging transducers, are generally considered safe. However, the safety of piezoelectric materials depends on factors such as the specific material composition, the application method, and the exposure duration. Researchers are continually developing biocompatible and non-toxic piezoelectric materials to ensure their safe use in medical devices and implantable sensors.
Conclusion
Piezoelectric technology has revolutionized various fields, from sensors and actuators to energy harvesting and ultrasonic transducers. The unique ability of piezoelectric materials to convert between mechanical and electrical energy has opened up a wide range of applications, enabling precise sensing, actuation, and power generation.
As research continues to advance, piezoelectric materials are becoming more versatile, efficient, and sustainable. The development of lead-free piezoelectric ceramics, flexible and stretchable piezoelectric polymers, and optimized energy harvesting techniques promises to expand the possibilities of piezoelectric technology.
With ongoing advancements in materials science, electronics, and manufacturing techniques, piezoelectric devices are poised to play an increasingly important role in shaping the future of sensing, actuation, and energy harvesting. As we move towards a more connected and sustainable world, piezoelectric technology will undoubtedly contribute to the development of smart, efficient, and self-powered systems across various industries.
Piezoelectric Material | Piezoelectric Coefficient (d33) | Relative Permittivity (εr) | Curie Temperature (°C) |
---|---|---|---|
PZT (Lead Zirconate Titanate) | 200-600 pC/N | 1000-3000 | 150-350 |
BaTiO3 (Barium Titanate) | 190 pC/N | 1700 | 120 |
PVDF (Polyvinylidene Fluoride) | 20-30 pC/N | 6-12 | 100-200 |
AlN (Aluminum Nitride) | 5-7 pC/N | 8-10 | 2200 |
ZnO (Zinc Oxide) | 12 pC/N | 8-10 | 700 |
Table: Comparison of common piezoelectric materials and their properties.
This comprehensive guide has provided an in-depth understanding of piezoelectricity, its fundamentals, materials, applications, and future prospects. By harnessing the power of piezoelectric technology, we can develop innovative solutions to address various challenges in sensing, actuation, energy harvesting, and beyond, paving the way for a smarter and more sustainable future.
Leave a Reply