What are Piezoelectric Materials?
Piezoelectric materials are a class of materials that exhibit the piezoelectric effect, which is the ability to generate an electric charge in response to applied mechanical stress. Conversely, these materials also exhibit the reverse piezoelectric effect, where they undergo mechanical deformation when exposed to an electric field. Some common piezoelectric materials include:
- Quartz (SiO2)
- Lead Zirconate Titanate (PZT)
- Barium Titanate (BaTiO3)
- Polyvinylidene Fluoride (PVDF)
The piezoelectric effect is attributed to the asymmetric crystalline structure of these materials, which allows for the separation of positive and negative charges when subjected to mechanical stress.
Piezoelectric Coefficients and Constants
To quantify the piezoelectric properties of a material, several coefficients and constants are used:
Coefficient/Constant | Symbol | Unit | Description |
---|---|---|---|
Piezoelectric charge constant | d | C/N or m/V | Ratio of generated charge to applied force (direct effect) or induced strain to applied electric field (converse effect) |
Piezoelectric voltage constant | g | Vm/N or m²/C | Ratio of generated electric field to applied stress (direct effect) or induced strain to applied charge density (converse effect) |
Electromechanical coupling factor | k | – | Efficiency of energy conversion between mechanical and electrical domains |
Permittivity | ε | F/m | Dielectric constant of the material |
Compliance | s | m²/N | Elastic compliance of the material |
These coefficients and constants are essential for designing and analyzing Piezo Circuits, as they determine the performance and efficiency of the piezoelectric elements used in the circuit.
Basic Piezo Circuit Configurations
There are two basic configurations for piezo circuits, depending on the desired application:
Sensor Configuration
In the sensor configuration, the piezoelectric element is used to convert mechanical energy (e.g., force, pressure, or vibration) into an electrical signal. The piezoelectric element is typically connected to a high-impedance input, such as an operational amplifier or a charge amplifier, to minimize loading effects and maximize the output signal.
Actuator Configuration
In the actuator configuration, an electrical signal is applied to the piezoelectric element to induce mechanical deformation or displacement. The piezoelectric element is usually driven by a high-voltage amplifier or a switched-mode power supply to generate the required electric field.
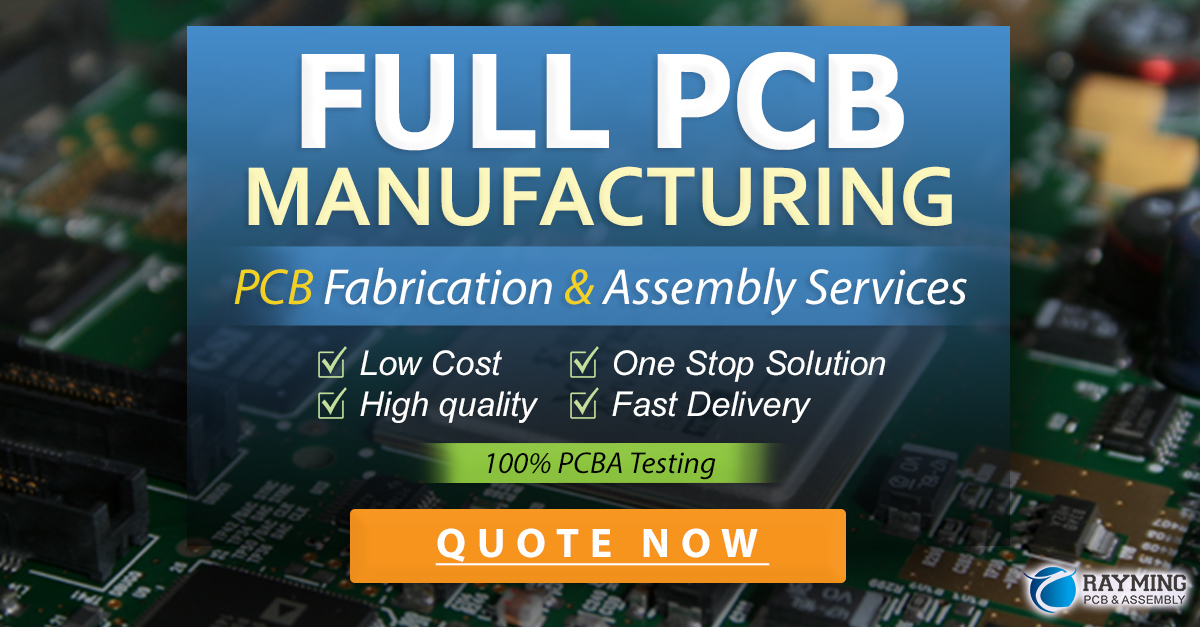
Applications of Piezo Circuits
Piezo circuits find applications in various fields, ranging from industrial automation and automotive systems to consumer electronics and medical devices. Some notable applications include:
Sensors
- Accelerometers
- Pressure sensors
- Force sensors
- Vibration Sensors
- Acoustic sensors (microphones)
Actuators
- Piezoelectric motors
- Ultrasonic transducers
- Micro-positioning stages
- Fuel injectors
- Inkjet printheads
Energy Harvesting
- Vibration energy harvesters
- Pressure energy harvesters
- Fluid flow energy harvesters
Signal Processing
- Filters (e.g., Surface Acoustic Wave (SAW) filters)
- Delay lines
- Resonators
Design Considerations for Piezo Circuits
When designing piezo circuits, several factors need to be considered to ensure optimal performance and reliability:
Impedance Matching
Piezoelectric elements have high output impedance, which requires proper impedance matching to maximize power transfer and minimize signal distortion. This can be achieved using high-impedance input stages, such as charge amplifiers or voltage followers, or by using impedance matching networks.
Frequency Response
The frequency response of piezoelectric elements is characterized by their resonant frequency and quality factor (Q). The resonant frequency depends on the material properties and dimensions of the piezoelectric element, while the quality factor determines the bandwidth and selectivity of the element. The circuit design should take into account the frequency response of the piezoelectric element to ensure optimal performance in the desired frequency range.
Temperature Stability
Piezoelectric materials exhibit temperature-dependent behavior, which can affect their performance and reliability. The circuit design should incorporate temperature compensation techniques, such as using temperature-stable materials or implementing active temperature control, to minimize the impact of temperature variations on the piezo circuit.
Electrical Noise and Interference
Piezo circuits are susceptible to electrical noise and interference, particularly when dealing with low-level signals. Proper shielding, grounding, and filtering techniques should be employed to minimize the impact of noise and interference on the circuit performance. This can include using shielded cables, implementing ground planes, and incorporating low-pass or band-pass filters.
Power Consumption and Efficiency
In battery-powered or energy-harvesting applications, power consumption and efficiency are crucial considerations. The circuit design should optimize power consumption by using low-power components, implementing power management techniques (e.g., sleep modes), and minimizing power losses in the piezoelectric element and associated circuitry.
Challenges and Future Trends
Despite their widespread use and numerous advantages, piezo circuits face several challenges and opportunities for future development:
Integration with MEMS Technology
The integration of piezoelectric materials with Microelectromechanical Systems (MEMS) technology has opened up new possibilities for miniaturized, low-power, and high-performance piezo devices. However, this integration also presents challenges in terms of material compatibility, fabrication processes, and packaging.
Novel Piezoelectric Materials
Researchers are continuously exploring new piezoelectric materials with improved properties, such as higher piezoelectric coefficients, better temperature stability, and enhanced mechanical strength. These materials, such as single-crystal piezoelectrics and piezoelectric composites, have the potential to revolutionize the performance and applicability of piezo circuits.
Wireless and Batteryless Operation
The development of piezo circuits that can operate wirelessly and without batteries, by harvesting energy from the environment (e.g., vibrations, pressure fluctuations), is a promising trend for self-powered sensors and actuators. However, this requires efficient energy harvesting and power management techniques, as well as low-power circuit designs.
Integration with IoT and Smart Systems
The integration of piezo circuits with the Internet of Things (IoT) and smart systems presents new opportunities for remote monitoring, control, and automation. However, this integration also poses challenges in terms of data processing, communication protocols, and security.
Frequently Asked Questions (FAQ)
-
What is the difference between direct and converse piezoelectric effects?
The direct piezoelectric effect refers to the generation of an electric charge in response to applied mechanical stress, while the converse piezoelectric effect refers to the mechanical deformation of a piezoelectric material when exposed to an electric field. -
How do I select the appropriate piezoelectric material for my application?
The selection of the appropriate piezoelectric material depends on several factors, such as the desired piezoelectric coefficients, operating frequency range, temperature stability, and mechanical properties. Consult the manufacturer’s data sheets and application notes, and consider factors such as cost, availability, and ease of integration with your circuit design. -
What is the role of a charge amplifier in a piezo sensor circuit?
A charge amplifier is used to convert the high-impedance charge output of a piezoelectric sensor into a low-impedance voltage signal, while minimizing the loading effect on the sensor. The charge amplifier also provides signal conditioning, such as amplification and filtering, to optimize the output signal for further processing. -
How can I minimize the impact of temperature variations on my piezo circuit?
Temperature variations can be minimized by using temperature-stable piezoelectric materials, implementing active temperature control (e.g., using heaters or Peltier elements), or employing temperature compensation techniques in the circuit design (e.g., using temperature-sensitive components or digital compensation algorithms). -
What are the key challenges in integrating piezo circuits with wireless and IoT systems?
The key challenges in integrating piezo circuits with wireless and IoT systems include power consumption, data processing, communication protocols, and security. Piezo circuits should be designed for low-power operation, and efficient data processing and communication techniques should be employed to minimize power consumption and ensure reliable data transfer. Additionally, appropriate security measures should be implemented to protect the system from unauthorized access and data breaches.
In conclusion, piezo circuits offer a versatile and powerful solution for converting mechanical energy into electrical energy and vice versa, with numerous applications in sensing, actuation, energy harvesting, and signal processing. By understanding the fundamentals of piezoelectric materials, basic circuit configurations, and design considerations, engineers and researchers can develop innovative and efficient piezo circuits for a wide range of applications. As the field continues to evolve, the integration of piezo circuits with emerging technologies, such as MEMS, IoT, and smart systems, presents exciting opportunities for future development and growth.
Leave a Reply