Introduction to PCB standards
In the world of electronics manufacturing, printed circuit boards (PCBs) play a crucial role in connecting and supporting electronic components. To ensure the quality, reliability, and consistency of PCBs, the electronics industry relies on a set of standards and guidelines. Two of the most important standards in PCB production are IPC-6012 and IPC-A-600. These standards provide a common language and set of requirements for PCB manufacturers, designers, and end-users, helping to streamline the production process and maintain high-quality products.
What is IPC-6012?
IPC-6012, titled “Qualification and Performance Specification for Rigid Printed Boards,” is a standard developed by the IPC (Association Connecting Electronics Industries). This standard establishes the requirements for the qualification and performance of rigid printed boards, including single-sided, double-sided, and multi-layer boards. IPC-6012 covers various aspects of PCB production, such as:
- Material requirements
- Dimensional tolerances
- Conductor definition and spacing
- Hole size and placement
- Surface finishing
- Electrical properties
- Mechanical properties
- Environmental testing
By adhering to the guidelines set forth in IPC-6012, PCB manufacturers can ensure that their products meet the necessary quality and performance criteria for a wide range of applications.
IPC-6012 Classifications
IPC-6012 classifies rigid printed boards into three performance classes based on their intended end-use and reliability requirements:
Class | Description |
---|---|
Class 1 | General Electronic Products |
Class 2 | Dedicated Service Electronic Products |
Class 3 | High Reliability Electronic Products |
Each class has its own set of requirements and acceptance criteria, with Class 3 being the most stringent and suitable for applications where high reliability is critical, such as in aerospace, medical, and military industries.
What is IPC-A-600?
IPC-A-600, titled “Acceptability of Printed Boards,” is a companion standard to IPC-6012. While IPC-6012 focuses on the qualification and performance requirements of rigid printed boards, IPC-A-600 provides visual acceptance criteria for PCBs. This standard includes high-resolution color photographs and illustrations that demonstrate the acceptable and unacceptable conditions of PCBs in various categories, such as:
- Solderability
- Laminate conditions
- Conductor definition and spacing
- Hole characteristics
- Solder mask and marking
- Surface finishing
By using IPC-A-600 as a visual reference, PCB manufacturers, inspectors, and end-users can quickly and easily assess the quality of a PCB and determine whether it meets the required acceptance criteria.
IPC-A-600 Target Conditions
IPC-A-600 defines three target conditions for each characteristic:
Target Condition | Description |
---|---|
Target | The desired condition for the characteristic |
Acceptable | A condition that, while not perfect, still meets the functional requirements of the PCB |
Nonconforming | A condition that does not meet the requirements of the specification and may affect the functionality or reliability of the PCB |
By understanding these target conditions, manufacturers can strive to produce PCBs that meet the “Target” condition while ensuring that any deviations fall within the “Acceptable” range.
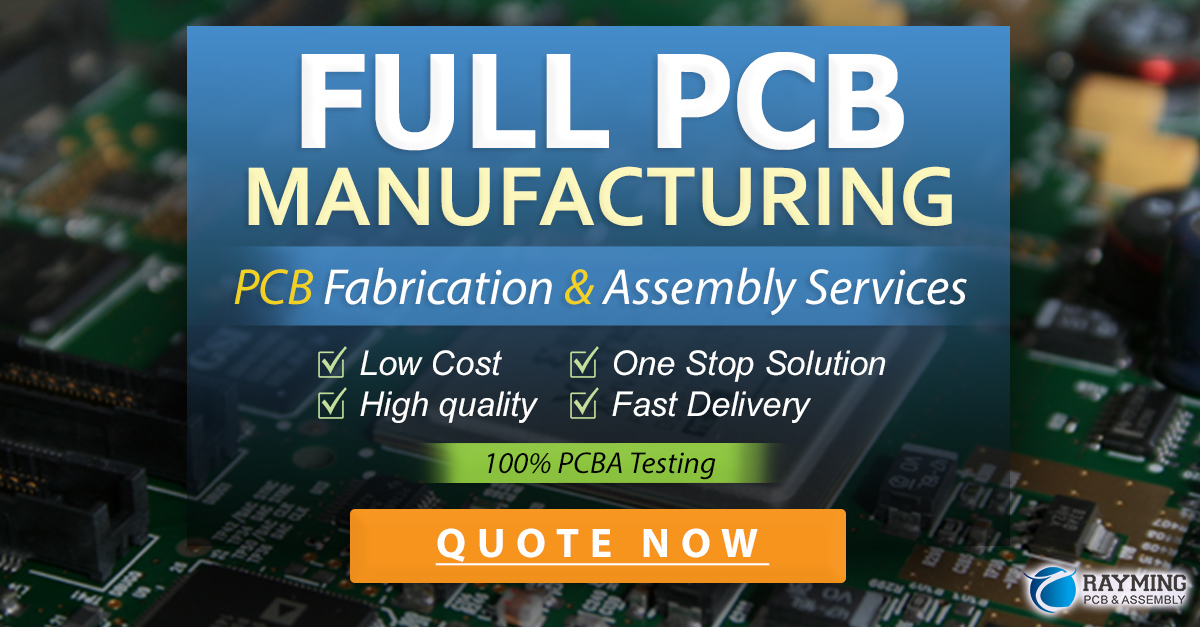
The Benefits of Adhering to IPC-6012 and IPC-A-600
Adhering to IPC-6012 and IPC-A-600 standards offers numerous benefits for PCB manufacturers, designers, and end-users, including:
-
Improved Quality: By following the guidelines set forth in these standards, manufacturers can consistently produce high-quality PCBs that meet the necessary performance and reliability requirements.
-
Reduced Costs: Adhering to IPC standards helps minimize the occurrence of defects and rework, which can lead to significant cost savings in the long run.
-
Enhanced Communication: IPC standards provide a common language and set of expectations for all stakeholders involved in the PCB production process, improving communication and reducing misunderstandings.
-
Increased Customer Satisfaction: By delivering PCBs that meet the quality and performance requirements outlined in IPC standards, manufacturers can enhance customer satisfaction and build long-term relationships.
-
Competitive Advantage: Manufacturers who consistently adhere to IPC standards can differentiate themselves in the market and gain a competitive edge by demonstrating their commitment to quality and reliability.
Implementing IPC-6012 and IPC-A-600 in PCB Production
To successfully implement IPC-6012 and IPC-A-600 in PCB production, manufacturers should follow these steps:
-
Obtain the Standards: Purchase the latest versions of IPC-6012 and IPC-A-600 from the IPC website or an authorized distributor.
-
Train Personnel: Provide comprehensive training to all relevant personnel, including designers, engineers, operators, and inspectors, to ensure they understand and can apply the requirements of the standards.
-
Establish Processes and Procedures: Develop and document processes and procedures that align with the requirements of IPC-6012 and IPC-A-600, ensuring consistency and compliance throughout the production process.
-
Invest in Quality Control: Implement robust quality control measures, including regular inspections and testing, to verify that PCBs meet the acceptance criteria defined in IPC-A-600.
-
Continuously Improve: Regularly review and update processes and procedures to incorporate best practices, technological advancements, and feedback from customers and stakeholders.
By following these steps and maintaining a commitment to quality and continuous improvement, PCB manufacturers can effectively implement IPC-6012 and IPC-A-600 standards and reap the benefits of producing high-quality, reliable PCBs.
Frequently Asked Questions (FAQ)
-
Q: Are IPC-6012 and IPC-A-600 mandatory standards for PCB production?
A: While not mandatory, IPC-6012 and IPC-A-600 are widely adopted and recognized as industry standards. Many customers and industries require adherence to these standards as a condition of doing business. -
Q: How often are IPC-6012 and IPC-A-600 updated?
A: IPC standards are regularly reviewed and updated to keep pace with technological advancements and industry needs. It is essential to obtain and reference the latest versions of the standards to ensure compliance. -
Q: Can IPC-6012 and IPC-A-600 be applied to flexible and Rigid-flex PCBs?
A: IPC-6012 and IPC-A-600 specifically address rigid PCBs. For flexible and rigid-flex PCBs, manufacturers should refer to IPC-6013 and IPC-A-600F, respectively. -
Q: How can I ensure that my PCB supplier adheres to IPC-6012 and IPC-A-600?
A: When selecting a PCB supplier, ask for evidence of their compliance with IPC standards, such as certifications, audit reports, or references from other customers. Regularly communicate your requirements and expectations to your supplier and consider conducting on-site audits to verify their compliance. -
Q: What should I do if I receive PCBs that do not meet the requirements of IPC-6012 or IPC-A-600?
A: If you receive non-conforming PCBs, document the issues and communicate them to your supplier as soon as possible. Work with your supplier to determine the root cause of the problem and establish corrective actions to prevent future occurrences. In some cases, you may need to reject the non-conforming PCBs and request a replacement or rework.
Conclusion
IPC-6012 and IPC-A-600 are essential standards in the world of PCB production, providing a framework for ensuring the quality, reliability, and consistency of rigid printed boards. By adhering to these standards, PCB manufacturers can streamline their production processes, reduce costs, and deliver high-quality products that meet the needs of their customers. As the electronics industry continues to evolve, the importance of these standards will only continue to grow, making it crucial for manufacturers to stay up-to-date and committed to their implementation.
Leave a Reply