Introduction to Rayming-reflow-pilot
Rayming-reflow-pilot is a cutting-edge technology that has revolutionized the manufacturing process of electronic components. It is a highly automated system that enables the precise and efficient soldering of surface-mount components onto printed circuit boards (PCBs). The Rayming-reflow-pilot system is designed to optimize the reflow soldering process, ensuring consistent and high-quality results.
What is Reflow Soldering?
Reflow soldering is a process used in the manufacturing of electronic devices, where surface-mount components are attached to a PCB using solder paste. The process involves applying solder paste to the PCB, placing the components onto the solder paste, and then heating the entire assembly in a reflow oven. The heat causes the solder paste to melt and form a strong, permanent bond between the components and the PCB.
The Importance of Reflow Soldering
Reflow soldering is a critical step in the manufacturing of electronic devices. It ensures that the components are securely attached to the PCB and that the electrical connections are reliable. Poor reflow soldering can lead to a variety of issues, such as:
- Weak or incomplete solder joints
- Bridging between adjacent components
- Tombstoning (where a component stands up on one end)
- Insufficient wetting of the solder onto the component leads or PCB pads
These issues can cause the electronic device to malfunction or fail prematurely, resulting in costly repairs or replacements.
The Rayming-reflow-pilot System
Overview of the System
The Rayming-reflow-pilot system is a highly advanced reflow soldering machine that incorporates a range of features to optimize the soldering process. Some of the key features of the system include:
- Precise temperature control
- Accurate conveyor speed control
- Nitrogen atmosphere capability
- Automatic profile generation
- Real-time process monitoring
These features work together to ensure that the reflow soldering process is consistent, reliable, and of the highest quality.
Temperature Control
One of the most critical aspects of reflow soldering is temperature control. The Rayming-reflow-pilot system uses advanced heating technology to precisely control the temperature throughout the soldering process. The system can be programmed to follow a specific temperature profile, which is optimized for the specific components and PCB being soldered.
Temperature Zone | Temperature Range (°C) |
---|---|
Preheat | 150 – 200 |
Soak | 200 – 240 |
Reflow | 240 – 260 |
Cooling | 100 – 150 |
The system also includes multiple temperature sensors that monitor the temperature in real-time, ensuring that the actual temperature closely matches the programmed profile.
Conveyor Speed Control
Another important factor in reflow soldering is the speed at which the PCB travels through the soldering machine. The Rayming-reflow-pilot system includes a highly accurate conveyor system that can be programmed to move at a specific speed. The speed is optimized based on the size and complexity of the PCB, as well as the specific components being soldered.
PCB Size | Conveyor Speed (mm/s) |
---|---|
Small | 50 – 100 |
Medium | 30 – 50 |
Large | 20 – 30 |
The conveyor system also includes sensors that monitor the speed in real-time, ensuring that the actual speed matches the programmed speed.
Nitrogen Atmosphere Capability
The Rayming-reflow-pilot system also includes the capability to solder in a nitrogen atmosphere. Soldering in a nitrogen atmosphere has several benefits, including:
- Reduced oxidation of the solder and components
- Improved wetting of the solder onto the component leads and PCB pads
- Reduced voiding in the solder joints
The system includes a nitrogen generator and a control system that maintains a consistent nitrogen atmosphere throughout the soldering process.
Automatic Profile Generation
One of the most innovative features of the Rayming-reflow-pilot system is its ability to automatically generate a temperature profile based on the specific components and PCB being soldered. The system includes a database of common components and their recommended soldering profiles. The operator simply needs to input the components being used, and the system will generate an optimized temperature profile.
This feature greatly simplifies the process of setting up the soldering machine and ensures that the optimal temperature profile is used for each job.
Real-Time Process Monitoring
The Rayming-reflow-pilot system also includes a range of sensors and monitoring capabilities that allow the operator to monitor the soldering process in real-time. The system includes cameras that provide a live video feed of the PCB as it travels through the machine. The operator can zoom in on specific areas of the PCB to check for any issues or defects.
The system also includes sensors that monitor various parameters of the soldering process, such as:
- Temperature at various points in the machine
- Conveyor speed
- Nitrogen flow rate
- Solder paste dispense rate
The data from these sensors is displayed on a user-friendly interface, allowing the operator to quickly identify any issues and make adjustments as needed.
Benefits of the Rayming-reflow-pilot System
Improved Soldering Quality
The primary benefit of the Rayming-reflow-pilot system is improved soldering quality. The precise temperature control, accurate conveyor speed, and nitrogen atmosphere capability all work together to ensure that the solder joints are strong, reliable, and free of defects.
Increased Efficiency
The Rayming-reflow-pilot system is also designed to increase the efficiency of the soldering process. The automatic profile generation feature reduces setup time, while the real-time monitoring capabilities allow the operator to quickly identify and address any issues. The system can also handle a high volume of PCBs, further increasing efficiency.
Reduced Costs
By improving soldering quality and increasing efficiency, the Rayming-reflow-pilot system can help to reduce costs associated with rework, repairs, and scrap. The system can also help to reduce labor costs by automating many aspects of the soldering process.
Flexibility
The Rayming-reflow-pilot system is highly flexible and can be used to solder a wide range of components and PCBs. The system can be easily programmed to handle different types of components and can be quickly adjusted to accommodate changes in production requirements.
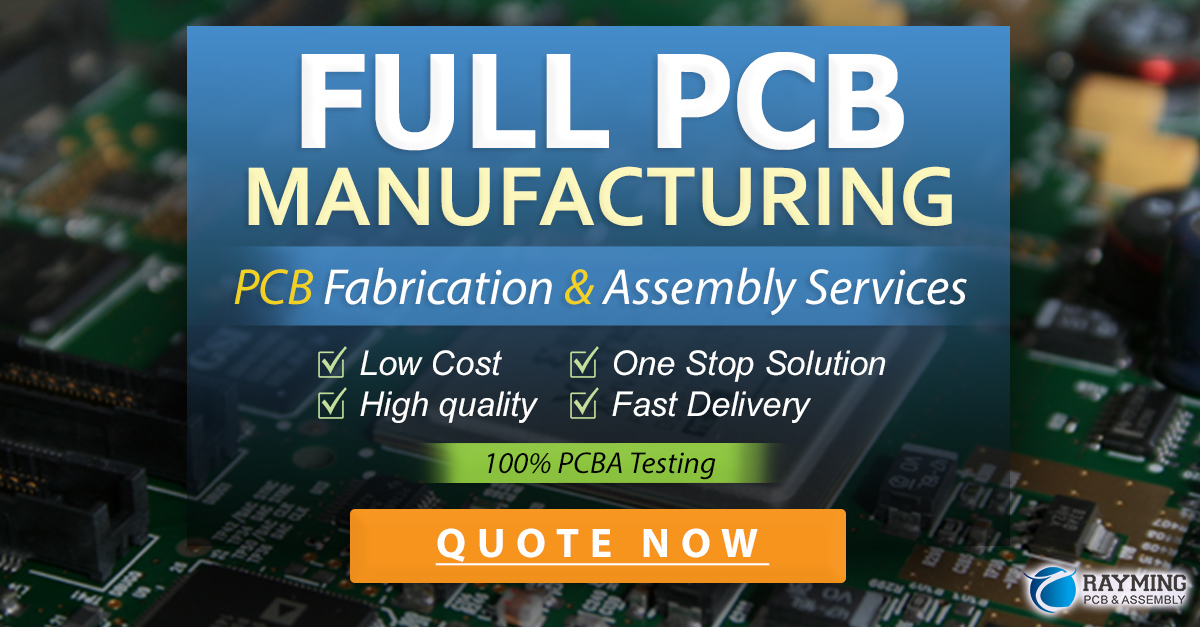
Applications of the Rayming-reflow-pilot System
Consumer Electronics
The Rayming-reflow-pilot system is widely used in the production of consumer electronics, such as smartphones, tablets, and laptops. These devices often include a large number of small, densely packed components that require precise soldering to ensure proper function.
Automotive Electronics
The Rayming-reflow-pilot system is also used in the production of automotive electronics, such as engine control units, infotainment systems, and advanced driver assistance systems (ADAS). These electronics must be able to withstand harsh operating conditions and meet strict reliability requirements.
Medical Devices
The Rayming-reflow-pilot system is used in the production of medical devices, such as pacemakers, defibrillators, and patient monitors. These devices must meet stringent quality and reliability standards to ensure patient safety.
Industrial Control Systems
The Rayming-reflow-pilot system is used in the production of industrial control systems, such as programmable logic controllers (PLCs), human-machine interfaces (HMIs), and sensors. These systems must be able to operate reliably in harsh industrial environments.
Conclusion
The Rayming-reflow-pilot system is a highly advanced reflow soldering machine that offers a range of benefits for manufacturers of electronic devices. The system’s precise temperature control, accurate conveyor speed, nitrogen atmosphere capability, automatic profile generation, and real-time monitoring capabilities all work together to ensure consistent, high-quality soldering results.
By improving soldering quality, increasing efficiency, reducing costs, and offering flexibility, the Rayming-reflow-pilot system is a valuable tool for manufacturers in a wide range of industries, including consumer electronics, automotive electronics, medical devices, and industrial control systems.
Frequently Asked Questions (FAQ)
Q1: What is the Rayming-reflow-pilot system?
A1: The Rayming-reflow-pilot system is a highly advanced reflow soldering machine that incorporates a range of features to optimize the soldering process, including precise temperature control, accurate conveyor speed control, nitrogen atmosphere capability, automatic profile generation, and real-time process monitoring.
Q2: What are the benefits of using the Rayming-reflow-pilot system?
A2: The benefits of using the Rayming-reflow-pilot system include improved soldering quality, increased efficiency, reduced costs, and flexibility. The system ensures consistent, high-quality soldering results while reducing setup time, labor costs, and scrap.
Q3: What industries use the Rayming-reflow-pilot system?
A3: The Rayming-reflow-pilot system is used in a wide range of industries, including consumer electronics, automotive electronics, medical devices, and industrial control systems.
Q4: How does the nitrogen atmosphere capability of the Rayming-reflow-pilot system benefit the soldering process?
A4: Soldering in a nitrogen atmosphere helps to reduce oxidation of the solder and components, improve wetting of the solder onto the component leads and PCB pads, and reduce voiding in the solder joints. This results in stronger, more reliable solder connections.
Q5: Can the Rayming-reflow-pilot system be used to solder different types of components and PCBs?
A5: Yes, the Rayming-reflow-pilot system is highly flexible and can be easily programmed to handle different types of components and PCBs. The system can be quickly adjusted to accommodate changes in production requirements.
Leave a Reply