Introduction to Hi-Speed Design
In today’s fast-paced world, the demand for high-speed electronic systems has never been greater. From cutting-edge research to everyday consumer products, the need for reliable and efficient high-speed designs is paramount. This seminar aims to provide a comprehensive overview of the principles, techniques, and best practices in hi-speed design, equipping attendees with the knowledge and skills necessary to tackle the challenges of modern electronic systems.
What is Hi-Speed Design?
Hi-speed design refers to the process of designing electronic systems that operate at high frequencies, typically in the gigahertz (GHz) range. These systems require careful consideration of various factors, such as signal integrity, power integrity, electromagnetic compatibility (EMC), and thermal management, to ensure optimal performance and reliability.
Importance of Hi-Speed Design
As technology advances, the demand for faster and more efficient electronic systems continues to grow. Hi-speed design plays a crucial role in meeting these demands across various industries, including:
- Telecommunications
- Aerospace and defense
- Automotive
- Medical devices
- Consumer electronics
By mastering the principles of hi-speed design, engineers can develop innovative solutions that push the boundaries of performance and functionality.
Signal Integrity in Hi-Speed Design
Signal integrity is a critical aspect of hi-speed design, as it directly impacts the quality and reliability of the system. Poor signal integrity can lead to data corruption, system failures, and reduced performance.
Understanding Signal Integrity
Signal integrity refers to the ability of an electronic system to maintain the quality and fidelity of signals as they propagate through the system. In hi-speed designs, several factors can affect signal integrity, including:
- Reflections
- Crosstalk
- Attenuation
- Dispersion
- Jitter
To ensure optimal signal integrity, designers must carefully analyze and mitigate these effects throughout the design process.
Techniques for Improving Signal Integrity
There are several techniques that designers can employ to improve signal integrity in hi-speed designs:
-
Impedance Matching: Ensuring proper impedance matching between components and transmission lines can minimize reflections and improve signal quality.
-
Termination Strategies: Implementing appropriate termination strategies, such as series termination or parallel termination, can help reduce reflections and improve signal integrity.
-
Routing Techniques: Careful routing of signals, including the use of microstrip, stripline, or coplanar waveguide structures, can minimize crosstalk and improve signal quality.
-
Material Selection: Choosing appropriate materials for the printed circuit board (PCB) and components can help reduce losses and improve signal integrity.
Technique | Description | Benefits |
---|---|---|
Impedance Matching | Matching component and transmission line impedances | Minimizes reflections, improves signal quality |
Termination Strategies | Implementing series or parallel termination | Reduces reflections, improves signal integrity |
Routing Techniques | Using microstrip, stripline, or coplanar waveguide structures | Minimizes crosstalk, improves signal quality |
Material Selection | Choosing appropriate PCB and component materials | Reduces losses, improves signal integrity |
Power Integrity in Hi-Speed Design
Power integrity is another critical aspect of hi-speed design, as it ensures that the system receives a clean and stable power supply. Poor power integrity can lead to signal degradation, EMI issues, and reduced system reliability.
Understanding Power Integrity
Power integrity refers to the ability of an electronic system to maintain a stable and clean power supply to all components. In hi-speed designs, several factors can affect power integrity, including:
- Voltage drops
- Ground bounces
- Electromagnetic interference (EMI)
- Switching noise
To ensure optimal power integrity, designers must carefully analyze and mitigate these effects throughout the design process.
Techniques for Improving Power Integrity
There are several techniques that designers can employ to improve power integrity in hi-speed designs:
-
Power Distribution Network (PDN) Design: Designing a robust and efficient PDN can help minimize voltage drops and ensure a stable power supply to all components.
-
Decoupling Capacitors: Placing decoupling capacitors close to power pins can help reduce high-frequency noise and improve power integrity.
-
Power Plane Segmentation: Segmenting power planes can help isolate noisy circuits and reduce EMI.
-
Voltage Regulator Module (VRM) Selection: Choosing appropriate VRMs with adequate transient response and load regulation can help maintain a stable power supply.
Technique | Description | Benefits |
---|---|---|
PDN Design | Designing a robust and efficient power distribution network | Minimizes voltage drops, ensures stable power supply |
Decoupling Capacitors | Placing capacitors close to power pins | Reduces high-frequency noise, improves power integrity |
Power Plane Segmentation | Isolating noisy circuits | Reduces EMI |
VRM Selection | Choosing VRMs with adequate transient response and load regulation | Maintains a stable power supply |
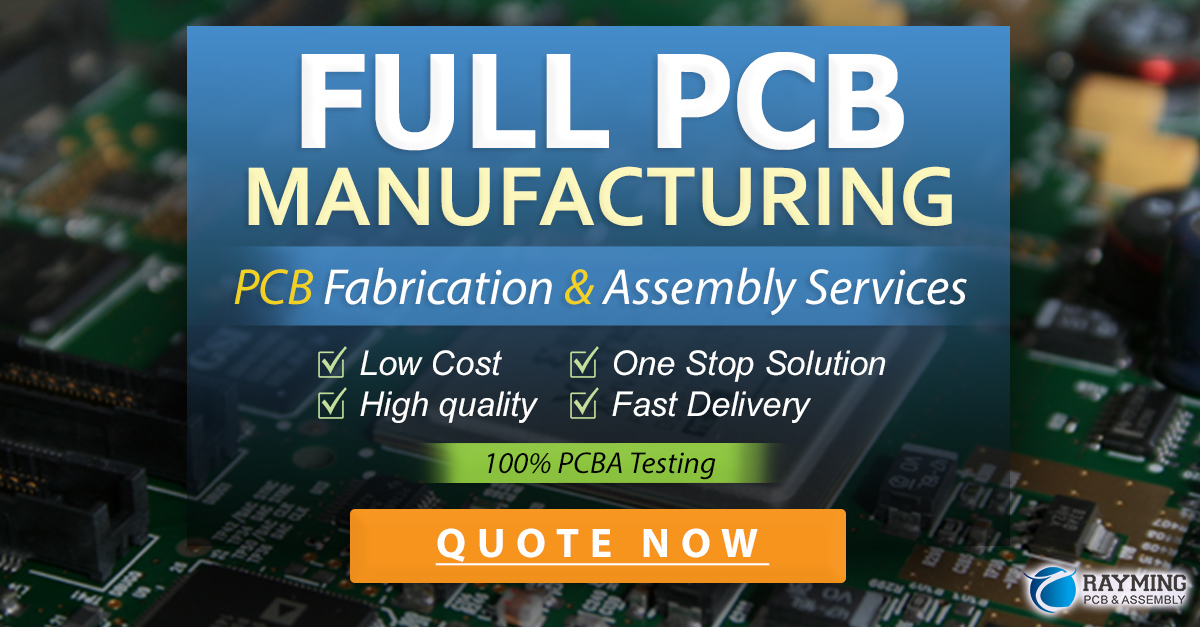
Electromagnetic Compatibility (EMC) in Hi-Speed Design
Electromagnetic compatibility (EMC) is a crucial consideration in hi-speed design, as it ensures that the system does not interfere with other electronic devices and is not susceptible to interference from external sources.
Understanding EMC
EMC refers to the ability of an electronic system to operate correctly in its electromagnetic environment without causing or being affected by electromagnetic interference (EMI). In hi-speed designs, EMC is particularly important due to the high frequencies and fast edge rates involved.
Techniques for Improving EMC
There are several techniques that designers can employ to improve EMC in hi-speed designs:
-
Shielding: Using shielding materials, such as metal enclosures or shielded cables, can help contain EMI and prevent it from affecting other devices.
-
Grounding: Implementing a proper grounding strategy, such as a single-point ground or a multi-point ground, can help reduce EMI and improve system stability.
-
Filtering: Using filters, such as ferrite beads or common-mode chokes, can help suppress high-frequency noise and reduce EMI.
-
Layout Techniques: Careful layout of components and traces, including the use of guard rings or stitching capacitors, can help minimize EMI and improve EMC.
Technique | Description | Benefits |
---|---|---|
Shielding | Using shielding materials, such as metal enclosures or shielded cables | Contains EMI, prevents interference with other devices |
Grounding | Implementing a proper grounding strategy, such as single-point or multi-point ground | Reduces EMI, improves system stability |
Filtering | Using filters, such as ferrite beads or common-mode chokes | Suppresses high-frequency noise, reduces EMI |
Layout Techniques | Careful layout of components and traces, using guard rings or stitching capacitors | Minimizes EMI, improves EMC |
Thermal Management in Hi-Speed Design
Thermal management is an essential aspect of hi-speed design, as high-frequency operation and increased power densities can lead to elevated temperatures, which can negatively impact system performance and reliability.
Understanding Thermal Management
Thermal management refers to the process of controlling and dissipating heat generated by electronic components to maintain optimal operating temperatures. In hi-speed designs, effective thermal management is crucial to ensure reliable operation and prevent premature component failure.
Techniques for Improving Thermal Management
There are several techniques that designers can employ to improve thermal management in hi-speed designs:
-
Heatsinks: Using heatsinks to dissipate heat from high-power components can help maintain optimal operating temperatures.
-
Thermal Interface Materials (TIMs): Applying TIMs, such as thermal grease or thermal pads, between components and heatsinks can improve heat transfer efficiency.
-
Airflow Management: Designing proper airflow paths and using fans or other cooling solutions can help dissipate heat and maintain optimal operating temperatures.
-
PCB Design: Incorporating thermal relief pads, using high-thermal-conductivity materials, and optimizing component placement can help improve heat dissipation and reduce thermal stress.
Technique | Description | Benefits |
---|---|---|
Heatsinks | Using heatsinks to dissipate heat from high-power components | Maintains optimal operating temperatures |
Thermal Interface Materials | Applying TIMs between components and heatsinks | Improves heat transfer efficiency |
Airflow Management | Designing proper airflow paths and using fans or other cooling solutions | Dissipates heat, maintains optimal operating temperatures |
PCB Design | Incorporating thermal relief pads, using high-thermal-conductivity materials, and optimizing component placement | Improves heat dissipation, reduces thermal stress |
Best Practices in Hi-Speed Design
To ensure the success of hi-speed design projects, it is essential to follow best practices throughout the design process. These best practices encompass various aspects of the design, from planning and simulation to fabrication and testing.
Planning and Simulation
-
Define clear design requirements: Establish well-defined performance, reliability, and cost targets early in the design process.
-
Perform system-level simulations: Use simulation tools to analyze signal integrity, power integrity, EMC, and thermal performance at the system level.
-
Collaborate with stakeholders: Engage with stakeholders, such as mechanical engineers, manufacturing experts, and component suppliers, to ensure a holistic approach to design.
PCB Layout and Routing
-
Follow layout guidelines: Adhere to industry-standard layout guidelines, such as trace width and spacing, via sizing, and component placement.
-
Optimize signal routing: Use appropriate routing techniques, such as microstrip, stripline, or coplanar waveguide structures, to minimize crosstalk and improve signal integrity.
-
Implement proper grounding and shielding: Employ a well-designed grounding strategy and use shielding techniques to reduce EMI and improve EMC.
Fabrication and Assembly
-
Choose appropriate materials: Select PCB materials and components that meet the performance, reliability, and cost requirements of the design.
-
Communicate with fabrication and assembly partners: Clearly communicate design intent and requirements to fabrication and assembly partners to ensure accurate and reliable manufacturing.
-
Perform design for manufacturability (DFM) analysis: Conduct DFM analysis to identify and resolve potential manufacturing issues early in the design process.
Testing and Validation
-
Develop a comprehensive test plan: Create a test plan that covers all aspects of system performance, including signal integrity, power integrity, EMC, and thermal performance.
-
Perform pre-compliance testing: Conduct pre-compliance testing to identify and resolve potential issues before final compliance testing.
-
Validate system performance: Validate the system’s performance under real-world operating conditions to ensure that it meets the design requirements.
FAQ
-
What are the main challenges in hi-speed design?
The main challenges in hi-speed design include maintaining signal integrity, ensuring power integrity, achieving electromagnetic compatibility (EMC), and managing thermal performance. These challenges arise due to the high frequencies and fast edge rates involved in hi-speed systems. -
How can I improve signal integrity in my hi-speed design?
To improve signal integrity in your hi-speed design, you can employ techniques such as impedance matching, appropriate termination strategies, careful routing, and proper material selection. These techniques help minimize reflections, reduce crosstalk, and improve overall signal quality. -
What is the importance of power integrity in hi-speed design?
Power integrity is crucial in hi-speed design because it ensures that the system receives a clean and stable power supply. Poor power integrity can lead to signal degradation, EMI issues, and reduced system reliability. Techniques such as robust PDN design, decoupling capacitors, power plane segmentation, and proper VRM selection can help improve power integrity. -
How can I mitigate EMI in my hi-speed design?
To mitigate EMI in your hi-speed design, you can use techniques such as shielding, proper grounding, filtering, and careful layout. Shielding materials, such as metal enclosures or shielded cables, can help contain EMI. Implementing a proper grounding strategy and using filters can also reduce EMI. Careful layout of components and traces can minimize EMI and improve EMC. -
What are some best practices for thermal management in hi-speed design?
Some best practices for thermal management in hi-speed design include using heatsinks to dissipate heat from high-power components, applying thermal interface materials between components and heatsinks, designing proper airflow paths, and optimizing PCB design for heat dissipation. These techniques help maintain optimal operating temperatures and prevent premature component failure.
Conclusion
Hi-speed design is a critical aspect of modern electronic systems, enabling the development of faster, more efficient, and more reliable products across various industries. By understanding the principles of signal integrity, power integrity, EMC, and thermal management, and employing best practices throughout the design process, engineers can successfully tackle the challenges of hi-speed design and create innovative solutions that meet the demands of today’s fast-paced world.
Leave a Reply