Introduction to PCB Classification Standards
Printed Circuit Boards (PCBs) are essential components in modern electronics, providing the foundation for interconnecting electronic components. To ensure the quality, reliability, and manufacturability of PCBs, various classification standards have been established. Two important aspects of PCB classification are the Pattern Class and Drill Class, which define the complexity and precision of the PCB design and manufacturing process.
In this article, we will explore the concepts of Pattern Class and Drill Class in PCB classification, their importance, and how they impact the design and manufacturing of PCBs.
What is Pattern Class?
Pattern Class, also known as Surface Finish Class or Copper Foil Class, refers to the classification of the conductive pattern on the PCB surface. It defines the minimum line width, spacing, and feature size that can be achieved on the PCB. The Pattern Class is determined by the capabilities of the PCB manufacturing process and the requirements of the PCB design.
The most widely used standard for defining Pattern Class is the IPC-6012 standard, which is part of the IPC (Association Connecting Electronics Industries) standards family. IPC-6012 defines three main Pattern Classes:
- Class 1: General Electronic Products
- Class 2: Dedicated Service Electronic Products
- Class 3: High Reliability Electronic Products
Each Pattern Class has specific requirements for the minimum line width, spacing, and feature size, as well as other aspects such as hole size, via size, and surface finish.
What is Drill Class?
Drill Class refers to the classification of the drilled holes on the PCB. It defines the minimum hole size, hole-to-copper spacing, and the accuracy of the drill registration. The Drill Class is determined by the capabilities of the PCB Drilling process and the requirements of the PCB design.
The IPC-6012 standard also defines three main Drill Classes:
- Class 1: General Electronic Products
- Class 2: Dedicated Service Electronic Products
- Class 3: High Reliability Electronic Products
Each Drill Class has specific requirements for the minimum hole size, hole-to-copper spacing, and drill registration accuracy.
Importance of PCB Classification
PCB classification standards, such as Pattern Class and Drill Class, play a crucial role in ensuring the quality, reliability, and manufacturability of PCBs. Here are some reasons why PCB classification is important:
-
Design Guidelines: PCB classification standards provide clear guidelines for PCB designers, helping them create designs that are compatible with the manufacturing process and meet the required performance and reliability criteria.
-
Manufacturing Process Control: PCB manufacturers use classification standards to control their manufacturing processes, ensuring that the PCBs are produced consistently and meet the specified requirements.
-
Quality Assurance: PCB classification standards help in establishing quality assurance procedures, allowing manufacturers to verify that the PCBs meet the required specifications and performance criteria.
-
Communication and Collaboration: PCB classification standards provide a common language for communication between PCB designers, manufacturers, and customers, facilitating collaboration and reducing the risk of misunderstandings or errors.
-
Cost Optimization: By understanding the requirements of different PCB classes, designers and manufacturers can optimize the PCB design and manufacturing process to minimize costs while still meeting the required performance and reliability criteria.
Pattern Class Details
Let’s take a closer look at the details of each Pattern Class defined in the IPC-6012 standard:
Class 1: General Electronic Products
Class 1 PCBs are used for general electronic products where the primary requirement is the function of the completed assembly. The following table summarizes the key requirements for Class 1 PCBs:
Attribute | Requirement |
---|---|
Minimum Line Width | 0.2 mm (0.008 in) |
Minimum Spacing | 0.2 mm (0.008 in) |
Minimum Feature Size | 0.4 mm (0.016 in) |
Hole Size Tolerance | ±0.1 mm (±0.004 in) |
Via Size Tolerance | ±0.1 mm (±0.004 in) |
Surface Finish | Hot Air Solder Leveling (HASL) or Immersion Tin |
Class 2: Dedicated Service Electronic Products
Class 2 PCBs are used for dedicated service electronic products where high reliability and extended life are required. The following table summarizes the key requirements for Class 2 PCBs:
Attribute | Requirement |
---|---|
Minimum Line Width | 0.1 mm (0.004 in) |
Minimum Spacing | 0.1 mm (0.004 in) |
Minimum Feature Size | 0.2 mm (0.008 in) |
Hole Size Tolerance | ±0.05 mm (±0.002 in) |
Via Size Tolerance | ±0.05 mm (±0.002 in) |
Surface Finish | Immersion Silver, Immersion Gold, or Organic Solderability Preservative (OSP) |
Class 3: High Reliability Electronic Products
Class 3 PCBs are used for high reliability electronic products where continued performance and extended life are critical. The following table summarizes the key requirements for Class 3 PCBs:
Attribute | Requirement |
---|---|
Minimum Line Width | 0.05 mm (0.002 in) |
Minimum Spacing | 0.05 mm (0.002 in) |
Minimum Feature Size | 0.1 mm (0.004 in) |
Hole Size Tolerance | ±0.025 mm (±0.001 in) |
Via Size Tolerance | ±0.025 mm (±0.001 in) |
Surface Finish | Electroless Nickel Immersion Gold (ENIG) or Electroless Palladium Immersion Gold (EPIG) |
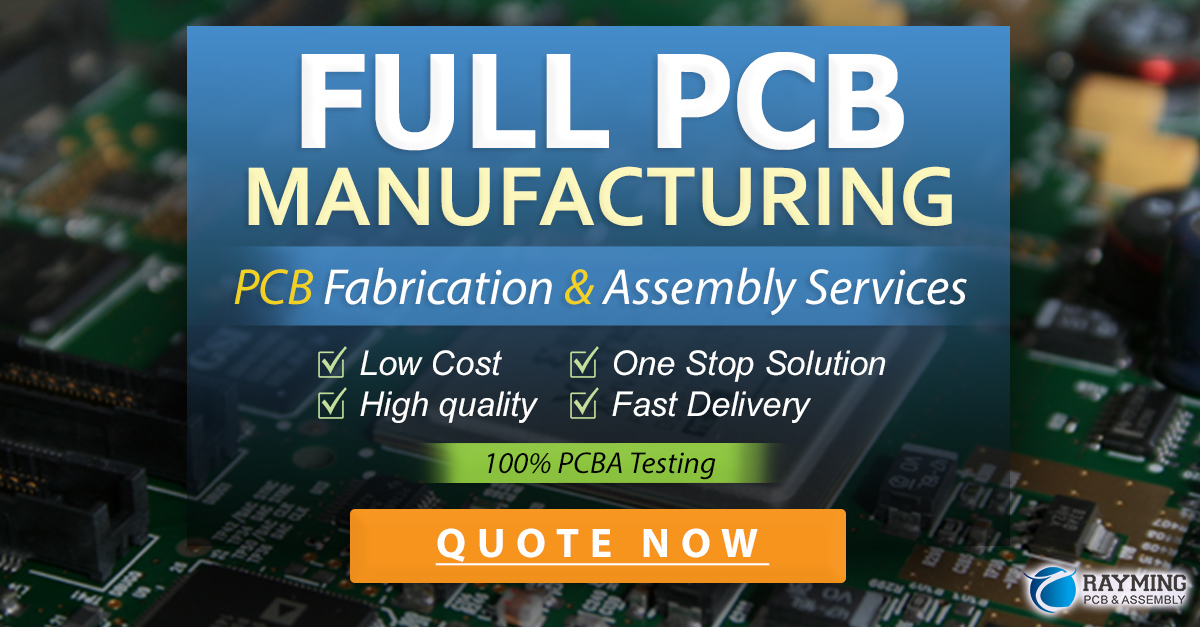
Drill Class Details
Now, let’s explore the details of each Drill Class defined in the IPC-6012 standard:
Class 1: General Electronic Products
Class 1 PCBs have the following requirements for drilled holes:
Attribute | Requirement |
---|---|
Minimum Hole Size | 0.5 mm (0.020 in) |
Hole-to-Copper Spacing | 0.25 mm (0.010 in) |
Drill Registration Accuracy | ±0.1 mm (±0.004 in) |
Class 2: Dedicated Service Electronic Products
Class 2 PCBs have the following requirements for drilled holes:
Attribute | Requirement |
---|---|
Minimum Hole Size | 0.3 mm (0.012 in) |
Hole-to-Copper Spacing | 0.2 mm (0.008 in) |
Drill Registration Accuracy | ±0.05 mm (±0.002 in) |
Class 3: High Reliability Electronic Products
Class 3 PCBs have the following requirements for drilled holes:
Attribute | Requirement |
---|---|
Minimum Hole Size | 0.2 mm (0.008 in) |
Hole-to-Copper Spacing | 0.15 mm (0.006 in) |
Drill Registration Accuracy | ±0.025 mm (±0.001 in) |
Choosing the Right PCB Class
When designing a PCB, it is essential to choose the appropriate Pattern Class and Drill Class based on the specific requirements of the application. Here are some factors to consider when selecting the PCB class:
-
Performance Requirements: Consider the performance requirements of the PCB, such as signal integrity, power handling, and thermal management. Higher PCB classes offer tighter tolerances and more precise features, which can help meet demanding performance requirements.
-
Reliability Requirements: Evaluate the reliability requirements of the PCB, considering factors such as the operating environment, expected lifetime, and consequences of failure. Higher PCB classes offer improved reliability through tighter tolerances and more stringent manufacturing processes.
-
Cost Considerations: Higher PCB classes generally come with increased manufacturing costs due to the tighter tolerances and more advanced manufacturing processes required. Consider the cost implications of choosing a higher PCB class and weigh them against the performance and reliability benefits.
-
Manufacturing Capabilities: Consider the capabilities of the PCB manufacturer when selecting the PCB class. Not all manufacturers have the equipment and expertise to produce higher-class PCBs consistently. Engage with the manufacturer early in the design process to ensure they can meet the required PCB class specifications.
-
Industry Standards and Regulations: Some industries, such as aerospace, defense, and medical, have specific standards and regulations that dictate the minimum PCB class requirements. Ensure that the selected PCB class meets any applicable industry standards or regulations.
Frequently Asked Questions (FAQ)
-
What is the difference between Pattern Class and Drill Class in PCB classification?
Pattern Class refers to the classification of the conductive pattern on the PCB surface, defining the minimum line width, spacing, and feature size. Drill Class refers to the classification of the drilled holes on the PCB, defining the minimum hole size, hole-to-copper spacing, and drill registration accuracy. -
Why is PCB classification important?
PCB classification is important because it provides clear guidelines for PCB designers and manufacturers, ensures quality and reliability, facilitates communication and collaboration, and helps optimize costs while meeting performance requirements. -
What are the three main Pattern Classes defined in the IPC-6012 standard?
The three main Pattern Classes defined in the IPC-6012 standard are Class 1 (General Electronic Products), Class 2 (Dedicated Service Electronic Products), and Class 3 (High Reliability Electronic Products). -
What factors should be considered when choosing the appropriate PCB class?
When choosing the appropriate PCB class, consider factors such as performance requirements, reliability requirements, cost considerations, manufacturing capabilities, and industry standards or regulations. -
Can all PCB manufacturers produce high-class PCBs?
Not all PCB manufacturers have the equipment and expertise to consistently produce high-class PCBs. It is important to engage with the manufacturer early in the design process to ensure they can meet the required PCB class specifications.
Conclusion
PCB classification standards, such as Pattern Class and Drill Class, play a vital role in ensuring the quality, reliability, and manufacturability of PCBs. By understanding the requirements of different PCB classes and selecting the appropriate class for a given application, designers and manufacturers can optimize the PCB design and manufacturing process to meet performance and reliability goals while managing costs.
When designing a PCB, it is crucial to consider factors such as performance requirements, reliability needs, cost implications, manufacturing capabilities, and industry standards when selecting the PCB class. By working closely with PCB manufacturers and following established classification standards, designers can create PCBs that meet the demands of modern electronic applications.
As technology continues to advance and electronic devices become more complex, the importance of PCB classification standards will only continue to grow. By staying informed about these standards and their implications, designers and manufacturers can stay ahead of the curve and deliver high-quality, reliable PCBs that power the electronic devices of today and tomorrow.
Leave a Reply