Introduction to PCB Machining
Printed Circuit Board (PCB) machining is an essential process in the manufacturing of electronic devices. It involves the use of various techniques to create slots, milling, contours, and rout-outs in the PCB design. These features are crucial for the proper functioning and aesthetics of the final product. In this article, we will explore the different aspects of PCB machining and how to effectively indicate these features in your PCB design.
Types of PCB Machining
Slots
Slots are elongated openings in the PCB that are used for various purposes, such as:
- Mounting components
- Providing ventilation
- Allowing access to underlying layers
To indicate slots in your PCB design, you need to specify the following parameters:
- Length
- Width
- Location
- Orientation
Milling
Milling is the process of removing material from the PCB using a rotating cutting tool. It is used to create features such as:
- Pockets
- Cavities
- Channels
- Cutouts
To indicate milling in your PCB design, you need to specify the following parameters:
- Depth
- Width
- Location
- Tool diameter
Contour
Contour machining is the process of cutting the outline of the PCB to its final shape. It is used to create features such as:
- Rounded corners
- Complex shapes
- Beveled edges
To indicate contour machining in your PCB design, you need to specify the following parameters:
- Outline shape
- Cutting depth
- Tool diameter
Rout-outs
Rout-outs are similar to slots but are typically used for more complex shapes and larger openings. They are used for purposes such as:
- Creating openings for connectors
- Providing access to underlying components
- Allowing for the insertion of other parts
To indicate rout-outs in your PCB design, you need to specify the following parameters:
- Shape
- Size
- Location
- Depth
Best Practices for Indicating PCB Machining Features
To ensure that your PCB machining features are accurately and efficiently manufactured, follow these best practices:
- Use clear and consistent naming conventions for all machining features.
- Provide detailed dimensions and tolerances for each feature.
- Specify the required tools and cutting parameters.
- Use appropriate layer designations for machining features.
- Communicate any special requirements or considerations to the manufacturer.
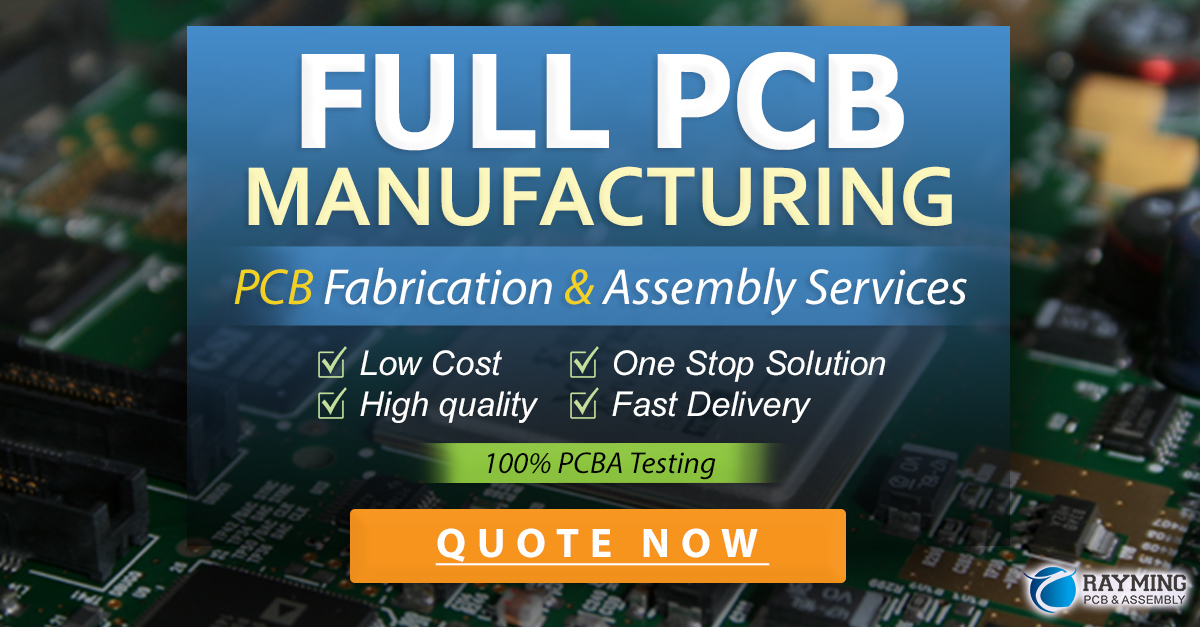
PCB Machining Tools and Equipment
To perform PCB machining, manufacturers use a variety of tools and equipment, including:
- CNC routers
- Milling machines
- Laser Cutters
- Drilling machines
- Engraving machines
Each tool has its own advantages and limitations, and the choice of equipment depends on factors such as:
- Material type
- Feature complexity
- Required precision
- Production volume
Material Considerations for PCB Machining
The choice of material is crucial for the success of PCB machining. Different materials have different properties that affect their machinability, such as:
- Hardness
- Brittleness
- Thermal stability
- Electrical properties
Some common PCB materials include:
- FR-4
- Aluminum
- Copper
- Polyimide
- Ceramic
When selecting a material for your PCB, consider the following factors:
- Mechanical requirements
- Electrical requirements
- Environmental conditions
- Cost
PCB Machining Tolerances and Precision
PCB machining tolerances and precision are critical for ensuring the proper fit and function of the final product. Some factors that affect the achievable tolerances and precision include:
- Material properties
- Feature size and complexity
- Tool type and condition
- Machining parameters
To achieve the desired tolerances and precision, consider the following:
- Use appropriate tools and equipment
- Optimize machining parameters
- Implement quality control measures
- Communicate tolerance requirements clearly
Design for Manufacturing (DFM) Considerations
To facilitate efficient and cost-effective PCB machining, it is important to incorporate Design for Manufacturing (DFM) principles into your PCB design. Some key DFM considerations include:
- Minimizing feature complexity
- Avoiding unnecessary machining operations
- Providing adequate clearances and tolerances
- Using standard tools and processes
- Optimizing panel utilization
By following DFM guidelines, you can reduce manufacturing costs, improve yields, and accelerate time-to-market.
Common PCB Machining Challenges and Solutions
PCB machining can present various challenges that may affect the quality and reliability of the final product. Some common challenges include:
- Tool wear and breakage
- Material deformation and stress
- Burr formation
- Delamination
- Dimensional inaccuracy
To overcome these challenges, consider the following solutions:
- Use appropriate tools and machining parameters
- Implement proper workholding and fixturing
- Perform regular tool maintenance and replacement
- Use coolants and lubricants as necessary
- Implement quality control measures
Quality Control and Inspection
To ensure the quality and consistency of PCB machining, it is important to implement appropriate quality control and inspection measures. Some key aspects of quality control include:
- Visual inspection
- Dimensional verification
- Electrical testing
- Microsectioning
- Failure analysis
By implementing a comprehensive quality control program, you can identify and address issues early in the manufacturing process, reducing scrap and rework costs.
PCB Machining Service Providers
If you do not have the in-house capabilities for PCB machining, you can outsource the process to specialized service providers. When selecting a PCB machining service provider, consider the following factors:
- Experience and expertise
- Equipment and capabilities
- Quality control measures
- Turnaround time
- Cost
It is important to establish clear communication channels and provide detailed specifications to ensure that the service provider can meet your requirements.
Future Trends in PCB Machining
As the electronics industry continues to evolve, PCB machining technologies and processes are also advancing. Some future trends in PCB machining include:
- Increased automation and robotics
- Additive manufacturing (3D printing)
- Micromachining and nanotechnology
- Smart materials and structures
- Sustainable and eco-friendly processes
By staying up-to-date with the latest trends and technologies, you can ensure that your PCB designs remain competitive and innovative.
Frequently Asked Questions (FAQ)
- What is the difference between slots and rout-outs in PCB machining?
-
Slots are elongated openings used for mounting components, ventilation, or access to underlying layers, while rout-outs are used for more complex shapes and larger openings, such as creating openings for connectors or allowing for the insertion of other parts.
-
How do I specify the required tools and cutting parameters for PCB machining?
-
To specify the required tools and cutting parameters, provide detailed information about the tool type, diameter, cutting speed, feed rate, and depth of cut. This information should be clearly communicated to the manufacturer to ensure accurate and efficient machining.
-
What are some common materials used for PCBs?
-
Common materials used for PCBs include FR-4, aluminum, copper, polyimide, and ceramic. The choice of material depends on factors such as mechanical and electrical requirements, environmental conditions, and cost.
-
How can I ensure the quality and consistency of PCB machining?
-
To ensure the quality and consistency of PCB machining, implement a comprehensive quality control program that includes visual inspection, dimensional verification, electrical testing, microsectioning, and failure analysis. Regular tool maintenance and replacement, as well as the use of appropriate machining parameters, can also help maintain quality.
-
What are some future trends in PCB machining?
- Some future trends in PCB machining include increased automation and robotics, additive manufacturing (3D printing), micromachining and nanotechnology, smart materials and structures, and sustainable and eco-friendly processes. Staying informed about these trends can help you maintain a competitive edge in the electronics industry.
Conclusion
PCB machining is a critical process in the manufacturing of electronic devices, and indicating slots, milling, contour, and rout-outs in your PCB design is essential for ensuring the proper functioning and aesthetics of the final product. By understanding the different types of PCB machining, best practices for indicating machining features, material considerations, tolerances and precision, DFM principles, and quality control measures, you can create PCB designs that are optimized for manufacturing and reliability.
As the electronics industry continues to evolve, staying up-to-date with the latest trends and technologies in PCB machining can help you remain competitive and innovative. By partnering with experienced PCB machining service providers and implementing a comprehensive quality control program, you can ensure the success of your PCB projects and deliver high-quality products to your customers.
Parameter | Slot | Milling | Contour | Rout-out |
---|---|---|---|---|
Length | ✓ | |||
Width | ✓ | ✓ | ||
Depth | ✓ | ✓ | ✓ | |
Location | ✓ | ✓ | ✓ | |
Orientation | ✓ | |||
Shape | ✓ | ✓ | ||
Tool Diameter | ✓ | ✓ |
Leave a Reply